Starting a family business and keeping it going for more than 55 years takes dedication, resourcefulness, business acumen and the foresight to invest in modern technology. These traits are particularly apparent when one takes a walking tour of the sprawling Garden Street Iron & Metal recycling complex, located just west of downtown Cincinnati.
Set on 22 acres with three nearby rail spurs in Spring Grove, Ohio, the complex is a beehive of activity as both consumers and businesses truck in ferrous and nonferrous metals for reprocessing. Owned and operated by the Weber family, the recycling operation has undergone a major transformation since the end of 2013 with almost $19 million invested in new equipment and infrastructure, including a variety of recycling equipment from Eriez, Erie, Pennsylvania.
The upgrades have enabled Garden Street to process more than 8,000 tons of scrap each month, says Earl Weber Jr., president and manager of the company’s Ohio operations.
His brother, Rob Weber, runs Garden Street Iron & Metal of Southwest Florida Inc. That company has operations in Fort Myers, Naples and Cape Coral.
“We spent about three years getting everything together for the upgrades at our Spring Grove operation and finally broke ground on Dec. 6, 2013,” Earl recalls. “We talked to companies at the ISRI (Institute of Scrap Recycling Industries) show for two years, including Eriez.”
He continues, “We like the fact that the equipment we chose is made in the U.S.”
Putting the pieces together
Garden Street began working with American Pulverizer, St. Louis, and Hustler Conveyor, O’Fallon, Missouri, to install an APCO 98-by-10, heavy-duty automobile and scrap shredding system, an integral piece of equipment the company needed to grow its regional business, Earl says. That collaboration also resulted in ongoing discussions with representatives from Eriez with the goal of providing Garden Street the highest levels of metal recovery.
From those discussions and on-site evaluations, Garden Street installed a PokerSort™, two P-Rex84 scrap drum magnets with Underflow Processing System, two magnetic pulleys, two RevX-E® eddy current separators (ECS), one ProSort II airless metal recovery system, one FinesSort® metal recovery system and a Metal Loss Monitor.
“Once we got the shredder, we ultimately decided to purchase the right kind of equipment to make this a full-scale operation where we are now a regional player in this business,” Earl says. “This is a very competitive atmosphere, and we realized we needed the most technologically advanced equipment in the market.”
Following the shredder, scrap material passes through the PokerSort, which extracts long, troublesome pokers, such as automotive springs, tie rods, steering and axle components and other uncooperative long shapes before heading to the drum magnets.
Once that step is complete, the material is conveyed through two P-Rex scrap drums with Underflow Processing System, where Garden Street is “running at 99 percent ferrous recovery,” Earl says.
Fluff passes under the P-Rex drum rather than over it as it does in traditional processes. This modification enhances fluff removal and metal recovery, generating increased profits for Garden Street, according to the supplier.
Tim Shuttleworth, Eriez president and CEO, remembers that Garden Street was one of the initial recycling operations to install the drum magnet with Underflow Processing System and is now realizing the quantitative benefits. “The standard over-the-drum processing approach is not very efficient for cleaning fluff out of the frag or ferrous product since most of the cleaning action is in a very narrow zone and some items cleaned from the frag actually fall back into the feed source.
“Conversely, when you go on the underflow of the drum, any fluff released from the ferrous product stays out of the ferrous product, enabling a 50 percent reduction in the amount of entrained fluff compared to over-the-drum processing,” Shuttleworth adds.
Because the drum magnet is a permanent magnet, the magnetic force extends to the edge of the drum. Earl says it’s one reason that Garden Street is able to recover more large sphere-shaped meatballs and knuckles, whereas before that recovery task was limited to hand picking.
Removing the nonferrous
arden Street then installed two side-by-side RevX-E units to handle nonferrous metals. These particular units with 84-inch rotor widths are designed with an eccentrically mounted magnetic rotor within the nonconductive larger diameter shell. This eccentric rotor design reduces long-term wear that results from heated ferrous buildup. The ECS units “throw off a very clean aluminum product,” Earl observes.
Resulting from extensive research and development, the eccentric rotor design offers high performance in terms of material displacement and reliability, according to the equipment manufacturer. The RevX-E rotor has been proven by independent third-party testing to throw aluminum “fines” nearly 20 percent farther than other ECS units, the manufacturer says.
Garden Street now recovers valuable metals that would normally go to landfill, enabling its customers to purchase a high-grade metal product.
The company installed yet another piece of equipment—the ProSort II Airless Metal Recovery System—to gain even higher levels of ferrous recovery. This unit uses high-sensitivity metal sensors aligned with low-energy electromagnetically driven paddles to separate valuable metals from the shredded material, the manufacturer says.
The ProSort II uses a traditional conveyor belt and sensors to detect metals, then, instead of costly air systems, 2-inch “electromagnetic motorized paddles” reject material. The paddles are positioned side by side in a bank as wide as the belt; when the sensors detect metal on the belt, the control circuit energizes the appropriate paddle at the moment the metal passes below/under, diverting from the product stream, the manufacturer says. This system is designed to recover the majority of nonferrous and stainless steel from the material stream.
The motorized paddle is adjustable. By replacing expensive air compressor plants, valves and airlines with energy-efficient electromagnetic drives, the ProSort II requires less than 25 percent of the electricity needed to operate a comparably sized air-powered sorter, according to the equipment manufacturer.
The finer points
According to Earl, Garden Street wanted to ensure it was recovering as much metal as possible before the end of the waste stream. The other piece of equipment that Garden Street installed was a FinesSort metals recovery system, which recovers metal less than 1 inch in size.
This unit receives the discarded “fines” material that has passed through the initial screening process. The material flows through the machine’s magnetic separators, removing metals from the flow, dropping them onto a cross-belt conveyor and into a recycling container.
Ferrous is first separated using a powerful rare earth pulley. The ferrous metal then passes over a magnetic drum to further separate the ferrous from any remaining residual waste. The fraction is dropped onto a cross conveyor and into a collection bin. Also at this stage, light nonmetal materials fall out of the stream onto the waste conveyor below.
The second stage reclaims the nonferrous metals. Here, a high-frequency ECS recovers fine nonferrous materials that the main ECS has missed. The nonferrous material is propelled by the special ECS onto a cross conveyor and from there into collection bins.
Finally, the Metal Loss Monitor (MLM) enables Garden Street to determine the quantity of metals that are passing through its scrap yard unrecovered. The MLM continually scans the residue stream for metal that has escaped the process and is headed for landfill disposal.
Staying competitive
Establishing a niche within the competitive scrap metal industry in and around Cincinnati now requires the combined efforts of the Weber family and its 70-plus employees. What started out as a scrap metal trucking company founded by Earl Weber Sr. in 1958 has now grown into a technologically driven operation with continuous upside.
“There have been a lot of changes in this business, with a lot of older scrap yards no longer around,” Earl says.
“Once we decided to invest in the upgrades, there was no question we need the best equipment possible to stay competitive and purchase the equipment from companies we trusted,” he adds.
This article was submitted on behalf of Eriez, www.eriez.com, Erie, Pennsylvania. The company’s magnetic lift and separation, metal detection, materials feeding, screening, conveying and controlling equipment have applications in the recycling industry as well as in other industrial sectors.
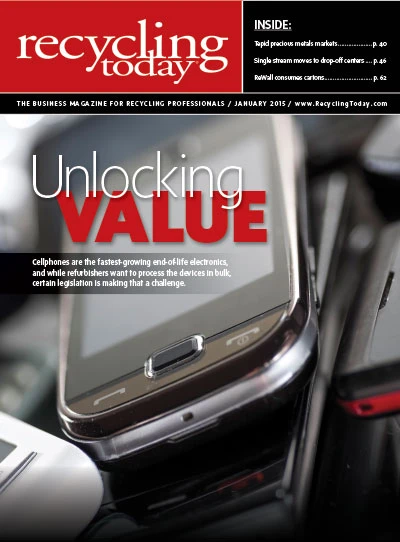
Explore the January 2015 Issue
Check out more from this issue and find your next story to read.
Latest from Recycling Today
- Lindner shredders prepare Brazilian plastic for recycling
- China ups steel output while other nations cut back
- ReElement, Posco partner to develop rare earth, magnet supply chain
- Comau to take part in EU’s Reinforce project
- Sustainable packaging: How do we get there?
- ReMA accepts Lifetime Achievement nominations
- ExxonMobil will add to chemical recycling capacity
- ESAB unveils new cutting torch models