Padnos (formerly Louis Padnos Iron & Metal) has been repurposing recyclables for more than 100 years, serving industrial and commercial accounts throughout the U.S. and residents in and around Michigan.
Headquartered in Holland, Michigan, the company has 21 locations and accepts a wide range of materials, including ferrous and nonferrous metals. The company sells its processed metals to foundries and mills that melt them as feedstock.
In addition to its metals processing machinery, Padnos also has made significant investments in processes and technology to recycle paper, plastics and, more recently, electronics.
Among the company’s core philosophies are continuously building relationships with scrap dealers, logistics providers and buyers across the country. Now in its fourth generation of family management, Padnos draws upon a century of scrap management expertise, striving to implement industry best practices for optimal efficiency while also seeking to maintain the highest level of environmental stewardship within its operations.
Disdain for dust
As part of that philosophy, Padnos says it is constantly developing and refining its approach to fugitive material management, with a goal of preventing the escape of any dust or spillage that may be generated by its activities. In late 2012, the company researched equipment to deliver open-area dust suppression at its location in downtown Holland.
“The site is about 29 acres,” says Padnos Purchasing Director Bruce Karger. “We handle primarily metals at this facility, such as scrap from stamping plants and other metalworking operations, as well as peddler scrap from our smaller yards,” he adds. “Most of it comes in by truck, and it’s moved by front loaders and cranes, though we also have rail and barge service.”
The loaders feed a Metso Texas Shredder plant and a Lindner Universal shear-style shredder. Both have integrated dust suppression, but the outflow dries fairly quickly, especially in hot weather. Subsequent handling of the shredded material inevitably creates dust, which can migrate long distances if left unchecked.
Surrounded by businesses and neighborhoods, company officials wanted to invest accordingly in proactive measures to ensure that dust would not create a nuisance for the surrounding community or create a workplace hazard.
Design decisions
After investigating several manufacturers and reviewing their equipment choices, Padnos selected a DustBoss DB-60 to deliver suppression over three processing centers, covering about 3 acres in all.
“Other than basic material handling, the main dust-generating activities are shearing, shredding and briquetting,” says Karger. “Our goal is to ensure that airborne particles don’t leave the property.”
The DB-60 is supplied by Dust Control Technology (DCT), Peoria, Illinois. The atomized misting unit generates millions of droplets specifically sized to maximize dust suppression and then launches them over large distances in an engineered air plume created by a powerful ducted fan.
A 25-horsepower electric motor gives the machine a reach of nearly 200 feet (about 60 meters), allowing the oscillating unit to cover an area as large as 125,000 square feet (more than 11,600 square meters) with a virtual dust blanket. Supplied with a 20-foot (6-meter) mounting tower, the DB-60 was installed atop a 10-foot (3-meter) concrete pedestal to increase its range and aiming ability even further.
The control panel, booster pump and three-way valve are located inside a shed for protection.
“We’ve used hoses and sprinklers in the past, and at times we’ve had our own water trucks on site,” says Padnos Yard Superintendent Tim Driesenga. “But the suppression performance wasn’t what we had hoped for. We’ve also tried dust suppression equipment from other suppliers,” he continues.
“When we compared results from [previous] machines we had to the DustBoss, the DB-60 was far more effective [and] clearly a higher-quality design. It does a much better job of knocking down the dust and keeping it down,” Driesenga adds.
From the time of its initial arrival, the Padnos team says it was pleased with the results of using the dust-suppression equipment. “The performance of this design is better than any method we’d tried in the past, and eliminating the manual spraying presented immediate labor savings for us,” Driesenga says. Though it’s one of the largest models DCT offers, the DB-60 uses less than 24 gallons (90.85 liters) of water per minute, even with the booster pump raising pressure to 160 PSI (11 bar).
Remote control
The unit was originally supplied with four optional remote controls, giving loader operators the ability to turn the unit and the oscillation on or off at any time. The oscillation range, however, was only programmable at the panel. Although the system performed well, operators noticed an opportunity to better serve the unique layout and work flow at the Holland plant, so they contacted the supplier to discuss some possible modifications to the system.
“We felt that we could make dust control even easier and more efficient for the operators who are moving our material,” says Driesenga. “The easier the equipment is to operate and the more efficiency we can build into the dust management process, the more likely that the equipment will be used and used correctly,” he adds.
During the initial meeting, Driesenga said loading and unloading could take place at nearly any point within the 3-acre area, and the 359-degree oscillation was a key to reaching those activities. But the relatively slow oscillation speed prevented quick rotation of the barrel to focus on arriving trucks. Operators had to wait for the unit to oscillate to the required spot.
The big question was whether DCT could redesign the unit to reach any point on the oscillation arc in 30 seconds or less and build the control capability into the remotes that the company already had. Adding the ability to set the arc remotely also would be a bonus, relieving operators from having to visit the control panel.
“The first reaction we got was ‘We’ve never done that before,’” recalls Karger. “But no sooner was that said then the DCT team got busy with us to figure out exactly what features we needed and how it could be done. We were extremely impressed with the technical assistance they provided in developing the concept and turning it into a working reality.”
The supplier’s engineers decided they could achieve the desired repositioning speed by replacing the fixed-speed oscillation motor with one that turned approximately four times faster, coupled to a variable-frequency drive (VFD). To avoid having to ship the unit back to Illinois for the revisions, DCT personnel performed the gear motor change-out, panel modifications and VFD installation on site.
While maintaining all existing controls on the remotes, the manufactuer’s technicians also added the ability to select from eight preset oscillation ranges, which could be programmed by operators from the modified panel with its touchscreen display. Finally, they added a “jog left/right” switch and a “home” button to the remotes for quick repositioning.
“With the modified remotes, we have much more versatility in aiming the DustBoss and quickly bringing it to the exact location needed at any given time,” Driesenga says. “And the oscillation arc can be changed even while the oscillator is running,” he adds.
Constant air monitoring at the Padnos site has confirmed the unit’s effectiveness, helping the company to remain in full compliance with air quality regulations. “We recently had an inspector review our operations this past summer, and he commended us on our dust control measures,” Driesenga comments. “The results were better than he expected.”
Karger adds, “I feel like these are the tools that enable us to do a better job of preventing dust from leaving our property. For us, it’s taking our dust management to the next level. In fact, we have plans in place for another unit.”
This article was supplied by Peoria, Illinois-based Dust Control Technology, www.dustboss.com.
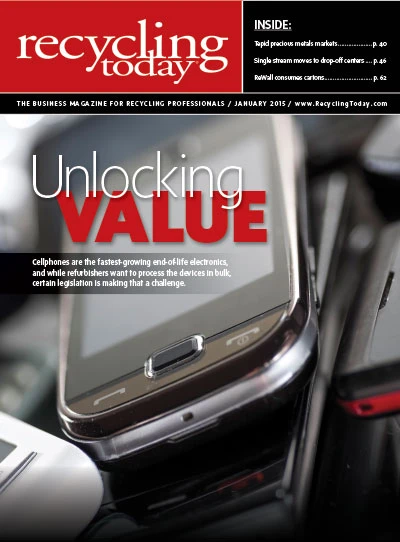
Explore the January 2015 Issue
Check out more from this issue and find your next story to read.
Latest from Recycling Today
- Registration opens for Scrap Expo 2025
- Toyota opens ‘circular factory’ in UK
- Agilyx works with former Plastic Energy CEO on sourcing venture
- Two factors raise ferrous export questions in April
- Analyst: Scrap imbalance lost amid copper’s critical status
- AF&PA report shows decrease in packaging paper shipments
- GreenMantra names new CEO
- Agilyx says Styrenyx technology reduces carbon footprint in styrene production