MUNICIPAL
Republic Services to expand recycling capacity in Nevada
Republic Services Inc., based in Phoenix, has announced that its subsidiary, Republic Silver State Disposal Inc., Las Vegas, has begun construction on a new recycling facility that will double residential recycling capacity in southern Nevada. The new 110,000-square-foot facility will be home to highly advanced recycling technologies, the company claims, and will be built next to an existing 88,000-square-foot facility. The increased capacity is expected to make the Southern Nevada Recycling Complex the largest residential recycling complex in the nation, Republic Services says.
“This is a special day for the city of North Las Vegas, Clark County and customers throughout southern Nevada,” says Tim Oudman, area president of Republic Services. “It is fitting that a recycling complex of this magnitude is coming to Las Vegas. Southern Nevada is home to considerable natural beauty, and this community is deeply committed to sustainability. We are truly proud to invest in a recycling complex that will help preserve the local environment for future generations and enable customers to meet or exceed their recycling goals.”
Construction at the Southern Nevada Recycling Complex is expected to create 80 new jobs between project partners Cambridge Construction, CP Group and EV&A, Republic Services says.
The company adds that the complex is scheduled to begin operations in fall 2015 and is expected to eventually employ 180 people.
“The city of North Las Vegas is proud to be the future home of the nation’s largest residential recycling complex,” says North Las Vegas Mayor John J. Lee. “Our community will take tremendous pride in this complex and its contributions to the local economy. With expanded recycling capabilities and a world-class learning center, our residents and businesses will have more resources than ever before to increase overall recycling participation.”
He adds, “We applaud Republic Services for making a sustainable investment in Southern Nevada’s future.”
The Southern Nevada Recycling Complex will feature an interactive learning center that offers visitors a firsthand view of the recycling process, according to Republic Services. It will include displays, videos and educational materials on recycling and sustainability.
Advanced recycling technologies from the CP Group that will be installed at the new complex will include a highly automated control system, touch-screen human machine interface (HMI) control, supervisory control data acquisition (SCADA) monitoring and remote access that enables continuous monitoring operations for optimal performance, Republic Services says. The new system also will have five optical sorters to maximize the recovery of all grades of plastics, including PET (polyethylene terephthalate) and HDPE (high-density polyethylene), and aseptic containers/cartons.
The Southern Nevada Recycling Complex will be able to process approximately 1,000 tons of mixed recyclables per day, or 70 tons per hour, the company says, and will accommodate future growth in residential recycling as well as increased commercial, industrial and construction and demolition recycling demands throughout southern Nevada.
Republic Services employs more than 1,300 people in southern Nevada who serve more than 535,000 households and 27,000 commercial customers, including the University of Nevada Las Vegas, Sands Corp., MGM International, Wynn Group, Las Vegas Convention and Visitors Authority, McCarron Airport and Las Vegas Motor Speedway.
METALS
American Specialty Alloys to build aluminum plant in the Southeast
American Specialty Alloys (ASA), Flowood, Mississippi, has announced plans to build what it calls an aluminum mini-mill in the U.S. Southeast. The scrap-fed $1.2 billion facility will supply more than 600,000 tons of flat-rolled aluminum product to the automotive industry, according to the company.
ASA says a “shortage of modern, efficient, clean manufacturing facilities to keep up with the new demand” is what led to its decision to build the new mill.
The company says it is now finalizing site selection.
The first phase of the operation is expected to begin in late 2016, with full Phase One capacity production occurring six months later, says Roger Boggs, founder and CEO of ASA.
“We are building a modern mill and using a process that will change aluminum production forever in this industry,” says Boggs. “The mill will leverage the use of automation, low-cost utilities in the South and will use recycled aluminum to efficiently produce the higher grade aluminum that will be used to make the Obama administration’s Corporate Average Fuel Economy standards (CAFE)-compliant automobiles of the future.”
ASA says it has chosen Italy-based Danieli Group as its technological partner to provide the hot and cold rolling and aluminum processing mill. In addition, United Kingdom-based Innoval Technology will provide system design support.
Boggs estimates that the company’s continuous casting model could be as much as 45 percent more efficient than current casting processes used in the aluminum industry.
METALS
MetalX celebrates second anniversary
MetalX LLC, a scrap metal recycling company headquartered in Waterloo, Indiana, celebrated its second anniversary at the end of October. (MetalX was profiled in the March 2013 issue of Recycling Today, online at www.Recycling Today.com/rt0313-metal-x-profile.aspx.)
The company received its first load of scrap at its new state-of-the-art processing plant located on 70 acres near Waterloo on Oct. 27, 2012.
Founded by former OmniSource CEO Danny Rifkin, his son, Neal, and a team of metals industry veterans, the business has expanded its footprint to include three facilities in the northeast Indiana cities of Waterloo, Auburn and Fort Wayne. Total scrap volume continues to increase, and MetalX currently employs 150 people, the company says.
“The last two years have certainly been exciting,” Danny Rifkin says. “Even though this is a tough business and current industry dynamics are challenging, we have achieved our initial objectives and have also been able to demonstrate that a well-capitalized, independent company with a cohesive team focused on creating value for customers, can build a sustainable business.”
Rifkin adds, “Our growth thus far confirms that our vision of creating an organization of dedicated people motivated by common goals can establish a foundation for long-term success is sound. Our people deserve all the credit for getting MetalX to this point.”
MetalX, a privately held company, offers recycling, processing and trading services for scrap and secondary metals in addition to providing consulting and management services to industrial scrap generators.
The company says it “is focused on creating value through relationships with suppliers and consumers while utilizing the most current industry technologies.”
METALS
Upstate Shredding – Weitsman Recycling expands in central New York
The scrap metal company Upstate Shredding – Weitsman Recycling, headquartered in Owego, New York, has acquired the assets of Murtagh Scrap Handling, a scrap recycling company in Rome, New York. The acquisition is expected to be finalized by January 2015, according to Upstate Shredding. Murtagh, which has been a family-owned business for more than 25 years, will be renamed Ben Weitsman of Rome.
“This is a very strategic move for the company as we continue to expand throughout the Northeast,” Adam Weitsman, CEO of Upstate Shredding, says.
Weitsman says Upstate Shredding will invest $3 million to renovate the acquired yard, including constructing new buildings, purchasing and installing new equipment, paving the entire facility and installing new fencing and landscaping.
Weitsman says the existing employees of Murtagh Scrap Handling will be retained and an additional 10 jobs will be created once the scrap yard reopens under Upstate Shredding’s ownership.
MUNICIPAL
Ohio County rejects recycling facility proposals
Medina County (Ohio) commissioners accepted a recommendation from a special bid team to reject proposals from two companies to operate the Medina County Central Processing Facility (CPF).
The CPF is a mixed-waste processing plant that handles solid waste collected from Medina County. Cleveland-based Envision Waste Services has operated the plant for the past 21 years. Its contract with Medina County expired Jan. 11, 2015.
Envision and another Medina-based company, Vexor, submitted bids to operate the CPF under a new contract. But, based on the recommendation of GT Environmental Services, Stow, Ohio, Medina County Commissioners Adam Freidrick and Steven Hambley passed a resolution rejecting all bids. The third commissioner, Patricia Geissman, abstained from voting.
According to GT Environmental, the county’s goal was to reduce tipping fees from $61 to $57 per ton while allowing for additional expenses to purchase a fleet and equipment. The county also sought a longer contractual period.
The first bid option, referred to as Option A, retained the status quo. Envison was the only bidder. As part of the bid, $1.4 million of county funds would be directed toward equipment improvements at the CPF. The proposed improvements included adding a process to the end of the mixed-waste processing equipment system but did not include updating or replacing the 21-year-old processing system, a representative from GT Environmental said.
The next option the county issued for proposals, known as Option B, allowed for more innovation and an opportunity for large-scale improvements with an incentive-driven program to maximize recycling extraction, the representative explained.
Envision bid on this option, again proposing to add a process at the end of the existing processing equipment.
Vexor, which produces engineered-fuel blends from secondary industrial materials, including some from the CPF, proposed to completely gut and rebuild the system with new processing equipment.
The GT representative said the proposals involved raising tipping fees. Vexor’s proposal was the most expensive and was eliminated from consideration. He said the bid team also was concerned that Envison’s proposal under Option B would mean the existing equipment would be 31 years old by the time the contract term ended, eliminating it from further consideration.
METALS, LEGISLATION & REGULATIONS
Commodity hedging margin rules go into effect
The sudden bankruptcy of New York-based commodities and derivatives trading house MF Global in 2011 caused problems for several nonferrous scrap traders who had been conducting business with the firm.
Subsequent dialog between traders and the U.S. Commodity Futures Trading Commission (CFTC) has resulted in the development of new hedging margin requirements rules.
Among the scrap traders who communicated with the CFTC about rules changes was Michael Eisner of the scrap metal trading firm Premier Metal Services, Solon, Ohio. (A September 2014 profile of Premier in Recycling Today is available at www.RecyclingToday.com/rt0914-premier-metal-services-profile.aspx.)
Eisner says he was among the parties harmed by the bankruptcy of MF Global and says in the wake of the event he spent considerable effort and raised his voice to help make sure scrap traders who hedge would be better protected in the future.
“When MF Global went down, I saw a lot of things that weren’t right about the terms and conditions with futures commissions merchants (FCMs). We decided to become proactive and met with the CFTC,” Eisner told Recycling Today for the September 2014 profile.
“We were successful in getting a lot of things changed,” Eisner said.
“We hedge strictly for risk management, not to make money,” Eisner continued. “The way things were set up, the money we had on account was at risk when it shouldn’t have been. The changes are for the better, but to enact those changes we had to involve the CFTC, several U.S. senators and congressmen,” he said.
The text of the final rules changes as they have been enacted by CFTC can be found at www.cftc.gov/ucm/groups/public/@lrfederalregister/documents/file/2013-26665a.pdf.
LEGISLATION & REGULATION
Sims Group settles enforcement action at California plant
Sims Group USA has agreed to pay nearly $2.4 million to settle a civil environmental enforcement action resulting from an investigation of its Redwood City, California, facility by California’s Department of Toxic Substances Control’s (DTSC) Office of Criminal Investigations (OCI).
Sims says the agreement is a “Stipulation for Entry of Judgment and Order” in settlement of claims related to the alleged dispersal of light fibrous materials (LFM) from the Redwood City metal shredding facility.
According to a statement issued by Sims, though the company has agreed to voluntarily settle the matter through the stipulation, it has not admitted to any of the allegations or claims made in the complaint or stipulation. The company maintains that, contrary to the allegations, LFM is a process-related material, not a waste, and that potential off-site dispersal of this material is regulated by the Bay Area Air Quality Management District under new regulations applicable to metal processing facilities and other district regulations.
The California Attorney General’s Office filed the civil action and negotiated the settlement on behalf of the DTSC, which alleges that Sims Group’s facility released LFM, some of which ended up at nearby properties.
DTSC claims that some of the LFM contains cadmium, copper, lead and zinc at levels that exceed hazardous waste regulatory thresholds and are considered toxic. The agency says the release, migration, deposition and accumulation of the waste outside the facility constitute the unlawful disposal of hazardous waste and a failure to minimize the possibility of a release of hazardous waste.
“The control of hazardous pollution that falls from the air and accumulates on the ground is an important enforcement initiative for DTSC,” says Miriam Ingenito, DTSC acting director. “The enclosure of the Sims facility will further protect the community and the environment by controlling the releases of metal-contaminated waste from the shredding operations.”
Sims reports that the company had implemented extensive best management practices to control LFM from its operations well before reaching the agreement but agreed as part of the settlement to implement additional control measures.
Sims also says the focus of the settlement is on the completion of those additional control measure upgrades specified in the agreement. The company has committed to spending at least $1.44 million for this purpose.
Under the settlement, Sims will pay nearly $2.4 million, of which:
- $825,000 will be allocated to DTSC in civil penalties and reimbursement of DTSC’s investigative costs;
- $125,000 will be allocated to the Environmental Enforcement and Training Account Program as a supplemental environmental project; and
- $1,443,814 or more will be allocated to upgrade the Redwood City facility beyond current regulatory requirements.
Sims says it already has implemented several of the upgrades, including installing additional windscreen and fencing at the facility, enclosing and modifying the layout of certain conveyors that were not already enclosed and completing the enclosure of two buildings that were partially enclosed. In addition, Sims committed to installing structures around the metal shredder mill and certain metal separation equipment that are designed to contain LFM that might otherwise be dispersed from that equipment.
Pending completion of these facility upgrades, Sims will conduct weekly inspections of off-site areas for LFM and, if present, remove and properly dispose of LFM it finds.
The agreement states that any LFM that might be released during the time required to complete the upgrades should not exceed the standards set forth in the Bay Area Air Quality Management District Permit.
Sims says it remains committed to environmental stewardship and improvement at its Redwood City facility and that for the past several years, it has been engaged in a continuous improvement program that has resulted in the implementation of a number of other facility upgrades which have significantly reduced the off-site dispersal of LFM.
MUNICIPAL
Organizations name top 10 household recyclables
With the national recycling rate slightly above 34 percent, Americans have the opportunity to capture more material for recycling, according to a number of national recycling organizations. Common barriers to recycling, however, include confusion about what can be recycled.
Keep America Beautiful (KAB), the National Waste & Recycling Association (NW &RA) and the Solid Waste Association of North America (SWANA) together with the U.S. Environmental Protection Agency (EPA) have partnered on an initiative to help make recycling requirements clearer and easier to follow. The first effort in this program is the “Top 10 in the Bin” list of the most widely and easily recycled items in America.
These organizations say they worked with their constituents and recycling experts from the industrial, government and nonprofit sectors to arrive at the “Top 10 in the Bin” list, which will be used by their members and affiliates as a platform for education and communication about recycling in their respective communities.
A 2014 NW&RA national survey found that one-third of Americans are not clear on what materials go in recycling bins and carts. NW&RA President and CEO Sharon H. Kneiss says, “Recycling and recycling technology have come a very long way in the past decade. However, it is still important to avoid contaminating the stream with items that don’t belong there. There is demand for high-quality recyclable material that can be turned into new products, but the key is ensuring that there are consistent, clean recyclables.”
A series of “Top 10 in the Bin” infographics were made available in advance of KAB’s America Recycles Day, which takes place annually on and around Nov. 15. The “Top 10 in the Bin” infographic is available to be downloaded as a flyer or poster. Web banners also are available in different sizes. The “Top 10 in the Bin” files are available at www.americarecyclesday.org/toolkit.
METALS, LEGISLATION & REGULATIONS
ISRI says state laws reflect industry efforts to end metals theft
As National Crime Prevention Month drew to a close in October, the Institute of Scrap Recycling Industries (ISRI), Washington, touted the growing use of ScrapTheftAlert.com as a victory in the fight against metals theft. According to ISRI, in addition to the more than 18,000 registered users, including more than 7,500 law enforcement officials, six states have signed laws requiring use of the alert system.
“ScrapTheftAlert.com is a proven and successful tool for law enforcement, private security and the recycling industry as we work together to stop metals theft,” says ISRI Director of Law Enforcement Outreach Brady Mills. “The more law enforcement officers who register and use the system, the greater the likelihood that recyclers are able to help recover stolen materials. It sends a strong message to thieves that stolen property will be turned away by legitimate scrap yards and thieves will be turned over to police.”
In September, California became the sixth state to codify the use of ScrapTheftAlert.com. California AB 2312 requires all recyclers to register and receive theft alerts from ScrapTheftAlert.com starting Jan. 1, 2015, and encourages local law enforcement to use the system to report metal thefts that occur within their jurisdictions.
Edward Kangeter, CEO of CASS Inc. and president of ISRI’s West Coast Chapter, says, “With the placement of ScrapTheftAlert.com into law as California’s official metal theft reporting system, ISRI has significantly validated its image as an organization of industry members who are committed to solving the problem of metal theft.”
ScrapTheftAlert.com allows law enforcement (and certain corporate security personnel) to post theft alerts that are sent to users within a 100-mile radius of the theft location.
PLASTICS
Sonoco to produce plant-based plastic bottle
Sonoco, a packaging company headquartered in Hartsville, South Carolina, has begun producing the plant-based plastic bottles for a new home care line marketed by Ecover.
“As a leader in the green cleaning space, Ecover sought a packaging partner who could collaborate on sustainable packaging solutions and meet an aggressive commercialization timeline,” says Andrew Moreno, Ecover’s North America’s procurement director. “We also required responsive service and a near-site manufacturing facility to minimize lead times and environmental impact. Sonoco has the ability to provide all of this and perfectly meet our needs. We feel this new line of packaging will help Ecover reach more consumers while continuing to be deeply rooted in nature-based science.”
Ecover’s new packaging line first appeared on store shelves in August 2014 in Sonoco’s extrusion blow-molded bottles made from Plantplastic, Ecover’s blend of biosourced high-density polyethylene (HDPE) and postconsumer recycled (PCR) resin. The bioresin, which is produced using plant-based feedstock and recycled resin collected from municipal curbside programs, uses up to 90 percent less energy and emits 75 percent fewer greenhouse gases compared with petroleum-based virgin resin and is recyclable in most curbside recycling programs, the company says.
“Sonoco is proud to partner with Ecover to become the brand’s HDPE bottle provider in North America, collaborating to produce a fresh new line of bottles,” says Jeff DiPasquale, vice president, Sonoco Blow Molding. “Our material and technical expertise, responsiveness and customer focus created a perfect match between Sonoco and Ecover.”
Ecover has manufacturing plants in Belgium and France and is opening a plant in Chicago that it says is expected to be LEED (Leadership in Energy and Environmental Design) Platinum certified.
METALS
Novelis to convert its beverage can sheet production to Evercan
The aluminum rolling and recycling company Novelis, Atlanta, has announced that it will be converting all of its beverage can body sheet to its Evercan sheet by the end of 2017. The company says Evercan is the world’s first certified high-recycled-content aluminum sheet for beverage cans.
Phil Martens, Novelis president and CEO, says, “Our plan to produce only Evercan body sheet by 2017 is a bold move that extends our leadership in sustainability and is an important part of our long-term strategy to increase the recycled content in our products to 80 percent by the end of the decade.”
The commitment means that all can body sheet produced by Novelis will be certified to contain 90-percent-recycled content compared with the global industry average of 50 percent.
Evercan sheet is produced in Novelis facilities in North America, Europe, South America and Asia. Novelis says it is priced at the same levels as standard beverage can sheet and there is no difference in quality, technical characteristics or run speed at customer plants between Evercan and standard sheet.
“We understand that the shift to a certified, high-recycled-content aluminum beverage can sheet represents a significant change for the industry with far-reaching effects,” Martens adds. “Through an open-sourced platform, we are committed to working with beverage brands, can makers and other aluminum manufacturers to build the closed-loop, low-carbon economy of the future. Accomplishing this change is going to require all of these stakeholders to work together to make the use of recycled materials the standard for the beverage can industry and to increase recycling rates among consumers.”
Novelis says it will help other aluminum manufacturers by sharing knowledge of the process to certify high-recycled content beverage sheet using the methodology of SCS Global Services, the auditing firm that certifies Evercan’s recycled content.
ELECTRONICS
CEA releases study on electronics recycling
The Consumer Electronics Association (CEA), a technology trade association headquartered in Arlington, Virginia, has released a study showing that electronics recycling continues to receive significant support from consumers. The report, titled “Recycling and Reuse Study, 2014 Edition,” shows that 82 percent of U.S. adults say that recycling obsolete electronics is important. The survey also finds that 30 percent of consumers surveyed have recycled electronic products over the past year.
“We’re pleased to see continued consumer support for electronics recycling, especially as the power of innovation brings new and better products to market faster than ever,” says Gary Shapiro, CEA president and CEO. “Our industry has more than doubled the amount of consumer electronics recycling over the past three years. And this study makes it clear that our ongoing consumer engagement and recycling education programs are more important than ever.”
The CEA says the recycling survey, conducted every two years, is part of its efforts to guide the industry’s recycling initiatives. Among the other survey results:
- Fifty-nine percent of U.S. adults know where they can recycle electronics, a slight decline from 2012 (63 percent).
- Almost all consumers surveyed (98 percent) say they would travel some distance to recycle their unwanted electronics, and more than one-third (36 percent) would travel more than 10 miles to do so.
- While 82 percent of consumers say recycling old electronics is important or very important, that total is 4 percent lower than in 2012 (86 percent).
- The percentage of those who discard their electronics also is up, with 18 percent of consumers saying they discarded electronics devices in the trash during the last year, a 6 percentage point increase from 2012.
“Whether it’s through our electronics recycler locator, public service announcements, educational partnerships or the thousands of electronics collection locations our industry sponsors, CEA is committed to empowering consumers to recycle their used electronics,” says Walter Alcorn, CEA vice president, environmental affairs and industry sustainability. “Our industry has now picked up the recycling tab for billions of pounds of old devices—a truly unprecedented effort led by manufacturers of televisions, computers and similar consumer electronics devices.”
PAPER
UFP Technologies expands molded fiber operations
UFP Technologies Inc., headquartered in Georgetown, Massachusetts, has announced the expansion of its North American operations for molded fiber packaging, opening a new location in El Paso, Texas. The company specializes in creating custom packaging, component and product solutions for a range of industries.
UFP says the addition of the El Paso site expands its footprint in the United States and positions the company to meet the growing demand for 100-percent-recyclable molded fiber packaging in Mexico, the Southwest and the western United States. The company uses old newspapers as the basic raw material for its molded pulp product.
“Environmentally responsible molded fiber packaging is a rapidly growing business for UFP Technologies and an important part of our growth strategy,” says R. Jeffrey Bailly, chairman and CEO. “Our decision to locate in Texas was designed to both increase our capacity and better serve our current and prospective customers in that region.”
UFP operates 10 manufacturing facilities in the United States.
MUNICIPAL
One for All program designed to boost recycling in eastern Pennsylvania
Lycoming County (Pennsylvania) Resource Management Services (LCRMS) has celebrated the grand opening of its $5.3 million single-stream material recovery facility (MRF) and the subsequent launch of a new regional recycling program called One for All.
According to Jason Yorks, Lycoming County recycling coordinator, the new single-stream MRF allows residents to recycle more material, including Nos. 1 through 7 plastics and aseptic gable-top containers, such as juice and soup cartons.
The 60,000-square-foot MRF, which is adjacent to the Lycoming County Landfill in Montgomery, Pennsylvania, can sort and bale up to 20 tons per hour of commingled recyclables.
The participating counties in northeastern Pennsylvania include Lycoming, Columbia, Montour, Northumberland, Union and Snyder. Officials say when the facility is running at full capacity it will be able to serve an even larger area.
“Single-stream shifts curbside pickup from the county to private business, which we feel will be a much more efficient system,” says Yorks.
Green Machine Sales, Hampstead, New Hampshire, made and installed the equipment, designed to sort the commingled recyclables. A grant from the Carton Council also helped to purchase equipment that will sort the aseptic gable-top containers.
“With this new facility and program in place, we’ll now be able to preserve valuable landfill space, increase our capacity, have a more cost-effective, convenient way to recycle and hopefully improve local recycling participation,” Yorks says. “For residents, it’s a more convenient way to recycle, and for haulers, it’s an opportunity for business. We see it as a win-win.”
ELECTRONICS
BAN seeks changes enhancing electronics reuse in Basel Convention guideline
The Basel Action Network (BAN), Seattle, and its e-Stewards® recycler/refurbisher certification program say they are currently undertaking two initiatives to promote responsible electronics refurbishment.
The first initiative was introduced at the last Open-Ended Working Group of the Basel Convention in Geneva in September 2014. BAN says it offered an exemption that would allow some high-end electronic equipment, including medical equipment, to be exported outside of the control procedures of the Basel Convention to operators such as Asian equipment manufacturers for refurbishment. BAN says it is seeking “to break the impasse between developing countries and manufacturers” and to reach a “workable compromise to allow some small flows for very responsible refurbishment as long as the residual material from such refurbishment operations would not be allowed to remain in developing countries and violate the international Basel Ban Amendment.”
The second initiative the group is undertaking involves seeking a more liberal interpretation of when a secondhand laptop or phone battery should be considered waste. Currently, the international guidelines require a one-hour minimum charge on laptop or phone batteries. While well-intended to prevent the dumping of lithium-ion batteries, this guideline results in thousands of laptops that could otherwise find a second life as refurbished equipment being shredded and scrapped, the organization says.
The e-Stewards Certification program, created and administered by BAN, with the help of the e-Stewards Technical Committee, will revise and implement a new set of requirements for use in its e-Stewards Standard for testing and minimum state of health for used batteries. This will allow more used batteries to be considered nonwaste and available for reuse, BAN says.
“In BAN’s view, fostering greater reuse rates is compatible with ensuring that developing countries are not used as dumping grounds for electronic waste—a policy position that BAN has promoted for over a decade,” the organization says.
The e-Stewards program recently announced its e-Stewards Marketplace, www.e-Stewardsmarketplace.com, an e-commerce site where refurbishable equipment can be traded among e-Stewards Certified Recyclers and then refurbished and sold to businesses around the world to enhance greater reuse rates, BAN says.
METALS
Potomac Metals to open new facility
The scrap metal recycling company Potomac Metals, headquartered in Sterling, Virginia, has broken ground on a new facility in Ashburn, Virginia.
The new facility, expected to be operational by the first half of next year, will include a 65,000-square-foot building and a 3,000-square-foot mezzanine that will serve the company’s office needs, Potomac Metals says. The facility also will have a customized warehousing component that will allow the company’s operations to be streamlined and will provide room for further growth.
Potomac Metals is primarily a nonferrous scrap metal recycling company with seven locations in the mid-Atlantic region. The company presently has four locations in Virginia, two in Maryland and one in West Virginia.
One of the company’s existing locations is dedicated to handling obsolete electronics.
Mark Zwilsky, owner of Potomac Metals, estimates the company handles from 3 million to 3.5 million pounds of nonferrous scrap per month.
Construction of the building will be led by Merritt Construction Services, a Baltimore-based construction firm. Potomac reports that groundbreaking for the new facility began in late October.
According to Potomac Metals, its new facility will house a heavy-duty two-ram baler equipped with two 100-horsepower motors for processing scrap metal, two full-size truck scales, multiple ground buy/sell scale platforms linked to Potomac Metals’ scale data software and an electric material handler that generates zero emissions.
Potomac adds that the new corporate headquarters will give the company the opportunity to expand its retail, brokerage and processing divisions by a projected staff increase of 15 percent. In addition, the facility’s design and centralized location to Potomac’s other recycling facilities and current customer base will maximize convenience for the company’s retail, commercial and industrial accounts, according to the company.
“Our company researched and interviewed several contractors to build our new facility, but after having the opportunity to tour current and previous Merritt Construction projects and meeting the management team in Virginia—our choice to go with Merritt proved to be easy,” says Zwilsky.
METALS
Texas foundry to expand and modernize
GE Oil & Gas, Houston, has announced plans to invest $60 million to expand and modernize its foundry operations in Lufkin, Texas. The Lufkin foundry produces iron castings, which are used to make Lufkin beam pumping units and Lufkin power transmission equipment.
GE says it plans to demolish 30,000 square feet of the foundry’s existing 515,000 square feet and construct 72,000 square feet of new buildings. The company also plans to refurbish the remaining facilities at the site.
The Lufkin foundry originally began operating in 1902. GE notes that while the foundry has been upgraded over time, the investment would provide the site with modern technology and practices to reduce emissions and boost production efficiency in an increasingly competitive global marketplace.
“We chose to invest in modernizing and improving our existing foundry because of the rich history and dedicated, skilled workforce associated with the Lufkin operation here in Texas,” says Jerome Luciat-Labry, president of Well Performance Services for GE Oil & Gas. “The goal is to make the facility as efficient as possible and help strengthen the competitive position of our business around the world. We are excited about continuing to support manufacturing jobs in the United States and especially here in Angelina County, where Lufkin Industries began.
“By having its own foundry, GE Oil & Gas has a strategically integrated supply chain that allows the company to more rapidly meet the needs of its customers, particularly in the fast-growing unconventional oil and gas sector,” continues Luciat-Labry.
As currently proposed and pending government approvals and permits, construction would be carried out in four phases commencing in 2016. Under that schedule, construction is expected to be completed in about three years, the company says.
The foundry manufactures gray and ductile iron castings. It is capable of producing about 72,000 tons of gray and ductile iron castings each year. About 87 percent of the foundry’s products is used to supply GE’s own Lufkin factories, while the remainder is sold externally to other customers.
METALS
Texas foundry to expand and modernize
GE Oil & Gas, Houston, has announced plans to invest $60 million to expand and modernize its foundry operations in Lufkin, Texas. The Lufkin foundry produces iron castings, which are used to make Lufkin beam pumping units and Lufkin power transmission equipment.
GE says it plans to demolish 30,000 square feet of the foundry’s existing 515,000 square feet and construct 72,000 square feet of new buildings. The company also plans to refurbish the remaining facilities at the site.
The Lufkin foundry originally began operating in 1902. GE notes that while the foundry has been upgraded over time, the investment would provide the site with modern technology and practices to reduce emissions and boost production efficiency in an increasingly competitive global marketplace.
“We chose to invest in modernizing and improving our existing foundry because of the rich history and dedicated, skilled workforce associated with the Lufkin operation here in Texas,” says Jerome Luciat-Labry, president of Well Performance Services for GE Oil & Gas. “The goal is to make the facility as efficient as possible and help strengthen the competitive position of our business around the world. We are excited about continuing to support manufacturing jobs in the United States and especially here in Angelina County, where Lufkin Industries began.
“By having its own foundry, GE Oil & Gas has a strategically integrated supply chain that allows the company to more rapidly meet the needs of its customers, particularly in the fast-growing unconventional oil and gas sector,” continues Luciat-Labry.
As currently proposed and pending government approvals and permits, construction would be carried out in four phases commencing in 2016. Under that schedule, construction is expected to be completed in about three years, the company says.
The foundry manufactures gray and ductile iron castings. It is capable of producing about 72,000 tons of gray and ductile iron castings each year. About 87 percent of the foundry’s products is used to supply GE’s own Lufkin factories, while the remainder is sold externally to other customers.
METALS
Alcoa sells its ownership stake in Century Aluminum
The aluminum firm Alcoa, headquartered in New York, has reached an agreement to sell its ownership stake in the Mount Holly aluminum smelter in Goose Creek, South Carolina, to Century Aluminum Co., headquartered in Chicago, for $67.5 million in cash, plus an additional potential earn-out. Alcoa presently owns 50.3 percent of Mount Holly, while Century owns 49.7 percent.
“While Mount Holly is a strong facility, its cost structure doesn’t match Alcoa’s criteria for a low-cost portfolio of upstream assets,” says Bob Wilt, president of Alcoa Global Primary Products. “The sale will help achieve Alcoa’s strategy to optimize its commodity portfolio and protect the facility’s jobs and economic contribution to the local community. We would like to thank our community stakeholders and the employees of Mount Holly for their years of support.”
The smelter has a capacity of 229,000 metric tons per year.
The divestiture will reduce Alcoa’s global smelting capacity to 3.5 million metric tons per year, the company notes.
Alcoa says the sale is aligned with its strategy to create a globally competitive commodity business and lower its position on the world aluminum production cost curve to the 38th percentile by 2016. Including this announcement, Alcoa has curtailed, closed or sold 1.3 million metric tons, or 31 percent, of its highest-cost global smelting capacity since 2007.
ELECTRONICS
Recleim and Pepsi Bottling Ventures announce recycling agreement
Recleim LLC, headquartered in Atlanta, has announced that it will serve as the recycling services provider for Pepsi Bottling Ventures (PBV), the largest privately held Pepsi-Cola bottler in North America.
PBV will work with Recleim to properly dispose of retired cold drink vending machines, fountain units, glass door merchandisers and other parts and components.
Founded in 2012, Recleim provides recycling and resource recovery for refrigerators, other appliances and related electronic scrap. The company says its exclusively licensed recycling technology enables it to recover 95 percent of PBV equipment by weight.
“Pepsi Bottling Ventures is committed to protecting the environment and that means ensuring our machines are recycled according to the highest standards,” says Roy Taylor, marketing equipment manager at PBV. “Recleim has the technology and process in place to maximize the amount of materials recovered from the items we retire. Our objective is to work with a company that shares our passion for responsible stewardship of the environment.”
Under the agreement, Recleim will transport retired equipment from PBV’s central distribution center in Winston-Salem, North Carolina, to its flagship recycling plant in Graniteville, South Carolina, for processing. Recleim also will provide PBV with a certificate of destruction, a traceable document that guarantees all goods received by Recleim are recycled in a way that meets or exceeds federal, state and local requirements, the company says.
“Companies want to feel confident that when they recycle equipment and parts, it will be done right,” says Doug Huffer of Recleim.
He adds, “Since not every recycler has the same capabilities, it’s crucial to work with one that can reduce the release of harmful substances—such as chlorofluorocarbons—into the environment. We provide that level of assurance, which is why companies like Pepsi Bottling Ventures turn to us for their recycling needs.”
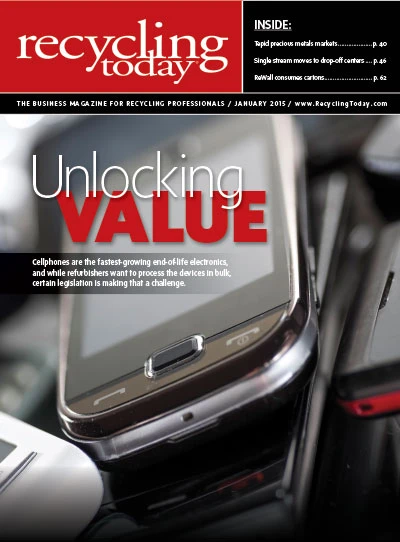
Explore the January 2015 Issue
Check out more from this issue and find your next story to read.
Latest from Recycling Today
- Electrolux commits to recycled content
- Duesenfeld system targets battery cell scrap
- Hyundai says it will make steel in the US
- APR announces Recycling Leadership Award winners
- Glass Half Full opens glass recycling facility in Louisiana
- AmpUp partners with Roundtrip EV
- Global Recycling Day event supports Pittsburgh school's recycling efforts
- President signs executive order on critical minerals