Covanta is known as one of the world’s largest operators of facilities dedicated to recovering energy from waste as well as to providing other waste disposal and recycling services.
The company, a subsidiary of the publicly owned Covanta Holding Corp., owns and/or operates 45 energy-from-waste (EfW) facilities that produce electricity for approximately 1 million homes in communities across North America.
The company’s EfW facilities are designed to integrate with municipal solid waste (MSW) systems to maximize the recovery of energy from waste via a complete combustion process. The company also is recovering metals that are byproducts of its combustion process.
Covanta reports that its North American facilities are converting 20 million tons of trash and residuals annually into 9 million megawatt-hours of clean, renewable energy and more than 9 billion pounds of steam sold to a variety of industries.
Unlike incineration, Covanta’s is a complete combustion process that burns MSW as the primary fuel source for energy in specially designed boilers. The controlled combustion process uses state-of-the-art pollution control equipment to scrub emissions and prevent them from being released into the environment, according to James Regan, corporate communications and media relations manager for Covanta.
The EfW process ultimately produces a combined ash comprising two of the byproducts of the EfW process: the bottom ash that remains after combustion and air pollution control residue. The bottom ash that remains after combustion—which comprises approximately 10 percent of the original waste stream by volume—contains valuable ferrous and nonferrous metals. Covanta recovers these metals by retrieving them from the bottom ash that remains at the end of the process. By recovering these metals, recycling rates are improved in the communities that Covanta serves, the company says.
The amounts of metals present in the ash are significant: Annually, Covanta’s EfW facilities recover about 430,000 tons of ferrous and more than 15,000 tons of nonferrous metals from the ash for recycling. That’s the equivalent amount of steel needed to build five Golden Gate bridges and the amount of aluminum in more than 1 billion beverage cans, Regan points out. The company has reported that all U.S. EfW facilities combined, including its own, are recovering more than 700,000 tons of metals for recycling annually. Covanta estimates that some 250 million tons of trash—containing metals—are still going to landfills every year in the U.S. Approximately 3 percent of the waste stream is metal, Covanta says, so potentially 7.5 million tons of metals are lost.
While Covanta’s proportion of about 450,000 tons of ferrous and nonferrous metals seems substantial, the company’s managers learned in 2013 that they could be doing more.
Increased recovery
Steve Bossotti, vice president of organic growth and innovation for Covanta, says increased metal recovery has in fact been one objective named in the company’s strategic organic growth initiatives rolled out in recent years. Covanta has highlighted the need to recover more ferrous as well as nonferrous metals from the bottom ash, Bossotti says.
“Two years ago we launched an organic growth initiative to recover more metals,” Bossotti says. Initially, the project was focused on increased nonferrous recovery across Covanta’s locations. Nonferrous metals were previously being recovered at fewer than half of Covanta’s facilities, so the company set up a program for added equipment companywide to recover the as-yet untapped nonferrous stream.
Wheelabrator teams with Inashco Rotterdam-based Inashco and Wheelabrator Technologies Inc., headquartered in Hampton, New Hampshire, are constructing a demonstration facility for the recovery of metals from energy-from-waste (EfW) ash in New England under a new North America-based joint venture company, Eco Recovery Solutions LLC (ERS). The two companies are 50/50 owners of the joint venture. According to a press release issued by the companies, ERS is dedicated to the recycling of ferrous and nonferrous metals from the waste-to-energy (WTE) process. ERS will use Inashco’s patented advanced dry recovery (ADR) technology to enhance the recovery of ferrous and nonferrous metals at WTE facilities. Nonferrous metals will include copper, zinc, lead and aluminum as small as 0.5 millimeters in size, the companies report. Wheelabrator says it selected the Inashco technology because of its proven track record and its ability to process fresh ash without aging that can result in oxidation and diminished product values. ERS says it will benefit from the use of Inashco’s specialized, proprietary central upgrading facilities currently located in Europe and planned for the U.S. According to the companies, the recycling process produces two streams of high-value material: a heavy nonferrous product and a light nonferrous product for sale to Fondel Metals, Inashco’s parent company. ERS also says it plans to develop aggregate reuse opportunities with the improved ash residue downstream of the ADR process with the ultimate goal of a circular economic solution for ash management. John Joyner, president of Inashco North America, observes, “This venture with Wheelabrator will establish the foundation for the deployment of a new, disruptive technology that will bring environmental benefits and enhanced economics to the waste-to-energy industry.” Mark Weidman, president of Wheelabrator Technologies, says, “This joint venture will allow us to recover significantly more recyclable materials to help preserve our world’s finite environmental resources.” According to Weidman, Wheelabrator recovered and recycled 142,000 tons of ferrous and nonferrous metals in 2013. |
As part of that process, Bossotti and Project Engineer Rich Molter conducted ash tests at some locations to determine the amount of metals remaining in processed bottom ash.
“We realized some of our facilities still had a percentage of ferrous left in the ash,” Bossotti says. That was surprising, he says, because virtually all Covanta facilities were already set up to recover ferrous metals using a variety of equipment, including various electromagnetic drums, overband magnets or permanent magnets.
One facility, though, stood out among the others as having less ferrous content in the processed bottom ash. That was the company’s Delaware Valley plant in Chester, Pennsylvania, which had upgraded its ferrous recovery in recent years, having previously installed a P-Rex permanent rare earth magnet from equipment company Eriez, based in Erie, Pennsylvania.
“When we looked at the performance of our facilities, Delaware Valley stood out as a better performer,” Bossotti explains. “We tried to understand what made them different, and we found it had a rare earth magnet,” he adds.
A natural progression of that discovery, Bossotti explains, was having reason to believe there were missed ferrous opportunities and room for improvement across other Covanta locations as additional performance comparisons continued to indicate recovery differences.
“The ash testing that we did to determine the nonferrous content revealed there was ferrous opportunity, and with the rare earth magnet quality, we realized we could capture it,” Bossotti says.
Bossotti and Molter concluded that some locations had outdated equipment and upgrades would provide opportunity for Covanta and its clients.
Based on the company’s experience in Delaware Valley, its knowledge of how the rare earth magnet performed and the desire to pull material in a way that would allow for maintaining a proper working gap to avoid operational issues, in early 2013 Covanta decided to purchase another rare earth magnetic scrap drum. This time the company’s Niagara Falls, New York, facility was selected for upgrading.
“Our ash testing indicated it would be a good place to start, and the facility was excited to do so,” Bossotti recalls.
The results in Niagara Falls, Bossotti says, were almost instantaneous. “Literally the day we turned it on, there was a considerable increase in ferrous recovery,” he says, explaining that Covanta’s engineers saw a 50 percent improvement in recovery. Those results convinced Bossotti and Molter to continue looking for other upgrade opportunities across the Covanta locations.
“We were so impressed by it at the two facilities, we wound up buying four more,” says Bossotti. In fact, Bossotti adds, the company has decided to replace some scrap drums in other locations, starting with Covanta’s bigger facilities.
Considered factors
A key advantage with the rare earth magnet, Bossotti explains, is that because of the drum’s magnetic strength, it can be installed with a greater gap between the conveyor and the drum, where it’s better able to deal with the widely varying sizes of metal objects remaining in Covanta’s bottom ash.
He explains that closer gaps traditionally cause large objects—something like an iron safe—to potentially become wedged between the belt and the magnet, leading to an equipment jam or damage. “The natural thing to do is to set the gap higher than what will cause problems,” he explains.
“With rare earth magnets, I can keep a gap greater than 9 inches, and it can still pick up the material, so that has a real competitive advantage for me,” Bossotti explains. “I’m not wrecking conveyors, and my operator’s not dealing with jams.”
With conventional scrap drums, he adds, “for me to get the same pickup, I would have to get the magnet a lot closer, but then ugly things can happen.”
Another key benefit of rare earth magnets, Bossotti says, is the fact that its magnetic force remains consistently strong across the width of the drum. “With some magnets, the force in the middle is greater.” That means ferrous materials located at the sides of the conveyor belt might not get picked up, Bossotti says.
“Rare earth magnets allow you to get material across the full width,” he adds.
Bossotti now says, as a result of its testing, a variety of upgraded magnets, including some P-Rexes, have been selected for various Covanta locations depending on the increased recovery they will yield, and more are expected to follow.
Bossotti says new magnets in general are an important part of Covanta’s overall goal for improving its ferrous recovery going forward.
“We looked to upgrade six more facilities, and rare earth magnets will be a part of that equation,” he says.
Meldgaard recovers metals from WTE ash Capturing ferrous and nonferrous from waste-to-energy (WTE) ash is a growing business around the world. It also is an evolving business with more powerful magnets being continuously developed and more elaborate systems being designed every year.
The company says a significant difference between European and American WTE ash is that in Europe the bottom ash is kept separate from the fly ash, while in the U.S. the WTE ash is typically combined, leading to ash recycling challenges when dealing with the lime content of the fly ash—a challenge that Meldgaard says it rose to with detailed designs for advanced ash handling processes. The company now has three operating ash recycling plants in the U.S., each one slightly different because ash is different from each WTE plant. Each plant also is processing ash at a different stage in the ash handling process, either directly from the plant without any buffer storage through to processing on monofills with ash being stockpiled for several weeks. Meldgaard’s latest ash recycling plant is integrated into the ash handling system of the WTE plant so it does not interfere with ash removal for disposal. “The trucks loading the ash have no idea we have already extracted the valuable metals from the ash to share with the WTE plant operator,” the company explains in a press release. Meldgaard says it wasn’t an easy feat to accomplish because 500 tons of ash are delivered daily by conveyor straight from the WTE plant to Meldgaard’s feed hopper. That ash is still moist and fresh from the ash bunker, making it difficult for current U.S. recyclers to process. However, by drawing on its more than 20 years’ experience in designing and operating ash recycling systems, Meldgaard says it was able to develop a unique system for the ash processing and is now extracting record levels of nonferrous metals. With a throughput of nearly 200,000 tons per year, the company says it is proud to have designed, manufactured and installed this Danish ash recycling plant on American soil and looks forward to using the technological systems it has developed for additional U.S. facilities. |
The author is an editor with the Recycling Today Media Group and can be reached at lmckenna@gie.net.
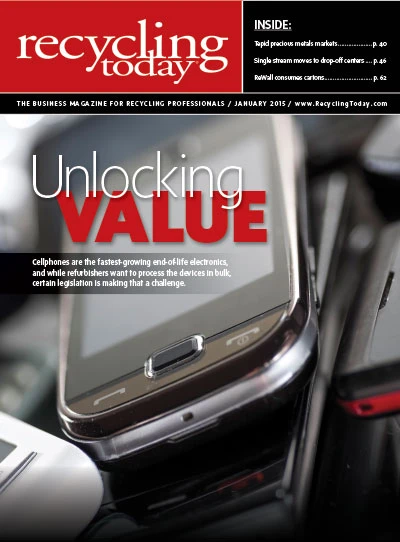
Explore the January 2015 Issue
Check out more from this issue and find your next story to read.
Latest from Recycling Today
- APR announces Recycling Leadership Award winners
- Glass Half Full opens glass recycling facility in Louisiana
- AmpUp partners with Roundtrip EV
- Global Recycling Day event supports Pittsburgh school's recycling efforts
- President signs executive order on critical minerals
- Registration opens for Scrap Expo 2025
- Toyota opens ‘circular factory’ in UK
- Agilyx works with former Plastic Energy CEO on sourcing venture