General Kinematics, MetalTech install equipment at North Carolina C&D recycling facility
MetalTech Systems, Pawleys Island, South Carolina, and General Kinematics, Crystal Lake, Illinois, have completed the installation of a construction and demolition (C&D) recycling system at Green Recycling Solutions in Maysville, North Carolina. Green Recycling Solutions held a ribbon-cutting and dedication ceremony to commemorate the event Nov. 6, 2014. Approximately 100 state and local officials attended a luncheon following the ceremony.
Paul Hanna, MetalTech Systems president and Thomas Musschoot, General Kinematics vice president, also attended the celebration.
The C&D recovery system the companies installed includes picking stations and quality control stations.
Green Recycling Solutions began accepting material for processing Nov. 20.
Founded in 2010, Green Recycling Solutions says it is committed to becoming the premier destination for C&D debris. The company’s operation includes a C&D landfill, a recycling facility and a roll-off company. The C&D landfill was scheduled to open in December 2014.
BACE to relocate headquarters
BACE, a manufacturer of balers and compactors for the recycling and waste management industries, has announced plans to relocate its corporate headquarters within Charlotte, North Carolina. Additionally, the newly acquired building will include 90,000 square feet of manufacturing space.
The company says it expects to complete the move by March 2015.
BACE President Matt Hatfield says, “At a time of continuing economic uncertainty and caution, our abiding commitment to customer service and satisfaction—combined with new products and patent-pending technology—is helping us grow in size, scope and reputation. We’re grateful to our expanding customer base and our partnerships. We look forward to providing even greater service and responsiveness from our new facility.”
Liebherr expands its worldwide spare parts distribution operations
Liebherr, Newport News, Virginia, has recently announced several developments that it says are helping to shape its global, local and regional spare parts distribution and logistics.
The company says its expansions will support Liebherr’s rapid growth and exceed customer-service expectations around the world.
The Liebherr Group has announced several positive developments that have an impact in the fulfillment and distribution of earthmoving Liebherr spare parts globally and within the United States.
In October 2014, the Liebherr Group gave a glimpse into the progress of its new spare parts and logistics center in Kirchdorf, Germany. The state-of-the-art facility is scheduled to begin operations in early 2015 and is expected to serve as its global logistics hub for earthmoving spare parts, the company says. The investment value for the first stage of construction is in excess of $143 million and covers an area more than 505,000 square feet. A large part of the investment has gone into implementing automated warehouse equipment and software that will enable the logistics center to employ leading-edge performance standards, the company says. The new warehouse solutions will allow the group to handle higher volumes of spare parts, reduce turnaround times and guarantee order accuracy for Liebherr customers around the world, according to Liebherr.
Additionally, the Liebherr Group is continuing a significant investment in building improvements, machinery, tools and infrastructure to expand the factory and enhance the warehouse at its Newport News location. These renovations are part of a $45.4 million investment, according to the company.
The Newport News location serves as the headquarters and central warehouse for the Liebherr Mining Division as well as for four other operating Liebherr companies, including Liebherr Construction Equipment Co. Major warehouse overhauls include the implementation of a warehouse management system (WMS). A wide range of process-improvement initiatives consist of a new racking system, more than 100,000 square feet of new epoxy floor and eight additional loading docks to speed up the traffic and help with the flow of trucks loading and unloading materials at the facility.
“The new WMS offers a multitude of functions that will optimize the overall logistics and support the daily operations of the facility ... it will provide a transparent work flow and enhance the visibility of the activities at each of the warehouse terminals, from receiving through shipping, in addition to providing inventory accuracy,” says Martin Seitz, WMS project coordinator, Liebherr Mining Equipment.
In addition, Liebherr Construction Equipment, responsible for the sales and distribution of the full line of Liebherr earthmoving and material handling equipment in the U.S., has announced the opening of a new spare parts facility in Visalia, California. The depot is expected to begin operations in early 2015, according to the company, and the facility will support western U.S. distribution with localized parts warehousing.
The National Parts Distribution Center in Newport News, along with its new distribution center in California, will help expedite parts orders, improve operational efficiency and minimize transit time while increasing customer support, according to Liebherr.
American Baler expands dealer network
Tade Mahoney at American Baler Co., Bellevue, Ohio, has announced the addition of two experienced sales and service providers to the company’s dealer network.
Greg Matheson and his colleagues at Recycle Systems of Kirkland, Washington, bring many years of baler sales and service experience in the Northwest U.S., according to American Baler. The company can be contacted by phone at 888-453-9300.
Mike McChrystal and his team at OBC, Cleveland, will assume responsibility for Ohio, Detroit, eastern Kentucky, western Pennsylvania and western New York. OBC can be contacted by phone at 855-744-4622.
Mahoney says, “The addition of these two well-respected dealers will greatly increase our visibility in the marketplace.”
American Baler, founded in 1945, is an Avis Industrial company.
CieTrade introduces mobile application
Stamford, Connecticut-based cieTrade, a provider of business management software for commodity trading and recycling companies, has introduced eDock, a mobile app designed for its suite of specialized productivity tools for recycling companies. The company says eDock eliminates paper breakdown sheets and shipping logs commonly used in recycling plants, allowing warehouse personnel to process and grade inbound loads and outbound shipments with a mobile touchscreen app that can be used directly from the loading dock or scale-enabled forklift.
“With today’s markets, recyclers are looking for every possible way to increase the productivity and effectiveness of their operation,” David Haber, president of cieTrade Systems Inc., says. “EDock helps by seamlessly integrating warehouse loading operations with your back office to save time, eliminate double-entry of data and minimize pricing, grading or other errors.”
The eDock app uses a touchscreen console interface that can be run from any Windows tablet, such as the Panasonic ToughPad, the company says. It offers weigh-bridge (truck) and floor scale integration, supports barcoding technology to tag inbound material and scan outbound loads and captures photos to document quality issues. It also produces documentation such as scale tickets, packing lists, bills of lading and more.
EDock works as an extension of cieTrade’s namesake commodity trading and recycling software and is provided for the benefit of clients using its system, according to the company.
More information is available at www.cietrade.com.
Ely Enterprises offers Safetech conveyor safety system
Ely Enterprises Inc., Lorain, Ohio, now offers the Guardian automatic personnel protection system, developed and refined by U.K.-based Safetech, to recycling industry customers throughout the United States.
The system “offers unique protection against accidents involving industrial conveyors and access points leading to hazardous machinery,” Safetech says.
The Guardian system is designed to prevent injuries with minimal operating cost, to reduce insurance premiums and to protect workers even if they are trapped, concealed, unconscious and/or injured. Safetech says the system allows uninhibited flow of material on conveyors and offers rugged construction suitable for harsh industrial environments.
More information is available at www.elyenterprises.com.
Benlee adds safety features
Benlee, a Romulus, Michigan-based manufacturer of roll-off trailers, has added safety features to its trailers and trucks in light of recent industry safety issues or incidents involving power lines and bridges.
The company’s new “Danger” plaque that measures 12 inches square is mounted behind the controls, and reads “Look Up!”
Benlee says the plaques will be provided at its cost of $25 and also includes a bracket. Benlee also reports it is making standard upward/rearward facing work lights on all tarp systems, including Benlee, Roll Rite and others, which will help the operator see overhead power lines in the dark. These tarp lights will be provided at Benlee’s cost of $95 and include two lights and a hoist up switch.
The company reports seeing disabled hoist up alarms on many roll-off trucks brought to its service operation. In light of this safety concern, Benlee says it now requires every driver to sign a document stating he or she is aware the alarm is disabled and does not want it fixed or that he or she wants the company to repair it.
While hoist up alarms are already standard on all Benlee roll-off trucks, the company is increasing its hoist up safety standard by adding a blinking light that is visible in the driver’s rearview mirror. It will be activated by a hoist up switch. These can be ordered at Benlee’s cost of $80, according to the company.
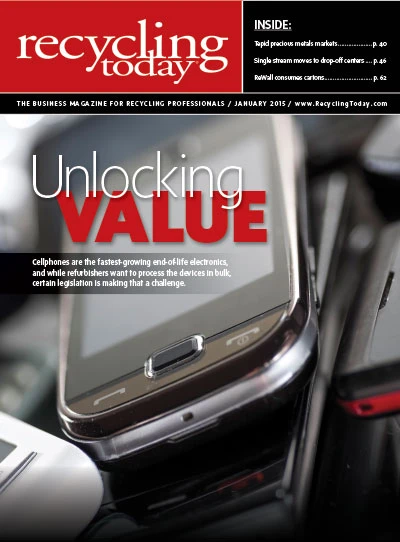
Explore the January 2015 Issue
Check out more from this issue and find your next story to read.
Latest from Recycling Today
- Electrolux commits to recycled content
- Duesenfeld system targets battery cell scrap
- Hyundai says it will make steel in the US
- APR announces Recycling Leadership Award winners
- Glass Half Full opens glass recycling facility in Louisiana
- AmpUp partners with Roundtrip EV
- Global Recycling Day event supports Pittsburgh school's recycling efforts
- President signs executive order on critical minerals