The 2014 China Nonferrous Metals Industry (CNIA) Association Recycling Metal Branch (CMRA) Annual Convention was Nov. 7-9, 2014, at the Dongfang Hotel in Guangzhou, China. The event’s theme was “confidence, transformation, upgrading, innovation and development,” and 23 speakers were invited to analyze opportunities and challenges facing the nonferrous recycling industry.
Favorable but not fantastic
The world needs scrap materials, but that does not mean business conditions consist solely of clear sailing. That was the message from two recycling organizations at the 2014 CMRA Annual Convention.
Scott Horne of the Institute of Scrap Recycling Industries (ISRI), Washington, noted that while the United States has experienced two straight quarters of gross domestic product (GDP) growth, one need only go back to the first quarter of 2014 to find a quarter with negative GDP growth.
Regarding global economic conditions, Horne indicated the International Monetary Fund (IMF) forecasts declining GDP numbers in the European Union and in Japan for 2014 and 2015.
The IMF and other forecasters continue to forecast China growing in the 5.5 to 7 percent range, however, China’s purchasing managers index (PMI) for future activity has flattened considerably, Horne noted.
In the United States, Horne said the light-vehicle industry has returned as an important generator and consumer of scrap metals. However, the housing market in the United States “remains bumpy at best,” he commented.
The health of the U.S. auto industry alone has not been enough to stave off the falling value of metals. At the same time, scrap processors are contending with lower steel and ferrous scrap prices, and they also are buying and selling in an environment where copper has lost 10 percent of its value in recent months.
Horne also remarked that developing nations throughout Asia are beginning to close their scrap supply deficits. He said one recent study forecasts China to be self-sufficient for red metal (copper) scrap by 2023.
Other forecasts see China becoming a net exporter of ferrous scrap within the next several years as its auto industry grows and as structures built since its post-1980 economic revival begin to enter the demolition cycle.
The previous 20 years have been marked by an incredible flow of secondary commodities from the United States to China, with China purchasing $145 million of these materials in 1993 and $9 billion worth in 2013, Horne said.
Seeking quicker clearance China’s customs agency is testing a pilot system in Guangdong Province to cut down on imported scrap container wait times. At a recycling conference in late 2014, a representative from China’s General Administration of Customs (GAC) acknowledged that scrap traders are running into bottlenecks at Chinese ports and outlined one measure the agency is taking to try to alleviate the situation. Chen Zejun of the GAC’s Guangzhou Merchandise Valuation and Information Office said the GAC is “focusing on fast declarations and customs clearance” in Guangdong province. A pilot project in that South China province is known as the “one declaration” system. “In the past it might take two days to two weeks with three different procedures involved,” Chen said of customs clearance. “We are trying to go faster with this model. You only need to declare [your inbound shipment] once, and then immediately examination and clearance will start—at the same time, not one-by-one in sequence,” said Chen. Traders gathered at the convention commented that the pilot system has the benefit of eliminating the need to unload and reload a container more than once for different inspections. However, it still can entail a wait time while trying to schedule inspectors from the GAC and the General Administration of Quality Supervision, Inspection and Quarantine (AQSIQ) to arrive at the same time. Scrap exporters from Europe and North America expressed discontent with China’s costly inspection regimes overall, citing redundancy between requirements and inspections of the GAC, AQSIQ, the Ministry of Environmental Protection (MEP) and the CCIC (China Certification and Inspection Group), which inspects shipments bound for China before they leave ports in other parts of the world. Chen, who has worked on scrap-related issues for the GAC, said, “I feel very close to this industry and have a deep understanding of the industry.” She outlined a series of rights and obligations attached to GAC and to scrap importers, including importers’ rights to seek quick clearance of their containers and to negotiate the value of their shipments. Chen suggested that importers continue to put in the effort to understand customs procedures and provide “true declarations” for every shipment. Both the GAC and importers need to “fight against fraud in order to safeguard fair competition and prevent market disorder,” Chen said. |
Ma Hanchang, the consultant for Chinese affairs to the Bureau of International Recycling (BIR), Brussels, said the recycling industry now collects, processes and consumes about 800 million metric tons of material each year. It employs at least 1.6 million people worldwide, though Ma indicated that figure is probably low in that a comprehensive employment figure from China is not available.
Ma cited trade barriers (such as high tariffs and export bans) as one of the major challenges facing recyclers, along with potential threats to free competition and global trade in the form of extended producer responsibility (EPR) systems.
On a more positive note, Ma said the savings in natural resources, energy consumption and reduction in CO2 (carbon dioxide) emissions means recycling has a secure place in the global economy of the future.
Several challenges in China
Despite recycling’s secure place in the global economy and the Chinese central government’s pledge of support for a recycling-friendly “circular economy,” secondary nonferrous metals producers in that nation may need every ounce of that support to make it past several current challenges.
Ren Xudong of the CNIA referred to “bottlenecks” restricting the growth of secondary metals production in China, including those involving “resource availability [and] environmental stress.”
Li Shilong, vice president of the Beijing-based CMRA, said many of China’s metals production and recycling companies “have met financing difficulties” and that “there is very slack investment in the sector” in 2014.
Shang Fushan, vice president of the CMRA, characterized nonferrous metals production in China in 2014 as “stable,” noting that while copper production was down by 1.05 percent in the first nine months of 2014, aluminum production increased by 4.77 percent during that period.
Nonferrous scrap continued to be imported into China at similar levels in 2014 as in 2013; however, falling prices have had an impact on trade values. Measured in dollars, the value of copper scrap imported into China in the first three quarters of 2014 was down by 11.4 percent, while aluminum scrap values dropped by 6.8 percent, Shang said.
As the value of copper and aluminum has dropped, production costs are rising in China, he remarked. Shang cited increases in labor, energy, financing and environmental compliance costs as challenges for secondary copper and aluminum producers in China. “In terms of global competition, our cost advantages are being undermined,” he said.
At the same time these processors are facing operational challenges—including container inspection and customs clearance bottlenecks at Chinese ports—nonferrous scrap recyclers and secondary metals producers are being told by the government that their sector is important to the future of China.
“Society has boosted the status of the secondary nonferrous industry,” the CNIA’s Ren said, noting that the secondary sector accounted for 25 percent of all nonferrous metals production in China in 2011. The Chinese central government has set a goal for that percentage to increase to 40 percent by 2020. “We believe this sector has a very promising future,” Ren said.
Shang also expressed confidence in the longer-term future for nonferrous scrap recyclers and consumers. “Natural resources are declining, [and] the world’s population is expanding. Nonferrous recycling is an inevitable trend,” he commented. “Recycled metals have rapidly become one of the important raw materials in China.”
Coping with risk
Several presenters at the convention pointed to risks in the current market but also presented suggested solutions.
Yang Yinghui, managing director and head of metals and chemical markets at Beijing-based COFCO Futures Co. Ltd. presented hedging as an important risk mitigation tool available to producers and recyclers of nonferrous metals in China.
Companies and trading offices “need to know the risk exposure connected to your link on the supply chain,” said Yang. She pointed to the inventory management, procurement and sales processes each as areas where price volatility can cause harmful effects.
Forward-thinking companies in China “have already started using hedging,” according to Yang.
“I think you should be sober-minded,” she cautioned nonferrous metals buyers and sellers, urging them to avoid price speculation. “You need to be aware of the risks,” she added.
Since many small and midsized enterprises “don’t have in-house professionals to manage risks,” according to Yang, she urged them to turn to a third-party futures provider such as COFCO for help.
In a separate presentation, Zhu Wuxiang of the Tsinghua University School of Economics and Management urged CMRA delegates to step back and reconsider their business models and strategies and to be prepared to innovate.
The Beijing-based professor said business owners are faced with considering new methods of financing and engaging in research, among many other choices. “In the distant past there was only one route to travel from Beijing to Guangzhou; now there are many options,” he commented.
He said Chinese companies have been urged to put 7 percent of their budgets into R&D, but this alone “does not guarantee good research or the development of products that people want. You spend the money without the benefits.”
He pointed to companies like IBM and Procter & Gamble working with venture capitalists to seek out R&D project candidates or using Internet open platform research forums as alternatives.
Regarding the current lending climate in China, he said small and midsized enterprises “cannot rely only on banks” and expressed optimism that venture capital funding can grow in China.
Recycling companies in China that can move to approved industrial parks may help mitigate risk in the form of greater cooperation with local governments, reducing the possibility of being forced to move at a later time because of new development projects.
CMRA’s Shang noted that China’s central government has approved 45 “urban mining parks” for the recycling of end-of-life vehicles, appliances, electronic scrap and other forms of recycling.
An expanding endeavor
China’s government is encouraging more systematic and regulated methods to collect obsolete electronics and appliances in that nation, according to several presentations given at the event.
A presentation prepared by Xu Kaihua of GEM High-Tech Co. Ltd., Shenzhen, China, and given by his colleague Jiang Zhengkang, outlined the national strategy for electronic scrap recycling that has been mandated to comply with China’s current five-year plan.
The strategy entails an “old-for-new” take-back system when consumer electronics are purchased and the licensing and construction of more than 100 certified or “appointed” electronic scrap processing facilities thus far. The strategy also has EPR aspects to it, according to Jiang.
“After three years of effort by the Chinese government, the recovery, treatment and policy of discarded electronic [scrap] in China has reached the advanced international level,” Jiang said.
Jiang and Xu claim that “90 percent of the [electronic scrap] has been treated by the 107 appointed recycling enterprises” in 2013 and that unsafe and environmentally unsound methods of processing circuit boards or monitors are fading.
The EPR system established in China calls for manufacturers and importers of appliances to pay from 7 to 13 renminbi ($1.15 to $2.10) for each TV, computer, air conditioner, refrigerator and washing machine produced. The “appointed” processing facilities, meanwhile, receive a subsidy of between 35 to 85 renminbi ($5.70 to $13.85) to dismantle end-of-life items that are collected.
Tang Aijun, deputy secretary general of the China Resource Recycling Association (CRRA), Beijing, provided another overview of China’s national system, noting that its “management procedure is very complicated.” Tang displayed a flow chart to match that description.
In 2012, the first year the system was in place, televisions flowed into the qualified facilities in overwhelming numbers, comprising 90 percent of the units these dismantling facilities received. By contrast, washing machines made up just 3.4 percent of the inbound stream and refrigerators accounted for just 1.7 percent.
In 2013, the inbound stream produced more than 455,000 tons of cathode ray tube (CRT) glass while yielding just 78,000 tons of scrap steel, 17,200 tons of copper and 1,430 tons of aluminum.
While the new facilities have provided a home for televisions and monitors, Tang said “compulsory collection and management” of appliances with a scrap metal value is “difficult to execute.”
Among the companies intending to benefit from managed appliance collection is GREE Electric Appliances Inc., presenter Wang Hongxia, general manager of that Zhuhai, China-based firm, said.
GREE makes air conditioners and, according to Wang, is aware that discarded “home appliance recycling channels mainly still rely on street vendors” and that recycling through these informal channels “is more profitable than direct dismantling” at licensed centers. “At present, the [subsidy] is 35 renminbi, but the scrap air conditioning recycling value is higher,” Wang said. “I suggest to adjust the limit of the subsidy to lay the foundation for [proper] reverse logistics.”
Manufacturers such as GREE, Wang said, “should strengthen cooperation with [licensed] recycling enterprises” that can help ensure air conditioners meet an environmentally sound end in China.
The author is editor of Recycling Today and can be contacted at btaylor@gie.net.
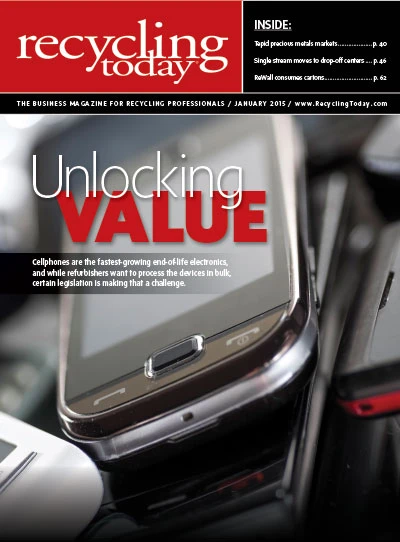
Explore the January 2015 Issue
Check out more from this issue and find your next story to read.
Latest from Recycling Today
- Hyundai says it will make steel in the US
- APR announces Recycling Leadership Award winners
- Glass Half Full opens glass recycling facility in Louisiana
- AmpUp partners with Roundtrip EV
- Global Recycling Day event supports Pittsburgh school's recycling efforts
- President signs executive order on critical minerals
- Registration opens for Scrap Expo 2025
- Toyota opens ‘circular factory’ in UK