Big River Steel’s plans to break ground on a new minimill in Arkansas has generated significant interest from throughout the country. One reason for the attention is because the steel mill and recycling facility, a $1.3 billion investment covering 1,400 acres in Osceola, Arkansas, will be the largest single private investment in the history of Arkansas.
The project also is drawing interest because of one of the names attached to it: John Correnti, a long-time steel industry veteran and the chairman and CEO of Big River Steel. Throughout the past several decades, Correnti has honed his reputation as an insightful, visionary steel expert.
Experienced leadership
In remarks he made during the groundbreaking for the facility in September 2014, Correnti said, “In my three decades in the steel industry, I’ve been fortunate to be in this position many, many times before. My team and I have been involved in launching a number of new steel mills, quite possibly more than any other group. Each and every time we have broken ground on a new project, I have been extremely proud of the advances in technology and mill capabilities a new mill has brought to the industry. But never before has the opportunity been as great as I believe it is for Big River Steel—producing not only the highest grades of steel for today but the highest quality steel grades for the future as well.”
Mark Bula, chief commercial officer at Big River, also has significant experience in the steel industry. He reiterates Correnti’s remarks about the experience of the company’s management, saying, “Combined, our management has probably touched 15 steel minimills in North America.”
Bula says Correnti has continually pushed the steel mills he is involved with toward greater efficiencies. “John likes to take advantage of new technology. And, overall, the project has been on his mind for a number of years,” he says of Big River.
Charles Bradford, an independent economist who closely watches the steel industry, also praises Correnti’s history in the steel business. “He has a history of building facilities at a low cost and of good quality,” he says.
While the pedigree of the steel mill’s executive staff may generate some initial interest in Big River, the company’s management team says it is building a mill that will sustain the company going forward. Big River says it plans to have the mill, which is expected to produce 1.5 million tons of flat-rolled steel annually, operational by 2016.
Targeted markets
The company plans to make steel that can be used in demanding applications, such as API (American Petroleum Institute) steels for pipeline applications, silicon steels for electrical applications and AHSS (advanced high-strength steels), which are ideal for use in the automotive sector, especially with the push toward using high-strength yet lightweight materials to increase fuel efficiency.
Bula concedes the steel industry is playing catch-up when it comes to the automotive sector. “We in the United States are late in coming to the game of high-strength steel,” he says. “The Big 3 also are late to the game. As a combined industry, they are all late to the game.”
Bula continues, “The best things for the steel industry—the best thing for the auto industry—is for the metals to push each other to get better. Innovate or die.
“Our mentality is we welcome competitors and technology that push us to get better,” he states.
Bula says he feels the outlook for the automotive industry is strong, adding that Big River Steel wants to help the industry meet its objective of improving fuel efficiency. “It will take time, effort and commitment to get there.”
He adds that he recognizes that it will take time for Big River Steel to gain the trust of the automotive and petroleum sectors. “We are going to play in the high-end markets,” Bula says, “and it will take time to prove ourselves in the auto and API industries. It is a long road to prove you are a valid supplier.”
Regarding the petroleum sector, Bula says, “Lots of imported pipe is coming in” to the U.S. market. “We would like to see more U.S.-based steel. We are going to try to compete on a global market to make API grades.”
In the longer term, Bula says the electrical grid will need upgraded, which is why Big River is interested in producing silicon steel. “All those transformers are aging and losing efficiency, and there will be a better silicon steel available,” he says. “We hope to have a role to play in the electrical market.”
Strategic location
Big River Steel chose to locate in Osceola for strategic reasons, Bula says, as it provides the company “with access to the vast majority of domestic steel consumers as well as to raw materials from across the nation.” He adds, “The site also has direct barge access adjacent to the Mississippi River and direct rail access via BNSF (Burlington Northern Santa Fe), the largest railroad in North America, as well as numerous highways in close proximity. These attributes provide Big River Steel with great flexibility in terms of receiving raw materials and shipping flat-rolled steel via barge, rail or truck.”
Bula says Big River Steel needs three key elements to realize its plans. “Ideally, we need power. That is important. For EAFs (electric arc furnaces) you need a good source of low-cost power. We are fortunate with that. NRG (a utility firm) gives us competitive rates,” he says.
“The next part is there has to be a market for the steel within 300 miles, which is your marketplace. I like to call it a day’s truck drive.
“The third thing is logistics. Do we have logistics advantage in and out? We are on the Mississippi; that is a huge advantage. We can get to a lot of places with the river system. Also being on a Class 1 railroad, the BNSF, with a big switching yard, helps.”
Bula says he expects Big Steel’s location to benefit the company when it comes to securing raw material. He is not concerned about being able to access sufficient supplies of ferrous scrap, though he says the company will supplement with DRI (direct reduced iron) and other scrap substitutes.
“Generally, the United States is a net exporter of scrap,” he says. “As the scrap price goes up, people recycle more. When scrap goes up, more comes out of the woodwork. So, if everyone is buying scrap at the same price, we are not worrying about it.”
Flexible production
Technology also is a factor that Big River Steel says will work in its favor.
The company says it plans to serve the automotive, petroleum and electrical sectors with a mill that offers a range of production capabilities often seen in an integrated steel mill though it offers the cost advantages and flexibility of a minimill. It refers to the Arkansas project as a “flex mill” that will allow it to produce various gauges, grades and widths of steel as is typical of an integrated mill.
“What Big River feels will help set it apart from other projects is the collaboration it has with the German engineering firm SMS Group, which will supply the technology for the plant,” Bula says. “The technology will include all plants complete with the electrical and automation equipment and the environmental systems.”
For the initial construction phase, SMS will supply a 150-ton EAF, a 150-ton ladle furnace with two treatment stations and a 150-ton RH-TOP (Ruhrstahl Heraeus).
The steel mill also will be equipped with a gas cleaning plant, which will ensure compliance with the stringent environmental standards in place, SMS says in a press release about the project. The dust will be collected and filtered in a baghouse.
“This steel mill will certainly be one of the cleanest steelmaking facilities in the USA,” says Axel Sprenger, SMS Siemag project manager.
With a maximum strip width of roughly 76 inches, the downstream single-strand CSP (compact strip production) plant with a six-stand rolling mill will be the widest of all CSP plants in operation in the market, SMS says. The initial annual capacity will equal 1.5 million tons. At a later stage, a second casting strand will be added, increasing the annual capacity to 3 tons.
One-third of the products made on the CSP plant will be sold as hot strip of various grades, SMS says. The other two-thirds will be processed in the pickling line. Approximately 120,000 tons per year will be sold as pickled and oiled hot strip. The pickling line will be coupled with a five-stand tandem rolling mill, according to SMS.
SMS and Correnti have an extensive history, with SMS noting that it has more than 30 years of experience working with the Big River Steel CEO, including the SeverCorr complex that SMS built in 2007.
Bula says Big River’s efforts to install a research and development division also will set Big River Steel apart from other EAFs in operation. “Minimills used to not think about R&D,” he adds.
Regarding the company’s focus on minimill production, Bula says it follows the general trend in the domestic steel industry. “Certainly it has flip-flopped over the last decade or so,” he says. “Ten, fifteen or 20 years ago EAF steel making was about 20 to 30 percent of the marketplace. Now it is 60 to 70 percent of the marketplace. It has been a wholesale change.”
He continues, “New technologies in EAFs and flat casting have allowed for new steel to be made.”
Bula says Big River has enhanced its minimill with the inclusion of what he says is the first RH degasser in the U.S. and possibly the first in all of North America.
“They are more common with blast furnaces,” he says of RH degaussers. “They are commonly used to make higher grades of steel, especially for automotive applications. Lots of the API grades will benefit at Big River from using the degasser.”
A key advantage Big River has, Bula says, is the size of the steel it will produce. “Our casters will have the flexibility of making a thicker slab that is better than other minimills’. We will be able to make a 3-to-3.5-inch slab,” he says, adding that the mill also will be able to produce “a 1-inch-thick hot melt band that is 76 inches wide.” Of the hot melt band, he claims, “Nobody with an EAF can make this type of steel.”
The size and scope of the mill has garnered attention from potential competitors, most notably Charlotte, North Carolina-based Nucor Steel, which operates a steel minimill in nearby Arkansas. The company filed a lawsuit in federal court this past summer claiming the construction of Big River would violate the Clean Air Act.
Bula was dismissive of the suit, saying Big River Steel would not get into a war of words with a potential competitor.
Instead, he remains focused on looking toward the company’s future plans.
“We are excited to have a partner like SMS as the equipment supplier,” Bula says. “We challenged them to develop the equipment that makes products that will differentiate us. They have combined the best of the best and put it into a mill that will be unlike anything else built in the United States from the degasser to walker tunnel to thicker slab ability and a longer run out table. All of that and other things that we have tweaked in downstream systems will allow us to be unique, to play in niche markets and to compete in different markets.”
The author is senior editor with Recycling Today and can be contacted via email at dsandoval@gie.net.
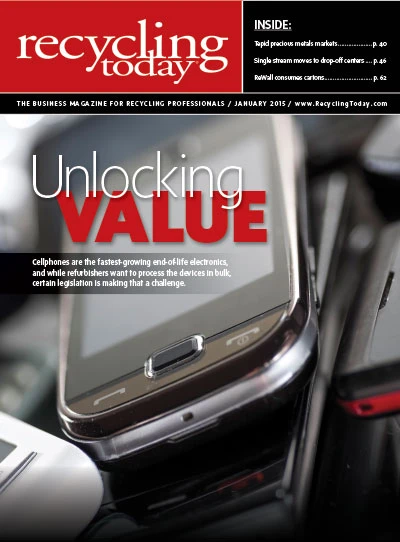
Explore the January 2015 Issue
Check out more from this issue and find your next story to read.
Latest from Recycling Today
- Hyundai says it will make steel in the US
- APR announces Recycling Leadership Award winners
- Glass Half Full opens glass recycling facility in Louisiana
- AmpUp partners with Roundtrip EV
- Global Recycling Day event supports Pittsburgh school's recycling efforts
- President signs executive order on critical minerals
- Registration opens for Scrap Expo 2025
- Toyota opens ‘circular factory’ in UK