Spend more than two decades buying, trading and exporting scrap metal, and you’ll build a network of industry contacts throughout the world. You’ll also amass a wealth of industry knowledge about what works and what doesn’t in scrap steel recycling, trading and export. And you’ll naturally learn what it takes to serve the world’s largest importer of ferrous scrap, the collective steelmakers of Turkey.
That’s been the experience of Philip Hoffman, president of the recycling and consulting firm Hoffman Iron and Steel, based in Houston. Hoffman cut his teeth on the steel recycling industry, having grown up in the business as the step-son of industry icon Robert Luntz. Luntz was the long-time president of Luntz Iron & Steel, the 100-year-old scrap recycling company based in Canton, Ohio. At the time the company was sold to Philip Environmental of Ontario, in 1997, it was processing 1.5 million tons of ferrous scrap per year via five locations in Ohio and Michigan.
Luntz, now age 97, was president of Luntz Iron from the mid-1960s through the mid-1980s an is credited with helping to revolutionize the shredding and mill services sides of the recycling business. In the mid-1960s, says Hoffman, Luntz decided to install what was then one of the nation’s earliest auto-shredders to help the company continue to serve Timken Steel and other area mills. “It was definitely Luntz and Henry Timken that developed the concept of putting a shredder next to the steel mill,” Hoffman says.
Today, Hoffman seems to be continuing in his step-father’s visionary footsteps, breaking new ground in the ferrous scrap recycling industry. In 2008 he advised China’s Tianjin Pipe Corp., conducting a feasibility study for the siting of its new pipe mill in the United States, which is currently being built in Corpus Christy, Texas, and due for completion in 2014.
And in 2012, Hoffman was named vice president of U.S. steel scrap trading for Medtrade Inc., based in Houston. The trading firm is a wholly owned subsidiary of the steel company Çolakoglu Metalurji, based in Istanbul, one of Turkey’s largest mills.
Hoffman credits his impressive Rolodex of industry contacts to the years he spent as a ferrous scrap buyer and trader with the likes of Sims Metal in San Francisco, CCF Recycling/Derichebourg in Houston and Hugo Neu Proler Co. in both New York and Los Angeles.
For Hugo Neu, Hoffman spent close to 10 years managing contracts on both the East and West coasts, and for three of those years he managed the company’s vessel chartering department and assisted in international trade. Hoffman went on to earn a law degree in international trade and maritime law, further cementing his specialty in what is often regarded as a complex, uncertain environment only navigated by the biggest players. After law school Hoffman started his own trading and consulting business with offices in Houston and Los Angeles, exporting containerized scrap from to the West Coast to the Far East.
His most recent contributions for Çolakoglu began when he explored the possibility of trading export container loads of scrap to Turkey from the East Coast, similar to the way containers are brokered from the West Coast to the Far East.
The container export model proved to be cost-prohibitive for Turkish buyers, but Hoffman didn’t give up there. “That’s when we started talking about loading bulk shipments directly, rather than going through the major exporters or trading companies,” explains Hoffman. He suggested that the company consider purchasing its scrap directly from midsize scrap dealers via the U.S. Gulf Coast using bulk vessels loaded with as much as 45,000 tons of scrap. The model proved to be far more competitive than containerized shipments, says Hoffman. “Also, they were set up to receive bulk,” he explains, which is how Turkish mills have always purchased scrap from major East Coast exporters. The idea took hold, and the Medtrade subsidiary was born, with the help of Hoffman’s expertise.
Medtrade now runs its own terminal operation and is able to stockpile and load bulk ship carriers for shipments direct to Turkey from the U.S. Gulf Coast. Hoffman says the arrangement marks the first time a Turkish steel mill has purchased scrap in this way from midsized dealers in the U.S.
Recently Lisa McKenna of Recycling Today spoke with Hoffman about the strength of the Turkish steel market, its wide ranging impacts and how this pivotal market may evolve in the months ahead.
Recycling Today (RT): Figures from the World Steel Association indicate that the world’s No. 1 importer of ferrous scrap, Turkey, may be reducing its imports. Do you see this happening and how would you describe the state of Turkey’s steel industry right now?
Philip Hoffman (PH): The steel industry in Turkey and, thus, demand for scrap is definitely weaker. Finished products for the Middle East and North Africa markets are not in heavy demand, and Europe is not growing at a very fast pace, so some Turkish mills are cutting back their production.
Also because the price of scrap is going up, some Turkish mills are replacing scrap with billet and slab and are making rebar out of billet and hot rolled coil out of slab instead of scrap. These mills can buy slab and billet from Russia and the Ukraine more competitively than higher priced scrap. When the price of scrap hits $400 a ton, then, depending on the price of iron ore, that’s when you see the Turkish mills turning to slab and billet as a replacement.
Turkey is buying less scrap than they used to: As of September 2013, Turkey was on track to import 20 percent less scrap overall than in 2012, and their capacity utilization rate is going down because there is less demand for finished product.
However, internally, the strength of the Turkish economy is increasing in 2013, and there is good internal demand for steel. The economy is projected to grow by 3.2 percent in 2013, up from 2.2 percent in 2012, so the demand for finished steel is projected to be 30.6 million in 2013. There’s also a stimulus package commencing next year for investments in roads, bridges and other government projects. That should help the demand for steel internally and will likely lead to an increase in demand in 2014. But the demand for finished product to export countries is not very strong.
RT: Is Turkey becoming more self-sufficient in terms of feedstock for its mills?
PH: There has been a push by the Turkish government to become more self-sufficient in terms of ferrous scrap, and they are doing an increased amount of ship-breaking in one section of Turkey in that sense, as a way to supplement their internal industrial production. However, the amount of the increase relative to their need is not that substantial. For example, over the past few years, they have imported 20 million to 22 million tons of steel scrap to melt in an average year, and their increased internal volume of scrap generation has been maybe 700,000 tons.
RT: What are the main end markets for Turkey’s finished products?
PH: Long products (mainly rebar) is the main finished product at 25 million tons in 2012, and the other main product, hot rolled coil, was at about 9 million tons in the same period. The Turkish mills are increasing their capacity for flat products, such as coils, because the internal demand for those products is there. There’s currently not enough capacity in Turkey to serve their own flat product demand so they are importing flat products from other countries, and, therefore, are increasing their steel-making capacity on the flat product side. But the Turkish mills are decreasing production rates on the long product side because there is too much capacity.
RT: According to your research, in recent years Turkey has purchased about 27 percent of its scrap from the U.S. Do you see the supply picture shifting, and will the U.S. share change?
PH: That’s a hard call, but I believe that it will remain fairly consistent. Even though the U.S. has decreased the amount of scrap exported to Turkey, U.S. exporters have maintained the same percent at between 27 and 30 percent of the total scrap imports to Turkey. So while it’s true that Turkey has imported less scrap overall, the U.S. remains at around 28 percent of the lesser total amount that’s imported. There also is a quality issue. U.S. scrap tends to have a higher level of quality and delivers a better yield, so Turkish mills want to utilize U.S. scrap because of that, even if they are importing less overall. I would argue that the U.S. market is still going to remain a fairly consistent percentage of the total.
RT: According to your charts, Russia now supplies about 11 percent, Romania supplies 10 percent and the U.K. supplies about 9 percent of Turkey’s imports. What are the reasons for these patterns?
PH: Russia and Romania are significant sources because of the freight differences of utilizing the short sea cargoes. Transportation costs on the Black Sea, because of proximity, are lower than from the U.K. and Western Europe.
Philip Hoffman can be reached via email at Philipsteel@yahoo.com.
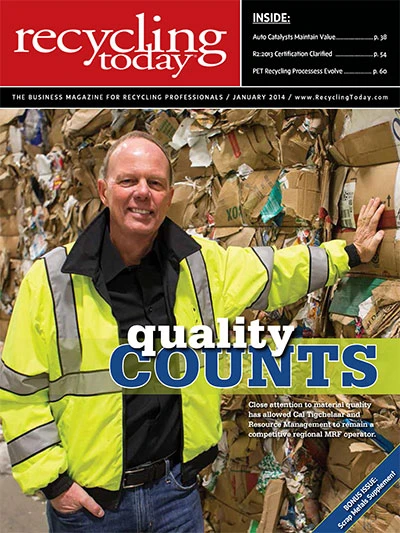
Explore the January 2014 Issue
Check out more from this issue and find your next story to read.
Latest from Recycling Today
- Aqua Metals secures $1.5M loan, reports operational strides
- AF&PA urges veto of NY bill
- Aluminum Association includes recycling among 2025 policy priorities
- AISI applauds waterways spending bill
- Lux Research questions hydrogen’s transportation role
- Sonoco selling thermoformed, flexible packaging business to Toppan for $1.8B
- ReMA offers Superfund informational reports
- Hyster-Yale commits to US production