Recycling facilities have many potential hazards that employees and management must understand and control as much as possible. Communication of those hazards and methods to reduce risk is essential to maintaining a safe and productive recycling facility.
While management may feel that safety is well-communicated throughout the facility and that the hazards are obvious, in the words of George Bernard Shaw, “The single biggest problem in communication is the illusion that it has taken place.” Repeating the message using multiple methods is essential when communicating safety messages, hazards and expectations.
Communication as it relates to safety management and hazards can take many forms: employer to employee, management to supervisors and employee to employee. This discussion focuses on employer to employee communication.
In each form of communication, the message of safety and hazard awareness is being relayed. The essential aspects are: What is the message and is it adequate?
Communicating to employees
Management and supervisors communicate to employees throughout each workday. What supervisors and management communicate regarding safety varies, and what employees hear can differ as well. However, key safety messages employees should receive daily from their employers include:
- That they are valued and that their safety is a priority;
- Operational changes that affect safety;
- Safety issues or problems employees need to avoid or adapt to; and
- The expectation that they are to work safely and to communicate any unsafe situations to their supervisors.
Employers have many opportunities to communicate with employees, including:
- New employee orientation – Best-practice employers provide newly hired employees with orientation training. Topics for this training include an overview of the job description, the operation of equipment and a detailed overview of safety rules and related hazards.
- Weekly safety message – Creating a weekly safety message is an effective way to keep employees well-informed about the company safety effort. A typical 10-minute agenda will include a specific topic related to operations safety and reinforcement that employee safety is a priority. These meetings will take place at the beginning of each shift and be presented by the supervisor. This is a high ROI (return on investment) activity to keep safety a focus in the yard and on the sorting line.
- Tracking and communicating safety results – Maintaining “Days worked without accident” signs can be an easy method to communicate a safety message. However, it is important that the signage be maintained weekly. By not updating this data, employers communicate to employees that safety may not be a priority.
- Safety training – Safety training is not an inoculation against incidents. Employees require periodic and regular safety training to keep the message present and well-applied. Regular safety training communicates the importance of safety and provides information to employees to help them work safely.
- Supervisor-employee interface – Supervisors interface with employees throughout the day. This provides an ongoing opportunity to communicate “safety” to employees. Proactive supervisors will discuss safety with their employees regularly.
Listening to employees
An essential element in safety communication is feedback provided from employees to management. Employees have firsthand insight of situations that affect safety. Employees are driving your trucks, operating the equipment and working on sorting lines. Supervisors should be trained to solicit feedback from employees on a regular basis. Employee ideas often result in operational improvements and valid safety improvement ideas.
Safety communication ideas
|
Employees also are the first to know when equipment is not operating safely. Management has the task to repeatedly communicate to employees that they are to report any unsafe situations immediately. The only proper response by management is to show appreciation for the information and respond promptly with repairs, replacement or other appropriate actions.
Communication to avoid
“Actions speak louder than words” is a well-known adage. Some examples of negative actions that will hurt a company’s safety management effort include:
- Not maintaining “Days worked without accident” posters;
- Creating generic safety rules that do not apply specifically to your operation;
- Not enforcing basic safety rules, such as the use of personal protective equipment (PPE);
- Allowing employees to use unsafe equipment;
- Management personnel not following basic safety rules (such as wearing hard hats and safety glasses);
- Ignoring employee comments about unsafe conditions; and
- Not providing safety training for temporary labor.
Safety performance continues to be the most effective controllable element of managing the cost of insurance and risk. Effectively managing safety in the long term is not possible without consistent positive communication of the message that safety is key to the operation.
Communication about safety is happening daily at each and every recycling facility. The message that is communicated is really the question.
Owners and supervisors should consider the message that they are communicating daily to their employees. Having no strategy and no plan ultimately can result in a negative safety message. Consider the most effective way to provide a positive safety message.
John E. Schumacher, CSP, CLCS, is an insurance and risk management professional with more than 25 years of experience with assisting organizations with developing strategic approaches to reducing losses and managing insurance costs. He can be contacted at jschumacher@assuranceagency.com or at 847-463-7224.
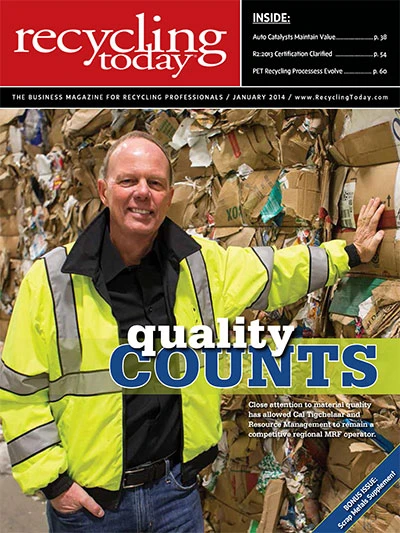
Explore the January 2014 Issue
Check out more from this issue and find your next story to read.
Latest from Recycling Today
- ReMA board to consider changes to residential dual-, single-stream MRF specifications
- Trump’s ‘liberation day’ results in retaliatory tariffs
- Commentary: Waste, CPG industries must lean into data to make sustainable packaging a reality
- DPI acquires Concept Plastics Co.
- Stadler develops second Republic Services Polymer Center
- Japanese scrap can feed its EAF sector, study finds
- IRG cancels plans for Pennsylvania PRF
- WIH Resource Group celebrates 20th anniversary