In 2013, the R2 (Responsible Recycling) Standard and certification program received a makeover that was designed to pave the way to ensuring industry best practices around the globe. The R2 Technical Advisory Committee (TAC) developed the updated R2:2013 Standard as the next generation of R2 Practices. It replaces the original R2 Standard, which was released in 2008 by the United States Environmental Protection Agency (EPA).
The TAC comprises representatives from government regulatory agencies; nongovernmental organizations (NGOs) and public interest groups; the electronics recycling, refurbishing and manufacturing industries; downstream vendors; and international trade experts. The TAC completed the update during a 15-month period, which included time for public review and comments. The final R2:2013 Standard took effect July 1, 2013.
The R2:2013 Standard seeks to clarify requirements of the R2:2008 practices, to improve the readability and understanding of the standard, to provide additional best practices and to enhance the quality of certification. The overarching goal of R2:2013 is to help electronics recyclers and refurbishers optimize their systems and practices and, by certifying to its requirements, assure upstream clients that they are fully addressing potential risks to their clients’ brands and protecting them from potential legal and financial liability.
The R2:2008 Standard included 13 provisions relating to the management of focus materials (FMs), including CRTs (cathode ray tubes), batteries, mercury-containing devices, items containing PCBs (polychlorinated biphenyls) and circuit boards. In the updated standard FMs still include the original five materials from the 2008 version with additional clarifications.
Also, two new categories of electronics were created with the updated R2:2013 Standard. The first category is collectible electronics, which refers to items that are rare or vintage and no longer manufactured or supported by the original manufacturer. The second category is specialty electronics, which includes rare and specialized equipment not generally available in retail. Medical, diagnostic and similar devices are examples of electronics that fall under this new definition.
The R2:2013 version includes the original 13 provisions with the following changes:
Provision 1: Environmental, health and safety (EH&S) management system. The most significant change is in Provision 1, the requirement for R2 facilities to have an EH&S management system. R2:2008 did not require companies to have a certified EH&S management system; rather, it allowed companies to develop their own EH&S management systems in accordance to R2 requirements. The new R2:2013 Standard, however, requires certification to either a combination of ISO 14001 (environmental management system) and OHSAS 18001 (health and safety management system) or to the Institute of Scrap Recycling Industries Inc. (ISRI) Recycling Industry Operating Standard™ (RIOS), which encompasses elements found in ISO 14001, OHSAS 18001 and ISO 9001 (quality management system). This more rigorous management system requirement is designed to substantially improve the integrity and accountability of the entire R2 certification.
Provision 2: Reuse and recover hierarchy of responsible management strategies. Two significant changes affect Provision 2, the first being a greater emphasis on the recovery of reusable and refurbishable parts and equipment. The second is a directive that states that an R2:2013 electronics recyclers shall not direct material to incineration, energy recovery or landfill disposal facilities unless no reuse or recycling options are viable.
The tougher stance on the “reuse, recover hierarchy” is designed to ensure that certified companies are doing their parts to recover products that still have legitimate reuse opportunities. Extending the useful life of electronics is widely recognized as the most environmentally beneficial practice in the hierarchy and minimizes the environmental footprint associated with manufacturing new products.
Provision 3: Legal requirements. From day one, R2 has advocated that laws from all governing jurisdictions regarding the handling of used electronics must be followed. Simply stated, if a recycler is sending product to a country that does not legally accept such product, it is wrong and expressly forbidden in the standard. The updated standard includes tighter controls on imports and exports, specifically mandating compliance with the export and import laws of all exporting, importing and in-transit countries regardless of whether they are members of the Organization for Economic Cooperation and Development (OECD).
Additionally, the updated standard places more emphasis on data security and requires R2:2013 certified companies to understand their legal obligations when handling any devices that contain data.
Provision 5: Focus materials. All FMs must be tracked through each downstream vendor until that material is processed to a commodity grade material, fully functioning piece of equipment or disposed of properly. R2:2013 has been designed to put greater emphasis on verifying that each downstream vendor in the recycling chain manages FMs to the standard’s requirements and that downstream vendors follow all applicable laws. Landfill and energy recovery of FMs are strictly prohibited, according to the R2:2013 standard.
Provision 6: Reusable equipment and components. R2:2013 strongly encourages extending the life of electronics equipment through reuse and refurbishment. As a result, the greatest number of changes are to Provision 6. A R2:2013 certified company must ensure all reuse equipment has its data sanitized and that equipment is handled in such a way to prevent damage.
In addition, the updated provision introduces new labeling requirements that companies will need to follow to ensure customers who purchase these goods for reuse or refurbishment are getting the products they expect to receive. As such, R2:2013 requires a written quality assurance plan (or certification to ISO 9001 or RIOS) and a policy to verify the accuracy of test methods and testing equipment. Certified companies must maintain records of effective testing methods, equipment and results.
Additionally, a certified company needs to implement a written product return plan and policy appropriate for the final destination of its equipment and components.
This provision also includes the new definitions of collectable electronics and specialty electronics. Under the R2:2013 Standard, as long as the sales of these items do not exceed 1 percent of total unit sales on a rolling 12-month average, companies can sell these items without functionality testing—a much more reasonable provision for companies that rarely come across such equipment or do not have the technical ability to test the equipment.
The R2:2013 Standard adheres to the principle of reuse as the most environmentally beneficial form of recycling and is designed to place a greater emphasis on requirements that will achieve this outcome. This universally accepted principle is what drove the decision to add allowances regarding collectible and specialty electronics. This change will enable recyclers and refurbishes who rarely encounter this type of equipment to make common sense business decisions that are more environmentally and economically sustainable.
Provision 8: Data destruction. The requirements regarding data destruction have been substantially strengthened. All data (from all media types) must be destroyed in accordance to established data destruction standards described in the NIST (National Institute of Standards and Technology) “Guidelines for Media Sanitation: Special Publication 800-88” or another generally accepted standard. Alternatively, companies may be certified by a generally accepted certification program. Employees involved in data destruction must receive specialized training, and the entire process needs to be validated by an independent party. All data-containing devices need to be stored in a secured environment and tracked throughout the entire recycling process, including transportation and storage. R2:2013 sets out to minimize the risk of brand damage, legal noncompliance and data liability, which are all major concerns of IT professionals and corporations around the world.
Provision 10: Security. The first thing that changed in Provision 10 is the name itself. By changing Facility Security to Security the provision broadens the scope to include security beyond the confines of the facility, encouraging the company to consider additional issues such data security, transportation and employee screening. In addition, the R2:2103 Standard is designed to require certified companies to consider and include necessary controls to secure electronic equipment upon acceptance of the equipment, which could mean from the time they pick up the material at the customer’s location.
Provision 11: Insurance, closure plan and financial responsibility. A much-applauded change occurs in Provision 11. In the past, R2 certified companies were required to have $1 million in pollution insurance. R2:2013 instead requires companies to demonstrate that they have evaluated the risks arising from the scope of their certification activities and that they have adequate insurance or reserves to cover liabilities (including environmental pollution and worker health and safety) that might arise from operations in each field of activity and in each geographic area in which the companies operate. Under the new standard, if a company shows it has evaluated its potential risks and it has been determined that pollution insurance is not required for the operation, it is not required to purchase it. This can be a significant cost savings—especially for a small refurbisher.
Provision 13: Documentation and recordkeeping. In recognition that many certified companies have multiple facilities, wording has been changed in Provision 13 to allow for a certified facility to have access to all company documents and records necessary to demonstrate conformity to each requirement. The R2:2008 Standard required the company to maintain all documents in a single location.
Facilities that are currently certified to R2: 2008 must meet all of the revised provisions of R2: 2013 by Dec. 31, 2014.
More information on the R2: 2013 Standard is available from R2 Solutions at www.r2solutions.com.
The author is in charge of business development and training for Greeneye Partners LLC, with offices in Apple Valley, Minn., and Santa Rosa, Calif. He can be emailed at bmccarthy@greeneyepartners.com.
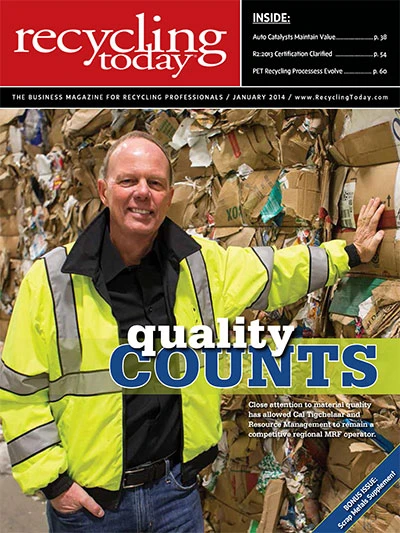
Explore the January 2014 Issue
Check out more from this issue and find your next story to read.
Latest from Recycling Today
- Astera runs into NIMBY concerns in Colorado
- ReMA opposes European efforts seeking export restrictions for recyclables
- Fresh Perspective: Raj Bagaria
- Saica announces plans for second US site
- Update: Novelis produces first aluminum coil made fully from recycled end-of-life automotive scrap
- Aimplas doubles online course offerings
- Radius to be acquired by Toyota subsidiary
- Algoma EAF to start in April