The recycling of PET (polyethylene terephthalate) has drawn increasing attention recently. With tightening end-product quality requirements occurring alongside increasing levels of contamination in the postconsumer plastic stream, recyclers are rethinking their PET sorting strategies. As such, this interesting yet challenging business area continues to evolve with new approaches to preprocessing and optical sorting that are geared to maximizing recovery and purity.
Plastics recyclers often source postconsumer PET bales from material recovery facilities (MRFs), and these bales can vary greatly in quality; however, the quality specifications for the PET recycler usually remain consistent and depend on its customers’ requirements.
A PET processor needs to have an established business plan to be profitable, and it should ideally encompass three things:
- A good, steady supply of incoming bales of acceptable quality;
- A sorting and washing system that is capable of meeting customers’ specifications; and
- A good market for the recycled flake or pellets that keeps the business sustainable.
A closer look at a PET recycling operation reveals that the sorting and washing system is a very involved process that sends material through several purification steps before the final product ends up in a Super Sack for shipment to the customer. The main revenue generator for any PET sorting plant is clear PET flake, which needs to be sorted with the highest purity and recovery rates, particularly if it is to be used in bottle-to-bottle applications. Expected purity rates for clear PET are not measured in percentages but in parts per million (ppm). Considering that 1 percent contamination translates to 10,000 ppm, it is easy to understand why plastics recyclers and consumers require this more exact unit of measurement.
Depending on the end market for the clear PET flake, the acceptable residual contamination can vary quite a bit. The higher the quality, the more value the washed flake has.
The highest quality flake has a total residual contamination of less than 200 ppm, which equals a purity of more than 99.98 percent. Considering that clear PET content can be as low as 50 percent in curbside PET bales, obtaining that level of purity from this type of stream poses an extreme challenge for the sorting process. It also dictates that multiple cleaning steps will be required to reach the desired quality level.
Sequence of events
Engineers at Van Dyk Recycling Solutions believe it is critical to gather as much knowledge as possible about the input material prior to designing a PET sorting facility. Curbside PET bales tend to vary somewhat in their composition, with clean PET content ranging from 50 percent to 90 percent. Colored PET content typically accounts for between 5 percent and 25 percent of a bale, with green being the most dominant color. Non-PET contamination can be as much as 20 percent in some bales.
PET container recycling rate tops 30 percent
The associations report that the total volume of postconsumer PET bottles collected was the highest to date at 1.72 billion pounds, as were both the total amount of recycled PET produced by U.S. reclaimers, at 930 million pounds, and the amount used across major domestic end-use markets, at 1.3 billion pounds. “The increase in the PET recycling rate is clear evidence of continued strong, domestic end-market demand for recycled PET, and we believe there’s considerable scope for the U.S. industry to readily absorb more recycled PET material if available. This strong demand continues to drive domestic investment,” says Tom Busard, chairman of NAPCOR and APR and chief procurement officer for Plastipak Packaging Inc., Plymouth, Mich., and president of Clean Tech, Plastipak’s recycling affiliate. |
A good sorting system should accommodate for these variances in incoming bale composition to maintain steady throughput and quality output of clear PET.
Before recyclers can optically sort the incoming material, they first need to prepare the stream for the optical sorting equipment, which starts with the debaler or the debaling process.
Most debaling equipment available on the market requires bale wires to be removed manually prior to sorting. This can be dangerous, since some bales are compressed more than others, depending on the equipment that baled them, and can cause injuries if safety procedures are not followed. But machines also are available that can accept entire bales. Once the bale has been broken, the bale wire can be removed during preprocessing with magnets and fine screens. If recyclers do not remove this ferrous material, it will most likely end up in the residue bales, and processors may not be able to gain any revenue from it.
Curbside PET bales can contain a large amount of fines, such as glass and grit, which should be removed on the front end of the processing system using a fines screen. Otherwise, these fines may end up in the flake wash line, making the washing process more difficult.
Following the fines screen, many PET processors integrate a whole-bottle wash into their systems prior to the optical sorting stage. Some of the advantages of including a whole-bottle washing process are the removal of labels and the declumping of the PET stream, both of which facilitate the optical sorting process.
After preprocessing, the material stream moves to the optical sorting process. To achieve the highest quality end product, recyclers need to carefully select their sorting strategy and generally must implement several sorting steps.
Traditionally, PET sorting plants follow a sorting strategy referred to as “negative sorting” of clear PET, in which the optical sorting equipment removes everything except clear PET from the material presented to it on the conveyor belt. Some recyclers may still prefer this sorting strategy if their incoming bales have lower levels of contamination and consist primarily of clear PET. Negative sorting was particularly popular in prior years when PET content in postconsumer bales tended to be at least 70 percent. In those cases it made more sense to focus on removing the contamination or the materials known to be in the minority.
These days, considering that the concentration of clear PET in curbside PET bales can be as low as 50 percent, the traditional negative sorting approach no longer may be suitable for some operations. Many PET processors say they are finding more random non-PET contamination in their incoming bales of curbside PET, which is difficult to remove via negative sorting, because the contaminating materials are either too heavy or not detectable.
A more modern alternative that has the potential to solve these challenges is the use of “positive sorting” techniques. Essentially the opposite of negative sorting, positive sorting is the process by which optical sorting equipment identifies and removes the clear PET from the material stream. By identifying and removing clear PET rather than what isn’t clear PET, in a single step, an optical sorter such as the TITECH autosort 4 may be able to create a clean, clear PET stream that is free of contamination, even that which is otherwise not detectable or too heavy to eject.
This positive sorting strategy places special requirements on optical sorting equipment. Optical sorters need to be able to detect material composition as well as color and need to be able to positively eject as much as 90 percent of the incoming stream to be effective. This is possible with a variety of optical sorters and system setups available on the market, some of which are able to sort for color, material composition and metal contamination either at the same time or in sequential steps.
Maximizing quality
After the initial positive sorting process, an additional sorting step may be needed to achieve the required purity level. At this point the contamination rates may be well below 5 percent, so the optical sorting equipment can perform a negative sort on the clear PET stream in one or more steps. A final manual quality-control step can be added to remove any colored containers the optical sorters missed before the clear PET bottles are sent to the grinder and then to the wash line.
Even after all of these sorting steps, label and cap removal and flake washing and drying, recyclers may find that their particular purity target has not been reached yet. Some contaminants are more critical than others and need to be reduced further to achieve the desired clear PET flake quality.
For the highest quality PET flake, non-PET contaminants such as PVC (polyvinyl chloride) and metals need to be brought to a minimum. This can be accomplished with today’s flake sorting equipment designed to reject color, material and metal contamination with the goal of producing recycled clear PET flake with the highest possible quality and the lowest possible contamination.
Many optical sorting system manufacturers say they are able to achieve the highest quality clear PET flake that meets or exceeds customer specifications using today’s optical sorting technology.
Alex Wolf is a sales engineer for TITECH and can be reached at wolf@titech.com. Ginny Marr is the copywriter at Van Dyk Recycling Solutions, Stamford, Conn.
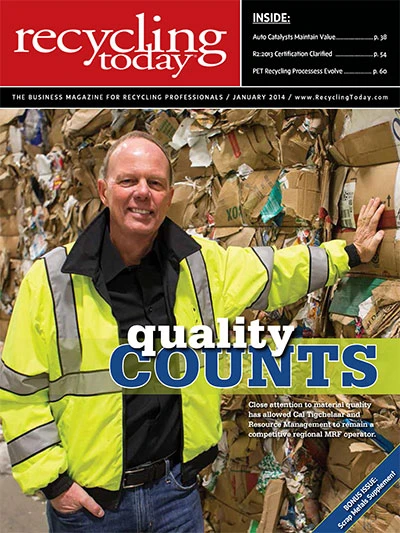
Explore the January 2014 Issue
Check out more from this issue and find your next story to read.
Latest from Recycling Today
- ReMA opposes European efforts seeking export restrictions for recyclables
- Fresh Perspective: Raj Bagaria
- Saica announces plans for second US site
- Update: Novelis produces first aluminum coil made fully from recycled end-of-life automotive scrap
- Aimplas doubles online course offerings
- Radius to be acquired by Toyota subsidiary
- Algoma EAF to start in April
- Erema sees strong demand for high-volume PET systems