As the United States space program declines, gone are the crowd-captivating shuttle launches and International Space Station trips. And while other countries continue space exploration, much of the infrastructure associated with NASA’s previous efforts is being retired, restructured or demolished to make way for new facilities.
At the agency’s Ames Research Center (ARC) in Mountain View, Calif., Pantano Demolition tackled the removal of four massive vacuum spheres once used in support of the facility’s hypersonic wind tunnel. It faced formidable challenges, but by using a pair of Genesis GXP 990R mobile shears, the company overcame them and redefined the phrase “heavy metal.”
Built in the late 1950s, the 3.5-foot diameter hypersonic wind tunnel at ARC was initially designed for basic aerodynamic research in the Mach 5 to Mach 10 range but then found broad use as part of the then-emerging U.S. space program. It eventually became the program’s workhorse, handling most of the atmospheric re-entry testing of the space shuttle and its ancestors.
A key component of that tunnel complex was a series of four spheres, which cooled the superheated, compressed gas used in testing. According to Ruben Hernandez, superintendent for Fresno, Calif.-based RS Morris Construction, the general contractor on the job, though the spheres were impressive in size, getting them down to a point where they could be recycled presented challenges.
“The wind tunnel facility was built in 1959 and busy almost right up to 1979, when it was decommissioned due to wear-related issues,” he says. “It has been idle since, and plans to build another facility on the site prompted the demolition. It’s ironic, but we actually took down a building adjacent to this, and I remember thinking as I looked over here that I would hate to be the company that had to take those spheres down. About seven months later, I walked into my office to find out we got that very job. Our first thought of course was: ‘What are our options?’”
Those options, it turned out, were very limited. Not only were the spheres constructed of 1-and-five-sixteenths-inch thick steel, but the steel had tempered. To simulate Mach 10 airspeeds, 10 times the speed of sound through the tunnel, compressed gas was heated to temperatures around 3,000 degrees Fahrenheit, the melting point of steel. While the gas was markedly cooler by the time it got to the spheres, it was still extremely hot, says Hernandez.
“It’s believed the continual high-temperature heating and subsequent cooling of the spheres caused the steel to temper,” says Hernandez. “It was definitely the toughest material we’ve ever encountered. We’d worked with Pantano Demolition in the past, and they were confident they could bring the tools to get the job done, so we subcontracted that portion to them.”
Plan of Attack
Each of the four spheres at ARC’s tunnel complex was 75 feet in diameter and 85 feet tall. It was determined that the best plan of attack for bringing the spheres down to ground level for processing was to attach cables to two of each of the sphere’s 12 legs and “trip” them. The processing, according to Giuseppe Pantano, the Fresno, Calif.-based demo firm’s owner, could then only be done with a large mobile shear.
“We looked at what we were getting into and knew immediately that this was not going to be a standard job; the material was just too hearty,” he says. “However, we’d been working with Bejac Corp., our local Link-Belt dealer, for a while, and I knew they were also handling shears from Genesis Attachments. We talked to them about what we were facing and made arrangements to outfit a Link-Belt 800 LX with a Genesis GXP 990R. We were looking at a fairly aggressive 16-week window to get things done but confident this was the best plan of action and started in early January.”
That early work was complicated by additional piping and other tunnel-related infrastructure that made the work site extremely congested. According to Pantano, just getting the first sphere down took a good deal of planning, and each subsequent sphere presented additional concerns, such as nearby traffic and an active gas manifold. “It got better as we started removing material,” he says, “but at the beginning, there was hardly room to turn the machine around.”
The Right Move
To gain an access point when processing a normal vessel such as a storage tank, shear operators generally use the attachment’s piercing tip to punch through the material and then process from there. The nature of the steel Pantano encountered at ARC, however, eliminated that method as an option.
“For us to cut with the shear, we had to first have a square section abated, then torched out so we could get the shear in,” he says. “We actually had the torchers do the entry cuts for all the spheres at once, then spot weld them shut again until we were ready to start on each one. At that point, I was able to just poke it with the tip of the shear to knock it inward and start cutting. Seeing how long it took just to torch those sections, anywhere from five hours for a smaller opening to two days for a larger one, reassured us that we’d made the right decision in going with the Genesis mobile shear.”
Because material had to be cut to a size where it would fit inside a standard scrap trailer, Pantano sheared to 8-foot and shorter lengths. But getting scrap to the scrap yard roughly 45 miles away was hindered by heavy area traffic, and the trucks were often only able to make two trips per day. Also, because the material was so dense, the loads had to be smaller.
“I had more than one instance where I put two good-sized pieces in the truck, and it was maxed out,” he says. “And, because of on-site congestion, we didn’t have the luxury of setting material aside for later. It got crazy at times, but we managed.”
Doubling the Effort
In addition to the spheres themselves, Pantano also processed the supporting legs and crossbeams as well as piping connected to the tunnel’s aftercooler and several other components on site. All told, Pantano estimates workers sheared and recycled about 2,500 tons of steel from the job. Midway through the project, to offset some unscheduled delays, Pantano contracted with Bejac for a second GXP 990R mobile shear, again on a Link-Belt 800LX.
“Bejac is an excellent dealer and was there for us whenever we had any issues,” he says. “So when we decided to add the second machine and Genesis shear, they stepped up to the plate and made it happen. So much of this job was driven by how tough the material was, and, in that regard, the Genesis shears were a lifesaver. I’ve used mobile shears before in building demolitions, so I know what they can do. But even a building’s I-beams are no match for what we were processing here. This was another world entirely.”
Looking back at how long it took to torch the four access points, Pantano estimates the job would have taken the better part of a year without the shear.
“Obviously that wouldn’t have worked for anyone,” says Pantano. “I was truly amazed at what that shear could do. At the outset, when I saw what we were up against, I thought: ‘No way.’ Turns out, there definitely was a way.”
Demolition at the ARC site wrapped up in late April, and plans to construct a new arc-jet tunnel complex at the same location are already in the works.
This article, which was submitted on behalf of Genesis Attachments, Superior, Wis., first ran in the November/December issue of Construction & Demolition Recycling, a sister publication to Recycling Today.
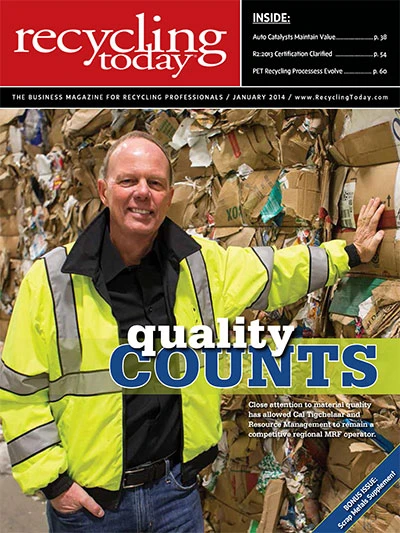
Explore the January 2014 Issue
Check out more from this issue and find your next story to read.
Latest from Recycling Today
- Washington legislature passes EPR bill
- PureCycle makes progress on use of PureFive resin in film trials
- New copper alloy achieves unprecedented high-temperature performance
- Gränges boosts profits and sales volume in Q1 2025
- RMDAS April figures show recycled steel price setback
- Steer World offers PEX plastic recycling machine
- New recycling grant program launches in Massachusetts
- Tire Recycling Foundation names executive director