Upstate Shredding to install auto shredder at new Albany, NY, plant
Upstate Shredding, headquartered in Owego, N.Y., has purchased a metal shredding and downstream sorting system for the company’s scrap yard and port facility in Albany, N.Y. Upstate Shredding says the new equipment at the facility, opened in August of 2013, should be operational by early April of 2014.
“We’ve spent years building our metals recycling network in New York and Pennsylvania into a highly efficient system,” Adam Weitsman, president of Upstate Shredding – Ben Weitsman, says. “We have ambitious goals for our Albany yard, and this shredder is the next step in putting that plan of expansion into motion.”
The company says the project represents a $25 million investment that is being funded privately through the company. Weitsman says the company did not seek any government assistance on the project.
The company says several million dollars more could be spent during the next several years to create and develop a network of recycling facilities to feed the new shredder.
“It took us years to build up our feeder yard system around our Owego shredder, and this new shredding location, in addition to our shredder in New Castle (Pennsylvania), which will be operational in the second quarter of 2014, will be the launching pad of the next phase of our expansion,” Weitsman explains. “We’ve examined the markets surrounding the Albany facility, and we plan to make several new acquisitions of scrap yards in the region to develop the network of yards to feed the Albany shredder.”
Wendt Corp., Buffalo, N.Y., will build the shredder and downstream sorting system. Although the installation is smaller than Upstate’s Owego shredding and sorting system, the company says several technological advances have been included, such as separation technologies to recover wire, plastics, nonferrous metals fines.
“We are pleased to have been selected by Upstate Shredding to construct a new state-of-the-art shredding plant at the Albany port facility,” says Tom Wendt Jr. of the Wendt Corp. “It’s a pleasure to be part of Adam Weitsman’s continued growth and success.”
In May 2013, Upstate announced that its second shredder would be installed in New Castle. The company acquired the New Castle yard in December 2012 and says the location provides access to new scrap and steel manufacturing markets.
All Metals Market commissions shredder
All Metals Market, a Fremont, Neb.-based third-generation scrap metal recycling firm, is operating a new auto shredder from the Italian firm Bonfiglioli at its yard in Fremont.
Kevin Yount, president of the company, says the shredder's installation reflects the company’s growth over the past three years. Yount says the equipment primarily will be used to shred sheet metal and other types of scrap.
The shredder is the sixth of its type manufactured by Bonfiglioli that has been installed in the United States, the company says.
The system includes an input hopper, the shredder mill, two drum magnets for sorting ferrous metals and a configuration of conveyors and eddy current magnetic systems. A walkway connecting the components was designed by Facilities Manager Todd Hoppe, who oversaw the system’s installation.
Yount says the decision to install the Bonfiglioli shredder follows All Metals Market’s purchase of a 2,000-ton gravity-feed shear from the company in early 2013. He says it is the first of its type in use in the U.S.
“We have been very pleased with the shear, so we decided to purchase an auto shredder as well,” Yount says. When fully operational, he says the shredder will be able to process between 20 to 30 tons of metal per hour.
The decision to expand All Metals Market’s services follows strong growth for the company over the past three years, Yount says. “We have a clean facility. We are noticing lots of people are staying away from the large city yards. They come to our yards here, and they are not intimidated by the operations.”
Yount also says All Metals Market makes customer service a priority. “If they call us we are out there right away,” he says.
While All Metals Market has seen strong improvement in its retail business, the company says it also has seen a sharp increase in its industrial business. The company has 400 boxes at various locations as well as trailers to quickly service customers. All Metals Market also recently expanded its warehouse.
The Bonfiglioli shredder, purchased through Alan Ross Machinery Corp., features a unique rotor design, dynamic throttling of feedstock and a semiportable downstream nonferrous recovery system, the company says.
E.L. Harvey opens single-stream MRF
E.L. Harvey & Sons, a family-owned recycling firm headquartered in Hopkinton, Mass., has opened a new single-stream recycling facility to serve residents in the Massachusetts cities of Hopkinton and Westborough as well as surrounding areas. Eugene, Ore.-based Bulk Handling Systems (BHS) designed, manufactured and installed the material recovery facility (MRF). The system is housed in a new 80,000-square-foot building and is permitted to process up to 600 tons of recyclables per day.
The MRF includes screening and optical sorting technology from BHS and NRT and is built to recover more than 95 percent of the available recyclables.
Ben Harvey, president of E. L. Harvey & Sons, says, “This project will help communities and businesses throughout eastern Massachusetts increase recycling rates, decrease disposal costs and lessen the use of traditional disposal sites. It is a step toward helping the commonwealth of Massachusetts Solid Waste Master Plan reach its 56 percent recycling goal.”
“We chose BHS after an intensive comprehensive analysis,” says Steve Harvey, executive vice president of the recycling firm. “A great deal of research and site visits went into the decision; the deciding difference was the superior design and performance of the BHS screens, which gave them the competitive advantage.”
“The Harveys have been leaders in this industry and in their community for decades, and it's an honor for them to place their trust in BHS,” says BHS CEO Steve Miller. “E.L. Harvey & Sons has a great story and a long track record of excellence in operations. I have no doubt that this system will deliver performance for years to come for their business and the communities that they serve.”
Harvey adds, “We have a very good working relationship with BHS. The field support, installation and engineering crews have been top-shelf. The project engineer, Bob Fry, was always available for me. All of our calls, questions and requests have been handled with first-class professionalism and in a very timely manner. They have provided 24-7 service to me, and, believe me, I have tested it.”
USA Hauling & Recycling upgrades its Murphy Road MRF
USA Hauling & Recycling, based in Enfield, Conn., is currently upgrading its Murphy Road Recycling facility in Bridgeport, Conn., with equipment from Van Dyk Recycling Solutions, Stamford, Conn. The commercial single-stream plant was expected to start up in December, 2013.
Owners Frank and Jerry Antonacci chose Van Dyk to help them keep up with tightening market requirements with regard to end product quality.
To meet Murphy Road Recycling’s specific needs, Van Dyk provided a custom-designed solution to improve the facility’s efficiency and end product quality. The upgrade includes infeed conveyors, a Bollegraaf old corrugated containers (OCC) screen and a TITECH optical sorter. According to Van Dyk, the optical sorter will allow the facility to make quick adjustments driven by fluctuating market dynamics.
Van Dyk Recycling Solutions is a North American supplier of recycling and recovery technology and the exclusive distributor of Bollegraaf, Lubo and TITECH machinery.
MOD shortens delivery times on container orders
Material handling product manufacturer Meese Orbitron Dunne Co. (MOD), based in Ashtabula, Ohio, says it has cut its average lead time for delivering standard recycling collection carts, bulk trucks and bulk containers in quantity to three weeks from order to arrival.
Approximately 50 percent faster than the commonly accepted delivery time, the MOD speedy deliveries help recycling and waste management companies begin serving commercial recycling program accounts quickly without delaying contract implementation pending arrival of new carts and containers, the company says.
MOD says the shorter average lead time is made possible by its experienced manufacturing team producing consistent, quality-controlled carts and containers using state-of-the-art rotomolding machines. In addition, deliveries are sent from multiple plants throughout the U.S., says MOD President Robert Dunne. The company’s East Coast, West Coast and Midwest plants permit manufacturing to be performed as close to a customer’s facility as possible for direct savings in transit times and freight costs, the company reports.
The short lead times are typically achieved on the entire line of MOD recycling carts and containers, including the Poly-Trux 50P16R collection cart, the 54P-20R electronic waste collection cart and the Ship Shape series reusable bulk containers. Most of the carts and containers nest, stack and cube out trucks and trailers for additional efficiency in transport, the company says.
Rumpke opens new MRF
The waste and recycling company Rumpke, based in Cincinnati, has officially opened its new material recovery facility (MRF) in St. Bernard, Ohio. The MRF replaces Rumpke’s facility that was destroyed by fire in April 2012 and is expected to serve more than 4.5 million residents in the Cincinnati area.
Rumpke invested $32 million in the 100,000-square-foot facility on 10 acres. When fully operational, the MRF will be able to process 55 tons of recyclables per hour. The volume is a significant increase from Rumpke’s earlier facility.
Steve Sargent, director of Rumpke Recycling, says the company built the MRF with future growth in mind.
The equipment used at the facility was designed by Machinex, Plessisville, Quebec.
“Machinex is extremely proud to partner with Rumpke on its state-of-the-art recycling facility,” says Pierre Paré, Machinex CEO. “This system is the achievement of a work team where both companies’ know-how and expertise have been combined. Machinex provided a custom design system that combined with the latest technologies on material separation.”
The facility includes six optical scanners, two eddy current separators and hundreds of spinning discs.
Southern Metals Co. adds eddy current separator
Southern Metals Co., based in Charlotte, N.C., has invested in a new Eriez RevX-E model eccentric eddy current separator (ECS) featuring an eccentric rotor design. The company was previously using an older concentric model ECS in need of repair work. Eriez’s sales representative Dominion Carolina Sales recommended the new ECS.
The RevX-E uses a smaller diameter magnetic rotor offset at the top of a larger outer shell. According to Eriez, this design allows the rotor’s repelling force to be focused in the area closest to the outer shell. Although the eccentric rotor radiates a more focused surface area for separation, Eriez says, this new design reduces ferrous buildup by releasing it from the belt after it has passed through the field.
“The new unit is probably 50 percent more efficient than our older eddy because of the new rotor design,” says Bobby Helbein, owner of Southern Metals. “The eccentric eddy has more throughputs, and it makes a cleaner job of separation.”
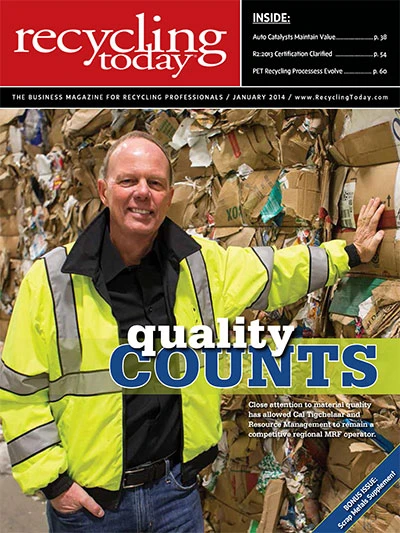
Explore the January 2014 Issue
Check out more from this issue and find your next story to read.
Latest from Recycling Today
- ReMA opposes European efforts seeking export restrictions for recyclables
- Fresh Perspective: Raj Bagaria
- Saica announces plans for second US site
- Update: Novelis produces first aluminum coil made fully from recycled end-of-life automotive scrap
- Aimplas doubles online course offerings
- Radius to be acquired by Toyota subsidiary
- Algoma EAF to start in April
- Erema sees strong demand for high-volume PET systems