In a well-publicized incident that occurred in the summer of 2005, a variety of items from a Boeing 737 commercial aircraft reportedly washed up on a beach in Scotland. Included in the collection were items from the interior of the plane, such as seats, in-flight magazines and safety information cards.
At first, government officials feared the worst, but further investigation showed the gathering of items actually came from a scrapped airplane that apparently had been dumped into the ocean.
Boeing has no control over what airlines or recyclers do with scrapped planes, but that didn’t make the news any easier to take, explains Boeing’s William Carberry, program manager, aircraft and composite recycling. Carberry also serves as Boeing’s technology leader for sustainable product development of commercial aircraft.
In response to the incident, says Carberry, the U.K. government initiated the WINGNET study (an acronym for Waste Reduction in Aircraft-Related Groups) in cooperation with Oxford University to explore solutions managing end-of-life aircraft. Then, in 2006, a group of 11 companies based in the U.S., the U.K. and France, banded together to form the Aircraft Fleet Recycling Association (AFRA). Its primary mission was to set up policies for the disassembly and recycling of aircraft that were both environmentally responsible and safe.
“It is important to have industry-accepted standards for aircraft dismantling and recycling,” says Martin Fraissignes, executive director of AFRA. “End-of-service aircraft are valuable assets; owners want to ensure that they are dealt with by skilled experts, who will manage their assets in both a responsible and environmentally sustainable way.”
Boeing, one of the founding members of AFRA, also has a vested interest in responsible recycling, says Carberry, who serves on AFRA’s board of directors. “When you’ve got a company acting rogue, then it looks bad for the whole industry,” he says.
Growing retirements
Jessica Kowal, a spokesperson for Boeing Commercial Airplanes, says the company estimates that as many as 14,000 commercial aircraft are likely to be retired over the next 20 years, as older, less fuel-efficient planes are replaced with newer, lighter and more fuel-efficient models. Toward that end, Kowal notes, the number of commercial aircraft in use is likely to double, to a level of around 41,000 planes, by 2032.
Separation issues Separate from the Aircraft Fleet Recycling Association’s (AFRA) “Best Management Practices (BMP) Guide” is the study of where and how aircraft aluminum, or other recyclable materials, can be reused. According to Boeing’s William Carberry, about 90 percent of the current value of a typical end-of-life aircraft is in the parts. “But that only constitutes about 20 percent of the weight,” he says. Among the planes being recycled today, aluminum is the largest recyclable component by weight, Carberry says. AFRA’s guidance document certainly recognizes the environmental benefit of recycling aluminum, he says, noting that recycled aluminum uses just 5 percent of the energy it takes to make new aluminum from bauxite. But today’s recycled aircraft aluminum typically isn’t as valuable as it could be, indicating one of the industry’s current challenges. At issue is the fact that some 15 different aluminum alloys are used to make a plane, and they’re held together with rivets. “Passengers really appreciate how tightly and well-bound those rivets really hold those aluminum panels together,” says Carberry, “but that’s really a challenge when you’re trying to separate those different aluminums.” If the various aluminum alloys aren’t separated, he says, they are suitable only for use in lower-end manufacturing applications. On the other hand, adds Carberry, “If you could separate that material into a high enough purity,” he says, “you could reuse it back into aviation.” Carberry says separation of the aluminum alloys could in fact lead to as much as a 100-fold increase in the scrap’s value. For instance, two different high-grade aluminum alloys are used for the top and bottom sections of airplane wings, where they provide the opposing characteristics of flex and compression. “The two are very different alloy chemistries, and when you mix them together, you destroy the value of both,” says Carberry. While the topic of how to deal with the various grades of aircraft aluminum is not one that’s covered under AFRA’s BMPs, it is a topic that AFRA members are now working to address. Carberry says AFRA members are studying an improved shredding technology designed to separate the different alloys. “There’s a need for better technology,” Carberry concludes. He explains that aircraft-grade aluminum isn’t used in other industries. But if it’s recycled properly, a closed-loop system could develop. “Our goal is to try and keep aerospace materials in aerospace manufacturing,” Carberry says. AFRA is hoping its future efforts will help the industry do just that. |
Another key objective for Boeing, Kowal describes, is the company’s focus on sustainability and environmental stewardship. “Our goal as a company and as an industry is to reduce the environmental footprint of the industry,” she says. That can be done in a number of ways, including fuel efficiency, air traffic management, reduced waste and increased recycling. “We try to take a life-cycle approach,” she says.
With what looks like an increase in fleet retirements likely to occur in the years ahead, AFRA’s efforts are coming at an opportune time. Carberry says AFRA is working to add controls and guidelines to an industry that, for the most part is unregulated: the disassembly and recycling of end-of-life aircraft.
AFRA says its members represent every sector of the aviation industry, from manufacturing to materials recycling, and that leaders from every part of the value-chain have joined AFRA to develop end-of-life solutions. Some of the more recognizable names in AFRA’s membership list include ELG Metals, Magellan Aviation Services, Rolls-Royce, Pratt & Whitney and Schnitzer Steel.
AFRA’s founding organizations succeeded in creating a charter with regard to the management of end-of-life aircraft, explains Carberry. The goal was promoting both safety and environmental responsibility in what Carberry says can be a rather abrupt scrapping process.
“The act of taking an airplane apart is not regulated by any agency,” Carberry points out. Therefore, AFRA’s goal, he says, has been to create controls that would bring environmental responsibility and safety to the process.
Within a year of AFRA’s founding, the members had published a guidance document comprising four procedure statements guiding processes as well as providing checks and balances for the disassembly of aircraft. Those procedures were revised over the next couple of years. Then, in late 2011, says Carberry, another AFRA initiative, inspired by growing numbers of recycling industry members, emphasized metals recovery and recycling. That effort resulted in a set of about 30 specific measures AFRA members specified as best management practices for recycling of end-of-life aircraft.
“Basically, that guidance said that you will collect your material in a way that it can be segregated and integrity maintained to the pedigree of the material, and you will do it within the jurisdictional requirements of where you are located,” Carberry says of the AFRA initiative.
In recent months, he says, the organization has merged the disassembly and recycling guidelines into a single document. The end result, which was completed in 2013, has been one guidance document containing three major sections, says Carberry: facility, training and certification requirements; disassembly activities; and recycling activities.
AFRA says its “Best Management Practice (BMP) Guide” has significantly improved the management of end-of-life aircraft in terms of environmental and sustainable performance.
“AFRA has connected all of the dots in pulling together industry-developed best practice throughout the whole process,” explains Fraissignes. “There is now a one-stop shop of best practice, which runs from the moment an aircraft lands after completing its final service flight, right through to when the aircraft material is fully recycled. This has to be a welcome development in the industry.”
Looking at AFRA’s growing membership numbers, its efforts appear to be well-received. As of late 2013, the Washington, D.C.-based organization comprised around 71 member companies from around the world specializing in the management of aging aircraft fleets.
AFRA also has created an accreditation program, based on the BMPs, operated with the assistance of a third-party auditing group. AFRA Accredited Companies must pass rigorous audits to ensure compliance with the BMPs, the association says. Independent auditors measure the company’s performance in each area, be it dismantling, engine removal, recycling or a combination of these processes.
“Very few companies pass that the first time out,” says Carberry. He adds, “It’s meant to be an interactive program.”
Today, 26 companies around the world are accredited to the disassembly, recycling or disassembly and recycling BMPs. Currently six companies are accredited recyclers of aircraft under AFRA’s standards, and three of those companies also are AFRA-accredited disassemblers.
Fraissignes says a key benefit of accreditation and the BMPs is the reassurance of abiding by the best industry standards available. “It is also clear that those offering tenders for dismantling aircraft are looking favorably on AFRA members and those who are AFRA accredited,” he says. “The guide contains valuable solutions for aircraft dismantlers and recyclers who wish to show they are at the forefront of best practice within the industry. It also allows them to capture maximum value, by increasing the amount of materials that are available for recycling.”
On a global scale
An important distinction of the BMPs, Carberry says, is that they were intended to be global, because member companies are located in countries with widely differing environmental regulations.
“What the standard said was, ‘You should do certain things, and you should do them in a way that meets the jurisdictional requirements of where your facility is located,’” says Carberry. For instance, the BMPs don’t specify recycling rates. Instead, they identify practices for both aircraft disassembly and recycling that are determined to be environmentally responsible and safe.
“You could read them from the perspective of any country where your facility is located and they would have relevance,” says Carberry.
He also notes that just as there’s no law guiding aircraft disassembly and recycling, recycling companies don’t have to be accredited in order to recycle aircraft materials. But by publishing, maintaining and promoting the BMPs, AFRA says it hopes to stave off the creation of government regulations that could potentially hurt the aviation industry, Carberry says.
“The philosophy is, if the industry doesn’t take responsibility, then the regulators will take over.” And that, he adds, could have negative business consequences. “It’s never good to be regulated by the government when you can do it better yourself,” he says.
While it appears that a good number of planes are expected to be retired over the next two decades, not all of those will be immediately scrapped, Carberry says. In fact, he says, some retired planes can sit in desert parking lots for years before being dismantled. The number of expected retirements also could change, he explains, depending on a host of factors, including the health of the global economy and whether airlines decide to fly newer, more fuel-efficient planes or to continue flying older gas-guzzling models. Either way, the recycling of aircraft materials is likely to increase in the years ahead.
The author is an editor with the Recycling Today Media Group and can be reached at lmckenna@gie.net.
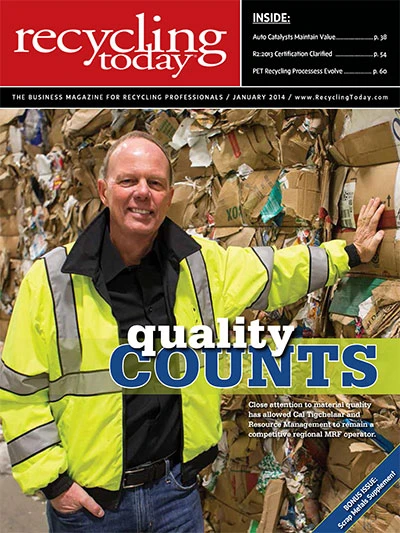
Explore the January 2014 Issue
Check out more from this issue and find your next story to read.
Latest from Recycling Today
- APR, RecyClass release partnership progress report
- Clearpoint Recycling, Enviroo sign PET supply contract
- Invista expanding ISCC Plus certification program
- Redwood partnership targets recycling of medium-format batteries
- Enfinite forms Hazardous & Specialty Waste Management Council
- Combined DRS, EPR legislation introduced in Rhode Island
- Eureka Recycling starts up newly upgraded MRF
- Reconomy Close the Gap campaign highlights need for circularity