New Ulm Steel & Recycling, New Ulm, Minn., buyers of scrap metal and sellers of new steel, serves southern Minnesota and surrounding areas. The company started as a service provider for residential, commercial and industrial metals recycling. Now, after a major investment in a shredder and downstream recycling equipment, New Ulm is enjoying a profitable venture in capturing ferrous and nonferrous metals for its growing customer base looking to purchase virtually clean recovered metal.
Working together
A significant part of New Ulm’s metal recovery operation comes from two 60-inch-by-72-inch electro agitating (E/A) scrap drum magnets from Eriez, Erie, Pa. These drum magnets are designed to work in tandem to recover valuable ferrous scrap metal before the nonferrous metal heads to other equipment in the downstream sorting process. Magnatech Engineering, the company that designed and manufactured New Ulm’s 72-inch-by-104-inch auto shredder and other recycling equipment for the operation, recommended the E/A drums.
“We found the Eriez scrap drums to be a good combination of price, size and value for the type of operation that New Ulm was looking to establish,” says Michael Graveman, president of Tonganoxie, Kan.-based Magnatech.
“Our customers ask us to be recycling equipment integrators, and we only work with reputable companies. In this case, we installed the Eriez scrap drums because of the excellent recovery and profitability.”
Eriez 5-Star Service Center offers rebuilds, repairs and recertification Designed to help recyclers keep equipment operating at peak performance and reduce downtime, Eriez 5-Star Service Center in Erie, Pa., is fully staffed and equipped to handle customers’ rebuild, repair and recertification needs, Eriez says. To ensure customer satisfaction, all rebuilt equipment leaves the 5-Star Service Center with an “as new” warranty, Eriez says. Typical rebuilt equipment includes vibratory feeders, drum magnet separators, wet drum separators and suspended electromagnets. Eriez says it uses original OEM parts for all jobs. The Eriez 5-Star Lift Magnet Certification/Refurbishment Program includes certification, refurbishment and magnet exchange. Eriez inspects lift magnets to ensure they remain in compliance with ASME (American Society of Mechanical Engineers) standards. Every magnet repaired by Eriez is returned with a “Certificate of Compliance,” guaranteeing the repairs and load tests of the magnet comply with ASME B30.20 as well as a one year “as new” warranty, the company says. The company says its 5-Star Service Center is equipped to remanufacture even the most complex systems. Additionally, Eriez says it can bring its 5-Star Service to customers’ facilities with available on-site field service. More information about the 5-Star Service Center is available by calling 888-999-ERIEZ (3743) or visiting http://service.eriez.com. |
The E/A scrap drums are positioned off the conveyor feed from the 4,000-horsepower auto shredder and immediately go to work removing large chunks of ferrous scrap—including meatballs. The scrap drums magnets are designed to offer a deep reach and wide pickup zone for increased recovery, which the New Ulm team says it has noticed and appreciated since the startup phase kicked into high gear in February 2013.
“Our operation is capable of moving 500 tons within a seven-hour day. We started with the shredder a little bit in December 2012, but our first big month was February 2013,” says Josh Luneburg, the second-generation owner of New Ulm. “A lot of the downstream equipment was recommended by Magnatech, and they made a very good decision in sourcing the Eriez scrap drums. The two, 60-inch drums were the right size for our shredder, and we’ve had no issues recovering a very high quality product without a lot of hand picking.
“Some manufacturers I researched said the scrap drums are capable of a 2 to 4 percent loss in iron, but after finetuning the Eriez scrap drums, we are down to a 0.5 percent loss in ferrous,” Luneburg observes. “A good dozen people have told us that we have the cleanest shred. It’s making our pickers’ jobs a lot easier when you get the majority of the ferrous out in the first pass.”
Improving performance
New Ulm decided on the two-drum installation to obtain the cleanest possible recovered metal. The first drum, suspended above the primary feed conveyor, picks up ferrous material from the shredder and carries it up and over the top to an intermediate conveyor section. The bulk of the nonmagnetic material falls to a take-away conveyor below the primary separator.
Because of the greatly reduced burden on the intermediate feed conveyor, the second drum often can be smaller and positioned closer to the conveyor. The drum rotates in a direction opposite to the material flow, which is designed to reduce jamming or bridging.
Clean metal with only a minimum of nonmagnetic material is deposited on the ferrous conveyor, the company says.
Luneburg says New Ulm installed two 60-inch-diameter drums to recover as much ferrous as possible and to decrease the time the pickers needed to monitor and remove leftover scrap. “It’s improving their productivity and increasing the amount of clean ferrous we’re getting in the long run,” he says of the second drum.
Raising the margin
“We don’t have the market share to be a high-volume player, so we’re trying to do the exact opposite in the industry: low volume and high, good margin,” Luneburg says. “Whether it’s steel or nonferrous, it’s all percentages. The more you can recover, the more profit you can make. However, you need to have the supporting equipment to do it.”
This article was submitted on behalf of Eriez, www.eriez.com.
Get curated news on YOUR industry.
Enter your email to receive our newsletters.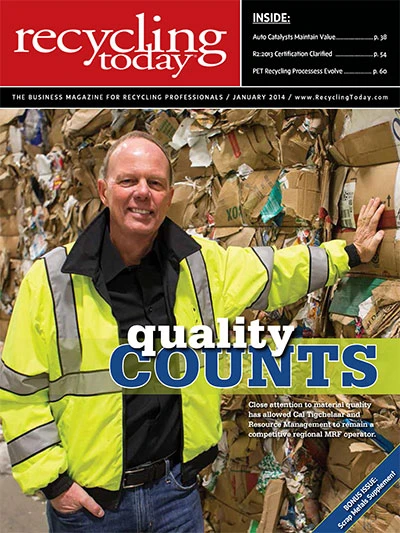
Explore the January 2014 Issue
Check out more from this issue and find your next story to read.
Latest from Recycling Today
- ReMA opposes European efforts seeking export restrictions for recyclables
- Fresh Perspective: Raj Bagaria
- Saica announces plans for second US site
- Update: Novelis produces first aluminum coil made fully from recycled end-of-life automotive scrap
- Aimplas doubles online course offerings
- Radius to be acquired by Toyota subsidiary
- Algoma EAF to start in April
- Erema sees strong demand for high-volume PET systems