Amsterdam-based Constellium is a global company with nearly 8,800 employees involved in many industry sectors, including aerospace, automotive and packaging.
The common thread weaving the company’s divisions together is made of aluminum, which Constellium produces in a variety of what it calls “aluminum solutions” using several different metallurgical processes.
As a producer of more than 1 million metric tons of aluminum annually at production sites around the world, Constellium pays close attention to how it sources raw materials and how products containing its metals are produced and then recycled when they become obsolete.
In the aerospace sector, where metallurgical chemistry is critical, Constellium has developed a closed-loop recycling process that it says benefits the environment while also offering the company a competitive edge.
Flying high
Constellium is a new name on the aluminum scene that was just introduced in 2011. However, the company’s product lines, facilities and many of its people trace back to three legacy companies with deep roots in aluminum: Alcan, AluSuisse and Pechiney.
In May 2011, the now-combined aluminum production activities of these three firms began operating under the Constellium name (excluding Alcan packaging, which had previously spun off as Novelis).
The company’s initial shareholders included mining firm Rio Tinto, the Apollo Global Management Fund and France’s Fonds Stratégique d’Investissement (FSI). Subsequently, Constellium issued public shares on the New York Stock Exchange in mid-2013.
Constellium’s three primary business units are:
- Automotive Structures and Industry, which produces crash-management systems and other structural and safety parts as well as extrusions and large profiles for the road and rail transportation, energy and other sectors;
- Packaging and Automotive Rolled Products, which develops, provides and recycles aluminum sheets and coils for packaging applications (beverage and food cans, closures, foils) as well as heat exchangers and some products for automotive body applications; and
- Aerospace and Transportation, which provides advanced aluminum and specialty materials products for the global aerospace, defense, transportation and industrial sectors. The business unit produces plate, sheet, extrusions and precision casting products for aerospace clients including Airbus, Boeing, Mitsubishi, Spirit, Embraer, Dassault, Bombardier, Kawasaki and others.
Among the initiatives within Constellium’s Paris-based Aerospace and Transportation division has been a closed-loop recycling process designed to recover its unique aerospace alloys.
The effort is being managed by Bruno Chenal, Constellium director for research and development. He has been with Constellium or its predecessor companies (first Pechiney, then Alcan) since 1987.
Three good reasons
The production of aircraft and aerospace components is a precision-intensive process that can involve considerable machining and metalworking.
“For some parts, only 10 percent of the aluminum products delivered by Constellium will actually fly or be part of the aircraft,” Chenal says. “That means as much as 90 percent of Constellium’s aluminum bought by our aerospace customers will be transformed into chips and offcuts during the manufacturing process.”
Constellium’s best interests are served by recovering this metal for several reasons, Chenal says.
By harvesting its own scrap, Constellium knows the chemistry will be right at the foundry or casting plant. “We know that we can make the most of the aluminum [scrap] and its ability to be 100 percent recycled without losing any of its properties,” he says.
This line of thinking has been critical with the recovery of Constellium’s Airware® aluminum-lithium material. Airware is designed for all parts of an aerostructure and was developed after considerable research involving nanoscale strengthening. (See the sidebar, “Rarefied Air,” available at www.RecyclingToday.com/rt0114-constellium-profile.aspx.)
Profit-and-loss thinking also figures heavily into making recycling a priority.
“From a recycling perspective, we had to develop a specific process dedicated to this family of advanced [materials],” says Chenal. “With Airware, we are using materials such as lithium and silver, which are very expensive. Finding a way to optimize the cost through recycling is part of the solution that we owe to our customers.”
As well, using a high percentage of internally sourced scrap provides a hedge “against the variations in the cost of aluminum on global metal markets,” he notes.
The recycling efforts also score well on sustainability scorecards. “The energy required to produce recycled aluminum is 20 times lower than that required for primary aluminum,” says Chenal, adding that “one [metric ton] of recycled aluminum saves four [metric tons] of bauxite.”
He continues, “The environmental impact of aircraft has become a key concern that we need to address at our level. The more calls for a greener aircraft, the better it is for our aluminum business, for sure. When one considers the major market drivers for the single-aisle civil aviation sector for the coming 20 years and beyond, it is clear that breakthrough solutions will be required to meet the stringent ACARE (Advisory Council for Aeronautics Research in Europe) targets for reduced fuel burn and reduced emissions.”
For Constellium that means a commitment to designing new technologies with specialized chemistries. “In that context, it is believed that airframe weight reductions and improved aerodynamics could contribute to at least 20 percent of these fuel burn targets, and on weight reduction and aerodynamics aluminum solutions will have a say,” says Chenal.
As Constellium introduces new aluminum solutions, it likely will be just as eager to recover them for its foundries and cast shops as it is to recover Airware.
In the loop
As explained by Chenal, the aluminum aerospace alloys recycling loop consists of more than one circle and more than one timeline.
In the shorter timeline, Constellium’s aerospace products shipped to manufacturers are generally machined and used within three to six months, generating offcut rates of up to 90 percent.
Working directly with these customers or with scrap companies, the goal of the closed-loop system is to fully recover this material stream to recapture the unique chemistry that will make it ideal feedstock.
The other 10 percent of Constellium’s products are now part of an airplane or helicopter that will have a useful life of from 30 to 40 years on average.
Although this fraction is dispersed globally and will follow many different timelines to obsolescence, Constellium is not giving up on the idea of working with aircraft dismantlers around the world to identify Airware and work with dismantlers to purchase this scrap for its foundries.
Establishing and managing these two loops involves considerable work. “The real challenge is within the management of supply chain, which involves a complex group of players,” Chenal says. “Lead times from demand forecast submitted to aluminum solutions suppliers to the final assembly line at OEMs can take up to 2.5 years, which is quite a long period of time.”
Aircraft orders can be made (or cancelled or delayed) in spurts, with global exhibitions and economic cycles figuring into the timing.
As well, it has become increasingly common for aircraft makers or buyers to request design changes in the midst of the production process to fill a given order. “At Constellium, we are working on how to be more predictive and be ready for both the specifications we are aware of and the specifications that could be added along the way,” Chenal says.
The closed-loop efforts fit into what Chenal and other Constellium executives see as “a holistic approach to aircraft manufacturing.” Thus, Chenal says, “We do sell not only sheets but true solutions. We always bear in mind that we’re selling aluminum solutions for fast evolving needs. We think that further breakthrough improvement is within reach through the co-optimization of materials, design and fabrication. Our holistic approach is thus definitely the right one, and all the more so as it enables us to develop tailored products for our customers.”
Those tailored products with their unique metallurgical properties maintain their intrinsic value as chips and offcuts. “Our products are meant to address all requirements from the supply chain, from design and engineering to manufacturing, maintenance and recycling,” he says.
The author is editor of Recycling Today and can be contacted at btaylor@gie.net. This article first ran in the July/August 2013 issue of Recycling Today Global Edition.
Get curated news on YOUR industry.
Enter your email to receive our newsletters.
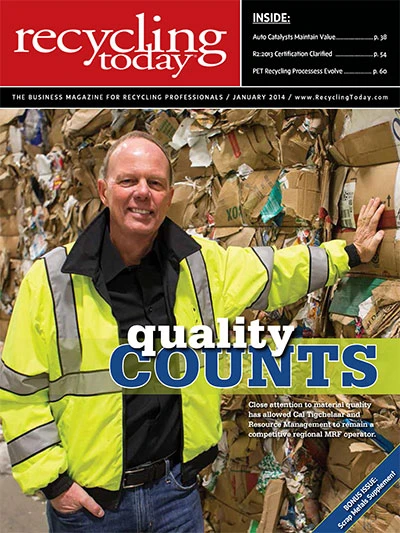
Explore the January 2014 Issue
Check out more from this issue and find your next story to read.
Latest from Recycling Today
- Astera runs into NIMBY concerns in Colorado
- ReMA opposes European efforts seeking export restrictions for recyclables
- Fresh Perspective: Raj Bagaria
- Saica announces plans for second US site
- Update: Novelis produces first aluminum coil made fully from recycled end-of-life automotive scrap
- Aimplas doubles online course offerings
- Radius to be acquired by Toyota subsidiary
- Algoma EAF to start in April