Few recycling-related events received more attention in 2013 than China’s Operation Green Fence. The coordinated effort by several Chinese government agencies to carefully scrutinize inbound shipments of recyclables caused considerable delays for all exporters and rejected shipments for many.
Cal Tigchelaar, president of material recovery facility (MRF) operator Resource Management Cos. (RMC), Chicago Ridge, Ill., is on the one hand reluctant to be seen as an advocate for Green Fence, saying, “I don’t want to be the one guy who says Green Fence is a good thing.”
On the other hand, he acknowledges that Green Fence-related traumatic effects were minimal for RMC, despite the fact that the company sells nearly all of its scrap paper tonnage to China. “We typically supply mills that have higher than average quality requirements, and we have always striven to meet their needs,” says Tigchelaar. “We are often paid a quality premium for our material, and so we feel that we were meeting Green Fence standards before the initiative was put in place.”
The lack of Green Fence drama testifies to RMC’s ability to adhere to a core principle of producing high-quality shipments of recyclables made from materials collected and processed via the single-stream method.
One contract and beyond
Tigchelaar founded RMC in 1991 to bid on the curbside recycling collection and processing contract for Naperville, Ill., a suburb of Chicago. He previously had been a partner in waste collection businesses in the Chicago area and in Michigan; but, to earn the Naperville contract, he says he decided to focus on “more modern collection and processing” of recyclables.
As RMC succeeded with the Naperville contract, it sought out and earned additional processing business. In 1995, RMC purchased a former railcar manufacturing plant in Chicago Ridge, Ill., to convert into a MRF.
The company’s ability to profitably handle materials collected by other haulers allowed it to keep expanding in the Chicago region and to bring its business model to the St. Louis area. Today RMC operates two MRFs in the Chicago area (including the Chicago Ridge plant) and a MRF in Earth City, Mo., near St. Louis.
In 2012, the Chicago Ridge MRF shipped out nearly 365,000 tons of material, making it the largest-volume MRF in North America, according to data collected by Recycling Today for its biennial list of largest MRFs. The company’s Plainfield, Ill., MRF ranked among the 35 largest with 120,000 tons shipped out, while the Earth City plant was not far behind with 108,000 tons shipped.
That RMC could achieve such scale as a regional operator is impressive enough. That the company also can pay such strict attention to quality that Operation Green Fence was largely a nonevent demonstrates the company has not sacrificed quality to achieve that scale.
Despite the considerable regional tonnage that RMC handles, Tigchelaar says it can still feel like RMC is a “minnow competing with whales” when the company’s size and financial resources are compared with the two large publicly traded solid waste and recycling companies that operate MRFs from coast to coast.
The company’s ability to keep swimming in those waters has been tied to several strategies, including not competing on the hauling side (the Naperville contract remains the sole RMC collection contract) and keeping a close eye on the changing nature of end markets for recyclables.
Glass half full
In the past several years, however, some consumers of recycled glass have made an effort to upgrade the value of the material and to provide a home for it, though they need the cooperation of MRF operators such as Resource Management Cos. (RMC), Chicago Ridge, Ill. Cal Tigchelaar, president of RMC, says he considers his company’s treatment of its inbound glass a successful turnaround story in recent years. “We have a supply of glass that is 100 percent fractured when we receive it, and it’s mixed with residues,” says Tigchelaar. “Initially, we attacked that stream from more of a cost-control aspect,” he adds, citing an approach taken by many MRF operators. With encouragement from some potential recycled glass buyers, Tigchelaar says RMC began investing to change its approach to the glass that flows into its MRFs. Among the ways RMC processes its glass is to:
“The custom crushing technique we use on glass to meet the specification for use as raw material in insulation manufacturing is a technology we developed ourselves,” says Tigchelaar. “Broken glass generated in a MRF operation is typically contaminated by organic material in percentages of up to 30 percent. Crushed glass cullet suitable for use as a feedstock for fiberglass insulation manufacturing must not exceed an organic contamination threshold of less than one-fifth of 1 percent.” It took a considerable amount of effort to create a system to meet the specification, but RMC says it is now able to recover 100 percent of the broken glass generated in its MRF operations. |
Home and away
RMC’s volume growth as a MRF processor occurred during the late 1990s and the early part of the new millennium, coinciding with the emergence of China as the leading global buyer of scrap commodities.
With its locations in America’s interior, far from Long Beach and other major port facilities, RMC could have chosen to focus on domestic consumers while allowing brokers to make connections with end markets in Asia.
Most of RMC’s plastic, aluminum, steel and glass shipments continue to head to domestic destinations, including secondary aluminum producers and plastics reprocessors such as KW Plastics, Troy, Ala.
On the recovered fiber side, however, Tigchelaar has positioned RMC to pivot toward the Far East. “Except for some spot OCC (old corrugated containers) selling, all our paper is now exported,” says Tigchelaar. “Chicago is every bit as much of an export area now as the West Coast or East Coast, and that has to do with Chicago being such a distribution hub.”
RMC recognized an opportunity in Chicago’s distribution-hub status in the form of overseas containers arriving in the region filled with small appliances, toys, clothing and other finished goods. The company zeroed in on a distribution center hub in Elwood, Ill., in particular.
“There are about 15 trains per day going from Elwood industrial parks to Los Angeles and back,” says Tigchelaar. “They are bringing in retail goods for Home Depot, Wal-Mart and other retailers and importers and going back to California with agricultural commodities or scrap paper.”
RMC has subsequently leased a 260,000-square-foot facility in Elwood amid the big box and online retailer distribution centers. The building houses balers to process OCC, plastic film and other commodities generated at the nearby distribution hubs but primarily serves as a transloading facility to load bales created at other MRFs into the ocean-going containers emptied by the retailers.
Mike Koh serves as president of RMC International Inc., a trading and logistics arm based in City of Industry, Calif., that is involved in the sale and transportation arrangements for the containers loaded in Elwood.
“The rates we get are inclusive from Elwood to China, including transloading in Los Angeles,” says Koh, who also buys material generated by third parties to sell to destinations in China or South Korea.
“The fact that we have our own direct trading company, managed by Mike, is a big advantage,” says Tigchelaar. “The coupling of our RMC International office in the Los Angeles area (run by Koh) with our RMC Logistics facility in Elwood gives our company direct access to overseas customers and provides efficient movement of material from our MRFs to Asia regardless of market conditions,” says Tigchelaar. “Mike Koh’s ability to stay in close contact with our Asian markets and our attention to the quality concerns of our customers gives us a preferred position when mills cut back on their orders,” he adds, referring to RMC’s ability to be a preferred seller when mills cut back on their orders.
In the details
In addition to strategic moves that affect trading options, RMC has put considerable thought into processing. The company’s inbound stream arrives almost completely in a commingled, single-stream format.
The positive and negative sides of single-stream have been the same for RMC as they have for other MRF operators, notes Tigchelaar. “The single-stream switch has brought growth to us—probably 20 to 30 percent more material—although it does increase the residue rate,” he comments.
RMC has taken its own approach to how it untangles the commingled stream. “We don’t buy complete systems from any of the equipment makers,” says Tigchelaar. “All of our conveyors and many of our screens and other equipment are designed and manufactured by CMD Conveyor, a company with which we have an exclusive arrangement. Our system design incorporates redundancies that provide our plants with almost 100 percent uptime.”
The company buys balers and other components from global equipment providers (See “Resource Management Cos. at a glance” above), but RMC has been wary of viewing automation as a cure-all, especially when producing recovered fiber grades, Tigchelaar says.
“We have not used optical sorting for scrap paper, and we don’t intend to,” says Tigchelaar. He says that some of the substandard bales that brought about the Green Fence reaction were caused by companies that relied solely on mechanical and optical sorting and “got away with it” for several years. “Green Fence means people with no manual sorters on their paper lines are in a real jam. We have long used mechanical systems for primary sorting and then people to clean it up.”
As newspaper readership has diminished, and while other MRF operators were retreating from the ONP (old newspapers) grade, RMC has been one of the last to do so. “The mixed paper grade coming out of the average MRF is now full of ONP, and the price spread between mixed and news has narrowed,” says Tigchelaar. “But we still get most of our newspaper into ONP bales. We make far more ONP than a lot of other MRF operators, although [as a grade] it will continue to disappear,” he predicts.
RMC also has been one of the pioneers in capturing more value from the glass stream, investing in improved processing techniques while identifying several viable end markets. (See the “Glass half full” above)
Clearing the fence
RMC ships nearly all of its recovered fiber to China, so it was a candidate for rejected loads prompted by a Green Fence-related inspection. But RMC President Cal Tigchelaar says the increased scrutiny from China has brought a late-arriving reward to some recyclers. “I’ve been going to Asia since 1997, and invariably in a paper mill we’d look at inventory of our material against others and I’d wonder why we bothered to strive for quality,” he comments. “Now I finally feel vindicated to some extent.” “For us, Green Fence really didn’t have as much of a negative consequence because we produce a good quality of paper,” says Mike Koh, president of RMC International Inc., City of Industry, Calif. “The people we do business with in China actually now want to do more business with us.” On the plastic scrap side, Tigchelaar says he believes the post-Green Fence difficulty of shipping mixed plastic scrap to China may yield some positive results as well. “We’re seeing this fundamental shift in what China will allow to be shipped in as feedstock, and it is opening doors for plastics reprocessors in North America.” The policy shift in China could provide an opportunity for RMC to further vertically integrate by engaging in post-MRF processing of some plastics, says Tigchelaar. |
Not standing still
While noting that he has been proud of RMC’s ability as a minnow to “compete with the whales,” Tigchelaar also says RMC faces no shortage of challenges in the near future.
Automated single-stream collection has been a positive in terms of worker safety and in keeping the labor costs of haulers in check, notes Tigchelaar. The downside has been increased volumes of nonrecyclable items arriving in RMC’s MRFs. (See the sidebar “Under the lid”)
Although RMC has thus far benefitted from staying ahead in terms of shipment quality, additional challenges are as unwelcome at RMC as at other MRF operators.
Tigchelaar says RMC is positioned to take on such challenges in large part because of the caliber of people in the company’s management and operations ranks.
Among those employees are other members of Tigchelaar’s family in Illinois (a son and son-in-law) and members of Koh’s family in California (his wife and son). Among the many nonfamily members who have earned considerable tenure with RMC is Senior Vice President Greg Maxwell, who wears multiple hats within the organization, Tigchelaar says.
“It may sound like a cliché, but the strength of the company really is found in the quality and longevity of the people who run it,” he says. “In the early days when the company employed fewer than 20 people, I found myself trying to manage operations, sales, accounting, maintenance, personnel and everything in between and doing a poor job in all of these areas.”
That situation is better now. “We’ve got several long-term employees, many with us for over 15 years in a 22-year-old company,” says Tigchelaar, adding that long-term relationships with customers also are the norm. He says a “golden rule” mentality is one of the primary reasons.
“Treating our employees and suppliers the same way we would like to be treated ourselves makes life very easy—doors open much easier when you have that reputation,” he comments. “It’s the right way to behave and it makes a lot of business sense to have integrity in everything you do.”
Under the lidAutomation has advanced not only in the sorting of recyclables but also in the collection of them. Cal Tigchelaar, president of material recovery facility (MRF) operator Resource Management Cos. (RMC), Chicago Ridge, Ill., says there are good and bad aspects to this. “The advancement in automated cart tipping is a great thing,” says Tigchelaar, when considered in terms of a reduction in back injuries to workers or labor costs for haulers or for keeping materials dry in bad weather. “However, in the days of blue boxes, a driver could see something that didn’t belong there,” notes Tigchelaar. “Now there is zero scrutiny in the collection process.” No scrutiny at the curb means anything a resident puts in his or her 96-gallon cart ends up at the MRF. “It puts a strain on efficient sorting processes when 10 to 15 percent of the material coming into a MRF may not belong there,” says Tigchelaar, who adds that RMC sees things ranging from toys, swimming pool liners or even weapons coming into its plants. “If you’re paying for this material, you need to know what you are buying. It needs to be kept in mind that some of this is not being recycled,” he states. |
The author is editor of Recycling Today and can be contacted at btaylor@gie.net.
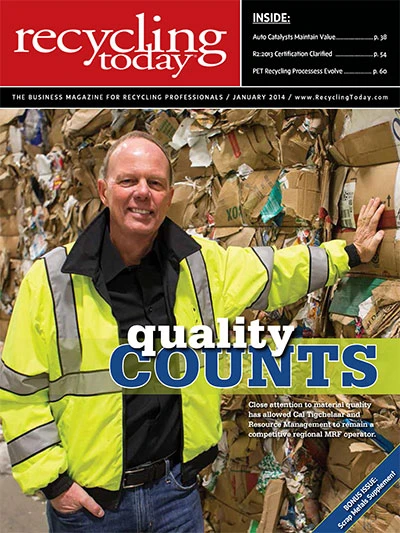
Explore the January 2014 Issue
Check out more from this issue and find your next story to read.
Latest from Recycling Today
- Astera runs into NIMBY concerns in Colorado
- ReMA opposes European efforts seeking export restrictions for recyclables
- Fresh Perspective: Raj Bagaria
- Saica announces plans for second US site
- Update: Novelis produces first aluminum coil made fully from recycled end-of-life automotive scrap
- Aimplas doubles online course offerings
- Radius to be acquired by Toyota subsidiary
- Algoma EAF to start in April