> METALS
MetalX Opens Indiana Scrap Facility
A new company founded by the Rifkin family, former co-owners of OmniSource Corp., has opened its first scrap metal facility in Waterloo, Ind.
The Rifkins sold their stake in Fort Wayne, Ind.-based OmniSource to Steel Dynamics Inc. (SDI) in 2007, ultimately leaving the company they helped found. After selling the company, the Rifkins started a venture capital firm while waiting for the end of a five-year noncompete contract they had signed with SDI. With that contract now concluded, Rifkin family members have opened MetalX, which will handle ferrous and nonferrous scrap.
According to the company, its recycling facility and corporate headquarters are located on a 70-acre site in Waterloo, Ind. MetalX says it began accepting wholesale and corporate business late in 2012, opening to the general public Dec. 1, 2012.
“We are excited to return to the scrap business,” says Danny Rifkin, MetalX president and CEO. “We followed the metals sector during our hiatus and believe the effects of consolidation and the recession have created new opportunities. Even though the landscape has changed dramatically, an independent company with a different approach and more efficient cost structure can be successful.”
MetalX says the facility will use the latest technologies and has been designed for maximum efficiency, offering customers a new level of convenience and service.
The company says it expects to employ as many as 75 people by spring of 2013.
In addition to Danny, Rick and Marty Rifkin, MetalX includes a number of other scrap industry veterans, including John Marynowski, Jim Ustian, Paul Everett, Jeff Rynearson, David Stage, Steve King, Brian Brown and Shari Zink.
“The town of Waterloo has been excellent to work with, as has DeKalb County,” Rifkin says. “While we envision our company’s growth to eventually include operations in other regions, we see this as our base and plan to keep investing in Fort Wayne and Northeast Indiana.”
> PAPER
Atlantic Packaging Reopens Ontario Mill
Atlantic Packaging Products, based in Scarborough, Ontario, Canada, has announced plans to reopen its Whitby, Ontario, paper mill by March 2013.
The mill, formerly a producer of newsprint, will be upgraded to produce 100-percent-recycled lightweight paper that will be used in high-performance corrugated packaging products, the company says.
Atlantic Packaging President Dave Boles says, “What we’re talking about is a disruptive technology that is capable of producing low basis weights (lighter paper) with sustainability and strength characteristics unlike anything in corrugated packaging today.”
Boles says large retailers’ sustainability objectives are driving the industry and Atlantic will be able to provide North America’s “most sustainable corrugated packaging option.”
> METALS
Steel Recycling Reaches 92 Percent in 2011
The Steel Recycling Institute (SRI) says the U.S. steel recycling rate reached a record 92 percent in 2011, with more than 85 million tons of steel scrap consumed. This represents an increase of nearly 10 million net tons from 2010.
“This high level of scrap consumption is a reflection of the North American steel industry’s commitment to conserving energy and natural resources,” says Gregory Crawford, executive director of SRI. “The use of steel in everyday products, including packaging, appliances, automotive and construction, ensures quality while also supporting product stewardship, knowing that these products are routinely recycled at the end of their use, thanks to steel.”
Pittsburgh-based SRI says the recycling rate for steel packaging in 2011 reached 70.8 percent, with more than 1.5 million net tons of steel recycled. The automobile recycling rate stood at 94.5 percent, while appliance recycling reached 90 percent, with more than 2.9 million net tons of steel recycled. The recycling rate for construction plates and beams was 98 percent, while the rate for construction rebar held steady in 2011 at around 70 percent.
“While steel continues to be North America’s most recycled material, there is still progress that can be made,” Crawford says.
“Educating recycling coordinators and consumers on the inclusion of materials, especially empty steel aerosol cans, will increase the overall tonnage for the industry.”
> PLASTICS
ACC Recognizes Plastics Recyclers
The American Chemistry Council (ACC), Washington, D.C., has recognized KW Plastics, Safeplay Systems and Sony Electronics Inc. for developing innovative processes and products using postconsumer recycled plastics with its Innovation in Plastics Recycling awards.
Steve Russell, vice president of plastics for ACC, says, “Thanks to the creative advancements brought about by these recyclers and others like them, we are able to keep more valuable plastics out of landfills than ever before. Used plastics are too valuable to waste and can be recycled to make high-quality, innovative products, such as furniture, car parts, home building products, fashion and packaging.”
The ACC recognized KW Plastics, Troy, Ala., for its approaches to recycling postconsumer polypropylene (PP) packaging. Despite difficulties experienced by many reclaimers in handling PP, KW Plastics has developed processes, specifications and equipment to allow the processing of PP yogurt cups, butter tubs, ketchup bottles, juice boxes and corrugated yard signs as part of an integrated processing system. It also is the first domestic reprocessor of woven and nonwoven flexible PP.
KW Plastics can reprocess 450 million pounds of high-density polyethylene (HDPE) and 300 million pounds of PP annually.
“As the world’s largest plastics recycler, KW Plastics has often been the leader in developing new markets and technologies to divert plastics from the landfill while creating jobs and revenue for the domestic economy,” says Stephanie Baker, director of market development for KW Plastics’ recycling division. “The innovations we have implemented, together with cooperative efforts with our partners and suppliers, are making plastics recycling easier than ever before.”
Safeplay Systems, based in Marietta, Ga., won for EcoPlay, its line of playground equipment for schools and parks made from a minimum of 95 percent postconsumer recycled HDPE. Safeplay has its own recycling program and accepts all its products for recycling at the end of their useful lives.
Eric Torrey, director of marketing for Safeplay Systems, says, “We are proud of our high-performance polypropylene structures that don’t splinter, crack, swell or rust and are virtually maintenance free. But more than that, environmental stewardship is an integral part of Safeplay Systems’ business, and we are honored to be recognized for our innovations in plastics recycling.”
Based in San Diego, Sony Electronics Inc. won for its development of SoRPlas, a material made from 99 percent recycled polycarbonate (PC) that is used in the housings of some of Sony’s popular consumer products, particularly in high-end cameras. To make SoRPlas, Sony uses 50 percent postindustrial scrap from optical disc manufacturing and 50 percent postconsumer recycled plastics from end-of-life products, containers and other items. In total, the Sony Group uses more than 17,000 tons of recycled plastics per year, including SoRPlas, in various products.
“Sony is dedicated to protecting and improving the environment in all parts of our business,” says Doug Smith, director of corporate environmental affairs for Sony Electronics Inc. “We are excited to be recognized for developing SoRPlas, a durable resin made from recycled polycarbonate that helps to conserve resources and reduce emissions in the manufacturing process and we are committed to expanding the use of recycled plastics in our products as research continues.”
> METALS
Mervis Opens Recycling Facility in Indiana
Mervis Industries Inc., a scrap metal recycling company based in Danville, Ill., has opened what it calls a full-service recycling facility in Crawfordsville, Ind., under its Advantage Recycling division. The new recycling plant is situated on 25 acres with an additional 10 acres available for future development, the company’s Michael Mervis says.
He says Advantage Recycling Crawfordsville is near Nucor Corp.’s Crawfordsville steel mill, making the location ideal. The recycling facility also is adjacent to a major highway.
The company executive also says the new facility includes some of the most updated equipment available on the market and ample concrete paving designed to ensure that it is easily accessible for commercial and retail customers. The plant has 10-foot berms on the perimeter and an 8-foot screen to ensure the operation is not visible from the highway, he adds.
In addition to offering full-service metals recycling operations, the new location will be the headquarters of Mervis’ transportation division.
Mervis also says the new facility reflects the company’s strategy to upgrade and convert its older peddler yards into facilities that are readily accessible by large industrial accounts as well as by retail clients.
Along with ferrous and nonferrous metals, Advantage Recycling Crawfordville will accept obsolete electronics.
Mervis says that by the end of 2013, the company planned to have all of its retail recycling facilities operating under the Advantage name. At the close of 2012, three facilities were operating under the Advantage name.
The company also is working to open a new scrap metal processing facility at an as-yet undisclosed location, which it expects to have operational in the first half of 2013.
> ELECTRONICS
Forward Progress
Obsolete electronics likely represent the fastest-growing stream of scrap materials, which means recyclers, researchers and trade organizations alike are scrambling to keep pace with the growth.
In two different presentations at the Electronics Recycling Asia conference in November, a researcher from an institute in South Korea and the president of the Washington, D.C.-based Institute of Scrap Recycling Industries Inc. (ISRI) talked about how their organizations are addressing the fast-paced growth.
ISRI’s Robin Weiner referred to obsolete electronics recycling as “the fastest-growing of recycling segments,” saying some 3 to 4 million tons of electronic scrap are now collected annually in the United States, with “75 percent from the commercial or business sector.”
Weiner said 70 percent of the collected e-scrap is processed and recycled within the United States and “resold as specification-grade commodities.” Some 10 percent of the collected volume is refurbished or consists of components that are resold, while some 18 percent is exported as reusable equipment.
She said ISRI preferred “positive intervention” when dealing with the rest of the world rather than advocating for “prohibitive” export bans. “Sharing best practices and offering certification overseas is the way to turn the tide on irresponsible recycling,” Weiner said.
Dr. Hyun Seon Hong, executive director of South Korea’s Institute for Advanced Engineering, provided an update on that country’s liquid crystal display (LCD) and other flat-panel recycling efforts.
Challenges for recyclers can include fasteners that make the dismantling process difficult and the “uncertain” value of fractions, such as glass and the rare earth element indium.
Hong said the institute is conducting research to overcome these challenges, since the recycling of 13,000 tons of obsolete electronics can result in 12,000 tons of CO2 emissions reductions.
The Electronics Recycling Asia conference, organized by ICM AG, was Nov. 13-16, 2012, in Guangzhou, China.
> PAPER
Pioneer Industries Opens New Location
Minneapolis-based Pioneer Industries International, a privately owned recycling firm serving the Midwest, has recently opened a plant in Milwaukee, its eighth location.
Pioneer’s Milwaukee plant will offer a full slate of recycling services and will process a wide range of materials, including paper and printer grades, cardboard, hard and soft plastics, packaging materials (including polystyrene) and metal.
The company’s leadership includes individuals who were formerly with a prominent recycling company that had directly serviced the Wisconsin market until 2004.
According to Pioneer, “The principals of excellent customer service, strong end-user relationships and being a true sustainability partner to its customers resonate within this new venture just as it did before.”
The Milwaukee facility has added eight new hires since opening in August. The company says it anticipates further expansion at the facility.
Pioneer Industries has operations in Minneapolis; Chicago; Kansas City, Kan.; Kansas City, Mo.; Dallas; Addison, Ill.; Oklahoma City; and Milwaukee.
> METALS
Novelis Breaks Ground on Aluminum Recycling Plant in Germany
Novelis, an aluminum rolling and recycling company headquartered in Atlanta, has broken ground on a $250 million aluminum recycling and casting center at its plant in Nachterstedt, Germany. The recycling center will be built adjacent to the company’s existing aluminum rolling mill and is expected to be completed by the middle of 2014.
When completed, Novelis says it will be able to produce 400,000 metric tons of aluminum sheet ingot yearly from recycled aluminum.
“This investment represents another step in delivering on our commitment to dramatically increase the recycled content of the rolled aluminum sheet we provide to our world-class global customers,” says Phil Martens, president and CEO of Novelis, “while also signifying our long-term commitment to the European market. The advanced sorting, processing and casting capabilities of the new Nachterstedt operation will propel us closer to our goal of 80 percent recycled content by 2020.”
The new center will support the company’s drive to increase end-of-life recycling in Europe, according to Novelis, processing used beverage cans (UBCs) as well as other forms of aluminum scrap from across continental Europe.
The Nachterstedt expansion is the latest in a series of recycling and casting expansion projects Novelis has launched in the past two years.
> MUNICIPAL
Pay-as-You-Throw Program Yields Results
This summer marked the three-year anniversary of the pay-as-you-throw (PAYT) program in Grafton, N.C. In the past three years, according to Assistant Town Administrator Kevin Mizikar, Grafton residents have reduced their solid waste from 5,169 tons in 2009 to 3,041 tons in 2012, a 41 percent reduction. Additionally, recycling efforts have nearly doubled from 888 tons in 2009 to 1,744 tons in 2012. The town’s solid waste disposal costs have dropped more than $135,000 annually, topping out at $136,742 for the past fiscal year ending July 1, 2012.
“From the beginning, the residents of Grafton have supported the program, and the results have exceeded our expectations,” Town Administrator Tim McInerney says. “Recycling has increased dramatically, we’ve reduced our solid waste and we’ve saved more than $135,000 in waste disposal costs in each of the last three years, which has allowed us to help offset cost increases of other critical services.”
The goals of the PAYT program include increasing recycling and reducing solid waste.
Before PAYT was implemented, Grafton spent $357,178 to dispose of its solid waste in fiscal year 2009. With PAYT, in fiscal year 2012, the town spent $220,436, a savings of more than $135,000, despite modest increases in tipping fees at the Wheelabrator waste-to-energy facility in Millbury, N.C.
“The decision to switch from the traditional 18-gallon recycling bins to the new 36- and 96-gallon Toters in June 2011 has paid off in dividends, further reducing our solid waste and increasing our recycling by almost 15 percent over 2011,” Mizikar says.
“The success of the Grafton program is proof positive that WasteZero’s Trash Metering is the single-most effective way a community can reduce its solid waste, increase recycling and generate savings and revenue,” says Mark Dancy, president of WasteZero, the town’s program provider. “The results are indicative of what we see in other cities and towns where residents support the program as enthusiastically as the town of Grafton has.”
WasteZero, a provider of waste-reduction programs, has offices in Cambridge, Mass.; Raleigh, N.C.; Murrells Inlet, S.C.; and Chicago.
> MUNICIPAL
Connecticut Economy Benefits from Recycling Industry
According to a study by the Connecticut Economic Resource Center Inc. (CERC), Connecticut’s recycling industry contributes $746 million and 4,800 jobs to the state’s economy. Since 2006, recycling has contributed nearly $5.17 billion to the state’s economy as measured in total sales, according to the study, which the Connecticut Resources Recovery Authority (CRRA) commissioned.
CRRA, based in Hartford, Conn., is a quasi-public agency established by the state in 1973 to modernize the state’s solid waste disposal. Its solid waste systems serve 74 Connecticut cities and towns, and it establishes best practices for solid waste disposal and recycling management on behalf of the municipalities it serves.
“This study shows recycling is a vibrant and growing sector of our state’s economy and that CRRA, as Connecticut’s recycling leader, is the cornerstone of that economic sector,” says CRRA President Thomas Kirk.
The recycling industry in Connecticut directly contributes $435 million in sales and provides for more than 2,710 jobs to the state’s economy, according to the study. When related industries are considered, recycling accounts for more than $738 million in total sales and 4,790 jobs per year.
From 2006 through 2012, CRRA’s economic impact was $883 million in total output, 861 jobs per year and $529 million in total value-added, which includes labor income of $362 million. In addition, CRRA, through its recycling processing center in Hartford and satellite transfer stations around the state, operates and accounts for 30 to 40 percent of the state’s total industry employment, according to the study.
Based in Rocky Hill, Conn., the Connecticut Economic Resource Center Inc. is a nonprofit corporation and public-private partnership that seeks to provide objective research, marketing and economic development resources consistent with making Connecticut a more competitive business environment.
> PLASTICS
Ravago, Avangard Innovative Join Forces
The plastics compounder and recycler Ravago Manufacturing Americas, headquartered in Orlando, Fla., and Avangard Innovative’s field service division, headquartered in Houston, have joined to create Ravago Avangard Innovative. The joint venture will combine Avangard Innovative’s expertise in its field-service program, called Natura, and Ravago’s relationships in the plastics industry and its processing capabilities.
Avangard Innovative Field Services offers a variety of environmental and industrial services at petrochemical plants, with a core focus on plastic resin production facilities.
Ravago has more than 50 years of experience serving the resins community, providing products to converters throughout the world. Ravago Manufacturing Americas will bring manufacturing and processing capabilities to the joint venture.
Chris Lendo, vice president and general manager, will run the Ravago Avangard Innovative business from the company’s existing site in Pasadena, Texas.
“With this investment and the formation of Ravago Avangard Innovative, we are raising the bar for producer services,” says Jim Ashton, president of Ravago Manufacturing Americas. “The Natura program provides a turnkey solution for a producer’s plant scrap management, environmental containment, regulatory compliance and industrial service needs.”
Rick Perez, CEO of Avangard Innovative, adds, “This opportunity will allow us to offer a complete package of producer services and a one-stop solution to our clients worldwide.”
Ravago’s activities include distribution, trading, risk solutions, recycling, toll processing, compounding and producer services. Ravago’s production division in the Americas is Ravago Manufacturing Americas (RMA), which operates 10 facilities in North America for processing plastics and rubber.
Avangard Innovative operates in 12 countries. The Avangard Innovative Field Services division offers a complete line of integrated field services solutions for recycling centers.
Get curated news on YOUR industry.
Enter your email to receive our newsletters.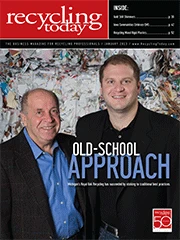
Explore the January 2013 Issue
Check out more from this issue and find your next story to read.
Latest from Recycling Today
- Altilium produces EV battery cells using recycled materials
- Brightmark enters subsidiaries of Indiana recycling facility into Chapter 11
- Freepoint Eco-Systems receives $50M loan for plastics recycling facility
- PET thermoform recycling the focus of new NAPCOR white paper
- Steel Dynamics cites favorable conditions in Q1
- Hydro starts up construction in Spain
- Green Cubes unveils forklift battery line
- Rebar association points to trade turmoil