According to the European Union WEEE (Waste Electrical and Electronic Equipment) Directive, 75 percent to 80 percent of all discarded electronic appliances in the EU should now be recycled. One of the reasons for this is to recover the large amount of valuable metals, such as copper and precious metals, inside these appliances.
Until now, recycling these products in some parts of the EU often meant manually dismantling the discarded devices and tediously sorting the various materials they contain.
However, this approach not only takes a lot of time, it also is a tough physical job, because the workers usually have to dismantle the appliances, some of which weigh tons, with a hammer and a screwdriver while on their knees. Also, much of the valuable materials can be lost because they are difficult to separate.
Adding Automation
Hellenic Recycling Center S.A. (EKAN), which has a contract through the Greek Ministry of the Environment to serve as a central appliance disposal company in southern Greece, has adopted an automated method that it uses to process large quantities of electronic scrap for recycling.
The system includes a shredder that was developed by engineers from the company Erdwich Zerkleinerungssysteme GmbH of Kaufering, Bavaria, Germany. Be it washing machines or motors, the shredding system can “gently process” six metric tons of electronic scrap every hour, according to Erdwich.
Washing machines, electric ovens and beverage vending machines comprise part of the 25,000 metric tons of electronic scrap sent to the EKAN facility in Corinth, Greece, every year. More than one-third of this material is steel or iron, and one-fifth is plastic. However, the focus at EKAN is on the valuable materials, such as copper, brass, aluminum and stainless steel, that are found in the drums of the washing machines or in the appliances’ motors, wires and cables.
Central Roles Every year the company Hellenic Recycling Center S.A. (EKAN S.A.), which was founded in 2002, processes roughly 25,000 metric tons of large electrical appliances, including washing machines, electric ovens and electronic control and switch cabinets. The company is the central disposal point in southern Greece and bills itself as the largest recycler of electronic scrap in the country. In 2004, EKAN joined Appliances Recycling S.A. and was authorized by the Greek Ministry of the Environment to handle waste electrical and electronic equipment (WEEE). The agreement has helped make the company a market leader in the WEEE recycling field. EKAN employs more than 100 people. Erdwich Zerkleinerungssysteme GmbH was founded by Hans Erdwich as a machine and metal engineering company in 1971. The Kaufering, Bavaria, Germany-based company currently has a workforce of 35. The company’s three core business areas are recycling and reprocessing of valuable materials; destruction of special waste of all kinds; and the volume reduction of waste or recyclable materials through shredding. In the refrigerator recycling system field, Erdwich GmbH bills itself as one of the top three companies in the world. |
“It is particularly difficult to separate the recyclable materials in large appliances of this kind,” says Norbert Streicher, the project manager at Erdwich responsible for the EKAN installation.
Until the Erdwich installation, the workers at EKAN had been engaged in the tedious job of dismantling the individual appliances by hand to remove their various components. This not only took a long time but also was very inefficient, the company says. The manual process also exposed EKAN’s employees to a high risk for injury when handling these heavy appliances.
This procedure was automated with the installation of the shredder. The Erdwich shredder, model HT520/2-2000, which was specially developed to process appliances and electronic scrap, is suitable for large appliances that weigh up to 992 pounds and features a capacity of six metric tons per hour.
Handle with Care
“It is very important when handling these appliances that they are opened carefully to prevent the parts from being destroyed by toxic substances and to prevent these substances being released,” Streicher says.
Therefore, the engineers at Erdwich have come up with a shredding method that carefully tears open the appliances using the working principles of slow rotation and low vibration, thereby allowing the parts inside to be released without being damaged, the company says.
Streicher adds that the unit can tolerate glass, iron and concrete without sustaining damage
Every knife shaft moves separately using a high-quality electro-hydraulic drive and is controlled electrically via an automation device made by Austria-based SPS Automation. “This allows both the speed and also the forward-backwards cycles of the shafts to be carefully adjusted for every application,” Streicher says.
The knife segments can be exchanged separately, allowing the operator to set the required particle sizes and edge lengths of the output individually. For example, a setting of 4 inches by 4 inches (100 millimeters by 100 millimeters) or 12 inches by 12 inches (300 millimeters by 300 millimeters) can be selected to suit further downstream processing.
If the knives show signs of wear, the blades can be welded on within the machine, which keeps maintenance costs very low.
Lending a Hand
The electronic scrap delivered to EKAN is initially picked up by grapples and transported via conveyor belts to the funnel of the shredder, which has an opening of roughly 78 inches by 47 inches (2,000 millimeters by 1,200 millimeters).
Sponsored Content
Labor that Works
With 25 years of experience, Leadpoint delivers cost-effective workforce solutions tailored to your needs. We handle the recruiting, hiring, training, and onboarding to deliver stable, productive, and safety-focused teams. Our commitment to safety and quality ensures peace of mind with a reliable workforce that helps you achieve your goals.
Sponsored Content
Labor that Works
With 25 years of experience, Leadpoint delivers cost-effective workforce solutions tailored to your needs. We handle the recruiting, hiring, training, and onboarding to deliver stable, productive, and safety-focused teams. Our commitment to safety and quality ensures peace of mind with a reliable workforce that helps you achieve your goals.
Sponsored Content
Labor that Works
With 25 years of experience, Leadpoint delivers cost-effective workforce solutions tailored to your needs. We handle the recruiting, hiring, training, and onboarding to deliver stable, productive, and safety-focused teams. Our commitment to safety and quality ensures peace of mind with a reliable workforce that helps you achieve your goals.
Sponsored Content
Labor that Works
With 25 years of experience, Leadpoint delivers cost-effective workforce solutions tailored to your needs. We handle the recruiting, hiring, training, and onboarding to deliver stable, productive, and safety-focused teams. Our commitment to safety and quality ensures peace of mind with a reliable workforce that helps you achieve your goals.
Sponsored Content
Labor that Works
With 25 years of experience, Leadpoint delivers cost-effective workforce solutions tailored to your needs. We handle the recruiting, hiring, training, and onboarding to deliver stable, productive, and safety-focused teams. Our commitment to safety and quality ensures peace of mind with a reliable workforce that helps you achieve your goals.
After the scrap has been gently shredded, a magnet separates the liberated iron and steel from the other material, sending the ferrous material to one sorting platform. The remaining materials are sent to a second sorting platform.
Employees do a negative sort of the iron and steel material, removing copper and aluminum scrap. The clean steel and iron scrap is then baled and sent to its melting destination.
At the second sorting platform, trained workers sort the mixed material to remove free and intact pollutants—such as batteries, mercury and condensers—and other materials, such as cables or stainless steel components.
From the sorting platforms, employees throw components they remove from the material stream into respective containers below via openings in the floor.
After the manual sorting process, the remaining material lands in a screening station with an integrated separation system. Here, the small mixed and type-sorted plastics, mixed nonferrous metals, copper and stainless steel parts and broken glass are separated into clean material streams.
The material is then feed to a granulator, which shreds it to a predefined size for further automated sorting. “This ensures that no valuable materials are lost,” says George Tzinis, head of engineering at EKAN. “We have also been able to ensure that no pollutants escape into the environment.”
The collected and segregated metals, in particular copper, gold, silver and palladium, are sold to consuming companies for use in new goods.
This article was submitted by Munich-based Pressebüro Beatrix Gebhardt-Seele on behalf of Erdwich Zerkleinerungssysteme GmbH and EKAN S.A. It first ran in Recycling Today Global Edition, a sister publication of Recycling Today.
Get curated news on YOUR industry.
Enter your email to receive our newsletters.
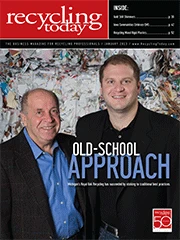
Explore the January 2013 Issue
Check out more from this issue and find your next story to read.
Latest from Recycling Today
- Green Cubes unveils forklift battery line
- Rebar association points to trade turmoil
- LumiCup offers single-use plastic alternative
- European project yields recycled-content ABS
- ICM to host colocated events in Shanghai
- Astera runs into NIMBY concerns in Colorado
- ReMA opposes European efforts seeking export restrictions for recyclables
- Fresh Perspective: Raj Bagaria