After a rapid price spike in 2011, users of rare earth metals quickly began considering how to best recycle the current above-ground supplies of these metals. However, despite their increase in value and common use in some types of electronics, how to profitably recycle rare earth metals and other minor metals has remained elusive.
In his 2007 book The Ingredients: a Guided Tour of the Elements, British chemist and author Philip Ball says a series of 14 elements with atomic numbers 57 through 70 are known on the periodic table as lanthanides and also by the label rare earths. Ball also notes that this second label is “a misnomer, for some are not particularly rare at all and they are metals, not earths.”
To further cloud things, recyclers and consumer electronics companies, when talking about reaching deeper into the obsolete electronics stream to recover materials, often lump other minor metals, such as cobalt, lithium and indium, into the rare earths category.
No matter how broadly they are defined or how their value rises or falls, interest in recovering metals beyond iron, copper, aluminum and precious metals from electronic scrap has strengthened, and progress is being made.
A Spike in Interest
A panel convened at the Electronics Recycling Asia conference, held in Guangzhou, China, in November of 2012, included comments from several panelists who pointed to significant barriers that remain before widespread recycling of rare earth metals can occur.
Freelance journalist Adam Minter moderated the panel and noted that prices for rare earth metals spiked in late 2010 and early 2011, then subsequently drifted back downward. “These kinds of price cycles will determine how much recycling takes place,” Minter said.
Professor Jinhui Li of China’s Tsinghua University commented that rare earths deserve their “rare” label, as the 130,000 metric tons produced in 2011 is a fraction of the 15 million metric tons of copper produced or the 1.5 billion metric tons of steel.
In an earlier presentation on rare earth metals recycling, Li noted that some 36 percent of the world’s rare earth metal reserves are believed to be in China, but that as of 2010 China’s mining activity was producing 94 percent of the world’s output.
From a mining viewpoint, panelist Christian Ekberg, a professor at Sweden’s Chalmers University of Technology, asked whether the potential supply of rare earth metals in the ground was especially lacking or whether regulations prohibiting mining are “the source of the problem.” The regulatory climate toward mining in much of the world, he suggested, is why China is nearly the sole source of output of mined rare earth metals such as yttrium, cerium, europium and terbium.
Ekberg also said rare earth metals “are rare because they are difficult to separate; this is why universities are involved—it is a challenge.”
Crystynna Ewe, the Singapore-based head of take-back for the Asia Pacific and Japan region for Dell Inc., said rare earth metals recycling “was a very new topic” for Dell, though the company considers product life cycles important and favors use of recycled content.
While some panelists and audience members expressed optimism that technological solutions to boost rare earth metals recycling will soon develop, Ekberg cautioned, “Technology will not automatically catch up. It is difficult to separate lanthanides from other materials. The technology is not emerging very fast, I must say.”
Li also pointed to attempts thus far to recover indium from LCD (liquid crystal display) monitors. At the current price of indium, “you’re going to lose money if you recycle it,” Li said.
At the previous year’s forum, held in November 2011 in Hong Kong, one of Ekberg’s students offered an overview of his research into using solvents to isolate indium while recycling LCD screens.
PhD student Yang Jiaxu of Chalmers University of Technology said, “LCD is the most sold type of display today and will consequently be a major portion of [electronic scrap] in the near future.”
In his experiments, Yang was able to use solvents to extract indium from other metals and materials, “although the separation of indium from zinc seems to be the most difficult,” he added.
Light and Attractive
Rare earth metals have become an important part of the economy in several different ways, though the two most widespread applications involve magnets, lighting and electronic image display.
Rare earth magnets, also known as permanent magnets, are used in the mining and metals recycling industries, so each of these two sectors has a direct interest in maintaining their availability and affordability. The two most common permanent magnet configurations use either neodymium or a samarium-cobalt alloy as their key materials.
Neodymium rare earth magnets have the biggest market share, and permanent magnets made with neodymium often include fellow rare earth metals terbium and dysprosium in their chemistry mix.
On the lighting and visual display side, europium, yttrium and terbium each have qualities of phosphorescence or fluorescence that make them ideal at transmitting certain colors in the light spectrum.
Although they are used in trace amounts per LCD screen or per fluorescent lamp, they can be found in every such screen, light tube or light bulb that is recycled. Whether they can be extracted, purified and aggregated in a way that makes economic sense remains the critical question, however.
Part of the Process Whether they are decades old or recent startups, many equipment makers who presented at the Electronics Recycling Asia conference, held in November 2012 in Guangzhou, China, say they can offer improved processing methods to recover rare earth metals. Joe Yob of Creative Recycling, Tampa, Fla., offered the viewpoint of a customer of the BluBox fluorescent lamp recycling system. The BluBox, made by Switzerland-based BluBox Trading AG, is designed to safely recover mercury from several types of obsolete items. Yob said Creative is using its BluBox to recycle “fluorescent tubes, compact fluorescent lamps, halogens, notebook computers and mobile phones.” The batteries of devices are removed first, he noted. Materials recovered using the BluBox include ferrous, glass, nonferrous, circuit board scrap, plastics and “lamp powder that contains rare earths.” Thomas Langer of German lighting company Osram AG said his company’s system for recycling fluorescent lamps includes the ability to recover rare earth elements in the form of a powder. “Europe has established quite a good collection system for end-of-life lamps,” said Langer, adding that Osram’s goal has been to capture these materials for reuse. |
“We are in a new stage,” Li said at the 2012 Electronics Asia Forum. “In the past, we were doing some ‘easy’ recycling. We are evolving,” he stated, adding that China’s government and recycling industries are now delving deeper to address the challenges and opportunities of recycling rare earth elements from the obsolete electronics stream.
Li said current efforts result in “a very serious waste of rare earth elements, and we need policies for the future.” Citing metals such as cobalt and lithium as well as rare earth elements, Li added, “The demand remains significant, so we do need to do significant work and have set policies. There is great room for improvement [and] new technologies.”
In Europe and North America, investments have been made to begin that improvement process. In October 2012, Brussels-based Solvay Group announced that it had opened two rare earth metals recycling plants in France. The two plants are designed to allow the company to diversify its supply of rare earth metals and preserve resources.
Solvay says it has developed a process to recover rare earth metals from end-of-life products that include new low-energy light bulbs, batteries and magnets. The company says it focuses on low-energy light bulbs because the recovery channels already exist. The light bulbs have six different rare earths—lanthanum, cerium, terbium, yttrium, europium and gadolinium—which Solvay says it is positioneed to recycle “while preserving 100 percent of their functional properties.”
The luminescent powders recovered are shipped to a Solvay Group facility in Saint-Fons, France, where the rare earth concentrate is extracted. The material then is sent to a Solvay rare earth metals recycling plant in Charente Maritime, France, which is equipped with additional separation technology. The separated rare earth metals are “reformulated into luminescent precursors to be reused to manufacture new lamps,” Solvay says.
Sponsored Content
Labor that Works
With 25 years of experience, Leadpoint delivers cost-effective workforce solutions tailored to your needs. We handle the recruiting, hiring, training, and onboarding to deliver stable, productive, and safety-focused teams. Our commitment to safety and quality ensures peace of mind with a reliable workforce that helps you achieve your goals.
Sponsored Content
Labor that Works
With 25 years of experience, Leadpoint delivers cost-effective workforce solutions tailored to your needs. We handle the recruiting, hiring, training, and onboarding to deliver stable, productive, and safety-focused teams. Our commitment to safety and quality ensures peace of mind with a reliable workforce that helps you achieve your goals.
Sponsored Content
Labor that Works
With 25 years of experience, Leadpoint delivers cost-effective workforce solutions tailored to your needs. We handle the recruiting, hiring, training, and onboarding to deliver stable, productive, and safety-focused teams. Our commitment to safety and quality ensures peace of mind with a reliable workforce that helps you achieve your goals.
Sponsored Content
Labor that Works
With 25 years of experience, Leadpoint delivers cost-effective workforce solutions tailored to your needs. We handle the recruiting, hiring, training, and onboarding to deliver stable, productive, and safety-focused teams. Our commitment to safety and quality ensures peace of mind with a reliable workforce that helps you achieve your goals.
Sponsored Content
Labor that Works
With 25 years of experience, Leadpoint delivers cost-effective workforce solutions tailored to your needs. We handle the recruiting, hiring, training, and onboarding to deliver stable, productive, and safety-focused teams. Our commitment to safety and quality ensures peace of mind with a reliable workforce that helps you achieve your goals.
In Pennsylvania, AERC Recycling Solutions is working with Global Tungsten & Powders (GTP) to recover rare earth metals from spent fluorescent lamps.
AERC and GTP started working together in 2008 to develop a process to recover rare earth materials from fluorescent lamps processed at the AERC facility in Allentown, Pa.
According to the two companies, AERC’s mercury retort process is followed by a process in which the mercury is removed prior to the recovery of rare earth metals. The AERC facility in Allentown is less than 150 miles from GTP’s plant in Towanda, Pa.
Widespread Attention
Judging by the amount of capital being invested and the time being dedicated to research throughout the world, the rare earth metals recycling frontier is the site of considerable activity.
At the Electronics Recycling Asia event, Dr. Hyun Seon Hong, executive director of South Korea’s Institute for Advanced Engineering, spoke about that country’s liquid crystal display (LCD) and other flat panel recycling efforts.
Recycling challenges include fasteners that make dismantling difficult and the “uncertain” value of fractions such as glass and the minor metal indium.
Hong said the Institute for Advanced Engineering is researching these challenges, since the recycling of 13,000 tons of obsolete electronics can result in 12,000 tons of CO2 emissions reductions.
Dr. Manis Kumar Jha of the CSIR-National Metallurgical Laboratory, Jamshedpur, India, said CSIR, in cooperation with a South Korean research institute, has developed a hydrometallurgical “organic swelling” treatment that offers an environmentally safe way to extract precious metals from obsolete circuit boards.
He added, “Steps for the extraction of rare earth metals from secondary sources are proposed to be done in future.”
If the effort is enough to lead to improvement, the recycling rate for rare earth and minor metals found in the scrap stream seems destined to increase.
The author is editorial director of Recycling Today and can be contacted at btaylor@gie.net.
Get curated news on YOUR industry.
Enter your email to receive our newsletters.
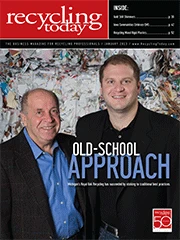
Explore the January 2013 Issue
Check out more from this issue and find your next story to read.
Latest from Recycling Today
- Green Cubes unveils forklift battery line
- Rebar association points to trade turmoil
- LumiCup offers single-use plastic alternative
- European project yields recycled-content ABS
- ICM to host colocated events in Shanghai
- Astera runs into NIMBY concerns in Colorado
- ReMA opposes European efforts seeking export restrictions for recyclables
- Fresh Perspective: Raj Bagaria