According to a statement on the Washington, D.C.-based Institute of Scrap Recycling Industries Inc. (ISRI) website, www.isri.org, lockout/tagout was one of the recycling industry’s most commonly cited violations of OSHA (Occupational Safety and Health Administration) standards, with fines totaling more than $400,000 in 2011.
Lockout/tagout procedures help employees avoid injuries that are the result of unexpected startup or release of stored energy in the machines they are servicing. According to the OSHA website, www.osha.org, “Workers servicing or maintaining machines or equipment may be seriously injured or killed if hazardous energy is not properly controlled. Injuries resulting from the failure to control hazardous energy during maintenance activities can be serious or fatal! Injuries may include electrocution, burns, crushing, cutting, lacerating, amputating or fracturing body parts and others.”
According to OSHA, workers who are injured on the job as the result of exposure to hazardous energy lose an average of 24 workdays for recuperation.
The OSHA standard for the control of hazardous energy for general industry (Lockout/Tagout, 29 CFR 1910.147) outlines procedures for addressing and controlling hazardous energy while servicing equipment. “Employers are also required to train each worker to ensure that they know, understand and are able to follow the applicable provisions of the hazardous energy control procedures. Workers must be trained in the purpose and function of the energy control program and have the knowledge and skills required for the safe application, usage and removal of the energy control devices,” OSHA notes.
EST Solutions President Susan Eppes says she has seen problems arise when the lockout/tagout procedure is complicated and time consuming. Typically, Eppes says, as many as eight locks can be hanging from one location on screening equipment used in material recovery facilities (MRFs) and it is not uncommon for someone to skip putting their lock on before entering the screen to clean it. Eppes adds that it’s also not all that uncommon to see only one lock in place even when up to five people are servicing the machine.
EST Solutions is a Houston-based safety and health consulting firm specializing in office ergonomics as well as in all areas of safety and regulatory compliance for the waste, recycling, manufacturing and service industries.
As an equipment supplier to the recycling industry, CP Manufacturing’s representatives often have heard their customers’ voice safety and productivity concerns regarding equipment maintenance. In response, the company has released a new disc screen for sorting paper from containers in MRFs that features a key-lock system designed to improve the lockout/tagout procedure.
CP Manufacturing is part of the CP Group, a San Diego-based supplier to the solid waste and recycling industries. In addition to CP Manufacturing, the CP Group includes MSS Inc., IPS Balers and Krause Manufacturing and Advanced MRF.
Jim Weller, CP design engineer and research and development manager, says, “This latest screen style represents feedback from our customers in every area, with a major focus on safety, access and extremely low maintenance. Screen technology has been around for quite a while now, and like the piston engine in your car, it can always be improved.”
Trapped Key System
Among the safety features CP added are mechanical backstops to lock rotors for cleaning, lanyards that can be attached to crossbars for easy access by maintenance personnel and a trapped-key system that is designed to add security to the existing lockout/tagout system.
To access the machine, service technicians must use a lockout system that CP calls the trapped-key system. Workers remove a key from the motor control center (MCC), shutting off power to the system. “There is a maintenance mode sequence on our touch screen. It’s an automatic process,” Weller says. “They now can open that door with the key that they have and access the screen safely.”
Katlynn Freeley, regional safety manager at ReCommunity Recycling, based in Charlotte, N.C., says, “The new key-lock system is a fail-safe way to make sure the screen cannot be started during maintenance. You cannot turn on the equipment unless both keys are in place—in order to get inside to do maintenance, you need to take one of the keys out of the MCC.” She adds, “This ensures the power is off.”
The screen also features a hydraulic folding floor so that workers do not have to stand on the screen’s rotors during maintenance.
Weller says the folding floor creates a platform for workers to stand on without fearing they will fall onto the conveyor below when they have to get inside of the screens to clear debris that has wrapped around the rotors.
“If two or three guys are standing on those rotors with their feet on the disks, they could start the rotors rolling backwards, and it would make it hard to stand on,” Weller says.
CP also has placed locks on the screens’ rotors to prevent them from rolling during servicing.
At the platform level, the company has added access doors in the tail section, eliminating the need for ladders.
Eppes says, “Generally if you make it easy for people to do something, they will go ahead and do it.” She says such measures could improve OSHA compliance at MRFs where lockout/tagout is concerned.
Closer to Zero
Safety concerns and potential lockout/tagout violations frequently occur when workers perform routine maintenance. Weller says customers said they would like to see a screen that required less maintenance, and CP decided to focus on several areas that typically require regular upkeep, such as drive components, roller chains and rotor couplings.
The company replaced chain drives with belt drives. Weller says the synchronous belts do not require lubrication or adjustments. With no regularly scheduled adjustments or lubrications needed on belt drives, workers are not exposed to situations that could pose possible safety hazards.
“I suggested CP engineers take a look at what actions were required by workers to clean screens and how often they needed to do this, as well as what it took to lock and tagout the system. They rose to the challenge,” Eppes says.
Lockout/tagout violations can be reduced by making the procedure as easy as possible, and that starts with machinery that provides convenient lockout/tagout points, she says.
The author is assistant editor of Recycling Today magazine and can be reached at kstoklosa@gie.net.
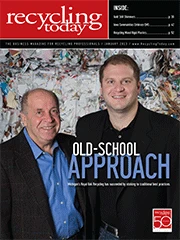
Explore the January 2013 Issue
Check out more from this issue and find your next story to read.
Latest from Recycling Today
- Toppoint Holdings expands chassis fleet
- Lego creates miniature tire recycling market
- Lux Research webinar examines chemical recycling timetables
- Plastics producer tracks pulse of wire recycling market
- Republic Services, Blue Polymers open Indianapolis recycling complex
- Altilium produces EV battery cells using recycled materials
- Brightmark enters subsidiaries of Indiana recycling facility into Chapter 11
- Freepoint Eco-Systems receives $50M loan for plastics recycling facility