Follow any supply chain for any product—backward or forward—and you will find industrial containers in use. Around the globe millions of steel and plastic drums, rigid intermediate bulk containers (IBCs) and flexible IBCs are being produced to safely store and transport the world’s goods. Although vital, manufacturing those containers requires the consumption of natural resources, including metal, resin and energy.
Because of growing expectations from stakeholders and increasing market competition, companies are looking for meaningful ways to reduce their environmental footprints and costs. In fact, according to a recent industry survey of packaging professionals, sustainability is the greatest challenge facing the global packaging industry—a bigger concern than costs and packaging availability. Corporate sustainability initiatives and programs such as the American Chemistry Council’s Responsible Care® are changing the metrics used by purchasing specialists, packaging engineers, recyclers and others as they re-evaluate their industrial packaging decisions.
Purchasing specialists, packaging engineers, recyclers and others are learning what the industrial packaging industry already knows: the best use of an industrial container is its reuse. Yet, decisions about how and when to work with reconditioned or remanufactured containers versus recycling and acquiring new containers can be challenging.
Obstacles to Reuse
Obstacles include how to evaluate and engage vendors offering used containers, assessing whether used containers are suitable for reconditioning or remanufacturing and how to acquire trustworthy reuse stock. Much of the industrial package reconditioning industry is fragmented, with few, if any, fully developed programs to meet the global needs of many manufacturers. Packaging professionals seeking more sustainable packaging options often find it challenging to locate reconditioners who can meet national and regional legal requirements and various program standards and who can provide verifiable stewardship practices.
Understanding the technology and processes required to extend the life cycle of industrial packaging also can prove problematic for the end user. Cleaning, a commonly used term, is actually a misnomer. Rather, reconditioning is the critical process, which actually starts with “cleaning” of the used container. For a steel drum, that process may potentially involve thermal cleaning. This is not merely a simple cleaning. The container, contents and other factors are considered. Often critical parts are exchanged for new parts. Steel drums go through additional testing and then are relacquered.
For plastic packaging, the process requires analysis of differing factors. Many plastic industrial containers are suitable for recycling. For IBCs, there are more options, which include exchanging components, such as valves that were in contact with the materials transported. In some cases the used IBC bottle must be replaced in a process known as “rebottling.” The used bottle is then recycled.
Depending, of course, on contents and condition of the drum when it is empty, as a general rule, a standard steel drum can be reused from three to seven times, depending on its condition and gauge, and a plastic drum can be reused up to eight times. Only when it cannot be reconditioned or remanufactured, should a container be slated for recycling.
Reporting Requirements
Reconditioning, remanufacturing and reuse are part of the considerations industrial packaging professionals make. Today, they also are seeking verifiable data, needed to document and measure sustainability initiatives.
From 2008 to 2011 EarthMinded™ LCS affiliate Greif commissioned several industrial packaging life-cycle assessment (LCA) studies to identify the impact of industrial packaging decisions on the environment.
The LCA evaluated a broad range of discharges and emissions from cradle to grave. The analysis included factors such as packaging material type, weight, how many times the container had been reconditioned and transport distances, among other factors. Each assessment of a container was unique because there is no one-size-fits-all formula—calculations are specific and detailed to the individual container.
The LCAs for industrial containers managed at Greif (and later EarthMinded LCS) were carried out by the Institute for Energy and Environmental Research (IFEU), a pioneer and specialist in packaging LCAs. The initial LCA work for assessing large steel drums, large plastic drums and classic composite IBCs underwent an independent critical external review, based on ISO standards for product LCAs targeting comparative assertion of products.
The data became the basis for an innovative proprietary reporting tool created by EarthMinded LCS. This tool allows packaging professionals to assess and understand the environmental impacts of various scenarios using common industrial container types.
The tool enables assessments of total packaging carbon footprint per site, total packaging carbon footprint per customer (whether it has one location or multiple locations across continents) and the environmental impacts of using alternatives, such as lighter weight and lighter gauge containers; containers with better emptying traits or more usable volume and different pallets; increasing trip rates; optimizing transport distances; and choosing to recycle containers at their end of life.
Ultimately, industrial packaging professionals can review the impacts of changes in their packaging decisions—from transport modes to reconditioning and disposal options—and how those changes affect their corporate sustainability goals.
The drive for better data and better results is shaping packaging and even collection costs and decisions. Industrial packaging collection services, which will need to be global and strongly managed, provide a practical alternative to storing used industrial packages on site or transporting them to the landfill with the attendant trucking costs and disposal fees. Reconditioning operations generate industrial packaging that can be sold at a discount to new packaging and, subsequently, reintroduced into the supply chain, which will continue the evolution of packaging life cycle, help contain costs and improve sustainability.
The author is president of EarthMinded™ LCS, the creator of a global network of industrial packaging reconditioners. The EarthMinded LCS network, launched in November 2011 by Greif, includes Pack2Pack (eight sites in seven European countries), Container Life Cycle Management (a joint venture including Greif, IndyDrum, Drumco of Arkansas and Drumco of Tennessee, which serves central and southern United States), Container Management Services (western United States), West Texas Drum Co. (Gulf Coast), Mid-America Steel Drum Co. Inc. (the Upper Midwest) and Great Western Containers (Canada).
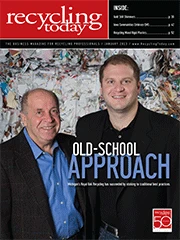
Explore the January 2013 Issue
Check out more from this issue and find your next story to read.
Latest from Recycling Today
- Athens Services terminates contract with San Marino, California
- Partners develop specialty response vehicles for LIB fires
- Sonoco cites OCC shortage for price hike in Europe
- British Steel mill’s future up in the air
- Tomra applies GAINnext AI technology to upgrade wrought aluminum scrap
- Redwood Materials partners with Isuzu Commercial Truck
- The push for more supply
- ReMA PSI Chapter adds 7 members