Few things in the everyday operation of a scrap processing facility are as important as keeping material flowing from pile to processing to shipment. Interrupt any facet of that stream, and production stops, turning what was once a bustling, money-making venture into a collection of idle, expensive, non-productive equipment.
When the stationary shear at Schnitzer Southeast’s Birmingham, Ala., facility went down for major repairs, just such a major interruption loomed large. The shear was an aging but vital component of scrap recycling operations at the processing site.
However, quick thinking—along with a pair of mobile shears to augment an existing unit the company had in the yard—has enabled production at the Schnitzer Southeast Birmingham location to continue largely unabated. At the same time, a railcar processing operation has kept growing, and the facility’s bottom line has remained intact. You might refer to it as “shear determination.”
14 AND COUNTING
Schnitzer Southeast was formed in 2005 when Portland, Ore.-based Schnitzer Steel Industries Inc. purchased Regional Recycling, a Birmingham scrap recycler with nine yards in Georgia and Alabama.
According to David Romanoff, the operating unit’s executive director and former co-owner of Regional Recycling, Southeast has seen steady growth since being acquired by Schnitzer. Today, the division operates 14 locations in the Southeastern United States as well as three in Puerto Rico.
Romanoff says that, despite the acquisition, the core of what was once Regional Recycling has remained unchanged, testimony to the value Schnitzer placed on the company. He and his business partner, Byron Kopman, retain executive director positions with Schnitzer Southeast, and the workforce has grown. “We employ about 450 people throughout the Southeast and know that Schnitzer shares our belief that our people are our most valued asset,” says Kopman.
MAJOR REBUILD
Schnitzer Southeast’s Birmingham yard is one of its larger sites, covering approximately 19 acres just southwest of the city’s central business district. The location takes in material from throughout Alabama, Georgia and Tennessee.
If the material is too large for the hopper of its 30-plus-year-old Harris Model 1350 stationary shear, the Schnitzer Southeast employees downsize it using a Genesis GXP 700R mobile shear.
Early in December of 2010, some issues were detected in the operation of the stationary unit, an inspection was conducted and it was determined that the shear needed a major rebuild.
“We knew immediately that we would be without one of the key pieces of our recycling operation for at least a month, perhaps longer,” says Dan Juneau, manager of equipment and special projects for Schnitzer Southeast. “With a major component like that, it’s not simply a matter of getting a replacement until the original is back up and running. We had to make adjustments to keep scrap flowing through here, and we had to do it fast.”
The decision reached by Schnitzer Southeast management centered on shifting the downsizing facet of the job to its mobile shear. Equaling the volume of scrap which normally went through the stationary shear, however, was far beyond the capacity of any single mobile shear.
“To meet the volume, we brought in a second shear from one of our other yards and then rented a third Genesis shear, a GXP 660R, from the Birmingham office of Cowin Equipment, our local Genesis dealer,” says Romanoff. “One of those shears is currently shuttling back and forth between our railcar processing operation and the shear pile. Then, once the stationary shear is back online, we will get down to a single mobile shear focused solely on cutting railcars.”
CUTTING THE CARS
Schnitzer Southeast’s railcar operation has been in place at several company sites for as many as 15 years, depending on the location. Recently, however, that operation has grown, both in volume and company-wide importance.
“In the last three or four years we have really intensified our efforts toward railcars as a good source of scrap,” says Romanoff. “Mind you, availability is a key. The flow of cars ready for decommissioning can be really sporadic: sometimes there can be an overabundance, other times a shortage.”
Advances in equipment, however, have allowed Schnitzer Southeast to broaden its flow of material. “Since starting to process cars with a mobile shear rather than with a crew of torch cutters, our whole approach has changed,” says Romanoff. “In the past, we tended to shy away from doing boxcars, hoppers and flatcars and so on, because torching them was costly. Now, with the mobile shear, not only has the whole process gotten a lot faster and more efficient, but we can tackle larger volumes and a broader range of railcars.”
Romanoff notes that while Southeast still does use a torch crew to process tank cars because of their double hull design, the balance of cars are processed with the Genesis 700R. Under normal circumstances, these cars are reduced to pieces that are capable of being fed to the stationary shear.
“We first remove the truck sets and sell those that are in good shape into the rebuilding market,” says Romanoff. “Then the Genesis shear cuts the car body and frame into a size that is manageable for the stationary shear. We really believe the combination of the mobile shear and the stationary unit is the most efficient means possible and allows us to maximize the number of cars we can prepare per day. However, with the stationary unit down, the Genesis shear is now taking each car all the way down to prepared size.”
STRONG SUPPORT SYSTEM
Juneau and Romanoff say they have a strong sense of trust in the half-dozen Genesis shears they have working in their Southeast yards. They estimate that Schnitzer Steel Industries has another 25 Genesis shears at work company-wide. Juneau says that confidence in its equipment comes from having a long-standing relationship that predates Schnitzer Southeast itself.
“We value a solid level of support from our equipment suppliers and have found that Genesis and Cowin Equipment will bend over backwards to make any issue right,” adds Juneau.
Romanoff concurs, “Over the years we’ve learned that no matter how well the equipment performs, you’re hurting if there isn’t a good level of support. Getting parts when you need them and service from the manufacturer, dealer or both are key,” he states.
“We’ve come to rely on our mobile shears—now more than ever before—and we like the changes they’ve brought to our operation,” says Romanoff. “They are helping us through this period with the stationary shear down, and, in the railcar operation, they’ve allowed us to process as many as a dozen cars a day versus doing only two or three with torches,” he continues. “In this part of the business it’s all about [processing] costs; if you keep those costs low, it makes you more competitive on the buy side of the equation, and our mobile shears have certainly helped us do that.”
This article was submitted on behalf of Genesis Attachments LLC, Superior, Wis. More information is avialable at www.genesisattachments.com.
Get curated news on YOUR industry.
Enter your email to receive our newsletters.
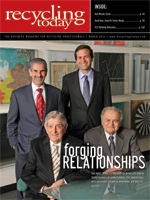
Explore the March 2011 Issue
Check out more from this issue and find your next story to read.
Latest from Recycling Today
- Republic Services, Blue Polymers open Indianapolis recycling complex
- Altilium produces EV battery cells using recycled materials
- Brightmark enters subsidiaries of Indiana recycling facility into Chapter 11
- Freepoint Eco-Systems receives $50M loan for plastics recycling facility
- PET thermoform recycling the focus of new NAPCOR white paper
- Steel Dynamics cites favorable conditions in Q1
- Hydro starts up construction in Spain
- Rebar association points to trade turmoil