Hudson Baylor Corp., a Newburgh, N.Y.-based material recovery facility (MRF) operator, hasn’t remained in business for nearly 30 years by sticking with a single approach to the recycling business. The company has been able to grow because it approaches recycling as a dynamic industry characterized by change. Nimbleness also is essential to Hudson Baylor’s operations because the company has no ties to solid waste hauling operations or to consumers, as some other MRF operators do.
The company currently operates 13 plants in the Northeast and Southwest and has signed long-term contracts with municipally owned facilities in Phoenix; Cape May County, N.J.; Atlantic County, N.J.; Dutchess County, N.Y.; Rockland County, N.Y.; and Brookhaven, N.Y.
BUILD TO SUIT
Hudson Baylor has demonstrated its willingness to adapt to the changing recycling industry by implementing ambitious retrofits of several of its MRFs in the Northeast, switching from dual-stream to single-stream processing systems.
Among these retrofits is a facility in Atlantic County, N.J. The company opted to undertake the conversion after signing a contract at the end of 2010 to design, build and operate a single-stream system for the Atlantic County Utility Authority at its existing MRF in Egg Harbor Township, N.Y.
Hudson Baylor is working with San Diego-based CP Manufacturing to install a system that, when operational, will process 34,000 tons of recyclables per year. The company says it worked closely with the Atlantic County Utility Authority on the specific goals and needs of the community and the recycling program. CP Manufacturing played an integral role in designing a system that would meet the authority’s stated goals and fit within the existing facility, says Chris Coady, a spokesman for Hudson Baylor.
Hudson Baylor also is retrofitting its Newburgh, NY MRF to accept Single Stream Material. In addition, the company is designing a new regional MRF in Beacon, NY. When complete, the company says its design for the 60,000-square-foot MRF in Beacon will take into account all facets of the operation to ensure the plant operates as efficiently as possible. “From truck scales to baled commodities, our traffic flow, tip hall, loading dock, processing hall and even our education center all fit according to the design that we believe will operate most efficiently,” Coady says. The facility is expected to be operational by the end of 2011.
The Dutchess County Industrial Development Agency has agreed to support the development of the facility with a set of tax incentives and potentially a bond offering to finance the construction.
Hudson Baylor is in discussions with multiple vendors and has not yet selected a vendor to design and install a single stream processing sysem at its new Beacon, N.Y., facility.
Tim Flanagan, Hudson Baylor vice president for the Eastern region and project development, says, “As municipalities and local haulers trend toward single-stream recycling programs, we see a need to accept and process single-stream materials. Hudson Baylor will continue to accept and process dual-stream materials and we have expanded our residential curbside recyclable processing in Newburgh to include plastics No. 1 through No. 7 in both single- and dual-stream programs.”
ROOM FOR GROWTH
William “Biff” Jennings, chief financial officer for Hudson Baylor, says that while single-stream collection is being fully embraced in the Western United States, in the East, where Hudson Baylor operates most of its MRFs, single stream is growing at a slower pace.
However, Jennings adds, “Every RFP (request for proposal) we have seen over the last two years has been either for an upgrade to a single-stream method or a new single-stream facility. The demand for single stream is nationwide.”
Scott Tenney, president of Hudson Baylor, says collection volumes increase by as much as 40 percent when communities switch to single-stream recycling.
Coady adds that the increase in volume is almost immediate.
Since the company first began processing recyclables in 1983, its Newburgh MRF has continually adapted to an ever changing material flow. For many years the facility recovered bottles and cans collected through the New York State bottle law. Today, the Newburgh facility accepts dual-stream, commercial-source-separated and, since the spring of 2010, single-stream materials.
MAKING THE SWITCH
Coady says Hudson Baylor encountered a number of challenges associated with retrofitting its existing dual-stream MRFs to be able to process single-stream collected materials. Despite the challenge, Hudson Baylor says it has avoided significant downtime during the conversion process by staggering its equipment installations. This approach has allowed the company to continue processing recyclables, albeit at a slower pace. By staggering the installations, the company also was able to analyze the performance of each piece of equipment, working with its equipment vendors to make adjustments.
The retrofit of the company’s Newburgh MRF is part of a multi-year strategy that includes a new regional single-stream facility a few miles away in Beacon, N.Y. The Beacon facility will have an annual capacity of 120,000 tons and will accept residential single-stream, dual-stream and source-separated materials, according to Hudson Baylor. The facility will employ laborers to perform material separation and quality control as well as use the latest optical and mechanical separation equipment, the company says.
“Operational efficiency comes from well-trained labor for quality control and the use of state-of-the-art optical and mechanical sorting,” Coady says. “In addition, attention to facility safety and scheduled preventive maintenance ensures a safe environment and optimal productivity.”
ENSURING QUALITY
To ensure that Hudson Baylor’s MRFs are supplying the highest quality materials and the best service they can, the company seeks to communicate with the communities it serves as well as with the consumers it supplies material to. “We see ourselves as partners to the communities we serve, and we see community education as a key element to any successful program,” Coady says.
He continues, “As we have seen in our single-stream facilities in the Southwest, a well-established education program that continuously informs the community has a direct effect on the quality of the material coming into the MRF.”
A key to ensuring the quality of the material coming into a MRF is continual education, which includes community outreach to schools and incorporating education facilities in MRFs to provide tours and informational programs, according to Hudson Baylor.
Municipalities have to continually update partner communities with instructional information that provides a clear and consistent message through many outlets, both traditional and Internet channels, according to Hudson Baylor. Haulers, processors and consumers must keep an open line of communication to ensure optimal operation. The more integrated these pieces are, the easier it is to met the goals of diversion and material quality in the company’s view.
Sponsored Content
Labor that Works
With 25 years of experience, Leadpoint delivers cost-effective workforce solutions tailored to your needs. We handle the recruiting, hiring, training, and onboarding to deliver stable, productive, and safety-focused teams. Our commitment to safety and quality ensures peace of mind with a reliable workforce that helps you achieve your goals.
“We feel the variation in quality is driven more by the company than [by] the market,” Jennings says. He adds that there is currently no price differential between recyclable commodities generated via dual-stream programs and those generated through single-stream systems.
While some consumers may still question the quality of recyclables collected via single stream, Tenney invites them to visit Hudson Baylor’s MRFs. “We will pass with flying colors.”
AN EVOLVING ISSUE
As the recycling industry continues to evolve, various materials are growing in volume while others are declining. Many earlier MRFs were designed to handle large volumes of old newspaper (ONP). However, as the generation of ONP declines, it creates challenges for companies that have invested heavily in processing equipment designed to handle the earlier version of the material stream. Hudson Baylor says it has adjusted its equipment and workforce to accommodate the changing nature of incoming material.
Hudson Baylor also says long-term contracts are important to efficient operations because they allow the company to develop markets for emerging materials.
Going forward, Hudson Baylor says it is looking to convert more of its MRFs so they have the ability to process single-stream material. “Our operational excellence is grounded in our focus on processing materials at the lowest possible cost per ton throughout our plants,” Coady notes. “We stress five core strengths that offer a total recycling package to our customers, controlling commodity volatility and stressing operational excellence. This enables us to be a trusted partner that offers unique solutions to our customers’ specific needs.”
Dan Sandoval is the senior/Internet editor of Recycling Today. He can be contacted at dsandoval@gie.net.
Get curated news on YOUR industry.
Enter your email to receive our newsletters.
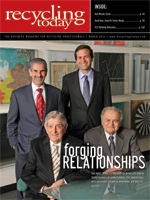
Explore the March 2011 Issue
Check out more from this issue and find your next story to read.
Latest from Recycling Today
- Nucor expects slimmer profits in early 2025
- CP Group announces new senior vice president
- APR publishes Design Guide in French
- AmSty recorded first sales of PolyRenew Styrene in 2024
- PRE says EU’s plastic recycling industry at a breaking point
- Call2Recycle Canada, Staples Professional expand partnership
- Circular Services breaks ground on north Texas MRF
- Tariff uncertainty results in choppy nonferrous scrap flows