With the goal of expanding its electronics recycling capacity, ECS Refining, based in Santa Clara, Calif., will be relocating its electronics recycling operations to a new 260,000-square-foot facility in Stockton, Calif. Along with the move, the company is investing in additional processing technology that is designed to allow ECS to reduce the need for additional downstream processing outside of the facility.
According to the company, the highly automated facility will be vertically integrated, enabling ECS to reduce incoming electronics to its constituent raw materials with improved efficiency.
The company’s current processing plant in Santa Clara suffers from a lack of integration, says Bill McGeever, vice president of operations for ECS. The Stockton plant, however, will enable the company to integrate the entire processing line for improved efficiency. It also will allow ECS to triple its current processing capacity of 100 million pounds of electronics per year.
FULLY EQUIPPED
Operations at ECS’ Stockton plant will begin with a picking line, where employees will remove plastic bags, corrugated containers and other product packaging. The reason behind this, McGeever says, is to reduce the amount of fluff produced during shredding. At this point, employees also will extract batteries, ink and toner cartridges, cords and large plastic pieces that are easily removed (paper trays and lids from printers, for example)—items that should not be shredded because they introduce hazardous contaminants or are difficult to separate.
The picking line has an added benefit. “This allows us to make a final check of what people are delivering to us,” McGeever says. If large pieces of metal or light bulbs are part of the incoming material stream, they will be removed here to prevent damage to the shredder and to reduce contamination.
From here the material will advance to the primary shredder and then to a secondary shredder, both of which are slow-speed, high-torque models. A 2-inch-minus particle size will be the result, McGeever says. “We want to leave the pieces as large as possible,” he adds, saying this will facilitate sorting.
The separation equipment the facility will employ includes eddy currents, magnets, various screens and optical sorting equipment from TiTech, which is distributed in North America by Van Dyk Baler Systems, based in Stamford, Conn.
The TiTech units, which the company currently has in service at its Santa Clara plant, can be programmed to separate light plastics from dark plastics, but they do not sort by resin type at this time, McGeever says. He adds that ECS has programmed the TiTech units to sort by color and metal content, making them ideal for sorting printed circuit boards. Additionally, McGeever says, “We use this technology daily and it helps to separate aluminum that is small enough to get by the eddy current.”
As of mid-February, ECS has been working with the TiTech units for eight months. “Now we are just getting clever about using them to separate stainless steel,” McGeever adds.
The Stockton facility also will be able to process glass from CRTs (cathode ray tubes), which McGeever says still make up a significant portion of the company’s incoming material stream at 4 million to 5 million pounds per month.
Once the Stockton facility is complete, he says ECS Refining is aiming for a purity level in the high 90s for the raw materials it will produce, thanks to downstream sorting equipment that relies heavily on compressed air and electricity as opposed to chemicals and water.
However, McGeever says rapid advancements in equipment mean that ECS Refining will be on the lookout regularly for better approaches for handling its electronic scrap.
WAVE OF THE FUTURE
“Something will change,” McGeever says of the technology available to electronics recyclers. “That is one thing you can count on. A new technology will come along, or we’ll find a way to solve one of our challenges with a new piece of equipment.” He adds, “There are always things coming down the pike that have to be evaluated. And you really have to keep your eyes open to it, or things will go right by you and you will miss some of the great new developments that are coming along.”
The large size of the Stockton plant will give ECS the flexibility that its Santa Clara location currently lacks in terms of adding additional processing capabilities, such as a wire-chopping line and equipment to process CRT glass.
McGeever says vertical integration of this nature requires a higher level of investment in capital equipment but has its benefits. “As the electronics recycling industry matures, processors are beginning to do more work ourselves to control the price and quality of what we are doing,” McGeever says. “All of the larger companies in the industry are leaning this way already or ought to be. It allows processors to control the quality of what they do and the disposition of residuals.”
He adds, “Small job shops will have a place, but they will not get the majority of the material.”
Buying a shredder is only an initial step in electronics recycling, he says. “Shredding is a quick way to destroy personal information on electronics but also to commingle materials.” The integration of downstream separation is an integral next step, he adds, especially when it comes to glass from CRTs in California.
“Shipping glass is a major challenge in California,” McGeever says, adding that recyclers must ship the material before they are able to file a claim with the state under the Electronic Waste Recycling Act of 2003, also known as SB 20/50. “If there is an interruption in a glass processor’s ability to receive material, it affects our ability to be paid by the state.”
McGeever adds, “Being able to process our own glass and sell it to end users directly puts us in control of our own destiny, and we like that component of it.”
A NATIONAL MODEL
The electronics recycling industry in California has consolidated “tremendously” in the last six years since the Electronic Waste Recycling Act of 2003 was enacted in 2005, McGeever says. In the last two years alone, he adds, three of the top six players in California have gone out of business. “There are three or four left that are grabbing the market share that has been abandoned by those departures.”
He predicts further consolidation at the national level in the near future as well. “I think you’ll see that there will be maybe four or five major players who have large processing plants strategically located in population centers.”
Of ECS’ strategy, he says, “We would like to have [processing plants] within 350 to 500 miles of each other so they can be self-supporting.” McGeever says this approach will allow the company to add processing equipment as the market volume dictates, because in the meantime a nearby plant could handle the devices requiring capital-intensive processing .
“It is the old hub-and-spoke concept,” he says. “The spokes are your transportation channels bringing material to your hub, where you do processing.”
Sponsored Content
Labor that Works
With 25 years of experience, Leadpoint delivers cost-effective workforce solutions tailored to your needs. We handle the recruiting, hiring, training, and onboarding to deliver stable, productive, and safety-focused teams. Our commitment to safety and quality ensures peace of mind with a reliable workforce that helps you achieve your goals.
Additionally, McGeever predicts that consolidation among electronics recyclers will result in the standardization of services and pricing structure. “This industry is well on its way to that consolidation,” he says. “There will be fewer big processors doing most of the work. They will have high standards for environmental protection and safety.”
CERTIFIED OPPERATIONS
McGeever says he sees certifications growing in importance, noting that companies will choose the option that works best for their operations and that best addresses their clients’ requirements.
ECS has opted to certify its operations to the Basel Action Network’s e-Stewards Standard for Responsible Recycling and Reuse of Electronic Equipment, which also requires ISO 14001 certification. McGeever says the company has opted for this certification because it feels the Responsible Recycling (R2) standard is “thin on certain aspects.” He adds, “We are going with the more stringent [certification] because it builds more barriers for competition. But it has also been adopted recently by cities and national bank chains. I think the momentum is there.”
McGeever continues, “Your customers tell you what certification you have to have. We may have to have both before it’s over. I’d be surprised if we don’t get there eventually.”
While ECS is still in the process of setting up its Stockton facility, McGeever says the company expects to be fully operational and to have completed its e-Stewards audit by Aug. 1 of this year. ECS has the incentive to stay on schedule, as it is moving its electronics recycling operation as opposed to setting up a new facility, McGeever says. “There is no rest for the wicked when moving a revenue-generating facility.”
With the company’s expanded downstream processing capabilities, McGeever and ECS expect to see higher returns in the future.
Listen to Bill McGeever, vice president of operations for ECS Refining, Santa Clara, Calif., discuss the merits of California’s advance recovery fee for electronics at www.recyclingtoday.com/bill-mcgeever-interview.aspx
DeAnne Toto is managing editor of Recycling Today and can be contacted at dtoto@gie.net.
Get curated news on YOUR industry.
Enter your email to receive our newsletters.
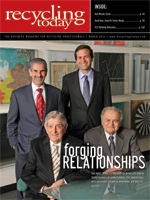
Explore the March 2011 Issue
Check out more from this issue and find your next story to read.
Latest from Recycling Today
- CP Group announces new senior vice president
- APR publishes Design Guide in French
- AmSty recorded first sales of PolyRenew Styrene in 2024
- PRE says EU’s plastic recycling industry at a breaking point
- Call2Recycle Canada, Staples Professional expand partnership
- Circular Services breaks ground on north Texas MRF
- Tariff uncertainty results in choppy nonferrous scrap flows
- CATL, Ellen MacArthur Foundation establish battery partnership