
Eureka Recycling is a nonprofit social enterprise headquartered in Minneapolis-Saint Paul that services more than 120,000 households per week with its recycling collection business and processes more than 100,000 tons per year of recyclables. With a mission to demonstrate that waste is preventable, it is the only organization in Minnesota to specialize in zero waste.
Eureka’s commitment to more sustainable operations runs deep: Its collection fleet was the first in the state and one of the first in the nation to run entirely on B20 biodiesel. Eureka also has diesel oxidation catalysts installed on its trucks to reduce particulate emissions.
With long-term contracts to provide recycling services to the cities of Minneapolis, Saint Paul, White Bear Lake, Roseville, Shoreview and Lauderdale, Minnesota, Eureka has served more than 500,000 people and recycled in excess of 1.5 billion pounds of material since it was established in 2001. It also has supported the local economy with more than 100 living-wage jobs that also provide benefits and has consistently provided environmental advantages to the communities it serves.
A smarter, greener, safer fleet
Switching from curbside collection of bins to collection of carts in alleys as part of its contract with the city of St. Paul led to a significant fleet upgrade at Eureka Recycling. The purchase of 21 semiautomated trucks was just the first step on the path to a smarter, greener, safer fleet for the company.
Next, Eureka started reviewing technology solutions and vendors in the industry for an onboard computing system with the goal of optimizing fleet monitoring, increasing efficiency and improving safety.
“We knew our needs were complex and would require extensive customization,” says Eureka Co-President Kate Davenport. “We were looking for a solution to accommodate a complete reroute of the city, including the detailed incorporation of small alleyways often difficult to map via GPS.”
McNeilus Truck & Manufacturing Inc., Dodge Center, Minnesota, introduced Eureka to Montreal-based FleetMind Solutions Inc. FleetMind is a brand of Belton, Missouri-based Safe Fleet. McNeilus has a partnership with FleetMind for its FleetLink Vision OBC system on new and aftermarket vehicles. After a review process, Eureka selected FleetMind’s FleetLink fleet management system.
A phased rollout plan
Eureka Recycling’s ambitious and phased rollout plan started in mid-2016 in preparation for the launch of the organization’s new fleet and the routes it would begin using in January 2017. Th rollout posed a number of significant challenges in terms of system customization, user adoption and change management.
Of Eureka Recycling’s fleet of 25 vehicles, almost all were to be upgraded. This included the addition of the following system components:
- in-cab smart displays with hands-free, turn-by-turn directions for drivers, along with electronic route sheet notifications;
- GPS tracking and telematics for improved customer service and real-time tracking of trucks, route progress, carts and other related activities; and
- digital video recorder (DVR) systems and 360-degree camera coverage for enhanced driver and public safety, improved service verification and expanded ability to easily capture all service exceptions.
The rollout schedule allowed for just four months of driver training. Drivers had a tremendous amount to learn and master in that time: new semiautomated trucks, new routes and new technology that would essentially change the way they worked. It was a completely new experience for frontline staff, and they felt hesitant about the change.
“Deploying the new system was like going from a rotary phone to an iPhone overnight,” Davenport says. “Our drivers had a lot of frustrations at first. Now, they can’t live without it.”

As the rollout progressed, a great deal of customization was required. A complex system of alleys and variable lot sizes had to be incorporated into Eureka Recycling’s daily routing. Also, the dense urban setting with a number of proximal carts and containers required a detailed and accurate tracking system.
“In all, it took a year to fine-tune the system to what we wanted and to get our team in sync,” Davenport says. “FleetMind worked with us throughout the process to figure out the best way to implement the system for our needs.”
The fleet management system also has improved collaboration among Eureka Recycling’s team members.
Improving frontline collaboration
Previously, when customers called to complain about missed pickups and other issues, it often came down to a “who do you believe” scenario.
For example, customer service staff had an irate customer on the phone saying the recycling wasn’t picked up, while drivers insisted the recycling hadn’t been put out. This created tension between frontline teams.
Now, service personnel can verify whether containers were placed out on time and provide evidence to customers when requested, establishing trust and collaboration between drivers and customer service staff.
“Drivers like that the system provides documentation on the route so that they feel supported in their decisions and get targeted training when needed,” Davenport says.
Routing efficiencies
Eureka Recycling used the fleet management system to perform an entire reroute of the city of St. Paul to ensure more accurate tracking and routing. This created dramatic efficiencies by optimizing daily routes, reducing missed stops and ensuring wireless delivery of electronic route sheets to drivers.
Davenport says, “Implementing a route management system allowed us to eliminate one route per day within two months.”
In addition, if a driver calls in sick, dispatch now can quickly redirect other drivers to cover the route, which eliminates miscommunication as to how the open route will be covered.
Better safety and improved reporting
Eureka Recycling also wanted to ensure maximum safety for its workers and the residents it services.
The new semiautomated trucks help to reduce risk for the organization’s drivers. The camera systems provide the drivers with 360-degree views around their trucks, virtually eliminating vehicle blind spots. Additionally, drivers can record and capture video of their activities from all angles. They also can secure video evidence for use in accident and dispute resolution.
Another significant side benefit to installing camera systems was the elimination of unnecessary trips. For example, when customers call to complain about a nonpickup, Eureka can provide evidence as to whether recycling was put out. This has dramatically reduced the number of unscheduled, and costly, retrieval trips.
“If you prevent just five unnecessary trips per day, the system pays for itself,” Davenport says.
For Eureka Recycling, having municipal recycling collection contracts also means tracking performance statistics and key productivity indicators. With its fleet management system’s enterprise reporting capabilities, Eureka can be more responsive to the municipalities it serves, identify and solve problems faster, improve operational efficiency, meet targeted goals, make better-informed decisions and capture the information required to better align the organization with its municipal clients.
Armed with its new fleet and fleet management technologies, Eureka has ensured that the trucks it sends out on its communities’ streets every day to collect recyclables are smarter, safer, greener and more accountable. What better way to align with the nonprofit’s mission of zero waste than to increase the efficiency of its operation?
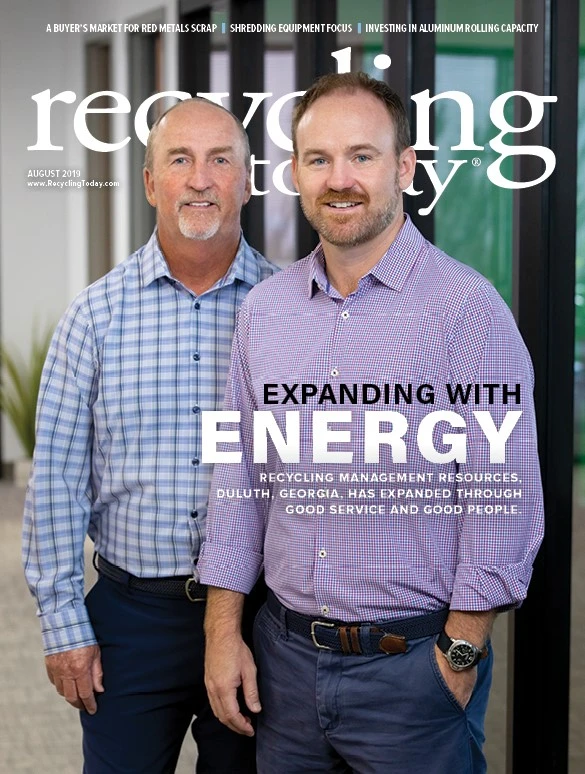
Explore the August 2019 Issue
Check out more from this issue and find your next story to read.
Latest from Recycling Today
- ReElement, Posco partner to develop rare earth, magnet supply chain
- Comau to take part in EU’s Reinforce project
- Sustainable packaging: How do we get there?
- ReMA accepts Lifetime Achievement nominations
- ExxonMobil will add to chemical recycling capacity
- ESAB unveils new cutting torch models
- Celsa UK assets sold to Czech investment fund
- EPA releases ‘National Strategy to Prevent Plastic Pollution’