
It seems like a no-brainer today. Rumpke Waste & Recycling was picking polyethylene terephthalate (PET) and high-density polyethylene (HDPE) out of the residential recyclables it collected in the Cincinnati area, and the rest of the plastic—including 40 to 60 tons per month of polypropylene (PP)—was being sent to a secondary processor.
But a combination of events enabled Rumpke to turn that PP into a valuable new revenue stream. Increased demand for PP, two grants totaling more than half a million dollars, improved processing technology and rising PP value all played a part in the development of that revenue stream. The risk Rumpke took on PP seems to be working out nicely.
Jeff Snyder, director of recycling at Rumpke, says demand for PP is strong. “If I had 50 MRFs right now and I was picking PP at all 50 of them, I could sell every single bit that I could get off the lines,” he adds.
In 2021, Cincinnati-based Rumpke received a $510,000 grant from The Recycling Partnership’s Polypropylene Recycling Coalition. A second grant worth $77,500 is coming from the same coalition in 2022.
The Polypropylene Recycling Coalition grants are designed to encourage material recovery facilities (MRFs) to increase recovery of PP, which can be used in a wide range of products, from food packaging to truck parts. According to The Recycling Partnership, Falls Church, Virginia, grant funding varies by MRF, depending on the needs and opportunities of each project.
Rumpke used the grant as part of a $1.6 million total investment to purchase three robotic sorters and wider conveyors and to make the plant modifications needed to accommodate PP sorting.
“We did a test of how much PP was actually in our system,” Snyder says. “We determined we had to have a robotic system that could make 200 to 220 picks a minute to be able to support the PP that was coming to our line. I would estimate it is in the range of 40 tons to 60 tons of PP a month.”
Snyder says that three SamurAI robots from Machinex Industries working together can meet that requirement. Although Rumpke considered other robot brands, it settled on the SamurAI models because Rumpke’s MRF features sorting equipment from Machinex, which is based in Plessisville, Quebec.
“They really work well within our system,” Snyder says.
The first three robots were installed in late July.
Machinex claims its robot can make about 70 picks per minute, about double the rate of a human sorter. Snyder says Rumpke’s early experience confirms the manufacturer’s performance data.
The SamurAI robots use artificial intelligence (AI) to identify products made from PP. Product recognition improves as the robots learn through experience.
The Cincinnati facility is a single-stream MRF. “We run the material off a conveyor belt through a metering bin that starts the process to get the material to a burden depth that makes sense,” Snyder says.
The next step is a presort to remove anything that is not actually recyclable, Snyder says. Bulky rigid items also are pulled off the line. Corrugated material is removed next, followed by a glass-breaker to remove glass. Next, 2D and 3D items are segregated in a step that uses screens and optics. Then, steel cans are removed, followed by items made with HDPE and then aluminum cans. The robots pick PP containers last.
The sorted PP is baled, and the bales are consolidated until a truckload is ready for shipment to a plastics reclaimer. Snyder says the baled PP is sold to reclaimers in the Midwest.
In addition to the robots, Rumpke had to install wider conveyor belts to better distribute the material and to accommodate the robots. It also had to install and move some bunkers and chutes to get the PP to the baling step.
Rumpke’s staff has had to navigate a learning curve. “It has not been negative; it has all been very positive,” Snyder says.
Machinex staff helped the MRF’s employees understand how the AI and camera systems work and the adjustments they needed to make.
“There is a lot of preventive maintenance that goes into the suction cups of a robotic head,” he adds.
The robots are fully encased with only the arms exposed to the recycling stream. This reduces maintenance requirements on the motors and other components.
The Cincinnati MRF runs a first and third shift. Maintenance is performed during the middle of the day.
_fmt.png)
Snyder says he expects to see a return on investment for the PP project in about three years.
The value of sorted PP is rising, which is good fortune for Rumpke. Baled PP was selling to reclaimers for 37 cents to 42 cents per pound as of mid-September. The price was in single digits when Rumpke did its initial justification for adding the robots.
“Obviously, we couldn’t see the future,” Snyder says. “We didn’t know the price was going to rise this much, but we are very happy with the PP pricing today. It’s going to help us get to our goal much quicker,” he adds.
The rapid rise in PP is being fueled in part by recycling technology improvements and increased demand for recycled resin, which have created a viable end market for postconsumer PP. Several recyclers have announced expansions this year to process more PP.
“Recycling technology has caught up with the product,” Snyder says. “They are able to take the color out, to make it clear and to get the smell out,” he says of Orlando, Florida-based company PureCycle Technologies, which has licensed technology from Procter & Gamble to recycle PP. Its nearby Ironton, Ohio, plant is under construction.
Synder adds, “Because of these things, they are able to make an end product that is comparable to virgin resin.”
He predicts that the market for recycled PP is going to be huge. “It is really unbelievable right now,” he says. “There are people lining up that want PP.”
Rumpke announced in January it would accept PP containers in residential collection bins, but thus far there has only been a modest increase in the amount of PP it collects. Snyder says the company is in the process of testing the amount of PP in its stream to determine the current volume.
Rumpke also has a smaller MRF in Columbus, Ohio, where PP is now being sorted by hand.
The success of the first three robots at the Cincinnati MRF has caused Rumpke to purchase a fourth robot that was installed in September and a fifth that is scheduled for delivery in the first quarter of 2022.
These additional robots will pick natural HDPE containers. Currently, Rumpke optically sorts HDPE and uses manual labor to remove contaminants and to separate natural from color HDPE. The new robots are expected to handle all those tasks.
Robots have not replaced human sorters at Rumpke’s Cincinnati MRF. Snyder says, “Nationwide, I think that is absolutely happening, but we are holding onto every person we can and using the robots to supplement our workforce.”
He says Rumpke likely would have moved to robotic sorting in the future even without the grants and the PP project, but they did push the company’s adoption of the technology more quickly. “It is the next logical thing when you think about advanced technology in our system. We already have all the bells and whistles in our system.
“Our system runs 55 tons an hour, so it is very, very large,” Snyder adds. “Robotics take it to the next level.”
He says Rumpke is not interested in acquiring the technology to turn its sorted and baled plastics into flake or pellets. “We are really good at collecting it. We are really good at sorting. That’s our niche, and that’s where we are going to stay,” Snyder says.
Another consideration for recovering PP was to open a new recycling market for its customers. “Can you really put a number on the value of that? I guess you can a little bit, but what a strong message we send to our customers.”
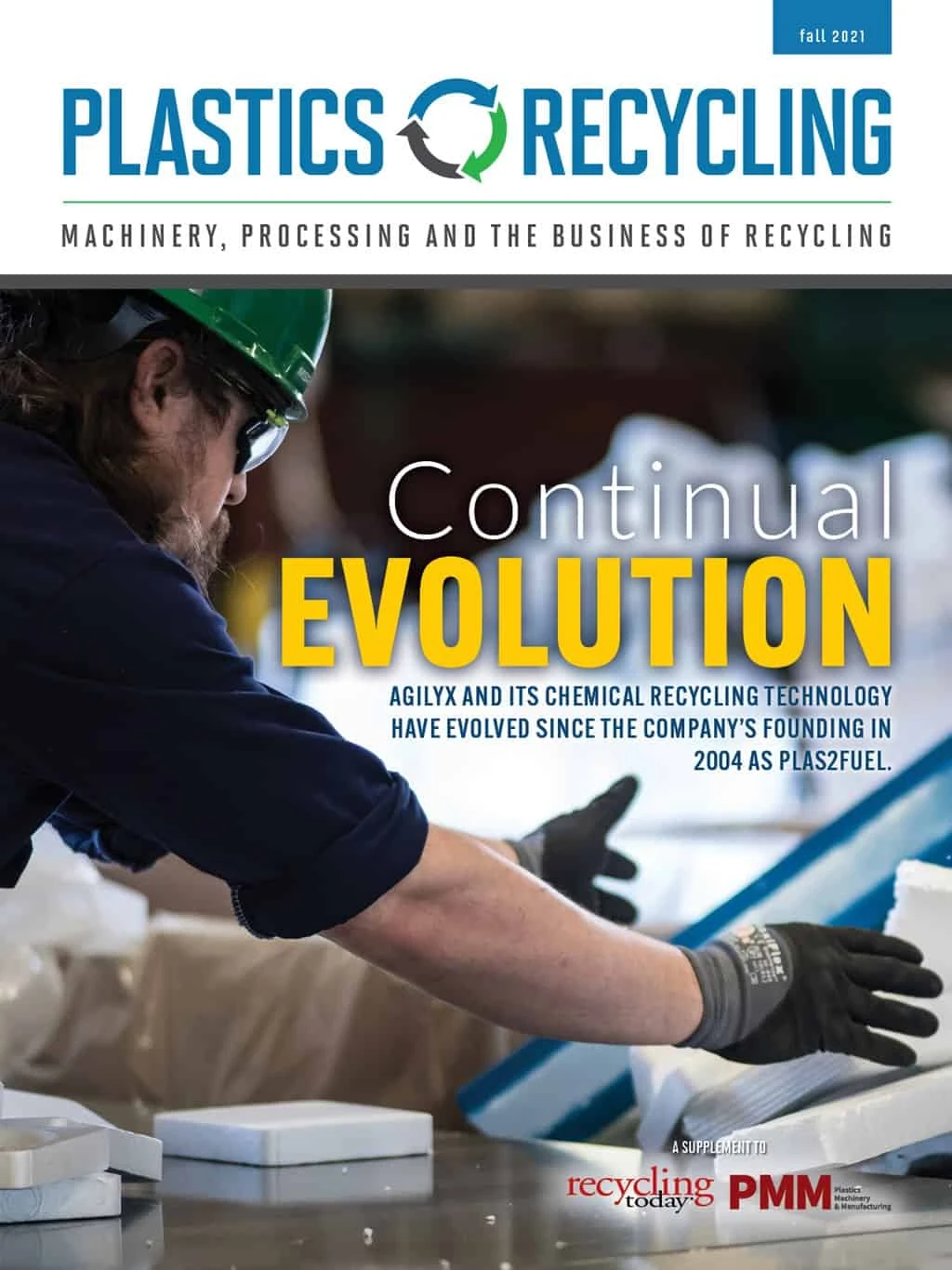
Explore the Fall 2021 Plastics Recycling Issue
Check out more from this issue and find your next story to read.
Latest from Recycling Today
- ReMA board to consider changes to residential dual-, single-stream MRF specifications
- Trump’s ‘liberation day’ results in retaliatory tariffs
- Commentary: Waste, CPG industries must lean into data to make sustainable packaging a reality
- DPI acquires Concept Plastics Co.
- Stadler develops second Republic Services Polymer Center
- Japanese scrap can feed its EAF sector, study finds
- IRG cancels plans for Pennsylvania PRF
- WIH Resource Group celebrates 20th anniversary