
Recycling and waste businesses are striving to adapt to the “evolving ton” as the mix of materials in residential recycling streams changes. In the case of recycler and hauler Penn Waste Inc. of York, Pennsylvania, officials noted a big increase in containers, primarily those made of polypropylene (PP) and polyethylene terephthalate (PET), in the residential recyclables coming into the company’s material recovery facility (MRF). The sorting line at Penn Waste’s MRF could not keep up.
“The amount of containers that was getting into the container line was about 30 percent higher than what it was designed for,” says Tim Horkay, director of recycle operations at the MRF. “It was a volumetric flow issue.”
The company was losing revenue because it could not sort containers efficiently enough. “So, we decided to take a look at the performance to improve the throughput and look at the design logic on the container line while we are at it,” he says.
It was a two-year process from design to commissioning last year. Penn Waste worked with Nashville, Tennessee-based National Recovery Technologies (NRT), a supplier of optical sorting equipment and a division of Eugene, Oregon-based Bulk Handling Systems (BHS).
“The main reason for the retrofit was not only to increase capacity but also to eliminate additional manual sorting,” says Matthias Erdmannsdoerfer, president of NRT.
A $3.5 million investment—including three new NRT optical sorters and a Max-AI Autonomous Quality Control (AQC) robotic sorter—increased overall throughput by 10 tons an hour, reduced labor requirements and improved the quality of the resulting material streams, Horkay says.
About 85 percent of Penn Waste’s materials come from residential sources, with the remainder coming from commercial operations.
The first new optical sorter is an NRT FiberPure model that uses NRT’s proprietary In-Flight Sorting technology to remove fiber (paper) products from the sorting line. In-Flight Sorting uses near-infrared technology to identify fiber products while they are in the air after falling off the end of a conveyor belt; streams of air eject the unwanted materials. Penn Waste added the FiberPure unit to handle the increasing number of small cardboard containers that are similar in size to many plastic bottles.
The company also added an NRT SpydIR with In-Flight Sorting, which separates plastics by material type.
From there, the high-density polyethylene (HDPE) that has been sorted out goes to another new machine in the process, a ColorPlus model that separates colored HDPE from natural HDPE.
NRT recently upgraded the ColorPlus line, replacing fluorescent lights with LEDs.
The ColorPlus unit reduces the need for manual sorting. “It was an upgrade for us because we were manually color separating prior to this,” Horkay says.
The new Max-AI AQC unit ensures the PET stream is free of non-PET materials. To identify different objects on the sorting line, it uses a vision system and artificial intelligence. That technology is combined with a robotic sorter.
“It’s doing quite well, as advertised,” Horkay says. “It’s doing approximately 60 to 65 discrete picks a minute.”
At the end of the process, employees still sort the remaining materials.
“Max can function at a higher rate and typically replaces one-and-a-half to two sorters. It takes this last check to make sure that we have the highest purity possible,” Erdmannsdoerfer says.
Penn Waste also got a new eddy current separator that NRT didn’t make but provided as part of the installation. It is used to recover aluminum.
The upgrade to the sorting line allows Penn Waste to target PP separately. Previously, PP wasn’t separated at the MRF and instead was sold mixed with other materials. “We recognized that mixed market just wasn’t going to be there for us,” Horkay says.
The company also has seen a substantial increase in the quality of the sorted material. He estimates that 23 percent of the commodities were lost before because the optical units were overburdened. With the new equipment, the loss is at less than 1 percent.
Horkay says Penn Waste has seen a 10 percent increase in its PET recovery, 8 percent for HDPE and the emergence of a strong PP segment.
He raves about the partnership with BHS and NRT. For one, Penn Waste was determined to not have any downtime with the conversion. “They reset our entire container line in nine days,” Horkay says.
Erdmannsdoerfer says the equipment was delivered mostly preconfigured, which helped to speed the installation.
“We hook them up to air and power, and they’re basically ready to go,” he continues. “And then, production starts, we do some fine-tuning, and then the machines are fully functional.”
Penn Waste might want to add more equipment, but markets for recycled materials will be a factor. “We’re taking a wait-and-see approach,” Horkay says. “We want to see the technology proven a little bit more. But we want to see the markets improve as well.”
Erdmannsdoerfer says Max-AI AQC launched in April 2017, and Penn Waste purchased one of the first systems. Some tweaks to the graphic system and an upgrade of some wear items, such as filters and screens, have been performed since. NRT also will provide Penn Waste with software updates without charging a subscription fee.
For more information: National Recovery Technologies LLC, 615-734-6400, www.nrtsorters.com Penn Waste Inc., 717-767-4456, www.pennwaste.com
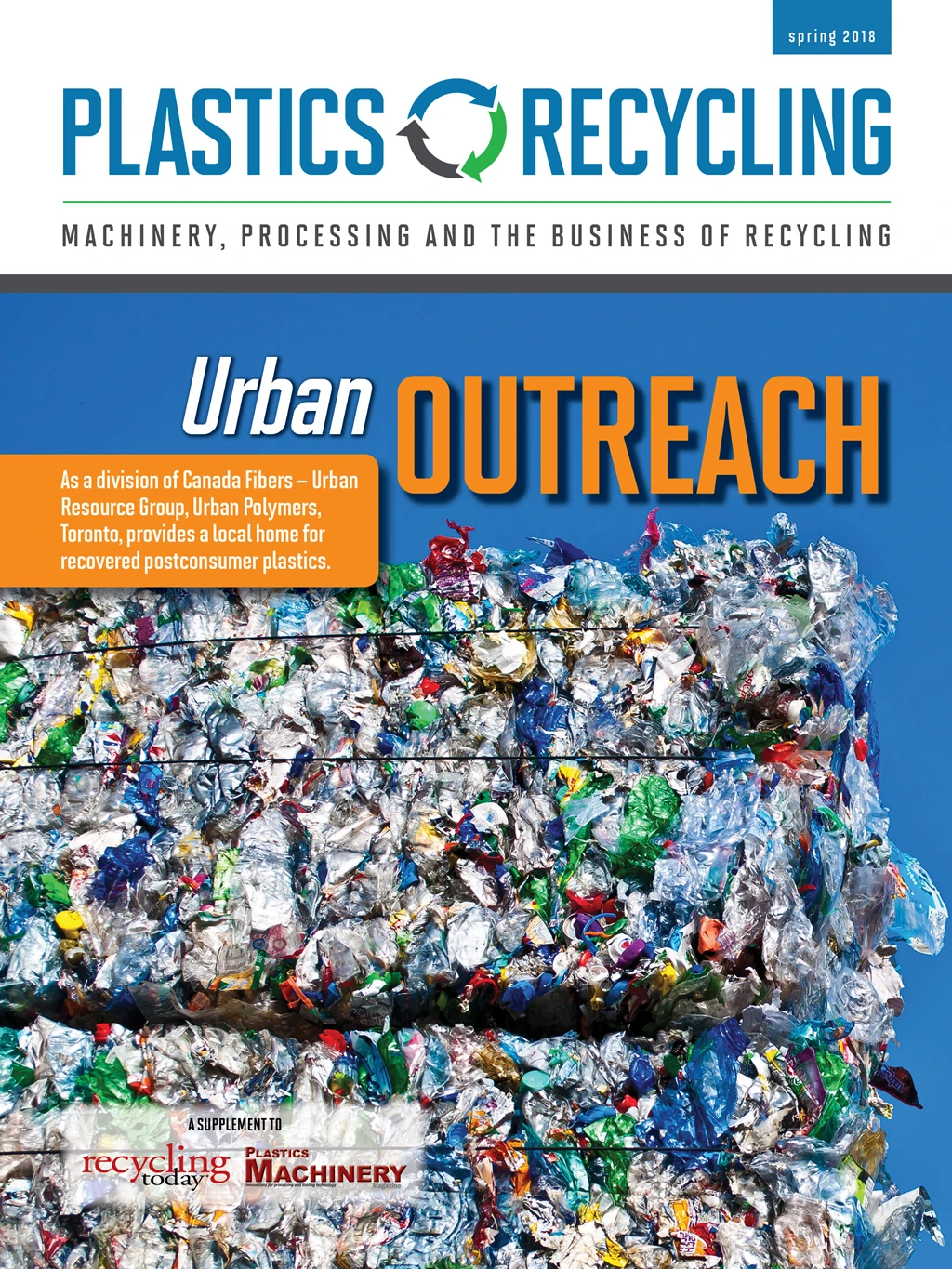
Explore the May 2018 Plastics Recycling Issue
Check out more from this issue and find your next story to read.
Latest from Recycling Today
- Hyundai adds dealer in Wisconsin
- Study finds recycling symbols largely recognizable
- Reworld announces executive leadership transitions
- Longtime paper industry veteran announces retirement
- Aurubis CEO says its metals play vital role
- Steelmakers await impact of tariff policy
- Radius loses money, says merger on track
- Electrostatic technology vies for role in ASR sorting