During his 35 years in the plastics recycling industry, Robert Render has had many roles and responsibilities. As co-owner and president of Maine Plastics, a plastics recycling firm he founded in Zion, Illinois, in 1983 with his father and another partner, Render experienced the highs and lows of business ownership. The company was well-known in the industry and managed recycling at NPE, the triennial trade show hosted by the Plastics Industry Association (PLASTICS), from 2000 through 2012, before shutting down in early 2014.
Now, Render is commercial manager for Ravago Recycling Group, the recycling division of the Belgium-based resin distribution company Ravago.
This year, he begins his term as chair of PLASTICS’ Recycling Committee. “I believe the activities and leadership of the PLASTICS Recycling Committee in sustainability and advocating for recycling are making an impact in the entire plastics industry.”
Render shares his thoughts on the industry in the Q&A that follows.
How have you seen plastics recycling change over the years? The policies of the Chinese government, including Green Fence and now National Sword, have forced us to create solutions capability and new processing capacity in North America. This has led to tremendous turmoil in recycling markets but has also created opportunities for companies to deploy new technologies and make investments in domestic processing capacity.
Chemical recycling, previously relegated to the R&D lab, is going to make a lasting impact. Companies like PureCycle [Technologies], Loop Industries and Agilyx will be joined by others due to the limits of mechanical recycling and the value created by new resins with like-virgin properties.
What lessons have you learned about the industry that have helped you throughout the years? When you connect people together without the expectation of financial gain, you build trusting relationships that pay off many times over. I always try to help connect people even if there is no imminent transaction for me to participate in.
Our industry thrives on collaboration, especially today, where challenging materials often require a combination of solutions. Building a network of industry professionals, processors and equipment and technology companies takes time, but you must be committed to building it.
Where do you see upcoming opportunities for plastics recycling? What about challenges? I see a bright future for nonmechanical polymer recovery, which includes depolymerization and polymer filtration. I am encouraged by the recent investments in this space and expect to see more. Recyclers will become part of a larger “recovery” network to prepare materials for these processes.
I also see a great opportunity for recycled content in products used in the rebuilding of our national infrastructure. As an industry, we need to ensure that we are at the table when infrastructure spending, which will have bipartisan support, is considered.
One of our biggest challenges is educating and re-educating the public on the role of recycling as part of the recovery of the value from the waste we create.
What’s the biggest professional mistake you have made? Expanding [Maine Plastics] too quickly and depending too heavily on a single large supplier. We thought we could use that supplier to anchor growth at each new location. We would have been better off operating in fewer locations and using strategic partners more.
How have equipment suppliers to the industry helped to advance plastics recycling? I started in the industry on the operations side and always enjoyed my relationships with equipment suppliers, working together to make improvements to increase efficiency, reduce maintenance costs and expand the variety of materials that could be recycled. Today, technology is driving the industry to help us process and recover value from materials that we used to export or landfill.
What misperceptions about plastics recycling do you wish you could debunk? First, that certain materials are not recyclable and, second, the purpose of resin identification codes on consumer products. The resin identification codes are simply codes—they do not indicate recyclability, nor do products without them mean they are not recyclable. I have little patience for people who complain that recycling is a failure when we as a country have not gone “all in” with resources, infrastructure and education. People will do the right thing if it is easy and convenient.
What advice can you offer to younger plastics recyclers entering the market? Spend time with your customers so you better understand what makes them successful and how you can support those efforts. I always ask my customers how I can help them win new business and make their products more successful. You just cannot see what you need to see and ask what you need to ask sitting behind a desk.
Who has served as your role model or mentor? My dad, who died in 2016, taught me the value of building trusting relationships with colleagues, employees, customers, vendors and competitors. He also showed me you could win business by outhustling, outthinking and outworking your competitors while retaining your core values of integrity, fairness and honesty.
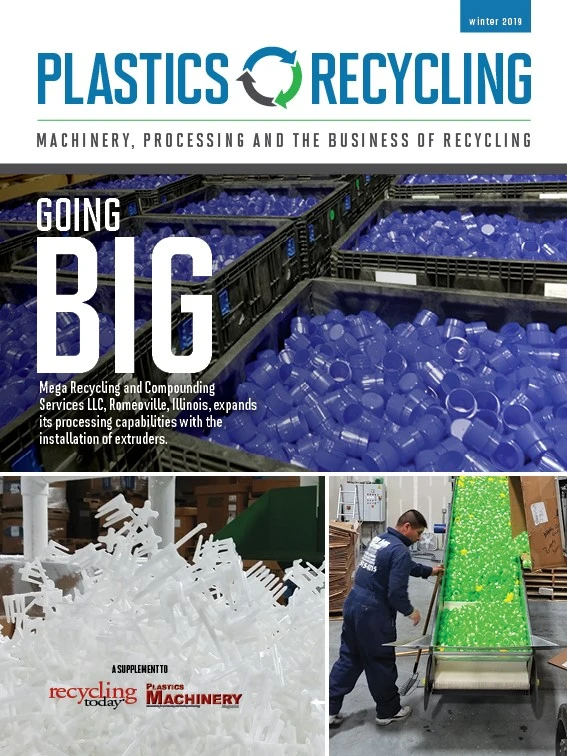
Explore the February 2019 Plastics Recycling Issue
Check out more from this issue and find your next story to read.
Latest from Recycling Today
- Toppoint Holdings expands chassis fleet
- Lego creates miniature tire recycling market
- Lux Research webinar examines chemical recycling timetables
- Plastics producer tracks pulse of wire recycling market
- Republic Services, Blue Polymers open Indianapolis recycling complex
- Altilium produces EV battery cells using recycled materials
- Brightmark enters subsidiaries of Indiana recycling facility into Chapter 11
- Freepoint Eco-Systems receives $50M loan for plastics recycling facility