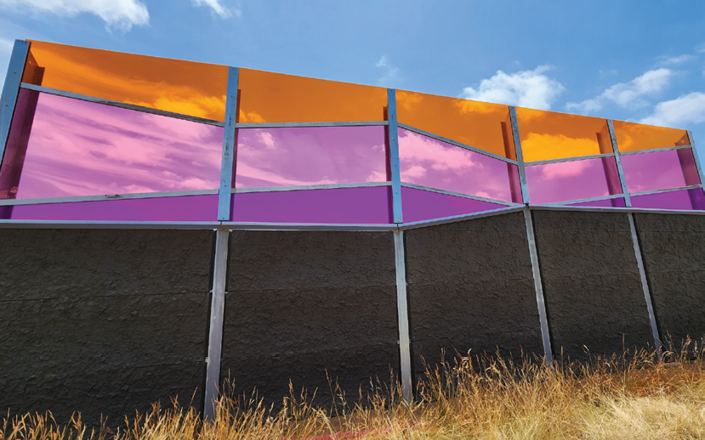
Australian manufacturer RMP Global has spent the last 15 years perfecting its sustainable infrastructure technology and, after successful installations in Australia and Europe, is introducing its recycled plastic noise walls, claddings and facades to the North American market.
RMP Global’s recycled plastic noise walls first were installed in Australia in 2008, but when the contractor on a project that required about 300,000 square feet of noise walls realized how costly concrete would be, the RMP panels really took off.
“This was kind of the moment where it sunk in how good the product was,” RMP Global President Doug Talbott says. “Then, [RMP Global] went and did more projects in Australia, and things really kind of kicked off. There was a myriad of jobs that happened.
“We even did a job in the Netherlands, who are one of the leaders in terms of infrastructure. This was really exciting as it was equivalent to exporting a pizza to Italy.”
Traditionally, noise walls have been built using concrete or steel, effectively blocking sound but doing little to resolve environmental challenges, according to RMP Global.
After many years of testing, the company developed a specialized technology to break down postconsumer plastics and remold the material into noise walls it claims can withstand the rigors of urban and transportation environments.
“Over the years, we had to do test after test after test because this is infrastructure; this is going to be up for 50 to 100 years,” Talbott says.
“The waste used in our manufacturing process is typically nonrecyclable and harmful to ecosystems, but our innovative technology repurposes it for noise barrier production. This transformative process is now poised to make a meaningful difference in North America’s low-carbon infrastructure landscape,” he continues.
Inside the RMP process
RMP Global employs a rotational molding system, or rotomolding, to produce its recycled noise walls.
Rotomolding involves a heated mold that is filled with powdered plastic resin. The mold is slowly rotated, dispersing the resin, which coats the inside of the mold as it is heated. The mold is rotated continuously as it cools to create the desired shape and avoid sagging and deformation.
The company uses a blend of different types of polyethylene plastics, including milk jugs and pallet wrap, to obtain the correct properties for rotomolding. The recycled plastic then is compounded with the desired color and pulverized.
“We want the color to be steadfast and through properly because our products are built to last,” Talbott says.
One of the major advantages of using recycled plastic noise walls compared with concrete, Talbott says, is the ease of installation. In fact, the walls are light enough to be lifted by hand and slid into place.
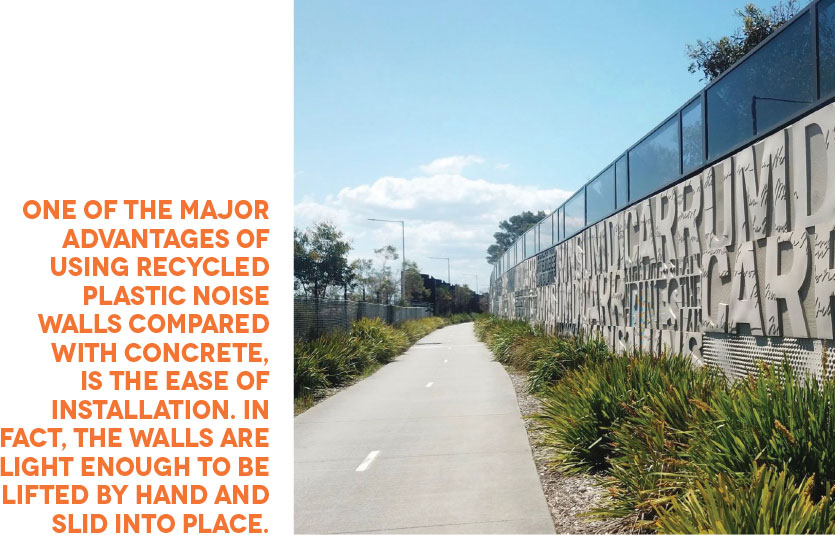
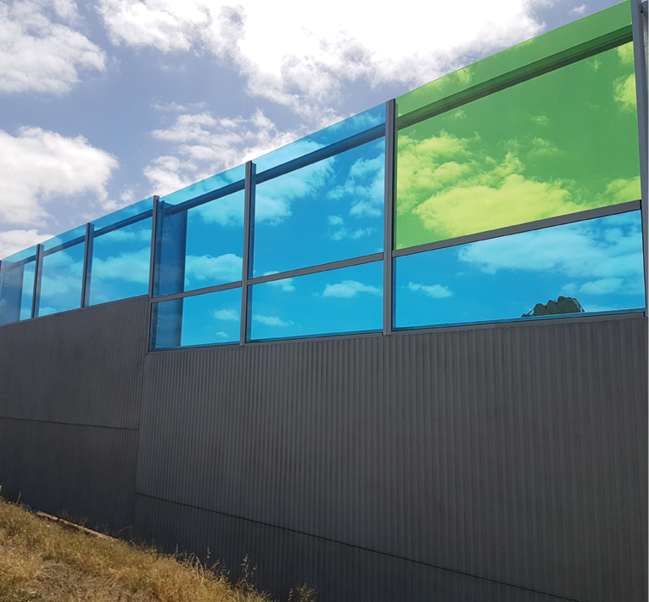
“If you were to put a concrete panel up, you’d have a giant crane with outriggers,” he says. “Every time you move it, you’ve got to pull the outriggers up, move the crane, set them up again. [The recycled plastic wall] goes up [at] at least twice the speed while using smaller, more agile equipment.”
The wall sizes vary but, on average, are approximately 20 feet tall and 10 feet wide and can be connected to support up to 24-foot post spacing. The posts used to hold the panels in place are the same used to hold concrete panels because, as Talbott explains, the posts don’t take on the weight of the panel, rather, they’re designed to withstand the wind loads.
The plastic noise walls have some design advantages, too. Talbott says the RMP panels can be made in any opaque color and can feature a different pattern on the front and back, allowing the side that faces the road, for example, to have a different look than the side that might be facing someone’s backyard or a public park. Whereas, with concrete walls, one side has to be flat.
Talbott says the walls also are graffiti-resistant and built to last 70 to 100 years.
“This provides an architectural option currently not available for existing noise wall systems,” he says.
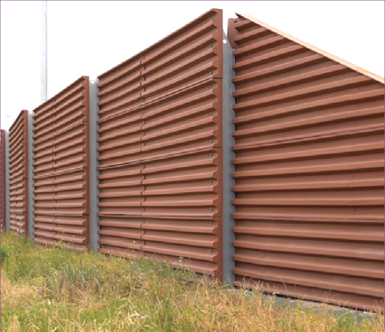
RMP noise wall molds can be customized to a specific job. Larger projects might require 10 molds, whereas smaller projects might only need one or two, for example.
Aluminum molds, often with variations in the pattern to make a matching matrix, are fabricated and used in the rotomolding process. Once a mold is made, however, it becomes part of the RMP Global “arsenal,” and a client can use one of these “off-the-shelf” molds to cut project costs. Each mold can make about 7,000 individual parts in its lifespan—about 300,000 square feet worth of noise wall.
To date, RMP Global has recycled the equivalent of about 6.44 million milk jugs and enough pallet wrap to stretch 6,200 miles.
Entry into the North American market
RMP Global introduced its recycled plastic noise walls in North America in November of last year. The success of the company’s walls in Australia and Europe prompted RPM to explore opportunities in the U.S., in particular, where Talbott says demand for noise walls is “through the roof.”
“They’re spending $500 million a year on noise walls alone,” he says of the U.S. market. “With that kind of volume, it was obvious this is where we can make the biggest difference in terms of carbon emissions.”
RMP Global then met with VX Group, a Cedarburg, Wisconsin-based business management consultancy that helps Australian businesses enter the North American market, and started to understand the scope of expansion opportunities in the U.S.
The company since has come to terms on a licensing agreement with Barrier Ridge Capital, a Toronto-based investment company that seeks opportunities in the highway and road safety infrastructure space and has provided funding “to really kick things off over in America,” Talbott says. In November, Barrier Ridge bought into RMP Global’s U.S. company, RMP Global Inc., creating a joint venture.
Along with roadside or other transportation-related applications, noise walls can be used around the perimeter of an industrial development, and RMP Global’s first job in the U.S. is at a distribution center where trucks will be arriving 24 hours a day. Other jobs provide noise protection for large construction projects for nearby residents.
One factor Talbott says has made RMP Global’s North American entry easier is that the company has contracted its manufacturing operations, partnering with Port Washington, Wisconsin-based CPI Products, a rotomolding company that manufactures solutions for the agriculture, automotive, public safety and waste management industries, among others.
“They have the right mindset, and that’s what we’re really looking for,” Talbott says of working with CPI. “It’s really important that you find the people you can get along with and have a similar mindset to you.”
Finding the right manufacturing partners has eased the transition, but sourcing material in the U.S. has been challenging.
In Australia, RMP Global sources mechanically recycled material, but in the U.S., Talbott has been unable to find a similar solution as recyclers aren’t necessarily sorting the grades in the manner necessary to achieve the desired blend in a clear color.
“We are fixing that and, along with RMP Global’s patent to ensure the product can withstand 70 to 100 years in operation, often adjacent to high-speed traffic and rail, we are influencing the postconsumer recycled plastic market,” he says.
For now, the solution has been chemically recycled material, and because that material often is more expensive, RMP Global’s first few jobs in the U.S. feature noise walls that, for now, have a lower percentage of recycled content.
“Some clients value product cost over recycled content, while others are willing to pay more to have a higher percentage of recycled content,” Talbott says. “It is a balance finding the right percentage of recycled content while still being the right price to win the project as the carbon footprint improvements are huge compared to concrete regardless.
“In Australia, the mechanically recycled material is roughly the same price as virgin. If we can achieve that in the U.S., all of our products can be the maximum percentage of recycled content while offering budget-friendly prices to our clients.”
What’s next
Talbott envisions having four RMP Global manufacturing locations in the U.S.
He’s explored sites in California, Pennsylvania and Texas, along with the company’s current contracted manufacturing operations in Wisconsin, prioritizing efficiency in terms of transportation and logistics.
“It’s not that expensive to ship from Wisconsin to the East Coast, but I don’t want to be shipping across multiple days; I would like to keep it within a day,” Talbott says, noting that shipping across the country also is not consistent with the company’s emissions goals, either.
“RMP Global really is looking to be a global influencer and partner to organizations that are aligned to our mission, ‘Transforming waste to sustainable and cost-effective infrastructure,’ whether that’s removing waste from the oceans or sustainable infrastructure and everything in between. … It goes beyond the infrastructure; we want to spark change.”
Get curated news on YOUR industry.
Enter your email to receive our newsletters.
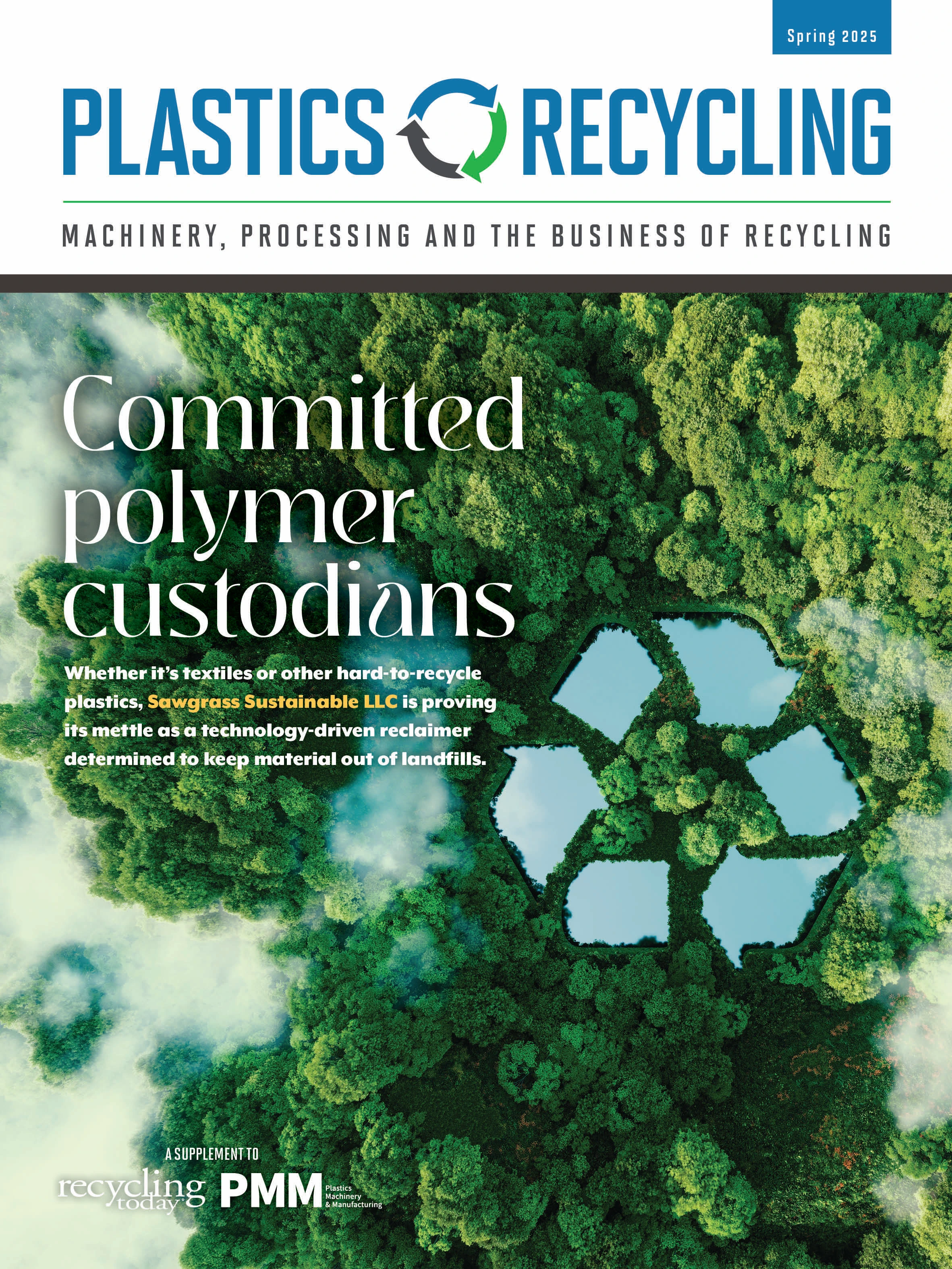
Explore the Spring 2025 Plastics Recycling Issue
Check out more from this issue and find your next story to read.