Riverside Engineering, San Antonio, has announced that it will begin installation of its model M-122 auto shredder at Upstate Shredding LLC in Owego, N.Y., in late November.
In a press announcement, Riverside says the initial phase of the installation is scheduled to occur over eight days, with Riverside’s staff working 24-hours per day in shifts to complete the project as quickly as possible. “What usually takes several weeks in our industry for this work will be done in days," says Rusty Manning, Riverside director of new wquipment sales.
“By completing the new in-feed roller conveyor system and downstream ferrous metal separation system quickly we will cause minimum disruption, allowing shredding and processing to continue as usual while we work,” Manning continues.
Adam Weitsman, president of Upstate Shredding-Ben Weitsman & Son, says, “We are a rapidly expanding company investing in the best available technology upgrades, but at the same time our Owego facility must continue to operate seamlessly to process the growing volume of metals arriving from our customers and feeder yard operations. We look forward to a smooth transition from our present shredder to the new M-122.”
A second phase, including the shredder section, will be installed in February on a similar expedited schedule.
Jim Olson, co-owner of Riverside Engineering, says he anticipates that 80 percent of the downstream system will be installed while the shredder is still in operation.
While the winter weather could pose challenges for installing the shredder, it is imperative that the facility be back in line as quickly as possible because it is at Upstate Shredding's main location, Olson adds.
Riverside says the facility upgrade will be 100 percent debt free.
Riverside claims that that when the installation of the M-122 is complete, it will be among the largest shredders in the world. Riverside adds that the shredder will have the highest capacity currently on the market, able to process up to 400 tons of metal per hour. The shredder will be using 1,000-pound hammers, allowing the shredder to process the largest vehicles on the road, including tractor trailers and buses, according to the company.
Riverside says the M-122 shredder is designed to accommodate a 10,000-horsepower motor. The shredder also represents what the company says are the latest advancements in machine automation and computer controls for maximum processing efficiency, safety, noise reduction and energy conservation.
The new in-feed system is a steel-belted conveyor that delivers raw scrap metal into the feed chute of the shredder.
The downstream conveyor and ferrous metal separation portion consists of six SGM 72-inch-by-110-inch electromagnetic drum units. Two of the drum units are specialized polishing drum magnets that retrieve electric motors and steel that is contaminated with other materials such as waste or copper, according to Riverside.
When the switch to the M-122 occurs, Upstate’s currently operating Newell 120-inch shredder will be available on the used equipment market.
“We have worked with Adam Weitsman, president of Upstate for many years. It brings us a lot of satisfaction that Adam has faith in Riverside Engineering to do a quick installation and make a major change over without causing problems. We are proud to make this positive contribution to his operation,” says Olsen.
Riverside Engineering provides metal shredding solutions for the recycling industry. The company’s product offering includes M-Series shredders, rotors, downstream separation equipment, controls automation and aftermarket parts.
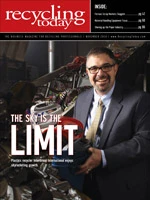
Explore the November 2010 Issue
Check out more from this issue and find your next story to read.
Latest from Recycling Today
- ReMA board to consider changes to residential dual-, single-stream MRF specifications
- Trump’s ‘liberation day’ results in retaliatory tariffs
- Commentary: Waste, CPG industries must lean into data to make sustainable packaging a reality
- DPI acquires Concept Plastics Co.
- Stadler develops second Republic Services Polymer Center
- Japanese scrap can feed its EAF sector, study finds
- IRG cancels plans for Pennsylvania PRF
- WIH Resource Group celebrates 20th anniversary