The Institute of Scrap Recycling Industries Inc. (ISRI) has been tapping into the efforts of certification and auditing specialists, staff members and recycling company owners and managers to develop the RIOS (Recycling Industry Operating Standard) process.
RIOS has been designed to offer the scrap industry a management system tailored to the unique aspects of an industry that serves customers when it buys, sells and processes material.
In particular, according to the ISRI Web site, RIOS is designed to address the quality, environmental and health and safety, (QEH&S) issues specific to scrap recycling operations.
John Bianculli and his brothers Rich, Mike and Charley of Ocala Recycling have been part of the RIOS development process from the beginning and were willing to become one of the first companies to go through the RIOS certification process.
Eventually, Ocala Recycling, Ocala Fla., was selected to be one of the three pilot program companies and worked with ISRI staff and a management system consulting company, First Environment, Boonton, N.J., to pioneer the program and bring RIOS from concept to implementation.
In the following interview, John offers his comments and insights into how the RIOS process has changed the way Ocala Recycling conducts business and manages its operations.
Recycling Today (RT): What are the operational benefits of obtaining RIOS certification and has it been an expense or an investment that has been worthwhile?
John Bianculli (JB): For us, RIOS is an investment that has paid dividends already. We’ve seen savings in the three areas where we had goals. For instance, in safety we’ve been able to steadily decrease our OSHA- (Occupational Health and Safety Administration-) recordable incidents. In 2007, mid-way to certification, our number of incidents went down. By the summer of 2008, when we felt we were ready to be RIOS-certified, the number went down again, dramatically. That’s money to the bottom line, between insurance, lost time and fewer medical bills.
On the environmental side, we recognized a decrease in exposure by maintaining the procedures we developed as part of our RIOS implementation. For example, our guys are trained on what to do to minimize the impact when a hydraulic hose breaks. This minimizes the risk of an environmental impact and helps with housekeeping, which dovetails with safety.
When our company has visitors from regulatory agencies, they see a facility that is well maintained and they see preventive procedures in place. That gives them a level of confidence and sets the tone for the rest of the visit.
On the operations side, we had a goal of fewer non-conforming loads. Of course, RIOS requires that we track results, and we’ve seen a decrease in non-conforming loads, which accrues to the bottom line.
There are other general benefits. For instance, RIOS warehouses our company’s institutional knowledge so that the information is not lost, altered or constantly reinvented over time. Knowledge doesn’t leave with the employee when that employee walks out the gate for the last time.
Plus you get to develop best practices in all production activities. We say, then, that excellence becomes repeatable. When you talk to an operations guy, that’s huge.
RT: What are some ways RIOS has changed the way Ocala Recycling operates on a day-to-day basis?
JB: In addition to what I’ve mentioned, we’ve instituted a lot of beginning-of-the-shift reporting. We learn of a potential issue, like down equipment, early on, and it gives the manager an opportunity to modify his battle plan for the day.
It’s not required, but in our implementation we developed our own computer application that is tied to our intranet application, which we call the Scorecard. One part of the system—we call it the reminder module—tracks repetitive tasks like maintenance procedures and sends out reminders and tracks those tasks to completion.
By putting the system on the computer, it allows you to see an overview of entire processes. For us, the system does a lot of the repetitive work.
With Scorecard in place, a manager spends less time collecting information on his department’s performance and more time on improving performance. It’s like having a permanent assistant.
RT: What were the initial steps you took to start down the path of RIOS certification?
JB: Very early on, my brothers Rich and Mike were attracted to RIOS. They are big proponents of creating standard policies and procedures and saw RIOS, a management system, as the next step in developing that discipline further and formalizing that process.
Once we were selected as a pilot project company, we met with First Environment and over the course of several meetings and conference calls we started to develop the system.
Since early on we’ve kept in contact with the other two pilot companies and have developed a bond with them as well. And, of course, David Wagger at ISRI has remained a strong support for us. In fact, David came to our facility during the Stage 2 audit to lend his support, and we really appreciated that. During the development of our RIOS system, we created several teams and broke the project responsibilities down among those teams. We would meet on a scheduled basis and create very specific action items and deadlines to help push the development along. You know, along with getting senior management buy-in, keeping to a schedule like this is probably the biggest key to maintaining momentum and getting through this development process.
RT: What were some things that the RIOS audit process showed you about your own company that surprised you?
JB: Well, the Stage 1 audit focuses on the system itself, and you never know how things are going to play out, especially since we were the first audit. So going into that audit, we were anxious about that. We ended up being very pleased with how well the system performed, and we received a lot of positive feedback from the auditors as we got through it with a list of findings but no major non-conformance.
The Stage 2 audit focuses on how well the system is being followed, and in this audit I think the first (good) surprise is how amazing our employees are. We spend a lot of time training, and sometimes you don’t see it paying off right away. But during the Stage 2 audit it was awesome—an exhilarating part of the whole process. The auditors didn’t let us know ahead of time which of our employees they were going to talk to, their goal being to pick a random sampling. They picked employees as they were auditing the relevant section of the standard.
The second day of the Stage 2 audit was pretty intense. It was August in Florida and our guys had been working on a sorting pad since 7 a.m. At 3:30 in the afternoon the auditors went to talk to them. They began asking questions, and the employee they went to was engaged and confident and gave such great answers. It was such a wonderful thing to see.
The whole RIOS process had become inculcated in our organization. The auditors were impressed too.
INSIDE ADVICE |
Having invested a considerable amount of time into obtaining RIOS (Recycling Industry Operating Standards) certification, offered by the Institute of Scrap Recycling Industries Inc. (ISRI), and in developing an application, John Bianculli says he is confident he and his team can help make that process easier for others. Bianculli, a vice president with Ocala Recycling, Ocala, Fla., plans to offer consulting services to other recycling firms pursuing RIOS certification. “From our experience, we can see the value of having someone who has already gone through the process assisting a company interested in going through the process themselves,” says Bianculli. “There’s no substitute for experience,” he comments. Bianculli says spreading the RIOS standard is ultimately good for Ocala Recycling and for ISRI. “A certification has more value when it becomes a recognized standard in an industry.” |
I think for employees a natural outgrowth of this is an increase in pride in the way they do their jobs. They become better trainers of new employees and can train to an actual standard that we set. We have a mentor program that all new employees go through with designated and trained mentors. If that protégé makes it 90 days, the mentor gets a bonus. They schedule times to talk about specific topics. Each meeting is scripted so everyone is working with the same definitions. It also helps with employee retention—another bottom-line goal of ours.
RT: Can you identify two or three procedural changes that Ocala Recycling has made as a result of having obtained RIOS certification?
JB: We’ve instituted a more formalized non-conformance tracking process, including driving our investigation down to the root cause level. Once we do that, we identify the steps we need to take to fix things. That generates work orders to close the nonconformance. Then, in six months, the system resets that nonconformance to be reviewed, so that we can verify that the steps we took actually eliminated the issue. That has helped us identify and fix underlying issues and reduce or eliminate recurring issues.
RT: Will you recommend RIOS certification to other recyclers, and if you do, what words of advice would you offer them?
JB: Absolutely, we would recommend pursuing RIOS certification on the grounds that it will make money for them. It will make the managers’ lives a lot easier. Managers will see economies and efficiencies in the operation of their businesses. As far as getting through the implementation process efficiently, I would recommend getting help. Talk to someone else that is going through or has gone through the process to get a feel for what to expect. Get that traction and help that can save you time and money.
John Bianculli is a vice president with Ocala Recycling, Ocala, Fla. He can be contacted via e-mail at jbianculli@ocalarecycling.com.
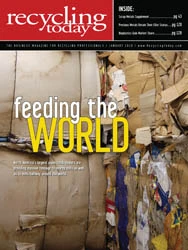
Explore the January 2010 Issue
Check out more from this issue and find your next story to read.
Latest from Recycling Today
- Nucor receives West Virginia funding assist
- Ferrous market ends 2024 in familiar rut
- Aqua Metals secures $1.5M loan, reports operational strides
- AF&PA urges veto of NY bill
- Aluminum Association includes recycling among 2025 policy priorities
- AISI applauds waterways spending bill
- Lux Research questions hydrogen’s transportation role
- Sonoco selling thermoformed, flexible packaging business to Toppan for $1.8B