After the shredding process, the traditional way processors removed ferrous scrap from the downstream line was by using a drum magnet. This magnet is capable of separating magnetic pieces, such as iron and steel, from nonmagnetic materials. The nonmagnetic residue was then sent to outside companies, where it was put through another separation process to recover nonferrous metals before disposing of the plastic, glass, rubber and other nonmetallics.
This is not the case today. Rising metals prices, along with the rising cost of transporting and landfilling material, are leading recyclers to invest in additional downstream sorting technology.
FIRST WAVEThere are two stages in metal sorting—recovery and separation—says Mark Ridall, marketing and sales manager for Wendt Corp., Tonawanda, N.Y. In the past, processors would use magnets and eddy currents to recover ferrous, aluminum and some other nonferrous material, and the rest was sent to the landfill, Ridall says. But with metal prices and transportation costs on the rise, recyclers are expanding their shredder downstreams to include the separation stage to further refine their material streams.
The first wave of separation equipment picks up where the eddy current left off. Manufacturers have come out with induction sensor separators, X-ray analyzers and digital camera technology to further separate nonferrous materials downstream of the shredder.
Induction sensor separators first appeared in the shredder world about seven years ago and gave recyclers the tools to recover metals that got past the eddy current separators, including stainless steel, copper, brass, aluminum and even plastic coated wires, says Bill Tigner, president of U.S. Shredder & Casting Group, Brookhaven, Miss., which represents Toratec Separation Systems in the North American market.
Analyzers can help recyclers produce a cleaner product by identifying specific metals, while cameras aid in the further separation of metals based on color, such as distinguishing red from white metals, Ridall says. Advancements in camera technology over the past couple of years now make color sorting even easier by allowing the recycler to program the system to look for a certain color, Ridall adds.
Behr Iron and Steel Corp., Rockford, Ill., currently uses eddy currents and high-frequency eddy currents to handle smaller fractional material, or fines, and computer-driven, air separation systems to recover stainless material. The company also recovers mixed red and white metals that it sells as regular zorba.
"Depending on future metals prices, we would consider purchasing a camera-driven separation system to further sort the red and white metals," says Bill Bremner, president of Behr. Bremner says he would also consider newer generation eddy currents that would allow Behr to pull out light aluminum from the residue product.
NEXT WAVEAs metal prices continue to rise, recyclers want equipment that can help them recover even more metals while also reducing their landfill costs. "What we are discovering is that processors want equipment that can remove nonferrous metals from trommel fines and/or post-eddy-current trash," says Al Gedgaudas, manager, resource recovery equipment sales, Eriez Magnetics, Erie, Pa.
Dennis Ciccotelli, sales and service manager for SteinertUS, Clearwater, Fla., adds that the rising prices of metals have also increased recyclers’ interest in using sensor and fines sorting as efficient methods for recovering and classifying metals from the shredder’s downstream.
To accommodate the rising needs of the industry, manufacturers have been upgrading and, in some instances, creating new sorting technology. Eriez, for instance, has built an airless metal recovery system called the ProSort that uses motorized paddles to reclaim stainless steel and 1 percent to 5 percent of the nonferrous metals missed by eddy currents, according to the company. Eriez has also come out with a technology, called the FineSort, that it claims can pull salable ferrous and nonferrous metals from fines.
How the process works, Gedgaudas explains, is after the eddy pulls out the majority of nonferrous metals, the remaining material travels to the ProSort, where the stainless steel and nonferrous materials that the eddy current missed is recovered. From there, the fines that would originally be sent to the landfill are sent through the FineSort, where the last of the salable ferrous and nonferrous materials are recovered, Gedgaudas says.
Wendt Corp. has also been responding to recyclers’ need for systems that can recognize and recover nonferrous particles. The company offers sensor-based technology that it claims can recover material smaller than the size of a dime. "We also understand our customers want flexibility, which is why we build modular additions so the equipment can be added to the recycler’s current system at any point in time," Ridall says.
Wendt continues to develop technology to recognize even smaller particles of metal. At the ISRI show in April, the company expects to announce a new product that Ridall says he believes is one of the last pieces of missing equipment to help processors generate additional revenue.
A GOOD INVESTMENTManufacturers have been focused on showing recyclers the increased revenue they can gain from investing in downstream sorting equipment. For instance, Ridall says the total installation cost for one of Wendt’s customers in South Carolina was approximately $1 million dollars. The revenue the customer generated by putting the equipment in service paid for the installation in less than four months, he says.
Tigner says the ROI (return on investment) calculation for a nonferrous sorting plant can be easily done by adding the extra income from the sale of nonferrous metals plus the reduction of landfill and transportation costs. "Depending on the existing sorting equipment, the extra metal recovery varies from 3 percent to 8 percent of nonferrous metals," Tigner says.
Behr uses time and recovery studies to track the company’s return on its sorting investment. "When we do time studies, we measure the time it takes to sort or run the equipment and the volumes we recover in that time period," Bremner says.
"The material recovered has a value and that same recovered volume reduces our landfill cost," he adds. "Putting the numbers together on the operating costs compared to the additional value gained gives us a return on investment number."
According to Eriez, by adding its metal recovery systems to an existing operation, a scrap processor can recover nearly 90 percent plus of the metals that come through the shredder and segregate the metal to maximize its value.
Ridall adds that with Wendt’s sensor-based sorting system, recyclers are sending less than 0.5 percent of metal to the landfill, saving them transportation and tipping fees.
Recently Howard Glick, president of Tri-State Iron & Metal, Texarkana, Ark., had a sorting system installed which consists of an 80-inch eddy current, 60-inch high-frequency eddy current and a 96-inch sensor sorter. Tri-State’s goal is to recover all the nonferrous it can out of the fluff so it’s not sending any of this metal to the landfill. "We recover about 99 percent of the metal in the shredder," Glick says. The system has also helped Tri-State meet its efficiency and product quality goals.
FUTURE WAVESEven though more recyclers are investing in downstream sorting technology, companies such as Huron Valley Steel Corp., Belleville, Mich., that purchase the shredders’ nonferrous mix (zorba) for further sorting are not worried about their future in the marketplace.
In fact, Huron Valley Steel purchases zorba from many shredder operators who have added downstream sorting systems, but these downstream systems don’t necessary separate the different nonferrous metals, says David Wallace, senior vice president of Huron Valley Steel Corp. "The product they produce is still an unsorted nonferrous mix, but with a greater metallic content than before," according to Wallace.
Recyclers who use outside companies for their nonferrous sorting do so for a couple of reasons; the main reason being their concern for nonferrous prices in the future. "Some recyclers choose not to capitalize on short-term markets rather than purchase equipment that they may not use in the long term," Ridall says.
The other reasons recyclers may not opt to add additional downstream sorting equipment is the volume of material coming into their yards and whether it would be cost effective to make such an investment. Bremner’s rule of thumb is there is only benefit when the cost of sorting is less than the additional value gained from sorting. "Companies will do the sorting if the additional value is there and they have a system which allows flexible, cost-effective sorting," he says.
Recyclers with smaller operations are wondering if there is any benefit to adding additional sorting capabilities. "Manufacturers have made their new sorting systems versatile enough so that both large and small processors can use them," Ciccotelli says. "Since all modern metal recovery units are available in incremental widths, small operators can scale down their investment to the volume process rate and repeat the relative results achieved by large volume processors."
The author is assistant editor of Recycling Today and can be contracted at kmorris@gie.net.
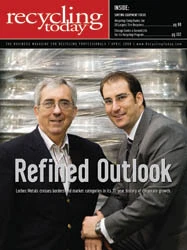
Explore the April 2008 Issue
Check out more from this issue and find your next story to read.
Latest from Recycling Today
- Athens Services terminates contract with San Marino, California
- Partners develop specialty response vehicles for LIB fires
- Sonoco cites OCC shortage for price hike in Europe
- British Steel mill’s future up in the air
- Tomra applies GAINnext AI technology to upgrade wrought aluminum scrap
- Redwood Materials partners with Isuzu Commercial Truck
- The push for more supply
- ReMA PSI Chapter adds 7 members