Using technology to automate the identification and tracking of waste and recyclables is not new. Since the German city of Dresden first employed an electronic system for cart identification in 1994, European businesses and municipalities have employed RFID (radio-frequency identification) technologies to track the collection of waste and recyclables for service assurance and billing purposes.
While RFID-enabled waste management systems are commonplace today in Europe, they are still in the early stages of market adoption in North America. This, however, is clearly the beginning of a more sweeping change. North American waste and recycling executives are already scouting available solutions on the market, launching pilot projects or rolling out actual deployments.
HOW IT WORKS
Delivering carts and managing inventory. Generally speaking, the approach to RFID-enabled cart management is simple. Using RFID tags, each garbage can or recycling cart can be associated with a specific customer address. Cart delivery personnel can quickly verify cart specifics by scanning each one using a handheld device, as well as geo-code the position of the cart using the GPS (global positioning system) receiver of the device. The scanned information, now associated with a specific customer, is sent automatically to the back office system.
Collection, maintenance and automated service assurance. With added GPS capabilities, fleet operations personnel can have real-time visibility into truck location and activity, can verify service accuracy and can quickly identify carts that have been moved, stolen or require servicing. As each household is serviced, its cart is automatically identified from its RFID tag, and the service is confirmed. The driver also can identify maintenance issues by using the inventory management capabilities of the system to update backend databases in real time with service or replacement and repair requirements. Individual customer information—from damaged carts to insufficient cart capacity—is easily captured in a centralized database. This further ensures immediate and accurate information for billing processes.
THE BENEFITS
The potential benefits of a cart delivery and management system are compelling.
Service and billing assurance are critical to every waste and recycling company. Updates on service delivery specifics and associated billing information are provided to operations in real time. This real-time service verification records detailed information on the specific container, pickup time and location and the nature of the material. As a result, the waste and recycling firm ensures greater accuracy and accountability for its programs and processes, and the customer is assured of accurate billing and any applicable recycling credits.
Complete visibility into truck and driver activity and cart usage are essential to efficient operations. An RFID-based on-board computer system provides this real-time visibility by collecting and forwarding this information back to the office. Customer service personnel have all the required information at their fingertips to respond to customer inquiries and complaints. These can be handled more efficiently and with verifiable data, including pictures and breadcrumb route data presented over detailed maps.
Automatic asset tracking enables process improvements and cost savings. Waste and recycling firms can manage and monitor their entire inventories of carts and containers automatically and online. Lost or stolen carts can be identified, and damaged carts can be flagged easily for maintenance and repair.
Since this process is automated by the on-board computer system, it requires virtually no driver intervention, thereby eliminating the human-error factor. Information is scanned and stored immediately into back-office systems.
Drivers are not required to fill out paperwork, nor do they get sidetracked with dispatch communications while on their routes. This can improve route and driver efficiencies. Furthermore, real-time service assurance data frees drivers from having to provide justification or verification of reports in response to customer complaints.
A cart management system also can provide the ability to measure participation in a recycling program. As the tags are read, the system can record which households are recycling and which are not. It can further measure service usage, such as whether a customer puts his or her cart out weekly or biweekly.
IN THE FIELD
FleetMind recently deployed an RFID-based cart management solution for Monroe County in Mississippi as a partner to truck manufacturer Labrie Environmental Group. The county had been seeking a solution to automatically track its residential waste carts to ensure service pickup and billing accuracy.
The county’s main challenge was to identify homes that were receiving regular garbage pickup service but not paying for it. Billing accuracy was a key issue for the county, as there was generally an understanding that a significant number of county residents were receiving waste pickup services free of charge. County and state laws mandate that all garbage that is set out on the curb must be disposed of by waste management services. The county and its waste management drivers could often not accurately identify the source of all waste to associate it to a specific residence and assign appropriate billing for the service.
To address the issue, the county decided to distribute customized carts implanted with RFID tags to each household. These tags identify and associate each household to a particular cart. The FleetMind cart management system then feeds immediate information back to the dispatch and back-office system to verify pickup services and to provide any updates on maintenance requirements or lost and stolen carts. With this system in place, it is now possible to identify anomalies and know which residents are not paying for service.
Monroe County implemented the FleetMind cart management system to track more than 8,000 carts and five trucks in August 2009. So far, hundreds of new billing opportunities have been identified. Monroe County has gleaned a number of benefits from the system, including accurate information for billing and invoicing, the capture of additional revenues, greater routing and service efficiency and better customer service.
WHAT’S NEXT?
Service assurance is the current and primary driver for this type of tracking solution today.
A logical next step is to add scales to the solution to allow for the weighing and metering of garbage volumes. Customers could then be billed on the amount of garbage generated as opposed to a flat monthly rate.
The clear goal of this approach is to drive higher recycling rates and encourage waste reduction. Using scales to automatically track and weigh recyclables will drive recycling credit and rewards programs to generate greater amounts of available materials. These capabilities will likely become essential to every community’s environmental policies.
The business and environmental benefits of using cart management technology to provide better waste and recycling services have been proven overseas. Now it’s our turn.
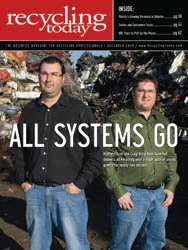
Explore the December 2009 Issue
Check out more from this issue and find your next story to read.
Latest from Recycling Today
- Aqua Metals secures $1.5M loan, reports operational strides
- AF&PA urges veto of NY bill
- Aluminum Association includes recycling among 2025 policy priorities
- AISI applauds waterways spending bill
- Lux Research questions hydrogen’s transportation role
- Sonoco selling thermoformed, flexible packaging business to Toppan for $1.8B
- ReMA offers Superfund informational reports
- Hyster-Yale commits to US production