
As commodity prices have fallen, one western material recovery facility (MRF) has sought to find ways to improve the quality and quantity of the plastics it recovers for recycling.
Revolve Recycling, which hauls waste and manages a MRF in Logan, Utah, recovers a number of recyclables, including paper, but decided to shore up its efforts to reclaim polyethylene terephthalate (PET) and high-density polyethylene (HDPE), explains President and CEO Alex Bearnson.
“The plastics are where we were actually making good margins,” Bearnson says. “And so that’s kind of where we shifted our focus a little. Yeah, we need to produce more overall of the paper and fiber and cardboard, but we also need to produce more plastics, because that’s really where we’re making the money. So, how can we produce a system that efficiently sorts more plastics while continuing to sort and clean the fibers the way we need?”
To meet its goals, the company opted to beef up its sorting capabilities. In December 2018, Revolve, which already had a 60-inch Green Eye optical sorter, added an 84-inch unit. The machines, made by Green Machine Sales LLC, Hampstead, New Hampshire, use optical scanners and patented artificial intelligence to collect 3-D data about each item in their sorting paths.
Having two sorters gives Revolve more flexibility to move between different recycling streams or materials, the company says.
“What that allowed us to do is, especially with plastics, we can actually shift,” Bearnson says. “Let’s say that PET suddenly becomes substantially more in value. What we’ll do is shift one of the two Green Eyes, preferably the larger one, to focus strictly on PET. Right now, initially, that’s what we’re doing anyway just because of volume. But the ability with two of them is, hey, we can now do HD colored. We’ve got a buyer that’s got a huge demand for it, well, let’s focus on that one. So, we’ll flip the second Green Eye [to] focus on HDPE color. And then it’s snagging every single item, and the rest of the items we’ll hand sort. It allows us to adjust to the markets as needed.”
Green Machine Sales worked with Revolve so that it can sort all seven types of plastics covered by the resin identification coding system. “We approached Green Machine with our goals along with some ideas on how we could accomplish those goals,” Bearnson says. “We don’t have engineers that designed the system, but I would say that the system layout and approach is completely new, and that was our brainchild.
“It’s a custom design, an approach that no one’s really done,” Bearnson says. “It should be good for us and our material stream.”
John Green, president and owner of Green Machine Sales, explains how the system works for Revolve.
Incoming materials travel on an infeed conveyor to the system’s polishing screen. Plastics fall to the bottom of the screen, then are fed into the Green Eye 84-inch sorter. The big sorter separates out PET, then the smaller sorter removes all the colored and natural HDPE. A crossbelt magnet and an eddy current separator then remove metals from the plastics stream. Green says, if necessary, the remaining materials can be sent through the sorters again to separate various other kinds of plastics.
The Green Eye sorters gather information based on an object’s molecular structure.
“It sorts so much better than other machines that I’ve seen,” Bearnson says. “And the downtime is minimal.”
Revolve obtains the materials it sorts from a wide range of sources, including commercial dry waste and residential recycling it collects as well as material from other collection companies and other recycling facilities that don’t have comparable sorting capabilities. For most of the materials it brings in, the company is either paid to handle them or accepts them for free. Occasionally, Revolve will pay for materials it sorts. The company bales and sells the sorted materials.
Bearnson says Revolve will look at vertical integration down the road. “But right now, our focus is to become the most efficient sortation facility, period.”
Revolve processed about 200 tons of salable plastics per month before adding the second Green Eye sorter. The system now can produce at least 500 tons to as much as 600 tons per month.
Even with the extreme temperature fluctuations that can occur in Utah and while using some equipment components that can be weather-sensitive, Bearnson says the company has experienced few issues.
“But the biggest thing is just the ability to sort literally anything that we want,” he says. “We could sort fabric with it if we wanted.”
Green says one challenge is to pace the processing of the plastics through the sorters. “We have automatic, variable- speed sensors and so forth that are set to determine certain pick rates that we can automatically slow the feed of the bales introduced into the line. So, we don’t overcharge the downstream optical sorters. You obviously want to maximize the single-stream processing at all times. But we want to make sure we manage the bale processing and make sure that we don’t overfeed the container sort line.”
Bearnson says the biggest challenge with the equipment upgrade is the general weak state of the recycling sector. “Right now, few people are upgrading on the MRF side of things,” he says. “It’s hard to convince people to give you money for a market that’s so horrible right now.”
In addition to this challenge, the approach Revolve is taking “is just a little different,” Bearnson continues. “We are taking a risk with this design. It’s quite a bit different than anything I’ve seen, and I think that exists in the industry. I think it’ll be rewarding in the end.”
Get curated news on YOUR industry.
Enter your email to receive our newsletters.
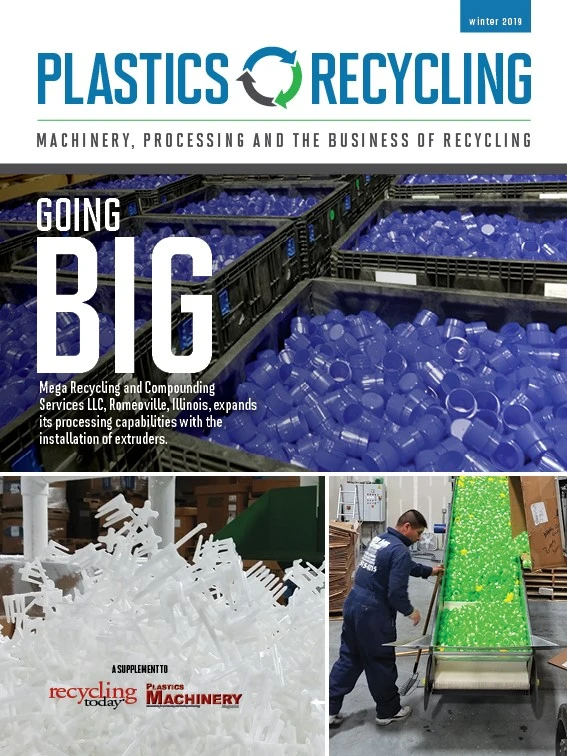
Explore the February 2019 Plastics Recycling Issue
Check out more from this issue and find your next story to read.
Latest from Recycling Today
- Toppoint Holdings expands chassis fleet
- Lego creates miniature tire recycling market
- Lux Research webinar examines chemical recycling timetables
- Plastics producer tracks pulse of wire recycling market
- Republic Services, Blue Polymers open Indianapolis recycling complex
- Altilium produces EV battery cells using recycled materials
- Brightmark enters subsidiaries of Indiana recycling facility into Chapter 11
- Freepoint Eco-Systems receives $50M loan for plastics recycling facility