When historians look back on today’s generation, it may be best remembered for two things: the explosion of technology and an increasing concern for the environment. We live in a society where presidents of corporations can negotiate business using hands-free Bluetooth headsets while driving hybrid-electric cars to reduce their carbon impact on the environment.
It is not surprising, then, that electronics manufacturers are focusing more of their attention toward making products that comply with environmental standards and appeal to environmentally conscious consumers.
"The sustainability movement and the green revolution are here to stay, and electronics manufacturers are really paying attention," says John Shegerian, founder of Electronics Recyclers International (ERI), based in Fresno, Calif.
One sign of this can be seen with Apple’s promotion for its new line of laptops. Rather than focusing on their faster graphics performance or more user-friendly touch pad, Apple has created its television and online ads to appeal to the environmentalist consumer.
Three critical components of electronics manufacturers’ efforts to achieve environmental responsibility are designing their products for end-of-life recycling, ensuring their materials are being transported to ethical recyclers and facilitating the recovery of their end-of-life products from businesses and consumers.
DESIGNED FOR DISASSEMBLY
As original equipment manufacturers (OEMs) showed heightened concern for the environment the last several years, they began consulting with electronics recyclers to determine what they could do in the production stage to increase the efficiency in the recycling process at end of life.
"Speed of disassembly is a result of effective and efficient assembly," says Doug Smith, an engineer with Sony USA, San Diego.
Dell employs a similar strategy, according to Joe Strathmann, senior manager of asset recovery services for Dell, Round Rock, Texas. He says Dell continuously consults with its asset recovery and recycling partners to influence best practices for recycling and has had tremendous results.
"We have been told by many of our partners that Dell products are the easiest to break down for proper recycling," Strathmann says.
Shegerian applauds manufacturers’ efforts to ease disassembly.
"They come right to our facilities and see transparently what’s going on, what’s working and what is still difficult, and they take that information back to headquarters," Shegerian says. "Right now our cell phones and laptops are getting turned over faster than ever before."
As a result of their collaboration with electronics recyclers concerning facilitating efficient disassembly and recycling, OEMs are reducing the number of screws and other fasteners as well as reducing the amount of lead in their products. Additionally, many OEMs are replacing engineered plastic components with easier-to-recycle materials such as aluminum and other metals, says Parker Brugge, vice president of environmental affairs and industry sustainability for the Consumer Electronics Association (CEA), Arlington, Va.
Additionally, some manufacturers are even providing guides for electronics recyclers to aid disassembly.
"Manufacturers of electronics products participating in the Electronic Product Environmental Assessment Tool (EPEAT) program make information available to recyclers about how to best dismantle their products," Brugge says.EPEAT was developed by the U.S. Environmental Protection Agency (EPA) as a voluntary program for electronics manufacturers. It is intended to be an easy-to-use evaluation tool enabling purchasers to compare electronic products based on environmental performance, as well as cost and performance considerations, according to the EPEAT Web site, www.epeat.net.
One of the biggest areas of growth in design for recycling is in reducing the amount of virgin plastics going into new electronics and making plastic components easier to recycle by limiting the types of plastics used and labeling them so they can be easily sorted.
Panasonic reports that from the 1980s to the 2000s, the company has reduced the total number of types of plastic it uses from 13 to two and also has reduced the number of plastic parts in its products from 39 to eight. As a result, the company reports a much more efficient recycling process, reducing the average time for disassembly from 140 seconds to 78 seconds.
Additionally manufacturers have stepped up their efforts to use recycled plastic in their new products, which can benefit recyclers.
"Some manufacturers have incorporated significant amounts of recycled plastic in their products," says Eric Harris, director of government and international affairs for the Institute of Scrap Recycling Industries Inc. (ISRI), Washington, D.C. "This creates demand for recycled plastics from computers, which increases the value that recyclers can capture for the material."
While OEMs are incorporating the suggestions of electronics recyclers to ease in the disassembly of their products, they are equally concerned with where electronics recyclers send materials after their products are dismantled, shredded and separated.
MONITORING DOWNSTREAM
In response to increasing pressure from environmental agencies and consumers for producer responsibility, manufacturers are ensuring that the electronics recyclers they work with are not only acting ethically in their own facilities, but are transporting their plastic, glass and metal commodities to downstream processors who also are acting ethically and in the best interest of the environment, says Thomas Hogye, manager of business development for AER Worldwide, Fremont, Calif.
"The manufacturers don’t want to work with electronics recyclers who ship metals, glass and plastics to downstream vendors if a portion of that material may end up in a landfill in China or any other developing country," Hogye says.
For this reason, electronics recyclers should confirm they are working with companies that recycle materials properly and operate their businesses with human rights in mind, Shegerian says.
"The last four years, I’ve averaged 250,000 flying miles per year," Shegerian says. "I’ve been to the glass smelter in Brazil and other parts of the world to make sure they have the best processes and practices and they don’t have 9- or 10-year-old kids working there. All the downstream vendors we have in the world, I’ve visited personally."
He adds that personally auditing downstream vendors is uncommon among electronics recyclers because of the increased costs and dangers associated with traveling internationally. However, he maintains that doing so gives his company a competitive advantage as more OEMs seek to achieve maximum environmental responsibility.
COLLECTION CHALLENGES
As electronics manufacturers strive to achieve maximum producer responsibility, they must confront many legislative challenges. More than 30 states have or are considering producer responsibility laws mandating specific actions manufacturers must take to collect and recycle their electronics, Shegerian says.
Hogye sympathizes with OEMs who struggle to follow different rules and regulations in different states.
"It is a significant problem and a mountain of paperwork for the producer to try to manage the recycling of their products when the state laws are so different and they are always trying to outdo other state laws so they can say they do it best. In the end, although good-intentioned, it’s rather counterproductive," Hogye says.
Brugge agrees that the array of state laws is cumbersome and says initiatives such as EPEAT are a more effective way to encourage producer responsibility.
"More comprehensive design incentives such as EPEAT have resulted in more design for recycling initiatives and end-of-life responsibility than the growing state-level patchwork of producer responsibility laws," Brugge says.
As of March 2009, 18 states had already passed legislation mandating the recycling of certain electronic devices, according to the Electronics TakeBack Coalition’s Web site, www.e-takeback.org. Additionally, six states—California, Maine, Massachusetts, Minnesota, New Hampshire and Rhode Island—ban certain electronic devices from being disposed of in landfills.
In the future, Shegerian predicts all states will mandate recycling for end-of-life electronics, leading to questions as to who should finance the collection and transportation of electronic scrap from businesses and consumers to recyclers.
This is a point of contention for electronics recyclers and OEMs. Most of the state laws mandating the recycling of obsolete electronics require the manufacturer to finance the collection and transportation of end-of-life electronics to the appropriate recycling facilities. While some producers may think it is unfair for them to bear the entire expense, Strathmann claims Dell fully supports producer financing of end-of-life collection and processing.
"We support a policy that would make all producers responsible for offering recovery and recycling services for their own brand products from consumers at no charge. We also believe that any legislation should not include fees or creation of new government infrastructure for collecting and recycling electronics," Strathmann says.
Some manufacturers may ultimately incorporate the end-of-life recycling costs they incur as a result of state laws into the price of their products, says Hogye, acknowledging that most consumers are probably unaware of this but would accept some fee if it meant the materials were recycled properly. He says he hopes a government subsidy program will be enacted within the next five years to encourage businesses and consumers to recycle their electronics rather than send them to landfills in states where doing so is still legal.
"In many areas there are fees associated with recycling old electronics and no structured subsidy. For instance, consider a school with storage of old electronics," Hogye says. "We can recycle their electronic waste, but we have to charge a processing fee," he says. "If, however, they can send it to the landfill for free or to a recycler who claims they can process the material responsibly for free, what do you think the school can afford to do?"
While Strathmann supports producer financing, and Hogye proposes a government subsidy, Shegerian says he believes the responsibility to recycle electronics should fall to the consumer. In California, whenever consumers purchase an electronic device with a screen measuring greater than 4 inches diagonally, they will see a $6 to $10 charge on their receipts as an advanced recycling fee, Shegerian says. He notes that opponents of the policy anticipated pushback from the consumers as a result of the charge, but says no resistance occurred. He says this signifies that consumers are willing to accept the cost of recycling.
If the current trend in state regulations continues, producers will continue to carry the costs associated with collection and recycling of electronics. However, Hogye and Shegerian say that federal, uniform standards for electronics recycling may be on the horizon. The upside to this is it would ease the demands various state laws put on the manufacturers and allow them to focus on the task at hand, rather than how to comply with narrow rules.
The author is an intern with Recycling Today.
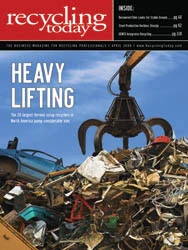
Explore the April 2009 Issue
Check out more from this issue and find your next story to read.
Latest from Recycling Today
- Aqua Metals secures $1.5M loan, reports operational strides
- AF&PA urges veto of NY bill
- Aluminum Association includes recycling among 2025 policy priorities
- AISI applauds waterways spending bill
- Lux Research questions hydrogen’s transportation role
- Sonoco selling thermoformed, flexible packaging business to Toppan for $1.8B
- ReMA offers Superfund informational reports
- Hyster-Yale commits to US production