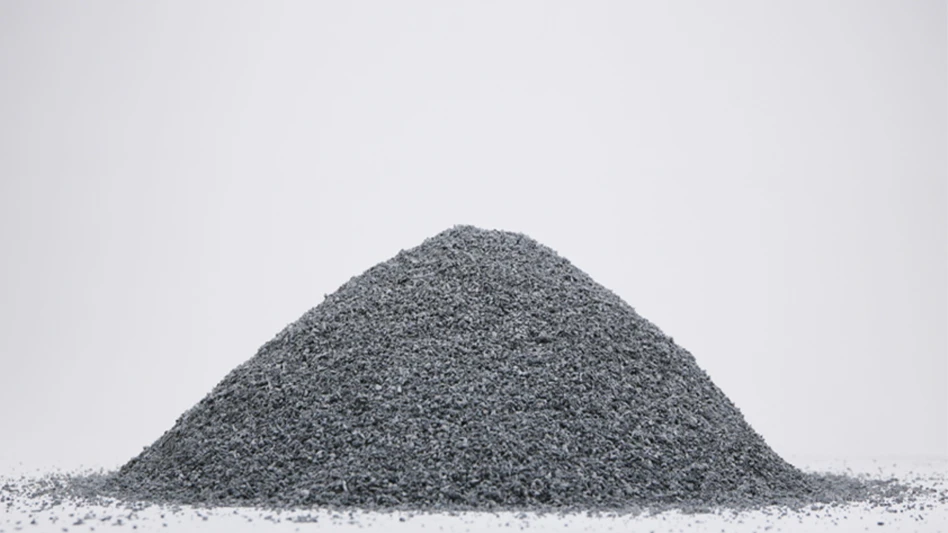
Photo courtesy of CRDC Global

Attempts in the past have tried adding plastic scrap to traditional building products, but shredding the material and dumping it into concrete or asphalt does not work in most applications because plastic repels water and cannot bond with those materials.
That might have changed with a new patented product called Resin8.
The Costa Rica-based Center for Regenerative Design and Collaboration, known as CRDC Global, has developed a process that allows plastic scrap to bond with concrete and asphalt. The company has two plants—one in Costa Rica and one in York, Pennsylvania—recycling Nos. 1 through 7 plastics for use as an additive in concrete blocks and pavers, precast concrete, ready-mix concrete and mortar and hot-mix asphalt.
CRDC Global executives envision up to 100 U.S. plants recycling all types of plastics for use in building products.
“We are excited about the possibilities,” says Ross Gibby, chief operating officer of CRDC Global and president of CRDC USA. “Our process is very locally focused. We envision each one of our locations serving … [a] 300-mile radius.”
He says the York plant, which opened in October 2022, is designed in modular units. “Our goal in York is to get it to a point where it is templated so that when we do move into a new market, we can deploy our team, get our machinery and execute the plan. It is a little bit of an out-of-the-box solution.”
The origin of Resin8 can be traced back to children picking up plastic litter every morning on a beach in Costa Rica.
Canadian businessman Donald Thomson, a materials scientist, was a young man working in the concrete industry in Costa Rica when he designed and patented a lightweight, tilt-up, insulated concrete wall system. He formed and eventually sold a company based on that product.
Thomson decided to stay in Costa Rica and moved away from concrete innovations, focusing instead on developing affordable housing and resort properties. He eventually owned a resort and saw plastic washing up on the beach every day.
He recruited local children to help pick up plastic litter every morning, but the volume of plastic became overwhelming.
Thomson then decided to develop ways to turn the collected plastic into useful products. He started with a plastic water bottle that could be folded into a roofing tile when discarded. Although the product won international awards, Thomson realized converting one water bottle into one roof tile would not solve the bigger plastic pollution problem. So, he sold the water bottle company and started working on projects that could be scaled more easily.
“He decided to attack the problem from the concrete and construction side, not from the plastic or environmental side,” Gibby says. “He wasn’t looking for a way to hide plastics; he was looking for a way to improve the construction industry and use a very abundant waste stream to do it.”
Thomson founded CRDC Global in 2018 and spent several years developing a procedure that lets mixed plastic scrap bond with concrete and asphalt. First, he shredded and granulated the plastic and mixed it with calcium hydroxide and ash before extruding the mixture, then he granulated it again to produce a final product CRDC Global calls a hybrid mineral polymer—80 percent plastic and 20 percent mineral additives. The polymer then is added to masonry products or asphalt.
The plastic is not wet-washed; rather, the mineral additives provide a dry wash that sanitizes the plastic and removes odors. According to CRDC Global, the plant produces no waste.
“We can accept the full waste stream, including contamination like food waste, sand off beaches and algae from rivers,” Gibby says. “We transform it into this material that is no longer just plastic.”
He says the transformed material has a very rough surface and open cell structure, which it maintains when granulated.
“It has irregularities that expose those mineral additives,” Gibby adds. “When it gets integrated into a concrete matrix, the cement paste permeates into all those little cavities. It is able to bond to the rough facial surfaces, then exposure of those two mineral additives has a bit of chemical bond.

“That’s where we get the strength of Resin8,” he says, as just adding plastic to concrete does not provide the strength needed for structural applications.
Resin8 looks like construction sand or limestone, Gibby says. It is one-fourth the weight of the aggregate material it replaces and reduces water absorption of the finished product, which he says is important in climates that have freeze-thaw cycles. It also has an insulation R-value that is almost three-times higher than sand and offers fire resistance when added to concrete.
“When it goes into a building, Resin8 can reduce energy usage of that building over time,” Gibby adds.
At the opening ceremony for the 14,000-square-foot York plant, Thomson, who serves as CEO of CRDC Global, said, “While we are helping to clean up plastic waste, we’re also providing a product that stands on its own in terms of performance and commercial viability. Resin8 has a positive impact on both the plastics and the construction industries as a functional example of zero waste.”
CRDC Global shopped for processing equipment in 2019 in Europe and the U.S. but ended up working with a Chinese manufacturer to customize equipment for its specific needs.
“We are producing a material that is very unrefined,” Gibby says. “It’s ugly. It’s a big chunk of plastic that looks like a lava rock, and the European and U.S. equipment is designed to produce a very clean, very detailed plastic product or pellet. The European and U.S. equipment was over-engineered for our need.”
Gibby also says the European machinery manufacturers needed 12 months to deliver one new system, while the Chinese manufacturer could deliver 12 machines in 45 days. The ability for CRDC Global to expand quickly across the world was important when selecting equipment, he adds.
The York plant is shipping Resin8 to more than 10 companies in the U.S. and Canada that need to test the material before it can be incorporated into their masonry products.

ready-mix concrete and mortar and hot-mix asphalt.
The facility operates one shift with six employees. Because accounting and other administrative functions are handled by CRDC Global, Gibby says maximum employment at the plant will be about 20 people when it is operating three shifts.
The York plant is in the scale-up phase, and Gibby says by later this summer it is scheduled to be capable of producing about 1.5 tons of Resin8 per hour. “We have a few projects in the pipeline that should be initiated in the next two to three months,” Gibby says when asked where the additional Resin8 material would be sold.
Resin8 produced at the York plant is targeted for concrete building products, such as blocks and pavers, and as an additive to ready-mixed concrete. It could replace up to 10 percent of traditional aggregate in concrete products.
Gibby says using Resin8 in asphalt will not be a primary target initially. CRDC Global has test projects in Costa Rica using Resin8 as an asphalt additive, but obtaining individual state approvals for U.S. projects would be time-consuming, he adds.
In addition to the Costa Rica and York plants, CRDC Global operates pilot plants in South Africa, the U.K., Mexico, Australia, New Zealand, Samoa and Hong Kong. He says CRDC Global is working with London-based PA Consulting to find additional markets and scale production worldwide.
Because CRDC Global accepts all plastics, including hard-to-recycle Nos. 3 though 7, to make Resin8, raw material has been pouring in. “As soon as you get some press that says you are accepting [Nos.] 3 through 7, it comes out of the woodwork. It’s amazing how many people call and ask us to take their plastic,” Gibby says.
York receives shipments from material recovery facilities and other collectors across the country, he says, but he expects shipments will become more local once additional processing plants are built.
Manufacturers that take back products such as printer ink containers also send material to York, and CRDC Global gives bags to a local residential drop-off program.
The Alliance to End Plastic Waste, a funding partner, describes Resin8 as an example of technology that unlocks the value of plastic scrap that can be replicated globally.
Virgin resin manufacturers Braskem and Dow are active in the alliance and are working with CRDC Global to get Resin8 into new markets.
Braskem used concrete blocks containing Resin8 to build a 15-foot wall in an expansion of its technical center in Pittsburgh in 2020—the first use of Resin8 in the U.S. Habitat for Humanity used Resin8 in building 200 homes in Costa Rica.
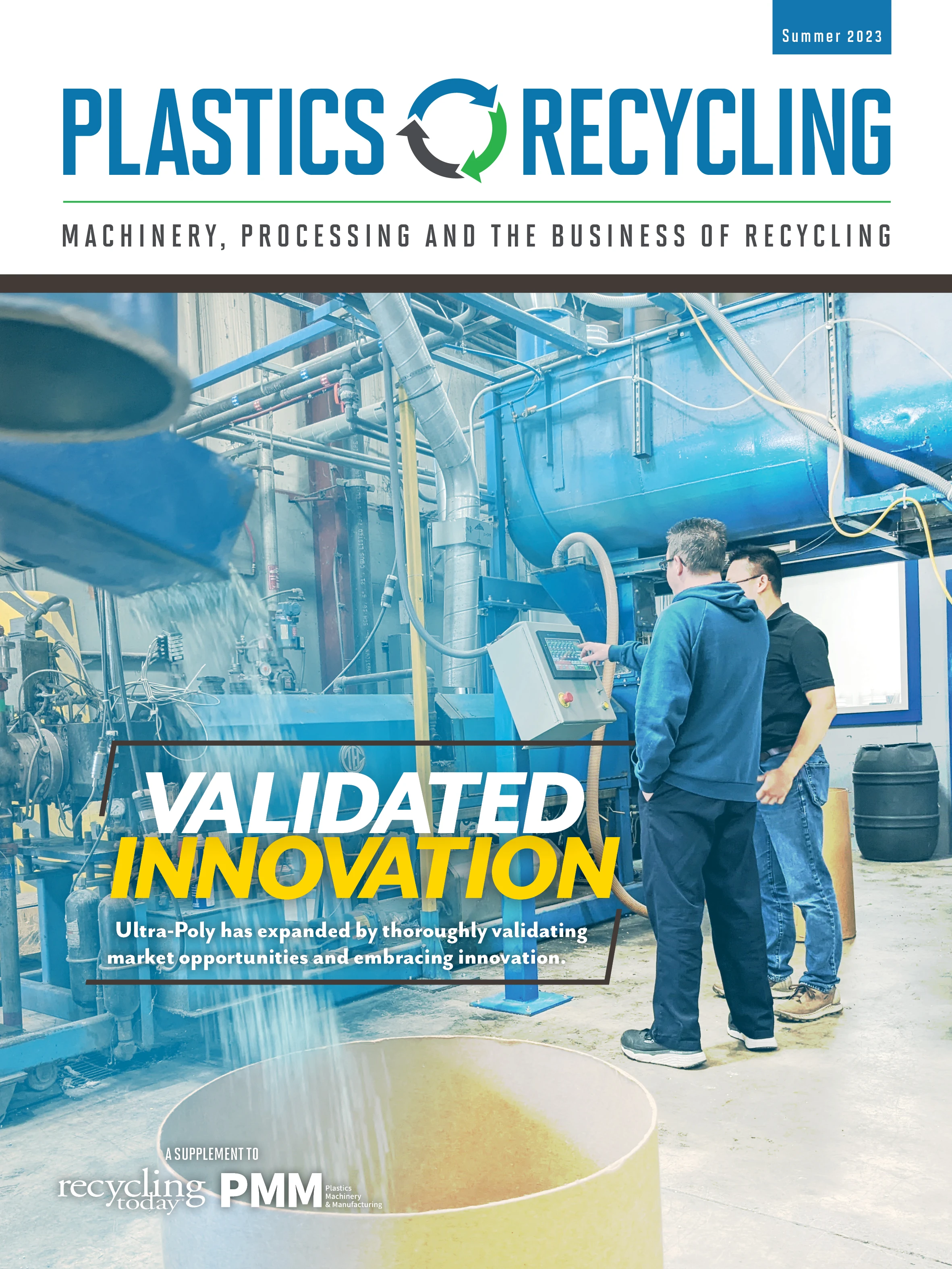
Explore the Summer 2023 Plastics Recycling Issue
Check out more from this issue and find your next story to read.
Latest from Recycling Today
- APR, RecyClass release partnership progress report
- Clearpoint Recycling, Enviroo sign PET supply contract
- Invista expanding ISCC Plus certification program
- Redwood partnership targets recycling of medium-format batteries
- Enfinite forms Hazardous & Specialty Waste Management Council
- Combined DRS, EPR legislation introduced in Rhode Island
- Eureka Recycling starts up newly upgraded MRF
- Reconomy Close the Gap campaign highlights need for circularity