
We know the benefits of plastics. They often are the more sustainable option when evaluated against other materials. Reducing a vehicle’s weight by 10 percent, which often is accomplished by using plastic to replace metal components, can increase fuel economy between 5 percent and 6 percent. It takes 10 times the amount of resources to produce food compared with the plastic packaging that protects and preserves it. Plastic products used in the medical field contribute to improved infection control. But just because plastics already were the sustainable material of choice doesn’t mean we shouldn’t continue to find ways to improve and address the unique challenges they have.
Sustainability is important as the plastics industry evolves alongside consumer perceptions, brand owners’ understanding about the recoverability and circularity of products and packaging and supply chain sophistication related to reduced environmental impacts. A 2018 Deloitte survey found two-thirds of shoppers are willing to pay extra for sustainable products. Brand owners such as PepsiCo have made public commitments to circular visions of their plastic use (“to build a world where plastics need never become waste”). Each of these factors plays an important role in optimizing products, affecting material selection, construction and disposal. This is echoed in legislative policies at all levels of government.
Bio-based alternatives
Within the realm of material development, companies have worked to create plastics with unique functional and compositional attributes. One family of polymers that continues to rapidly grow in popularity is bioplastics. They are either bio-based, meaning they originate wholly or partly from renewable feedstock; in some way biodegradable, such as through industrial composting facilities; or bio-based and biodegradable.
As a concept, bioplastics are not new—the first man-made plastic, Parkesine, was bio-based, and Henry Ford famously used corn- and soybean-based plastics to manufacture automotive parts until World War II. But the 1990s saw increased commercialization of bioplastics.
Professionals working with these polymers have had to think about how they fit within the existing recycling infrastructure and how that infrastructure can be adapted to handle these materials.
Recycling matters
For certain bio-based plastics, recycling is a relatively simple process because many are chemically identical to traditional plastics. For example, Braskem’s I’m green polyethylene (PE) is 100 percent bio-based and behaves no differently than fossil-based PE at material recovery facilities (MRFs). Coca-Cola Co.’s PlantBottle, which is up to 30 percent bio-based polyethylene terephthalate (PET), is another example. More than 1 billion bottles have been produced with bio-based PET, and they’ve presented no problems to recyclers. But manufacturers of novel polymers should keep recycling in mind to ensure they don’t unintentionally disrupt the recycling system.
New bio-based polymers in development, including polyethylene furanoate (PEF) and polytrimethylene furandicarboxylate (PTF), have physical properties that may make them more advantageous in certain applications than other available plastics. In particular, the two bioplastics exhibit increased gas barrier properties compared with PET. However, these polymers shouldn’t be mixed with PET in large volumes because they risk becoming contaminants in MRFs that don’t use optical sorting to identify and separate plastics. For instance, Wilmington, Delaware- based DuPont Industrial Biosciences has worked to prevent recycling stream disruption by reducing the risk of contamination by these bioplastics. DuPont Industrial Biosciences won the 2017 Innovation in Bioplastics Award in conjunction with Archer Daniels Midland for work commercializing a bio-based precursor to PTF.
Bioplastics and food waste
Regardless of the extra care required to recycle some of these materials, the benefits and opportunities presented by bioplastics and bio-based polymers are considerable. Bioplastics that are industrially compostable provide unique end-of-life advantages because they can break down completely via microbial digestion in the same environment as food or yard waste. This means these products can be used to help divert food waste from landfills—food waste can represent as much as 30 percent of the volume of a landfill by weight—to more sustainable end-of-life options, such as industrial composting or anaerobic digestion.
Professionals working with biopolymers have had to think about how they fit within the existing recycling infrastructure and how that infrastructure can be adapted to handle these materials.
Other compostable products used in food service also can promote diversion. In closed-loop systems such as stadiums, airports, arenas, etc., consistent selection of compostable food service products ensures little to no contamination of the recycling streams with compostable bioplastics and no contamination of the compost stream with noncompostable plastics.
A compostable polymer isn’t limited to use in food service applications. Firstly, the market for food service ware and compostable bags is a small part of the much larger plastics industry. A company only focusing on these products limits its potential growth. In addition to being bio-based or biodegradable or compostable, these polymers have other characteristics that can be put to good use.
Engaging with recycling
A great example of a bioplastic that not negatively affecting the recycling industry is polylactic acid (PLA). PLA is an industrially compostable plastic used in a wide variety of compostable products. But companies also produce PLA products outside this space. It is used widely in 3D printing because of its lower melt point and less pungent smell than some alternatives. Companies such as Total Corbion, Gorinchem, The Netherlands, are developing noncompostable grades with increased toughness and heat tolerance for other applications, including automotive.
Still, these products need an end-of-life option other than the landfill. For PLA, mechanical recycling remains an option. As a bioplastic that has been commercially available for a long time, the recycling industry does have some familiarity with PLA. A commonly expressed concern about allowing PLA to be included in single-stream recycling is its potential impact on other polymers, most notably PET. But PLA is no longer commonly used in soft drink and water bottle formats, reducing the potential of confusion via hand-sorting. PLA can be readily differentiated from PET using near-infrared technology and also can be removed through mechanical processes such as air or float separation.
Multiple studies also have shown that its presence in the recycling stream has minimal impact on the quality of the recycled material produced. A 2016 Wageningen Food & Biobased Research study on PLA and nine other potential contaminants showed no specific threats from PLA contamination, unlike the extreme impact of polyvinyl chloride (PVC). A 2017 study from the same institute showed including PLA at 10 percent in a DKR-310 (Germany’s Green Dot program) film mixture did not negatively affect the film’s properties and increased impact strength.
A commonly expressed concern about allowing PLA to be included in single-stream recycling is its potential impact on other polymers, most notably PET.
Currently, NatureWorks, Minnetonka, Minnesota, which has commercially produced PLA for decades, has a trial project in Los Angeles where PLA is collected from secondary plastic recovery facilities. Work also is being done to develop markets for recycled PLA (rPLA) beyond creating filament for 3D printing—companies such as Bioplastic Recycling Inc., Los Angeles, aim to take rPLA and make rPLA/wood composite products, such as coffee tables and embossed signs.
As industries transition from linear to circular supply chains with a greater focus on sustainable feedstocks and multiple end-of-life options, bioplastics companies are well-positioned to respond, but so are recyclers. To do so, they will need to consider the current recycling infrastructure to ensure new opportunities are being made for bioplastics that do not come at the expense of other materials.
Just as manufacturers of new and novel polymers should consider recycling, recyclers should be responsive as well. A system that is unwilling to entertain change has to be content with the stable of polymers that exist, and that does not reflect the broader community’s interest in new and novel plastics and plastic products. To prepare for a future where more bioplastics are produced, new identification and processing technologies will need to be developed and adopted for current recyclers to continue to be able to serve in their important role. Just as materials and packaging designs evolve, so must the recycling industry to capture value from these new streams.
All of this takes consideration, communication and collaboration. We are in the early days of this process, which means the moment is now for stakeholders to thoughtfully explore these new opportunities to ensure we all advance the industry sustainably together.
Get curated news on YOUR industry.
Enter your email to receive our newsletters.
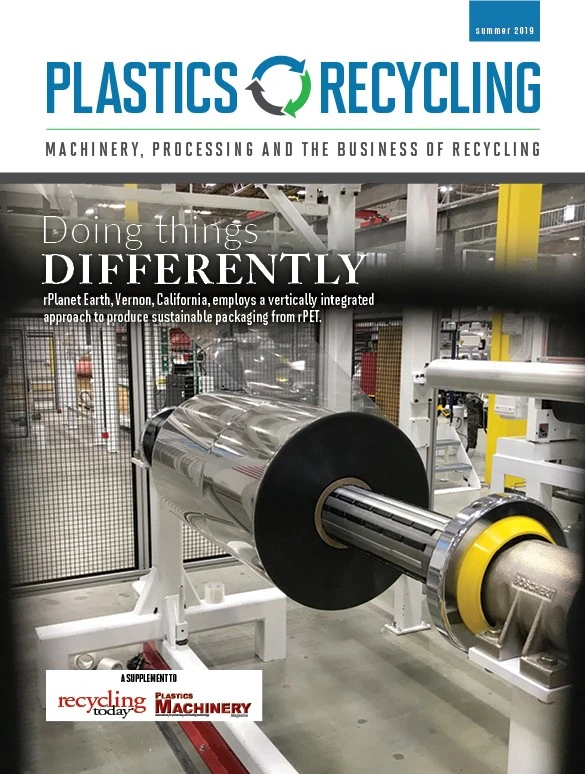
Explore the June 2019 Plastics Recycling Issue
Check out more from this issue and find your next story to read.
Latest from Recycling Today
- Circular by Shapiro releases "5 for Five" sustainability series
- Graphic Packaging set to close Ohio CRB facility
- Ameripen voices support for Maryland EPR bill
- Matalco to close Canton, Ohio, plant
- Maryland county expands curbside recycling to include electronics
- California EPS ban will be enforced
- YKK AP America introduces BetterBillet
- Fresh Perspective: Cameron Keefe