Thermoplastic contaminant removal. A patent application from Midland, Mich.-based Dow Global Technologies LLC proposes a process for removing contaminants from thermoplastics, such as postconsumer recycled (PCR) plastic, that avoids the negative aspects of previously devised methods, including solvent extraction, surfactants, caustics or complex/multistep processes. The result is a purified thermoplastic polymer useful for making other articles.
The PCR could contain a wide range of thermoplastics, including polyolefins, thermoplastic urethane and thermoplastic silicone, with potential contaminants including inorganic materials, paper, oil and food residue. The contaminated thermoplastic potentially could have contaminant levels as high as 50 percent of its total weight.

The method combines the contaminated thermoplastic with water and a dispersing agent, then subjects the combination to a shear at a temperature above the melt temperature of the thermoplastic. Optional additives include a cleaning agent to keep contaminants from redepositing, a compatibilizer and a neutralizer.
The process can run in a single extruder at a temperature from just above the thermoplastic’s melt temperature up to 536 F and, generally, a single extruder would not require venting. “However, in a system with two extruders in a series—one to convert the contaminated thermoplastic to a melt and a second to shear the combination of the contaminated thermoplastic melt, water and dispersing agent [and optional components] … there could be venting toward the end of the final zone for cooling—to dewater the combination to some extent,” the application states.
After shearing, the aqueous solution containing all the components can be separated to collect the purified thermoplastic polymer, which then can be dried to form a powder or pelletized.
Patent application 20230272180; published Aug. 31, 2023
Oscillating stack. A patent application by Reventas Ltd. of Livingston, Great Britain, describes a method of dissolving a polymer in a solvent to remove additives that can be used at commercial scale by cutting the required process time.
Current mixed plastic recycling methods offer limited value for resale and reuse, with most of the created products relegated to black, low-value and out-of-sight products.
While earlier patents discuss turning postconsumer or postindustrial polymers into virgin-like polymer using solvent, elevated temperature and pressure, the processes are time-consuming, limited to lab or batch scale and require a typical minimum polymer-to-solvent ratio of 1-to-100.
“It is therefore an object of the present invention to provide a method to dissolve at least one polymer in at least one solvent in a process for the removal of additives in plastics, which obviates or mitigates one or more disadvantages in the prior art,” the patent states.
The patent application calls for combining polymer and solvent in a reactor vessel equipped with a stack of perforated discs that oscillate in a linear motion, which can be arrayed vertically in some embodiments and horizontally in others.
The envisioned thermoplastic feedstock could be polyethylene (PE), polypropylene (PP) or, preferably, a mixed PE/PP recyclate.
According to the patent application, the stack’s linear motion cuts the dissolution time required to remove additives such as color pigments or odors from hours down to minutes and also can decrease the polymer-to-solvent ratio to 1-to-20 or even as low as 1-to-10. The patent application describes the ability to scale this process up to a vessel with a capacity of up to 30,000 liters.
Patent application 20230295394; published Sept. 21, 2023
Get curated news on YOUR industry.
Enter your email to receive our newsletters.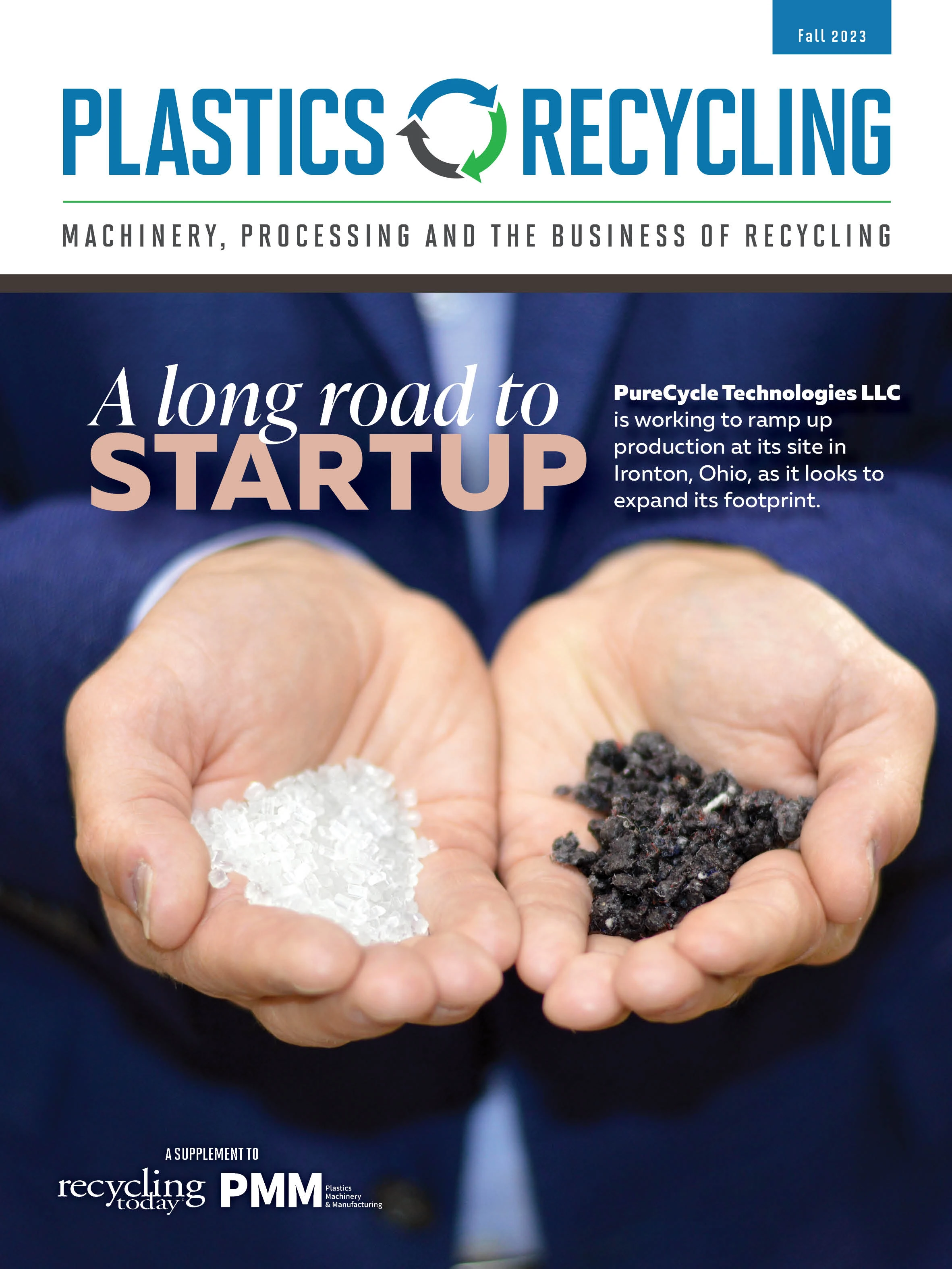
Explore the Fall 2023 Plastics Recycling Issue
Check out more from this issue and find your next story to read.
Latest from Recycling Today
- Athens Services terminates contract with San Marino, California
- Partners develop specialty response vehicles for LIB fires
- Sonoco cites OCC shortage for price hike in Europe
- British Steel mill’s future up in the air
- Tomra applies GAINnext AI technology to upgrade wrought aluminum scrap
- Redwood Materials partners with Isuzu Commercial Truck
- The push for more supply
- ReMA PSI Chapter adds 7 members