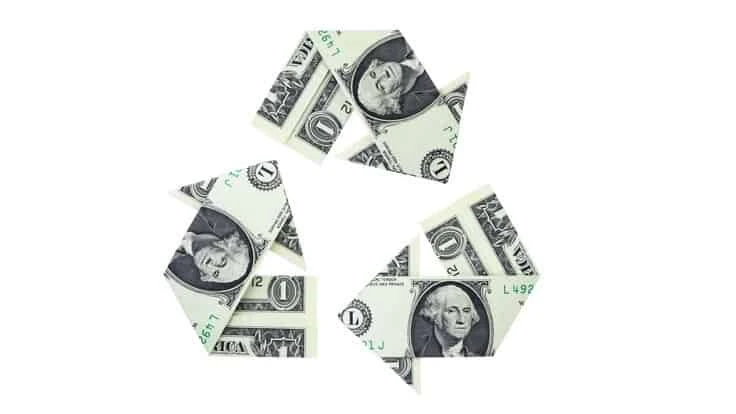
© Mcarrel - dreamstime.com
The Reducing Embodied-Energy And Decreasing Emissions (REMADE) Institute, Rochester, New York, has announced plans to invest $43 million in new technology research, selecting 24 new projects as part of its latest round of funding. The technologies aim to increase the recovery, reuse, remanufacturing and recycling of metals, polymers, fibers and e-scrap. According to a news release from the REMADE Institute, the $43 million investment is cost-shared between REMADE and the funding recipients.
Nabil Nasr, CEO of REMADE, says the results of these 24 projects will move the U.S. closer to the nation’s energy conservation and emissions reduction targets. He says REMADE’s mission is to reduce energy consumption and emissions, while increasing the nation’s manufacturing competitiveness. “Our experts are working diligently to reach these critically important goals and, in the process, accelerate the U.S.’s transition to a circular economy.”
The 24 research projects are expected to result in several positive impacts, such as increasing the recycling of materials by up to 20 million metric tons per year, saving up to 640 petajoules of embodied energy per year and decreasing greenhouse gas emissions by up to 30 million metric tons per year.
Selected projects include large-scale transformational projects that are led by industry and address issues across the supply chain:
- Selective Recovery of Elements from Molten Aluminum Alloys – Phinix LLC, Worcester Polytechnic Institute (WPI), Kingston Process Metallurgy, Smelter Service Corp. and Certified Flux Solutions LLC;
- Dynamic Crosslinking to Enable EVA Recycling – Braskem America, Case Western Reserve University and Allbirds Inc.;
- Diverting Mixed Polyolefins from Municipal Solid Waste to Feedstocks for Automotive and Building Applications – Michigan State University, National Renewable Energy Laboratory and Padnos;
- Chemical Recycling of Mixed PET/Polyolefin Streams Through Sequential Pyrolysis and Catalytic Upgrading –The Pennsylvania State University, Northwestern University, Shaw Group Industries Inc. and Process Systems Enterprise Inc. - A Siemens Business;
- Smart Additive Manufacturing Towards Use of Recycled Paper Fibers for Producing High-quality Fiber-Reinforced Plastic (FRP) Composites – University of Iowa and Impossible Objects, Inc.;
- Identification of Mixed Plastics and Valuable Electronics at the Source –University of Miami and Lid Vizion LLC;
- Recycling of PET in Sustainable Food Packaging Systems – MuCell Extrusion LLC, Plastilene SAS a Plastilene Group Co., Wingate Packaging, Sugar Creek Packaging Co., Center for Innovative Food Technology and The Ohio State University;
- Reprocessing and Upcycling of Mixed Polyurethane Waste Streams – Northwestern University and BASF;
- Efficient Purification and Reuse of Carbon Black Recovered from End-of-Life Tires – University of Utah, Idaho National Laboratory and OTR Wheel Engineering/Green Carbon;
- Delamination as Key Enabler for the Recycling of Polymer-based Multilayer Packaging – The Research Foundation for SUNY - University of Buffalo, Pacific Northwest National Laboratory, Modern Corp. and Honeywell (Performance Materials Technologies);
- Zero-Waste Recycling of Blended PET Fiber to Transform Polymer Sourcing – Circ, Fiber Industries, SeaChange Technologies, National Renewable Energy Laboratory, Pacific Northwest National Laboratory and lululemon;
- Development of Instruments and Techniques That Can Assess Tire Life and Increase Re-Manufacturing of Commercial Vehicle Tires – Michelin North America and Northwestern University;
- Development of Additive Manufacturing Material and Process Technologies to Improve the Re-Manufacturing Efficiency of Commercial Vehicle Tires – Virginia Polytechnic Institute, Arizona State University, Michelin North America, Nike Inc. and Sealed Air Corp.;
- Remanufacturing of Surface-Hardened Steel Components by Ultrasonic Surface Modification – Rochester Institute of Technology, Caterpillar Inc. and University of Pittsburgh;
- Repurposing of FRP Composites Using Next-Generation Technology – American Composites Manufacturing Association, West Virginia University, Polynt Composites, AOC Resins, Strongwell Corp., Owens Corning and Rhode Island Marine Trade Association;
- Supramolecular Interfacial Reinforcement for Manufacture Utilizing Mixed Secondary Plastic Feedstock – The University of Akron and Braskem;
- Achieving 100% Recycling Aluminum in Die Casting Applications – The Ohio State University, Alcoa USA Corp., North American Die Casting Association and CompuTherm LLC;
- Enabling Cross-industry Reuse of Comingled Waste Plastics as Quality Asphalt Modifier for Sustainable Pavement – University of Tennessee - Knoxville, Oak Ridge National Laboratory and Paragon Technical Services Inc. (a subsidiary of Ergon Asphalt and Emulsions, Inc.);
- Sustainable Automotive Manufacturing – Michigan State University, American Chemistry Council and BASF;
- Chemical Conversion and Process Control for Increased used of Polyethylene and Polypropylene Secondary Feedstocks – University of Massachusetts Lowell, Massachusetts Institute of Technology, SER North America LLC and iMFLUX Inc.;
- Material and Vehicle Design for High-Value Recycling of Aluminum and Steel Automotive Sheet – University of Michigan, Ford Motor Co., Novelis, Argonne National Laboratory, The Institute of Scrap Recycling Industries, The Aluminum Association and Light Metal Consultants;
- Analysis and Design for Sustainable Circularity of Barrier Film in Sheet Molding Composites – The Ohio State University, Kohler Co., National Renewable Energy Laboratory and Arizona State University;
- Building Re-X (BREX): Data, Methodology and Design Integration – National Renewable Energy Laboratory, Building Transparency and Skidmore Owings & Merrill; and
- Dynamic Systems Analysis of PET and Olefin Polymers in a Circular Economy – Michigan Technological University, Idaho National Laboratory, Resource Recycling Systems, Yale University, Chemstations and Honeywell UOP.
Magdi Azer, chief technology officer for REMADE, adds that the institute’s research examines the circular economy as a whole, focusing primarily on four material classes in which it can make an impact: metals, polymers, fibers and electronic scrap.
“REMADE’s projects address multiple aspects of the Circular Economy, including remanufacturing, recycling, and recovery,” Azer says. “These latest projects will, for example, explore ways to advance sustainable automotive manufacturing and address issues related to plastics recycling in food packaging—one of the fastest growing and most pressing sustainability issues in the U.S.”
According to REMADE, this latest round of funding brings its total number of research projects to more than 60, representing a value of $63 million since the institute was founded in 2017.
Nasr says a fifth round of funding, valued at about $50 million, is expected to be announced later this year. Projects that address education and workforce development will be considered in the next round of funding.
Latest from Recycling Today
- Commentary: navigating shipping regulations for end-of-life and damaged batteries
- Haber raises $44M to expand to North America
- Canada Plastics Pact releases 2023-24 Impact Report
- Reconomy brands receive platinum ratings from EcoVadis
- Sortera Technologies ‘owning and operating’ aluminum sorting solutions
- IDTechEx sees electric-powered construction equipment growth
- Global steel output recedes in November
- Fitch Ratings sees reasons for steel optimism in 2025