
Ask and you shall receive. In the case of Alpine Waste & Recycling, Commerce City, Colorado, the more the company advocates for recycling, the more material it sees in collection bins.
As for Alpine’s Denver-based Altogether Recycling material recovery facility (MRF), it was the first MRF in the state to accept plastics Nos. 3-7 and aseptic cartons and is currently the only program in Colorado to accept rigid plastics. After a recent facility expansion, Altogether Recycling’s Denver MRF is now the only facility in the state to accept and recycle polystyrene (PS) foam.
“The growth on the recycling side of the business has been exceptional,” says Brent Hildebrand, vice president of recycling at Alpine Recycling.
“Recycling is a heavily consumer-driven industry,” he adds.
Recognizing that collecting even more material from residential and commercial customers takes effort on their parts, Hildebrand says Alpine has made a point to increase the public’s awareness of the value and importance of recycling. He points to the company’s sustainability programs as a leading factor for Alpine’s growth in recycling among commercial customers.
“We went out there and pushed diversion programs,” Hildebrand says.
In addition, Alpine provides tours of its recycling and composting facilities for Colorado schools and youth organizations.
Through its customer relationship maintenance (CRM) software, Alpine says it offers its customers automated sustainability reports, which show customers precise weights of their waste and recyclables, historic trends, their performance versus other businesses and industry peers and the environmental impact of their recycling efforts.
Hildebrand explains how Alpine President Johnny Griffith started the company in 1999 out of his house with one truck. “Fast forward to today, and we’re approaching 100 trucks out there,” he says. “A lot of that has to do with our sustainability programs and being able to divert from landfill as much of the waste stream as possible.”
FULL CAPACITY

When Altogether Recycling opened in 2007, the 10-ton-per-hour system was handling about 200 tons of material per month. Within five years, more than 6,000 tons were processed monthly at the MRF.
The company’s initial residential single-stream processing line featured one baler. In 2009, Alpine added a second baler, and in 2011 it installed a commercial single-stream line. A combination of new and used equipment manufactured by various companies filled the MRF. While Hildebrand, who was part of Altogether Recycling’s inception, says that setup worked for several years, the system was operating at capacity. Altogether Recycling Plant Manager Tom Reed and Hildebrand discussed the ideal equipment for a new system.
“We had to look at it very seriously and figure out if we wanted to upgrade pieces of the system or upgrade entirely and make an innovative system,” Hildebrand says.
After a bidding process, Alpine chose Machinex, Plessissville, Quebec, to supply a system in its entirety for the Altogether Recycling MRF. Apart from a couple of conveyors, Alpine replaced all of its equipment.
In the summer of 2015, Altogether Recycling started up its $5 million system and instantly more than doubled its ability to process single-stream recycled materials.
The MRF is able to process in nine hours today what for years took 22 hours to complete, Hildebrand says.

“It’s obviously way more efficient,” Hildebrand says. “That’s just the start of it.
“This system is also better at separating materials, so we get some efficiency on the back end with less residue because of new technology,” he adds.
STRAINED OPERATIONS
While the system has allowed Altogether Recycling to double its processing capabilities, the new balers—a Machinex MTR-195 and a Bollegraaf—also are much faster. Additionally, they can be fed from any bunker in the facility.
Having this redundancy and flexibility, Hildebrand says, has made all the difference for the MRF.
Prior to updating its balers, operations would get strained by material buildup and machine shutdowns, Hildebrand describes. “And it’s not a good feeling when material builds up and you can’t run it. We were always able to manage it, but this new system was imperative for us to have,” he says.
Without walking floor bunkers and a redundant system with balers that can be fed from any bunker, when one baler failed in the old system, a bunker would fill up, and the system would have to be shut down as the full bunker of material had nowhere to go, Hildebrand explains. Although workers could pull material out and send it to the other baler, it wasn’t a productive process.
“With the two balers we have now, we can continue to process and maintain the production we have with two balers just by running the one,” he says.
“From an efficiency standpoint and a company revenue standpoint, we’re able to continue running the material and keep up with demand coming from the front end,” Hildebrand adds.
The decision to add two balers with full material redundancy was driven by “what direction the industry is going, which is the evolving single-stream ton,” he says.
Having that capability helps the company to keep up with demand and growth, Hildebrand says.
“We wanted to be able to send any material in any bunker to any baler, and the reason for that is in typical systems the full baler redundancy is what people are looking at more now; the retrofits can’t do that,” he continues.
NICE TRANSITION
Today, Altogether Recycling is processing 8,000 tons per month in its 30-ton-per-hour system, Hildebrand says.
When material enters the MRF, it is dumped on a tipping floor. Once loaded into a metering bin that feeds the system, the material travels up to a presort belt. Here, sorters pull out items that could damage equipment, such as certain types of plastics, as well as glass. Old corrugated containers (OCC) are removed using a triple-deck MACH OCC screen. After going through two paper screens, material is fed to quality control conveyor belts, where workers pull out unwanted materials.
Hildebrand says the ballistic separator does a better job than Altogether’s old system at cleaning up small bits of paper from the containers. Alpine’s leaders traveled across the country to observe the ballistic separator in action at other facilities, “doing our due diligence to see if it really works,” Hildebrand says.
Sponsored Content
Labor that Works
With 25 years of experience, Leadpoint delivers cost-effective workforce solutions tailored to your needs. We handle the recruiting, hiring, training, and onboarding to deliver stable, productive, and safety-focused teams. Our commitment to safety and quality ensures peace of mind with a reliable workforce that helps you achieve your goals.
Sponsored Content
Labor that Works
With 25 years of experience, Leadpoint delivers cost-effective workforce solutions tailored to your needs. We handle the recruiting, hiring, training, and onboarding to deliver stable, productive, and safety-focused teams. Our commitment to safety and quality ensures peace of mind with a reliable workforce that helps you achieve your goals.
Sponsored Content
Labor that Works
With 25 years of experience, Leadpoint delivers cost-effective workforce solutions tailored to your needs. We handle the recruiting, hiring, training, and onboarding to deliver stable, productive, and safety-focused teams. Our commitment to safety and quality ensures peace of mind with a reliable workforce that helps you achieve your goals.
Sponsored Content
Labor that Works
With 25 years of experience, Leadpoint delivers cost-effective workforce solutions tailored to your needs. We handle the recruiting, hiring, training, and onboarding to deliver stable, productive, and safety-focused teams. Our commitment to safety and quality ensures peace of mind with a reliable workforce that helps you achieve your goals.
Sponsored Content
Labor that Works
With 25 years of experience, Leadpoint delivers cost-effective workforce solutions tailored to your needs. We handle the recruiting, hiring, training, and onboarding to deliver stable, productive, and safety-focused teams. Our commitment to safety and quality ensures peace of mind with a reliable workforce that helps you achieve your goals.
Sponsored Content
Labor that Works
With 25 years of experience, Leadpoint delivers cost-effective workforce solutions tailored to your needs. We handle the recruiting, hiring, training, and onboarding to deliver stable, productive, and safety-focused teams. Our commitment to safety and quality ensures peace of mind with a reliable workforce that helps you achieve your goals.
From the ballistic separator, 2D materials, such as paper, travel over a top conveyor to a postsort line, while 3D items bounce and roll back toward the container line. A cross-belt magnet retrieves steel cans, and Machinex’s optical sorter, the MACH Hyspec, recovers polyethylene terephthalate (PET) bottles.
“Everything else falls down on the container line for manual sorting of other plastics,” Hildebrand says.
An eddy current and vacuum separation system collects aluminum.
The system installation took two months to complete, he says, crediting sufficient planning on Alpine’s part. “We had a good plan.”
He also credits the on-time delivery of the manufacturer for the “nice transition.”
Alpine Recycling plans to continue to invest in its recycling operations, he says, adding, “We believe recycling is economically viable.”
Hildebrand continues, “We feel the consumer is demanding good waste diversion programs, and the company will continue to invest—even in these times when other players are talking about not investing—because our customers demand it, and we feel like it’s the right thing to do.
Get curated news on YOUR industry.
Enter your email to receive our newsletters.
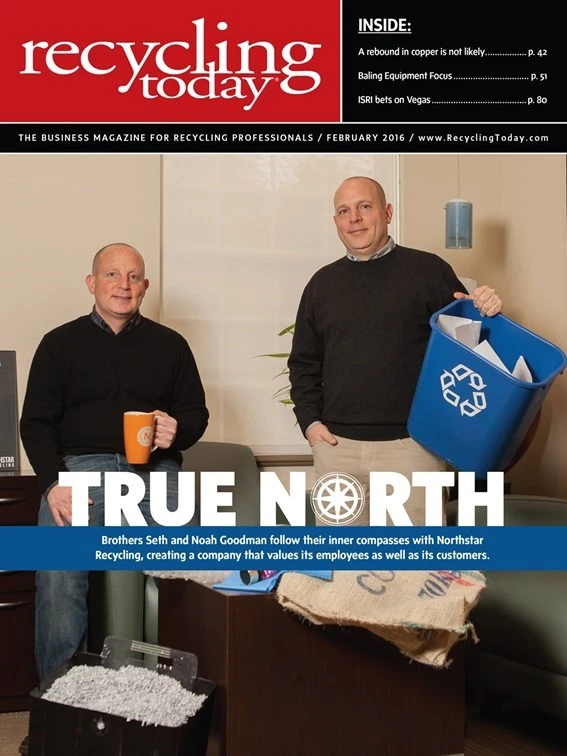
Explore the February 2016 Issue
Check out more from this issue and find your next story to read.
Latest from Recycling Today
- Green Cubes unveils forklift battery line
- Rebar association points to trade turmoil
- LumiCup offers single-use plastic alternative
- European project yields recycled-content ABS
- ICM to host colocated events in Shanghai
- Astera runs into NIMBY concerns in Colorado
- ReMA opposes European efforts seeking export restrictions for recyclables
- Fresh Perspective: Raj Bagaria