
Embedded deep in the practices of the recycling industry’s innovators is a resolute commitment to resource efficiency and waste avoidance. These commitments translate into strong recycling systems when human behaviors support and technology optimizes the capture of a suite of valuable focus materials.
Matt Todd, senior consultant at RRS (Resource Recycling Systems), headquartered in Ann Arbor, Michigan, says focus materials are “the predominant high-value materials found in a recycled material stream that drive an optimized hub-and-spoke recycling system.” For most communities, focus materials traditionally have been paper, plastic, metals and glass.
The new look of the recycling stream
However, recyclates today look much different than they did 15 years ago, creating tension among desired sustainability attributes. The prevalence of lightweight, flexible packaging formats—resealable food storage bags and pouches, detergent pouches, pet food bags and snack bags—that have better carbon footprints call for massive adjustment to recycling systems.
First, much larger volumes of flexible packaging are required to achieve a bale, so more space is required to collect this material for recycling. Second, if material recovery facilities (MRFs) were to accept flexibles via residential curbside recycling programs, most would need to perform upgrades to their sorting equipment. For example, ensuring disc screens have the proper diameter shafts and spacing to prevent films from wrapping, installing wider conveyor belts to distribute greater volumes of material and to allow for separation from the fiber stream and increasing sorting capacity and adjusting equipment to process it at scale are required to properly sort flexible packages from the rest of the incoming material stream.
Some successful efforts are underway to recycle this material. WRAP (Wrap Recycling Action Program) has recycled 0.64 million metric tons per year of films, according to a 2013 study published by Moore Recycling, Sonoma, California.
However, more remains to be done to recycle the quantity of flexible packaging available in the marketplace. The Flexible Packaging Association (FPA, www.flexpack.org), Annapolis, Maryland, estimated annual production of flexible packaging at 8.7 million metric tons in 2013. To recycle this material on par with average U.S. recycling rates (30 percent), a target capture rate at scale would mean finding markets for 2.6 million metric tons of recovered material. The most immediate, economically viable recovery option needs to be convenient for consumers and fit within the existing curbside system.
In collaboration with a handful of leading brands, manufacturers and packaging companies, RRS designed a research program to achieve their shared vision: recycling flexible packaging in a manner that allows the recovery community to capture value from this material. The program was christened Materials Recovery for the Future (MRFF), and immediately a number of additional partners joined in the effort, including trade associations and MRF technology companies.
MRFF is housed as an ongoing initiative of the Foundation for Chemistry Research and Initiatives, a 501(c)(3) tax-exempt organization the American Chemistry Council established. Sponsors are The Dow Chemical Co., LyondellBasell Industries, Nestlé Purina PetCare, Nestlé USA, PepsiCo, Plum Organics, Procter & Gamble, SC Johnson, Sealed Air, Target, the Association of Plastic Recyclers (APR), the FPA and SPI: the Plastics Industry Trade Association.
Research objectives
MRFF partners established the following research objectives in the first year:
- test the potential of existing automated MRF sorting technologies, particularly optical sorters and separation screens, to improve separation of prevalent flexible plastic packaging forms (e.g., pouches, chip bags, films, food storage bags, pet food bags) in the existing postconsumer municipal solid waste stream that consumers may at some point separate for single-stream collection; and
- define the recovery system of the future by identifying additional technologies required for plastics reprocessing to ensure the mechanical recycling of resins that currently have end markets.
The partners recognized the need for a multiyear effort and the importance of the impact of their work on the fiber products at the MRF. For that reason, measurements were taken of fiber and flexible product bales for sort efficiencies and purity.
Methodology
The research methodology involved:
- conducting a MRF flexible packaging material flow study to set a baseline;
- conducting a comprehensive set of flexible packaging material tests at MRF equipment labs to tune key sortation equipment; and
- a series of flexible packaging sortation tests in select MRFs with optical sorting capability on their fiber lines.
The MRF tests seeded a representative mix of preconsumer flexible packaging in a form that mimicked actual conditions of a standard single-stream material mix at three MRFs in the U.S. and Canada: IMS Recycling in San Diego and two Emterra Environmental facilities, one in Surrey, British Columbia, and another in Regina, Saskatchewan. The research sponsors supplied the packaging.
In the baseline test, the majority of flexible plastic packaging—88 percent by weight—flowed with the fiber streams. However, baseline testing also found the flexible packaging bale had a product purity of 26 percent.
The research team next went to the equipment labs to see how the machinery could be optimized for the future MRF tests to improve the results. Adjustments to airflow and to material spread had positive impacts in the controlled environment.
Once back in the MRF, the team studied whether optical sorters could correctly sort flexibles from fiber. After several rounds of tuning and testing, 89 percent of the flexibles were sorted correctly from the fiber. However, this was not without drawbacks. It took three passes to obtain 89 percent efficiency, an outcome that is not economically practical for most MRFs. In addition, the optical sorters erroneously sorted some of the paper into the flexible packaging product. The research team improved the product purity result during testing, achieving a flexible packaging product purity of 46 percent, up from the baseline test of 23 percent.
One of the most important byproduct findings was the quality improvement of the MRF paper products. In the last round of tests with one pass under the optical sorter, the resultant paper bale met the Institute of Scrap Recycling Industries (ISRI), Washington, specification threshold for nonpaper products.
According to the MRFF project’s research, by adjusting existing optical sorters and MRF equipment, flexible plastic packaging can be sorted at promising levels of efficiency while reducing contamination of fiber bales.
Sponsored Content
Still relying on manual sorters?
Let AI do the heavy lifting. Waste Robotics delivers reliable, high-performance robots tailored for complex waste streams. They require minimal maintenance, are easy to operate, and are designed to boost your recovery rates. Smarter sorting starts with the right partner. Waste Expo Booth #1969 & REMA #2843
Click here to see our robots in action!Sponsored Content
Still relying on manual sorters?
Let AI do the heavy lifting. Waste Robotics delivers reliable, high-performance robots tailored for complex waste streams. They require minimal maintenance, are easy to operate, and are designed to boost your recovery rates. Smarter sorting starts with the right partner. Waste Expo Booth #1969 & REMA #2843
Click here to see our robots in action!Sponsored Content
Still relying on manual sorters?
Let AI do the heavy lifting. Waste Robotics delivers reliable, high-performance robots tailored for complex waste streams. They require minimal maintenance, are easy to operate, and are designed to boost your recovery rates. Smarter sorting starts with the right partner. Waste Expo Booth #1969 & REMA #2843
Click here to see our robots in action!Sponsored Content
Still relying on manual sorters?
Let AI do the heavy lifting. Waste Robotics delivers reliable, high-performance robots tailored for complex waste streams. They require minimal maintenance, are easy to operate, and are designed to boost your recovery rates. Smarter sorting starts with the right partner. Waste Expo Booth #1969 & REMA #2843
Click here to see our robots in action!Sponsored Content
Still relying on manual sorters?
Let AI do the heavy lifting. Waste Robotics delivers reliable, high-performance robots tailored for complex waste streams. They require minimal maintenance, are easy to operate, and are designed to boost your recovery rates. Smarter sorting starts with the right partner. Waste Expo Booth #1969 & REMA #2843
Click here to see our robots in action!Sponsored Content
Still relying on manual sorters?
Let AI do the heavy lifting. Waste Robotics delivers reliable, high-performance robots tailored for complex waste streams. They require minimal maintenance, are easy to operate, and are designed to boost your recovery rates. Smarter sorting starts with the right partner. Waste Expo Booth #1969 & REMA #2843
Click here to see our robots in action!The research team recognized going into the study that flexible packaging, especially larger plastic film items, is a problem for many single-stream MRFs. However, in the test sites selected, the research team observed that improvements in screen technologies reduce wrapping on shafts, though wrapping likely will remain a concern for MRFs that do not have the most modern screen technology.
Jeff Wooster, global sustainability director for Dow Packaging and Specialty Plastics, says, “The results show us that existing technology found in more automated MRFs can separate flexible plastic packaging from other recyclable materials.”
Next steps
To implement an economically viable recycling solution for flexibles, this research shows the need for more work in five areas:- further equipment testing – This will most efficiently occur in a controlled environment, with a focus on optical sorters and design of air flow controls that optimize separation of fiber from flexible packaging. Additional technologies, such as vacuum systems, film grabbers, air drum separators and other evolving technologies, that augment optical sorters also will need to be pursued to achieve lowest cost solutions.
- end market assessment – While plastic film increasingly is being returned to packaging products, the majority is used for bulk extruded and molded products, such as plastic lumber. While most flexible plastic packaging today is constructed of a single resin that could be sorted and recycled by common methods, a growing segment is not marketable to the existing plastic film market because it has a multilayer, multiresin construction. Research is needed to estimate the market for end products produced with current and evolving conversion technologies.
- MRF processing economic analysis – An up-to-date MRF net system cost analysis that considers the economics of installing new equipment to sort flexible packaging and its subsequent impact on revenue, reprocessing costs, disposal and quality of paper after sortation must be undertaken to economically justify long-term change in MRFs and to provide useful information to municipalities that may want to add flexible packaging to the curbside mix.
- secondary processing economic analysis – Greater understanding of the technical feasibility, environmental impacts and economic value of flexible plastic packaging secondary processing is needed. Conducting trial testing with the most promising end markets will be necessary to confirm the feedstock is suitable for larger scaled applications.
- community MRF demonstration pilot – Once equipment tests are complete and end market trials confirmed, a pilot using a curbside collection program and MRF informed by the cost benefit analysis of capital costs, operating costs, secondary processing and market value of the MRF products will provide real-world metrics.
Designing the material recovery system of the future is a long path but feasible.
The findings from the MRFF-sponsored research are documented in the RRS report “Flexible Packaging Sortation at Materials Recovery Facilities,” available from www.materialsrecoveryforthefuture.com.
Get curated news on YOUR industry.
Enter your email to receive our newsletters.
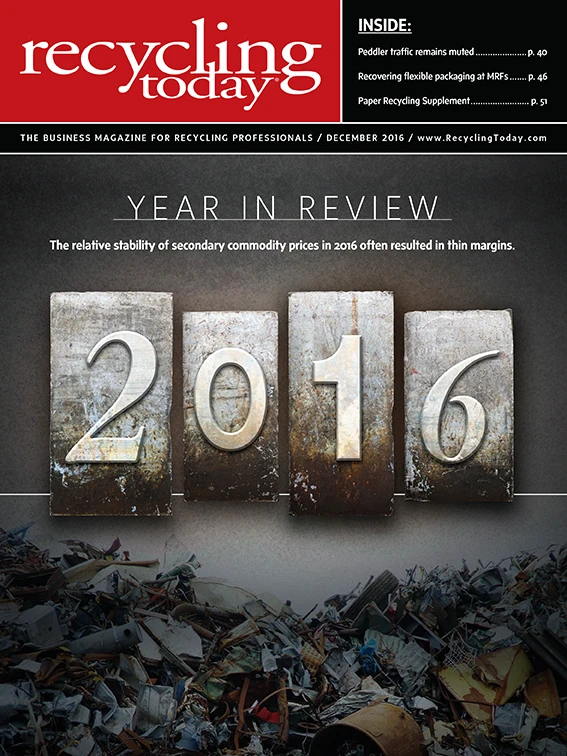
Explore the December 2016 Issue
Check out more from this issue and find your next story to read.
Latest from Recycling Today
- ReMA board to consider changes to residential dual-, single-stream MRF specifications
- Trump’s ‘liberation day’ results in retaliatory tariffs
- Commentary: Waste, CPG industries must lean into data to make sustainable packaging a reality
- DPI acquires Concept Plastics Co.
- Stadler develops second Republic Services Polymer Center
- Japanese scrap can feed its EAF sector, study finds
- IRG cancels plans for Pennsylvania PRF
- WIH Resource Group celebrates 20th anniversary