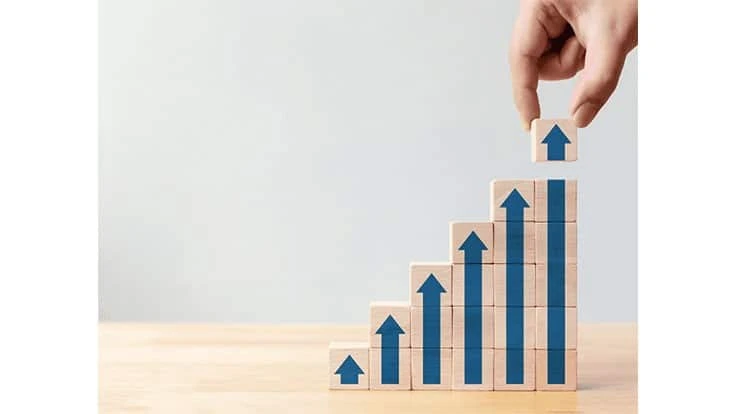

Metals markets have been robust in 2021, with demand often exceeding supply and prices on an upward trend. These circumstances have enabled some recycling companies to invest in their businesses.
Beyond the balance sheet, however, have been trends that also are prompting recyclers to consider if the time is right to leave the business on a high note, whether because of revenue that makes for a good selling proposition or because of regulatory concerns about the future of a vital processing method.
Without question, 2021 was a year of frenetic activity in the recycling industry. This activity was not only in the metals sector but also in the other portions of the industry where pricing was strong and demand remained healthy.
More winners than losers
Ferrous scrap processors certainly have experienced years when the value of their scrap inventories fell during the majority of a calendar year. Fortunately, they also experience years such as 2021, when the value of prompt scrap rose or remained steady in nine of the first 11 months of the year.
The positive price trend, which largely was mirrored in the nonferrous sector, led to healthy profits as reported by publicly traded metals recycling firms. For example, in its 2021 fiscal year, which ended in mid-2021, global recycler Sims Ltd. reported underlying earnings before interest and taxes of $287.3 million—up almost 768 percent over the prior year.
Portland, Oregon-based Schnitzer Steel Industries, with its 2021 fiscal year ended Aug. 31, reported net annual income of $170 million after losing $2 million during its 2020 fiscal year.
“Our fourth-quarter and fiscal 2021 results reflect our best operating performance in a decade,” said Tamara Lundgren, the company’s board chair and chief executive officer.
In the nonferrous sector, a new system in the People’s Republic of China allowed processors in the U.S. to send higher grade copper and aluminum scrap to that country in 2021, though a tariff on U.S. material remained a disincentive for some buyers.
Processors and secondary producers in Malaysia remained strong buyers of U.S. nonferrous scrap again in 2021, as they were in the prior year. However, an agency of that nation’s government has proposed a scrap purity and inspection regimen that could hamper what has been a prosperous business model.
The scrap opposition in China (and potentially Malaysia) seems curious if not outright self-defeating with recycling proving to be a policy and investment winner in the Paris Agreement era. The global effort toward greenhouse gas (GHG) emissions reductions favors the energy and resource savings that are inherent in recycling.
This November, Pittsburgh-based aluminum producer Alcoa Corp. unveiled technology created with the intended purpose of keeping more shredded aluminum scrap onshore in the U.S.
Also in November, St. Louis-based Alter Trading Corp. and Toyota Tsusho America Inc. (TAI) opened their Altech Recycling plant in North Little Rock, Arkansas. Alter and TAI formed a partnership at the beginning of the year to construct the heavy media metals separation plant, which is designed to provide clean aluminum scrap to make Toyota vehicle parts.
While China is rejecting or limiting scrap imports, many other nations are either placing restrictions on scrap exports or formulating policies intended to encourage keeping scrap at home.
The European Union’s Green Deal is being promoted for its recycling-friendly intentions, but global scrap traders fear it could close off free trade in scrap commodities that ultimately creates a good outcome.
“Don’t other countries outside the EU have a right to sustainable production?” asked Murat Bayram of European Metal Recycling as part of the early November Non-Ferrous Metals Division meeting during the Bureau of International Recycling Global eForum.
Trade barriers are a foremost regulatory concern for some recyclers. Environmental scrutiny is another regulatory concern, particularly among operators of auto shredding plants in the United States.

At considerable expense
While shredded scrap often gained value in 2021, the process of shredding itself has come under increasing scrutiny in areas ranging from California to Chicago to Washington—home of the United States Environmental Protection Agency (EPA).
Auto shredding has long been heavily regulated in California, with that state’s Department of Toxic Substances Control (DTSC) publicizing its campaign to “take action to protect communities” from metal shredding facilities on the homepage of its website.
In October, the DTSC received approval from another California agency to enforce a regulation with the premise that “the shredded materials metal shredders are managing is hazardous waste, and that metal shredders must apply for and receive authorization from DTSC to continue hazardous waste treatment and storage operations.” That same month, the DTSC notified Orange, California-based SA Recycling it was obligated to investigate what DTSC calls residual metal pollution levels at its metal shredding and exporting facility on Terminal Island.
California recyclers have not been alone in facing such scrutiny, however. Throughout 2021, Ohio-based Reserve Management Group (RMG) has faced a series of hurdles in the form of lawsuits and enforcement orders pertaining to its Southside Recycling facility in Chicago.
RMG says it has invested $80 million to build what it considers to be the most advanced automobile shredding facility in the U.S., featuring an on-site wastewater treatment plant and air monitors designed to measure emissions 24/7. Despite going through an established permitting process, RMG says U.S. EPA Administrator Michael Regan and Chicago Mayor Lori Lightfoot have taken actions to prevent the startup of the plant.
The EPA might have wider ambitions when it comes to stalling shredding. In early August, Recycling Today reported the EPA issued an “Enforcement Alert” targeting shredding facilities for air-quality reasons. The three-page document states in part that “EPA and state investigations have identified Clean Air Act violations at metal recycling facilities that operate auto and scrap metal shredders, causing excess emissions of air pollution. Shredder operators [should] contact their local regulatory or permitting authority for further guidance.”
Conversations among recyclers during the summer often focused on the potential cost of such compliance. Coincidentally or otherwise, a number of shredder yards changed hands in the second half of the year. To name a few, Cleveland-Cliffs acquired Detroit-based Ferrous Processing & Trading; Waterloo, Indiana-based MetalX sold its ferrous assets to Australia-based BlueScope; and PSC assets were sold to SA Recycling.
Beyond the unwelcome enforcement and trade hassles, wider economic and policy circumstances provided positive momentum in the recycling industry this year that seems likely to carry forward into 2022.

Of circularity and sustainability
Market incentives have long been the preferred motivator for many recyclers, and that preference is unlikely to change. However, a planet where governments and corporations are seeking reduced emissions and increased materials circularity has demonstrated the potential to boost markets.
Although the metals industry possesses the longest established recycling system, producers in that sector spent this past year raising awareness of the recyclability of steel, aluminum and other metals. Online presentations by Nucor Corp. and Cleveland-Cliffs in the first half of 2021 delivered that message.
The scrap-fed electric arc furnace production method is “the cleanest way to make steel, and America is the cleanest place on Earth to make steel— period,” said Benjamin Pickett, general manager of public affairs and government relations at Charlotte, North Carolina-based Nucor Corp. Pickett was speaking at an Institute of Scrap Recycling Industries (ISRI) online session in April.
Around that same time, the CEO of steelmaker Cleveland-Cliffs Lourenco Goncalves made a similar statement during the Fastmarkets AMM Scrap, DRI & Minimills Conference.
Goncalves said the steel sector in the U.S. is responsible for just 2 percent of global steel industry GHG output compared with 64 percent for China. Global warming concern surrounding the steel sector “doesn’t reside in the United States, it resides in China,” the CEO said.
Papermakers in the U.S., which rely on recovered fiber for up to two-thirds of their mill furnish, increasingly are pointing to paper’s recyclability as an advantage over plastic in the competitive packaging sector.
As part of its 2021 Sustainability Awards, the American Forest & Paper Association, Washington, honored Atlanta-based WestRock for its pizza box recycling research; Atlanta-based Georgia-Pacific for developing a paper-based mailer it calls 100-percent-curbside recyclable and a hot beverage cup that is made from 100-percent-postconsumer-recycled fiber and investing in paper cup recycling infrastructure; and South Carolina-based Sonoco for introducing EnviroSense PaperBlister packaging, which the company designed as a recyclable alternative to traditional plastic blister packaging.
Market incentives alone often have been most difficult in the plastic recycling sector, and the first quarter of 2021 featured a bankruptcy filing by CarbonLite LLC, which had been a growing reprocessor of polyethylene terephthalate (PET) beverage bottles.
While in years past such facilities exiting bankruptcy might have been a tough sell, less than three months after the CarbonLite filing, what appears to have been a competitive bidding process put all three PET bottle recycling plants into the hands of new owners.
Reached by Recycling Today, Yashovardhan Lohia, chief sustainability officer at Indorama Ventures, the Thailand-based company that purchased CarbonLite’s Dallas plant, said Indorama was pleased to have purchased a facility it considered “efficient” and “economically viable.” The Dallas plant is a “recycling facility [that] supports customer needs and consumer wants,” he said.
“Consumers want sustainable packaging, and global brands are using more and more recycled content in their bottles,” Lohia added. “We are delivering the infrastructure America needs to close the loop.”

Explore the December 2021 Issue
Check out more from this issue and find your next story to read.
Latest from Recycling Today
- EAF mill underway in California
- Constellium recycled feedstock rate holds steady in 2024
- Lamor buys remaining shares in plastic scrap-to-oil facility
- ReMA supports policy measures facilitating collection, safety and proper end-of-life management of small, medium batteries
- Balcones Recycling launches commercial recycling services in Phoenix
- Resynergi, Lummus Technology launch modular plastic recycling solution
- Shoe recycling the target of UK-based partnership
- If you melt aluminum scrap, 'Recycling Today' wants to hear from you