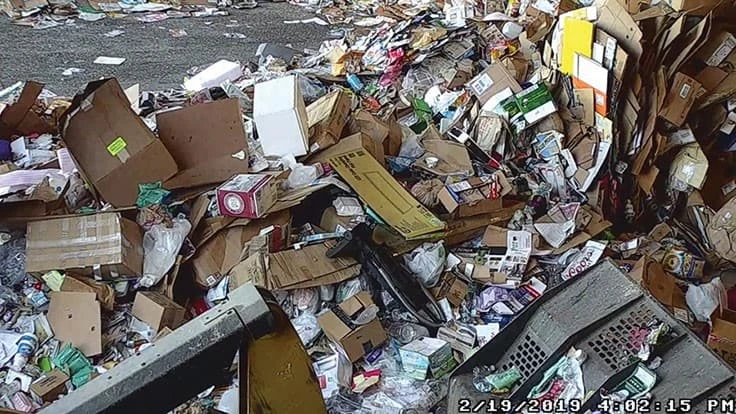
Photo courtesy of Waste Management

A picture may be worth a thousand words, but when it comes to curbing recycling contamination, its value is much greater for Waste Management (WM), based in Houston.
WM Vice President of Recycling Brent Bell says the company first began taking pictures of the loads coming into its material recovery facilities (MRFs) around the time China began cracking down on contaminated imports of recyclables in 2016 and 2017.
He says that by taking pictures of the material unloaded at the company’s MRFs, WM was able to then communicate with its customers regarding loads that contained foreign materials.
“We figured if our outbound customers were telling us the material is too dirty or has contamination, we needed to notify our inbound customers that are bringing in material where there was contamination,” Bell says.
WM first had workers on the tipping floor take photographs of the loads as they were dumped, he says. However, in an effort to keep workers out of harm’s way, the company instead had its wheel loader operators take these pictures from the safety of their cabs.
Now, WM has deployed stationary video cameras at a handful of sites. Workers can assess video and still-frame footage from a remote office setting and then share issues with drivers directly or forward them to management via email.
The value of detection
Bell explains that being able to provide real-time evidence of contamination eliminates disputes over the responsibility for the foreign material.
“By providing visual documentation of loads, you don’t have someone saying, ‘Oh, you guys just took these pictures on your own,’ or, ‘This wasn’t my truck.’ These images clearly show the truck number and the time of day because, ultimately, what we want to do is make sure that they can go back and identify the routes they were on or those customers on the routes and notify them of the contamination,” he says.
By being able to show municipalities and third-party haulers what their loads contain, he says, these customers can have conversations with specific clients who may be the source of the issue. This information also can help haulers identify which communities might need to be targeted for recycling education initiatives.
WM has worked with several camera monitoring vendors as it tests different systems, Bell says, but the most sophisticated systems allow for operators to take still shots or video and then send this visual proof out. These shots detail exactly what type of contamination is present, the estimated percentage of contamination within the specified load and any guidance on corrective actions the customer needs to take in the future.
Additionally, WM communicates any issues with incoming loads directly to drivers while at the site. “We want the drivers to be able to leave the site knowing that, if they were supposed to be bringing in clean cardboard, for instance, they’re not going to get paid for that because they had tires, batteries and all this other stuff that was not supposed to be in the clean cardboard load,” Bell says.
For extreme cases of contamination, he says the wheel loader operator could deem a load unrecyclable and push it to the side to be treated as trash.
“I think, more than anything, what this technology brings to the table is it shows our willingness to help fix the problem.” – Brent Bell, vice president of recycling, Waste Management
In addition to cutting down on contamination for economic reasons, Bell says WM works to reduce contamination at the source to help improve the efficiency and safety of its MRFs.
“Whether it’s tangling from a garden hose or a chain or the presence of a propane tank in a load, these contaminants could all cause downtime or even fires within these recycling plants. So, we definitely want to prioritize [clean loads] and make sure we don’t get in materials that are perhaps going to injure an employee or cause a fire,” he says.
Bell adds that large-sized contaminants are the easiest to identify and purge from incoming loads.
“It’s obviously really easy to see the large items that don’t belong, whether that’s a couch or a basketball goal or something similar,” he says. “We also don’t want any bagged recyclables, and when you see a lot of black bags in a load, it’s an indication that those bags typically contain trash. Mostly, any large items or things that look like they could tangle around the equipment or the machinery is what we would definitely prioritize.”
Perhaps above all, Bell says, WM is on the lookout for cellphones, electronics and other items that could contain lithium-ion batteries because they can easily start fires if left undetected. Bell says he’s hopeful the company’s emphasis on targeting items containing lithium-ion batteries will result in a reduction in this incoming material similar to when the industry worked to crack down on needles in the recycling stream in recent years. By identifying the problem on the tipping floor, he says, WM can keep these materials from being handled throughout the rest of the facility and can help haulers more effectively target neighborhoods with educational materials where this issue is the most problematic.
A deeper dive
Although WM’s camera imagery provides undisputed evidence of contamination, sometimes it doesn’t tell the full story of what a load contains. Bell estimates that the foreign materials a camera can detect usually only represent about half of the contamination that is in a load because much of the heavy materials falls to the bottom of the pile.
To better understand the contents in loads, WM performs regular audits where workers examine loads closely. Along with the images it takes, Bell says WM can paint a detailed portrait for its customers of what they’re bringing into its MRFs.
To help effect behavioral change, Bell says he thinks WM’s load-monitoring efforts speak to the company’s commitment to help customers stop problematic behaviors before they become a bigger issue.
“I think, more than anything, being able to have these discussions based on documented instances of contamination alerts customers to the fact we’re willing to take on the investment on our side and encourages them to partner with us and make investments on their side to [complete the process],” he says. “I think, more than anything, what this technology brings to the table is it shows our willingness to help fix the problem.”

An organizational change
Bell says essentially all the company’s MRFs use cameras to capture the contents of incoming loads, but only roughly 10 sites have automated cameras that can be accessed and managed remotely.
WM plans to roll out this technology over the next year to more of its MRFs to cut down on the waste it is processing.
Beyond the technology the company is currently using to monitor materials, Bell says he believes the next phase of load monitoring in recycling applications will be influenced by cameras with artificial intelligence capabilities, similar to those used on its sorting lines to identify and target specific materials.
“Ideally, what we want from these cameras is to make judgments on their own with the artificial intelligence and learn to say … that based on the camera’s memory, ‘This looks like something that does not belong.’ I don’t think we’re quite there yet, but I could see that being a very real possibility in the future,” Bell says.
Get curated news on YOUR industry.
Enter your email to receive our newsletters.
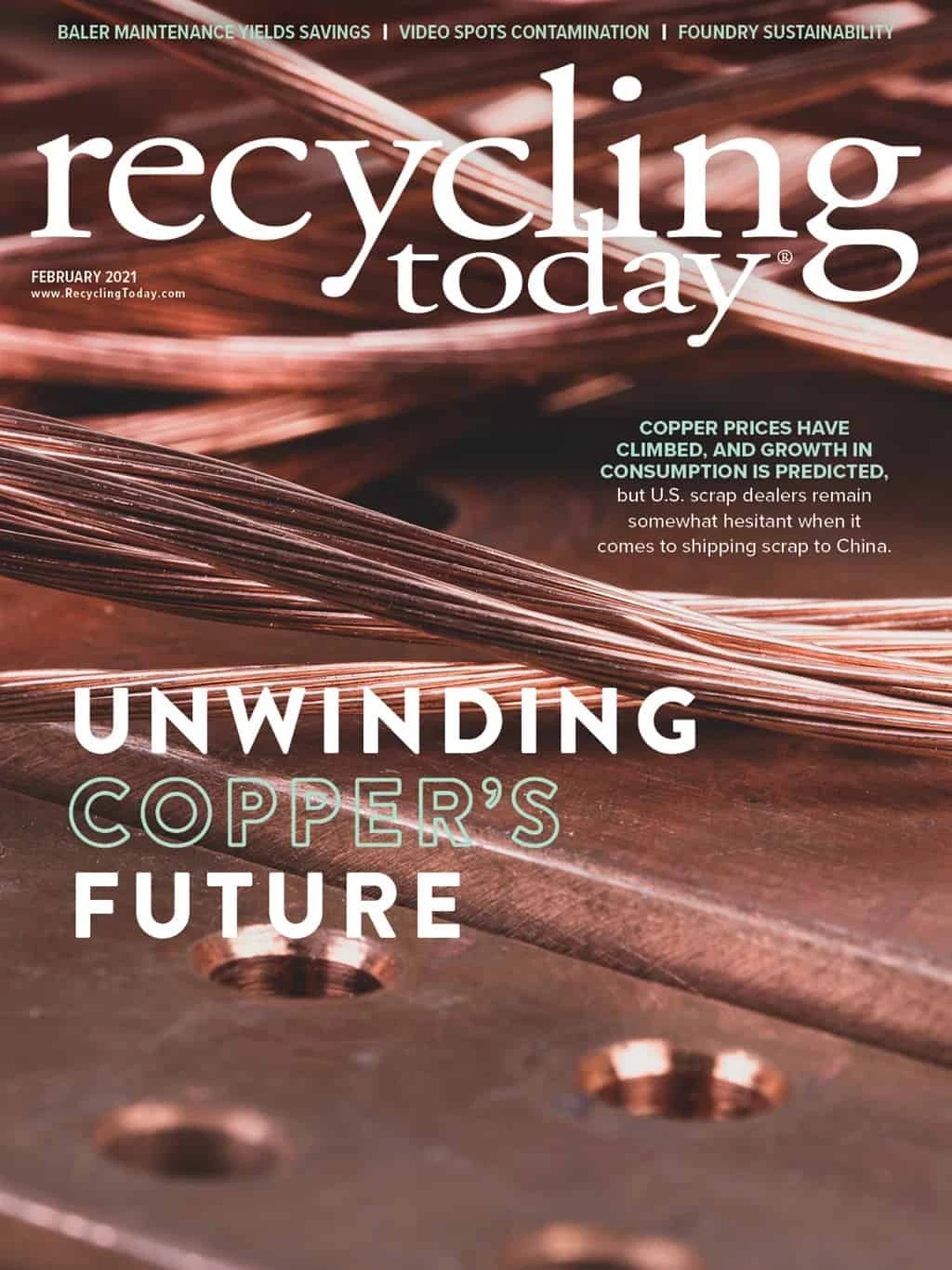
Explore the February 2021 Issue
Check out more from this issue and find your next story to read.
Latest from Recycling Today
- Toppoint Holdings expands chassis fleet
- Lego creates miniature tire recycling market
- Lux Research webinar examines chemical recycling timetables
- Plastics producer tracks pulse of wire recycling market
- Republic Services, Blue Polymers open Indianapolis recycling complex
- Altilium produces EV battery cells using recycled materials
- Brightmark enters subsidiaries of Indiana recycling facility into Chapter 11
- Freepoint Eco-Systems receives $50M loan for plastics recycling facility