The Rosen family and its key employees have built two successful recycling companies down the block from one another in Roseville, Mich. Great Lakes International Recycling has historically focused on paper recycling while Rosen Metal Recycling now operates from a separate building with its focus, as the name implies, on scrap metal processing.
An additional opportunity, however, is spurring the company to add processing equipment and curbside collection capabilities in order to step into a void in the metro Detroit recycling arena.
Great Lakes is planning to install a single-stream processing system to handle paper grades and containers collected throughout metro Detroit. The system will have enough capacity to handle commodities collected both by Great Lakes as it expands its recycling collection abilities and by other haulers serving routes through the Detroit area and beyond.
A STABLE BASE
With its foray into single-stream processing, Great Lakes is serving, to some extent, as a pioneer in the Midwestern region of the country. But the company enters its new venture with a track record and history that demonstrate its ability to innovate and compete in the recycling industry.
For several decades, the late Burt Rosen ran the operations at Great Lakes and helped turn the company into one of the Detroit area’s foremost paper recyclers. After Burt’s death in 1992, the company’s reins were handed to Burt’s brother Ben and Ben’s son Sandy Rosen.
Ben, who is now semi-retired, and Sandy, who has a background in computer science and business administration, have helped build the company’s business not only in the paper recycling industry, but also in the scrap metal markets, as a wire, cable and electronics recycler, and as a recycler of containers and other commodities collected curbside.
The company’s operations have branched out into several adjacent buildings:
•The paper operations remain the largest in terms of volume. The company has a rail spur that includes an indoor section where two cars can be loaded at once. There are also 13 truck loading docks at the 70,000 sq. ft. paper recycling plant.
•A 25,000 sq. ft. building houses metals recycling operations, where the focus in on nonferrous metals. This building was just constructed in 1999, and features two truck wells and six other doorways where trucks can be loaded.
•A third building, located across the tracks from the other Great Lakes operations, hosts corporate offices and plant space dedicated to wire processing and electronics recycling.
PAPER, METAL AND BEYOND
Great Lakes International Recycling has distinguished itself with its ability to tend to traditional revenue streams—paper and scrap metal—while also successfully venturing into newer areas, such as in the recycling of plastic containers and electronic scrap.
While many of the company’s goals involve expanding into additional recycling markets, to a visitor to Great Lakes International Recycling there is no mistaking that paper recycling remains a key component of corporate goal number one: growing from processing 10,000 tons per month to 40,000 tons per month.
In the company’s paper processing facility, a Bollegraaf 100 baler churns out bale after bale of different paper grades, nearly all of which are taken by a forklift driver to a waiting truck or railcar heading directly to a mill.
Great Lakes executive vice president of marketing and international sales Tony Joseph proudly notes that the company has set up its own JIT (just-in-time) inventory control system that allows it to minimize the amount of material warehoused on site. “Despite our increased volume, our warehouse needs are down 40% due to the JIT practices,” says Joseph. “I would have to say that we are vigilant about adopting JIT methods because we’d rather use the space we have for processing and other productive uses.”
In the best case scenario, according to Joseph, “we try to have materials tipped on the floor, sorted, processed and inside a truck or railcar to be shipped all within six hours.”
The number of paper grades the company handles is almost as numerous as the number of grades existing in the PSI specifications list. While OCC (old corrugated containers), ONP (old newspapers) and office paper grades are predictable volume leaders, such items as printer’s trimmings and leftover brochures on glossy stock from the Big Three auto companies adds constant variety to the grades handled by the company.
Metals recycling has also grown in importance, with Rosen Metal Recycling having been pulled out as a separate business with its own staffing and processing equipment. Canopied unloading areas and the spacious indoor facility allow the company to keep operating through the sometimes severe Michigan winters.
Beyond the established paper and metals markets, however, Great Lakes has proven to be adept at identifying and successfully entering new recycling markets, including segments of the plastic market, electronics recycling, and—soon—the single-stream curbside recyclables market.
In addition to handling plastic containers collected by curbside programs, Great Lakes has identified other plastic recycling opportunities within both the industrial and household markets.
Plastic packaging and materials used by the auto industry and its supplier companies has proven to be one of those key areas. Seat foam and shrink wrap are among the types of plastic for which Great Lakes has found markets while alleviating manufacturers from having to dispose of the material.
The company’s location in the metro Detroit area—one of the largest pleasure craft boat owner’s markets in the U.S.—has offered another niche opportunity. During the spring “re-awakening” season for local marinas, Great Lakes collects the plastic marine “shrink wrap” in which boats are shipped overland or stored, and sends the processed material to a waiting consumer.
Overall, the company plans to continue paying attention to plastics recycling, as its corporate goal of “increasing plastic handling by 60% per year” for the next several years demonstrates.
Another emerging market that Great Lakes has entered is the electronics recycling segment. While the processing of wire and cable has been pursued by scrap companies for some time (and Great Lakes does that, too), the opportunities in electronics recycling are not as clearly established. “We take personal computers from all over the country,” says Joseph, “including monitors and keyboards.”
The wire and cable processing portion of their electronics recycling business remains a key profit center, with the company owning a wire stripper, a chopper and a granulator for the plastic insulation. Regarding the plastics portion of the electronics stream, Joseph says, “it requires volume and weight to be profitable, but there are end markets to be served.”
VENTURING INTO THE SINGLE STREAM
In the realm of identifying recycling opportunities, one of the cases that has presented itself to the managers at Great Lakes is the collection and processing of recyclables collected by municipal programs in metro Detroit and other parts of Michigan and Ontario.
Great Lakes currently has the capability to process commingled collectibles, with mixed fiber being tipped into one area and mixed containers in another.
A series of equipment helps separate glass, plastic, aluminum and steel containers from one another, while a Lubo Star Screen system helps separate the mixed fiber stream into marketable grades.
But Tony Joseph and others at Great Lakes have witnessed the tendency for the large waste hauling firms (who also have recycling collection contracts) to outsource much of their recyclables processing. At the same time, haulers looking to minimize costs on the collection end are increasingly turning to single-stream collection, where not even fiber and containers have to be separated by home owners or collection route personnel.
Haulers like the single-stream concept because “they no longer need a recycling fleet of separate trucks. Single-stream recyclables can be loaded onto standard garbage trucks and compacted,” says Joseph. Compacting recyclables also allows them to be shipped more efficiently and to go longer distances, Joseph notes.
To make sense of the compacted, thoroughly mixed-together single stream, Great Lakes will be installing a sorting and separating system designed and built by CP Manufacturing Inc., National City, Calif. “This will be the first plant of its type in the Midwest and only the fifth in the U.S.,” says Joseph.
The system will initially separate the fiber from containers, with the fiber materials then being conveyed to the existing Lubo system in the paper recycling building. The containers fall into another sorter, where a trommel separates out broken glass, and a magnet next picks up steel cans. Using eddy currents and other equipment, positive sorts then occur for aluminum cans and polyethylene (PET) bottles. From the remaining material, a marketable HDPE grade is separated out, while residuals head down a “landfill conveyor” that delivers them to a waiting roll-off.
Joseph is convinced of the system’s ability to produce clean, marketable grades for all materials. “They’re almost too clean,” he remarks. “There’s not even a hint of broken glass in the paper.”
PLANS FOR GROWTH
“We will have the capacity to process recyclables collected throughout metro Detroit,” says Joseph. The company has signed its first collection contract with the suburb of Grosse Pointe, and has agreements with Waste Management to process recyclables collected in several other communities.
The system is also being designed to have the capacity to take in recyclables from beyond metropolitan Detroit, and due to the nature of hauling compacted single-stream recyclables, Joseph is confident that Great Lakes can serve as a processing center for recyclables collected throughout the state of Michigan.
“As far as shipping, haulers who collect single-stream recyclables in compacting trucks will have the same limitations as solid waste haulers,” says Joseph. “With single-stream, we can go over to Canada, up into the ‘thumb’ of Michigan or even to the Upper Peninsula,” he continues. “Just like garbage is hauled to out-of-state landfills, contract haulers can bring their recyclables here, and they’ll be charged a lower tipping fee than they’re charged for their solid waste.”
With Great Lakes operating profitably and growing with its current systems, Joseph acknowledges that the company is taking a bit of a risk by moving to the newer technology. But he is confident that the company will benefit from the installation of the single-stream system, and that the future of Great Lakes International Recycling is bright. He believes the Rosen family has demonstrated its ability to manage a company with a series of complicated operations that can grow together without any of the parts being neglected.
“I feel great about this company,” he states. “We have greatness within our company and we are doing great things.”
The author is the editor of Recycling Today.
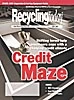
Explore the May 2000 Issue
Check out more from this issue and find your next story to read.
Latest from Recycling Today
- Fitch Ratings sees reasons for steel optimism in 2025
- P+PB adds new board members
- BlueScope, BHP & Rio Tinto select site for electric smelting furnace pilot plant
- Magnomer joins Canada Plastics Pact
- Out of touch with reality
- Electra names new CFO
- WM of Pennsylvania awarded RNG vehicle funding
- Nucor receives West Virginia funding assist