
A few years ago, Hong Kong-based Nine Dragons Paper (Holdings) Co. Ltd. announced plans to expand its footprint in the United States through ND Paper LLC, the company’s Oakbrook Terrace, Illinois-based subsidiary.
In June 2018, ND Paper purchased paper mills in Rumford, Maine, and Biron, Wisconsin, from Canada-based Catalyst Paper. Later that same year, ND Paper purchased a mill from Canada-based Resolute Forest Products Inc. in Fairmont, West Virginia. In October 2018, ND Paper acquired a kraft pulp mill in Old Town, Maine.
ND Paper set its sight on revitalizing these four mills.
“We have four mills, three of which were built more than 100 years ago,” said Ken Liu, chief executive officer at ND Paper, in a 2019 news release from the company. “By focusing on high-return strategic investments, we are building world-class, first-quartile mills that deliver innovative, high-quality products for our customers.”
The company finalized most of the construction on the rebuilds and conversion projects for these four mills in 2020.
“Trying to do a major rebuild during a pandemic where you have issues with getting contractors and vendors into the mill and assist you to put things together was not fun,” says Eric Bauer, director of business operations at ND Paper. “But we worked through it.
“Everything is fully operational now, running at capacity,” he adds.
Perfecting recycled pulp
Of its four locations, ND Paper has two pulp and two paper mills. The company’s Biron mill operates two machines, one that makes recycled containerboard and one that makes coated groundwood.
The company also operates a mill in Rumford, which operates three machines that make coated printing papers, uncoated printing papers and virgin brown packaging grades.
Of ND Paper’s pulp mills, Fairmont focuses exclusively on making recycled pulp. The company’s Old Town mill operates an unbleached virgin kraft mill as well as a recycled pulp operation. The company announced in April that it was launching a recycled pulping operation at the Old Town facility. That new production line makes about 200 metric tons of unbleached recycled pulp per day.
ND Paper is one of a few companies in North America that is making recycled pulp. ND Paper’s Biron facility produces recycled pulp that is consumed internally to make containerboard and linerboard, while recycled pulp produced at Fairmont and Old Town is sold to the open market as well as to ND Paper’s parent company in Asia.
Bauer says the company is on track to produce a combined total of 313,000 tons of recycled pulp at its Fairmont and Old Town facilities.
ND Paper consumes regionally sourced recovered paper, mostly old corrugated containers (OCC) with some mixed paper, as its primary feedstock for its recycled pulping operations. Bauer says the amount of OCC and mixed paper used in each batch of recycled pulp varies depending on whether the pulp is being sold to make containerboard or away-from-home tissue.
“Depending on what grade you’re making, you use different feedstocks,” he says. “From a containerboard side, we start with OCC, and we supplement like anybody else [does] with mixed paper. When you get to away-from-home tissue, it might be mixed office waste, news and those kinds of things, since they need a brighter, cleaner fiber in some cases.”
Recycled pulp can be used to make containerboard, away-from-home tissue products and for molded fiber applications. Bauer says ND Paper has sold some of its recycled pulp to domestic buyers at mills that manufacture away-from-home tissue products.
“Obviously, last year, the away-from-home tissue market was a very, very different world,” he adds. “A lot had gone away, but that [demand] is starting to come back.”
ND Paper sends some of its recycled pulp to its Asia-based parent company to make containerboard, as well. While ND Paper doesn’t sell its recycled pulp to other containerboard producers overseas, Bauer says other North American companies have started selling recycled pulp to other Chinese mills to make containerboard in recent years.“With the new tariffs that China put on in terms of waste product, there is need for recycled pulp to go to China, where we can actually produce it here, clean it here, make a bale, put it in a container and send it,” Bauer says.
Aside from shipping some of its recycled pulp to Nine Dragons, Bauer says the company prefers to sell its recycled pulp to domestic buyers, particularly this year as shipping has been more challenging.
Bauer adds that he expects to see more paper mills adding the ability to make pulp from recovered paper rather than buying recycled pulp to make containerboard or away-from-home tissue products. “They’re going to be more apt to say they’ll use the tons on their own versus go to the outside and find someone to buy recycled pulp [from],” he says.
Focused on operational enhancements
While ND Paper prioritized acquiring, rebuilding and converting its four U.S. mill operations in the last three years, Bauer says the company will focus on enhancing these operations rather than investing in or acquiring new facilities in the near-term future.

Bauer says, “Now, we’re just honing in on our processes and output capacities. We want to make operational adjustments to modify systems. We’re doing that across the board, not just with our recycled pulp mill. For example, in Old Town, we’re bringing online some other aspects to supplement and increase operations by a few thousand tons per year.”
He adds, “Now we’re going to hone in more to increase output and capacity, ideally for domestic markets and to support our own initiatives in other spaces.”
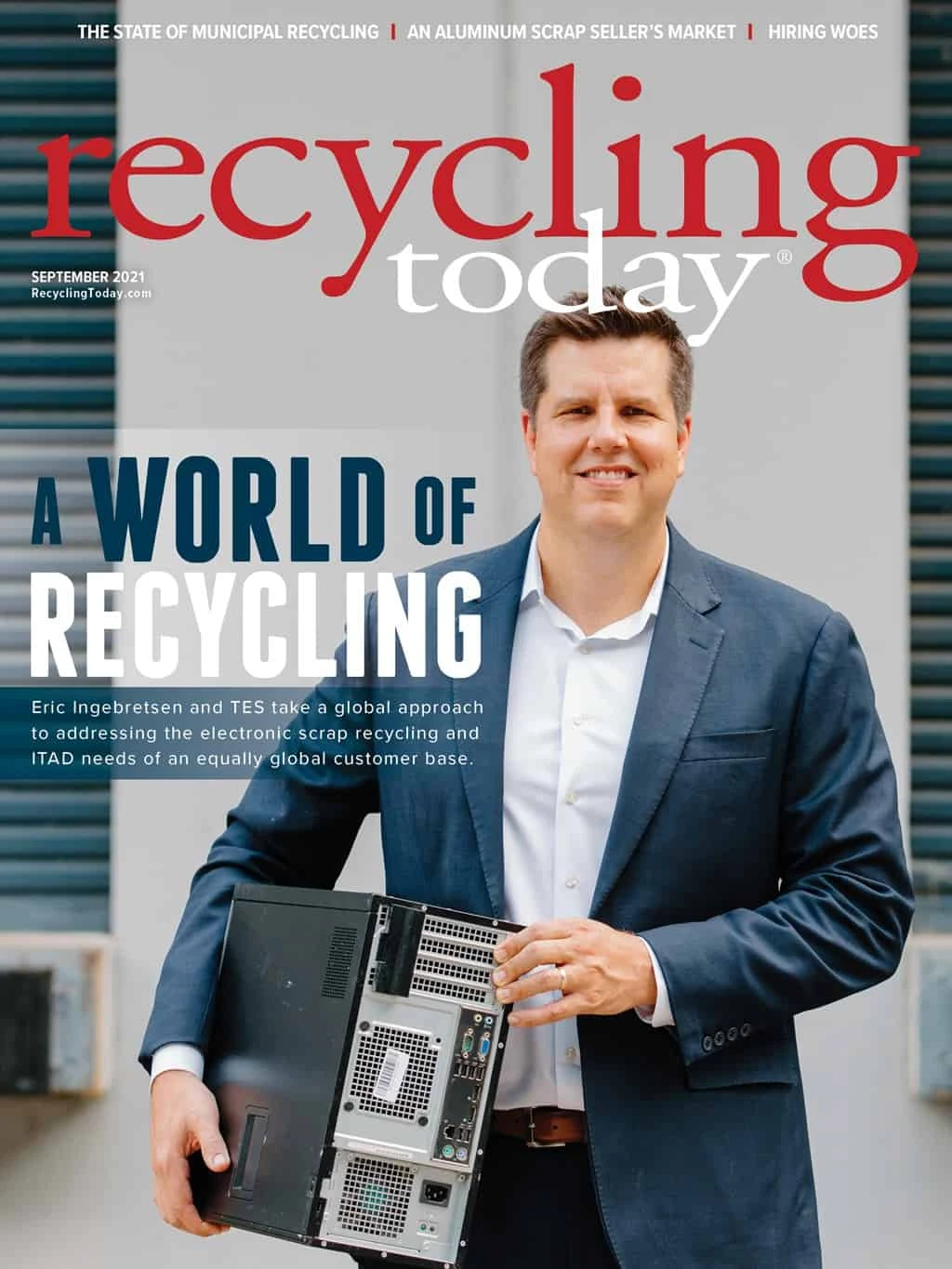
Explore the September 2021 Issue
Check out more from this issue and find your next story to read.
Latest from Recycling Today
- Aqua Metals secures $1.5M loan, reports operational strides
- AF&PA urges veto of NY bill
- Aluminum Association includes recycling among 2025 policy priorities
- AISI applauds waterways spending bill
- Lux Research questions hydrogen’s transportation role
- Sonoco selling thermoformed, flexible packaging business to Toppan for $1.8B
- ReMA offers Superfund informational reports
- Hyster-Yale commits to US production