
Recycled plastics entering a second or third life face some challenges. Repeated exposure to heat, light and processing can degrade mechanical properties, such as impact resistance.
Modifiers can help compounders produce materials that exhibit the physical characteristics, such as stiffness and strength, their customers seek, and some even make processing easier. Modifier manufacturers include Milliken Chemical, Addivant and DuPont.
Impact modifiers
“We look frequently at impact modification,” says Kevin Cronin, vice president of sustainability and R&D at Ultra-Poly. The company is a recycler and compounder based in Portland, Pennsylvania, that deals primarily with polypropylene (PP), polyethylene (PE) and polyvinyl chloride (PVC).
“As we produce polypropylene compounds, in order to get polypropylene that has copolymer-like properties, i.e., impact strength, we are constantly looking at incorporating impact modifiers,” he says. “Ideally, they would be streams of compatible polymers that are also from recycled sources—primarily postindustrial recycling.”
Ultra-Poly blends in elastomeric polymers that add impact strength in a PP compound, Cronin says.
PP is used in a wide variety of applications, ranging from car bumpers to pharmaceutical vials. When used in car bumpers, high impact strength is important to prevent cracking. Recyclers and virgin PP compounders often add rubber to increase impact strength. However, adding too much rubber to PP can reduce stiffness and increase viscosity, possibly making it more difficult to process. In addition, rubber, depending on the source, can be significantly more expensive than PP.
That has led companies like Milliken Chemical, Spartanburg, South Carolina, to develop modifiers that can improve impact strength without negatively affecting, and even perhaps improving, processability and stiffness. Milliken has created a new modifier called DeltaMax.
“We refer to our technology as a performance modifier,” says Prem Patel, global strategy and business development manager for Milliken’s plastics additives business. “DeltaMax is highly effective in redistributing the rubber content within polypropylene, which enables significant improvements in impact strength and allows recyclers to use lower amounts of rubber in their compounds,” he says. “This in turn helps drive improvements in the melt flow and stiffness properties of the recycled polypropylene that is on the market today.”
The product is unique in its ability to help improve all three properties, Patel says.
“There’s always this challenge to increase the processing, the stiffness and the impact performance,” Patel says. “And, typically, when you buy a performance modifier, such as an impact modifier or peroxide, it’s boosting one and sacrificing one or more of the others.”
Milliken’s DeltaMax allows recyclers to eliminate or reduce the amount of traditional impact modifiers they add, he says.
DeltaMax will be available in powder form and as masterbatch pellets. Milliken is working with several recyclers and auto manufacturers on the new performance modifier, and the company hopes to introduce it to the market later this year, Patel says.
Impact modifiers also are available for other types of plastics. Additives manufacturer Addivant, headquartered in Danbury, Connecticut, supplies an additive that is designed for recycled acrylonitrile butadiene styrene (ABS) and polycarbonate (PC).
“When recycled [plastics] are used, they don’t have as good mechanical properties as virgin materials,” says John Yun, technology and marketing manager of polymer modifiers at Addivant. “They lose properties, but we have a product to help recover those properties.”
Between 5 percent and 20 percent of Addivant’s RoyalTuf 372P20 is blended with recycled ABS or PC. “It is used to recover the lost impact properties as well as the lost weather-resistant properties,” Yun says.

Nucleating agents /crystallization additives
“We are constantly looking at ways to enhance specific properties of some of our recycled compounds, so we look at things like crystallization additives,” Cronin says. “Crystallization enhancement makes a compound mold a little more quickly [and] set up a little more quickly in tooling, so it can improve injection speed or injection cycle times. It also smooths out mechanical properties.”
Also known as nucleating agents, these additives most commonly are used in PP to enhance mechanical properties and improve molding productivity and transparency. Nucleating agents also can be used in polyesters, including polyethylene terephthalate (PET) and polybutylene terephthalate (PBT).
“That’s a common ingredient used in polypropylene in both virgin and recycled resin but may be especially critical in recycled resin, because when you expose plastics to heat, you tend to degrade them,” Milliken’s Patel says. “Degrading doesn’t just mean yellowing. It also means breaking down the polymer. You’re breaking down its chains. When that happens, you lose stiffness and mechanical properties. Fortunately, for polypropylene, there are a lot of nucleating agents out there that can help impart stiffness and improvements to the plastic.”
Milliken’s Hyperform nucleating agents work at a molecular level to improve the structure of the PP, its stiffness and its processing characteristics. The addition of a nucleating agent can allow recycled plastic to be used for applications that require high-grade or virgin resins.
Some nucleating agents also can reduce cycle times associated with processing plastics in injection molding, extrusion or thermoforming.
“The overall time to heat it and cool it is much shorter,” Patel says.
Milliken’s Hyperform HPN-20 E improves the impact strength and stiffness of PP while reducing shrinkage and warping. Hyperform HPN-68 L is designed to improve crystallization and to reduce processing times for PP, while Hyperform HPN 210 M is designed for use with PE in injection molding.
Multiple functions
Surlyn is an ionomeric ethylene copolymer manufactured by DuPont. Jose Torradas, a senior technical consultant with the DuPont Performance Materials division of DuPont, Wilmington, Delaware, says it can fit under more than one category of modifiers.
“In fact, there are some polymers that when added they can provide a double function,” Torradas says. “One of our resins, Surlyn, can be added to polyester to toughen it, and at the same time, Surlyn can nucleate polyester. So, it is two functions in one simple additive. The ions in Surlyn are good nucleating agents for PET.”
Surlyn, a well-known nylon impact modifier, also can be used as a compatibilizer. Additonally, it can be used to compatibilize nylon or PET with polyolefins, such as low-density polyethylene (LDPE) or linear LDPE, according to DuPont. It is available in a range of grades, each with a different balance of properties.
For more information: Addivant, 203-702-6140, www.addivant.com; DuPont, 302-774-1000, www.dupont.com; Milliken Chemical, 800-910-5592, www.millikenchemical.com; Ultra-Poly Corp., 800-932-0619, www.ultra-poly.com
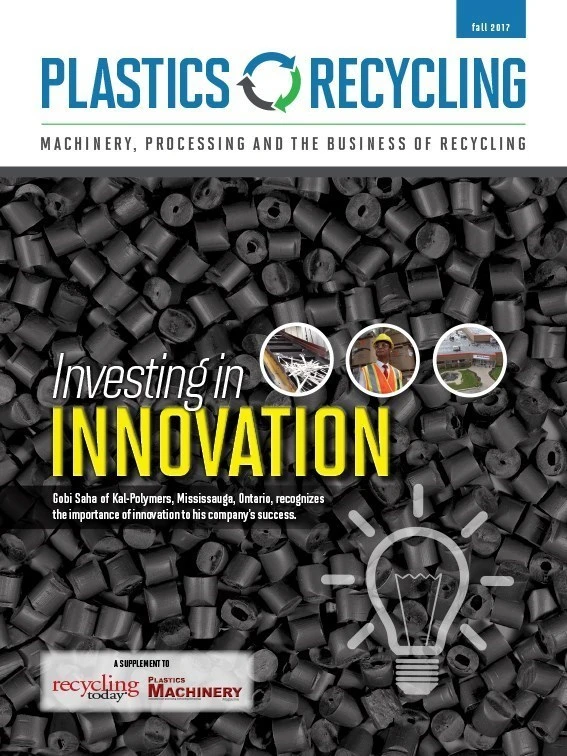
Explore the October 2017 Plastics Recycling Issue
Check out more from this issue and find your next story to read.
Latest from Recycling Today
- AF&PA report shows decrease in packaging paper shipments
- GreenMantra names new CEO
- Agilyx says Styrenyx technology reduces carbon footprint in styrene production
- SABIC’s Trucircle PE used for greenhouse roofing
- Hydro to add wire rod casthouse in Norway
- Hindalco to invest in copper, aluminum business in India
- Recycled steel price crosses $500 per ton threshold
- Smithers report looks at PCR plastic’s near-term prospects