
International Automotive Components (IAC), a Tier One supplier to the automotive industry, has been using recycled plastics in the automotive interior components it manufactures since the company was founded in 2006, says Susan Kozora, director of advanced engineering for the company. She adds that the “use of recyclates is part of the long line of experience from the companies who contributed to IAC’s heritage.” However, Kozora says, the company’s original equipment manufacturer (OEM) clients aren’t always so ready to embrace recycled-content components.
Kozora works in IAC’s Southfield, Michigan, North American headquarters. The company’s global headquarters are in Luxembourg. IAC is the third-largest automotive interior components supplier in the world by market share and the only global supplier solely focused on interiors. Its products include door and trim systems; instrument panels,
“IAC’s interest in using recycled content
Changing minds
Kozora says, “IAC has and continues to meet all product quality and performance requirements with the use of recycled materials, and we are trying to shift the paradigm that recycled materials are ‘cheap’ and
IAC’s recycled material supply base meets ISO quality standards and best practices, she says, adding, “We meet or exceed the OEM specifications with recycled products.”
The company’s work to gain respect for recycled materials in automotive products has helped to change automotive OEMs’ attitudes toward this material over time. “I see that our OEM customer base has ‘evolved’ over time with greater acceptance of the use of recycled materials and [as] IAC as a supplier has provided high-quality, consistent recycled materials in our products over the years,” Kozora says.
Some of IAC’s customers now are looking for recycled content in the design phase of their vehicles, she says, adding that they “are encouraging and even challenging IAC in their efforts to use and develop recycled materials.”
Among the recycled
In a year, the company consumes several million pounds of recycled plastics. “The total consumed depends on the type of material and the volume of the good-quality product on the market,” Kozora says. “For example, up to 70 percent of the HDPE is 100 percent recycled material, PC/ABS is about 30 to 40 percent, ABS is about 10 to 20 percent and PP ranges [from] 10 to 15 percent.”
She says this variation is
“IAC has and continues to meet all product quality and performance requirements with the use of recycled materials, and we are trying to shift the paradigm that recycled materials are ‘cheap’ and low performing.” - Susan Kozora
Overcoming hurdles
Finding consistent supplies of quality material in the quantities required for the automotive industry is one of the foremost challenges IAC has had to surmount over the years, Kozora says. But it is just one of many hurdles that IAC has had to overcome in its efforts to increase recycled content in its products.
Overcoming the prevailing paradigm concerning the use of recycled materials in the eyes of automotive OEMs continues to be an issue for suppliers like IAC, as well. “Automotive engineers still can see
Kozora adds, “Also, the more demanding the application, the less likely a recycled material will be considered. For example, low-functioning or nonvisible components are generally well-accepting of recycled materials, whereas high-functioning applications, like instrument panels, do not lend themselves well to recycled grades. Again, this is because it is seen as too risky for this level of performance, but it does not have to be perceived in that manner.”
Automakers also can expect recycled products to cost considerably less than their virgin counterparts, despite meeting the same standards and performance. “This type of expectation can bring to the market ‘low cost’ sources that may not meet quality standards, which may contribute to the aforementioned concerns with
Complications related to the recycling process also work against
This obstacle is related to another hurdle that Kozora sees as preventing more widespread use of recycled plastics by the automotive industry: dismantling and separating various plastics, particularly in the case of automotive recovery.
Recycled plastics also tend to be more regional than global in nature, she says, making it difficult to meet OEMs’ global design requirements.
“I see that our OEM customer base has ‘evolved’ over time with greater acceptance of the use of recycled materials and [as] IAC as a supplier has provided high-quality, consistent recycled materials in our products over the years.” – Susan Kozora
Designing sustainably
IAC is doing its part where possible to design with sustainability in mind. Kozora says the company takes many steps to do so, including optimizing materials for each application, improving product performance, improving product competitiveness and material cost stabilization, reducing shipments to landfill, using renewable resources and recycled materials and reducing part weight.
Regarding designing for recycling, Kozora says, “IAC considers
Ease of disassembly also is something IAC considers. “Design for disassembly helps to look at the end-of-life recycling of products to again provide a feasible method to dismantle and separate plastics to optimize reuse and promote closed-loop recycling,” Kozora says.
Engaging the supply chain
“Automotive material approval requirements are very rigorous, and they should be,” Kozora says. For this reason, IAC closely engages with its supply base.
“As with any other supplier to IAC, recyclers must go through quality certification, either through our quality
Kozora says IAC’s material approval process involves a number of steps:
- recycled resin evaluation;
- early resin supplier approval;
- resin property evaluation;
- initial product mold trial;
- an optimized test run;
- resin approval at the OEM;
- final product mold trial;
- final test evaluation;
- resin supplier approval; and
the product part approval process product.
“We have a good lineup of vetted recyclers, and we are always willing to look at new potential suppliers in the market.”
She adds that an established supply base is essential to the success of recycled material use. “It is critical to have grades of recycled resins approved at the OEMs so that they are available for use in new designs and where products can be launched with recycled resins.”
Top-down support from automotive OEMs also is critical. “Having the OEMs provide solid top-down objectives on recycling that are definitively communicated to engineering, purchasing and manufacturing communities will greatly improve and strengthen the use of recycled materials in the automotive industry,” Kozora says.
Benefitting from recycling
While there is no shortage of issues to address as IAC seeks to continue on its mission to incorporate recycled plastics in its manufacturing processes, Kozora says the company finds many benefits to using recycled content.
“In addition to increasing the green aspect and positive environmental impact on our products, we have seen benefits in cost, processing and a reduction in
For more information: International Automotive Components, 248-455-7000, www.iacgroup.com
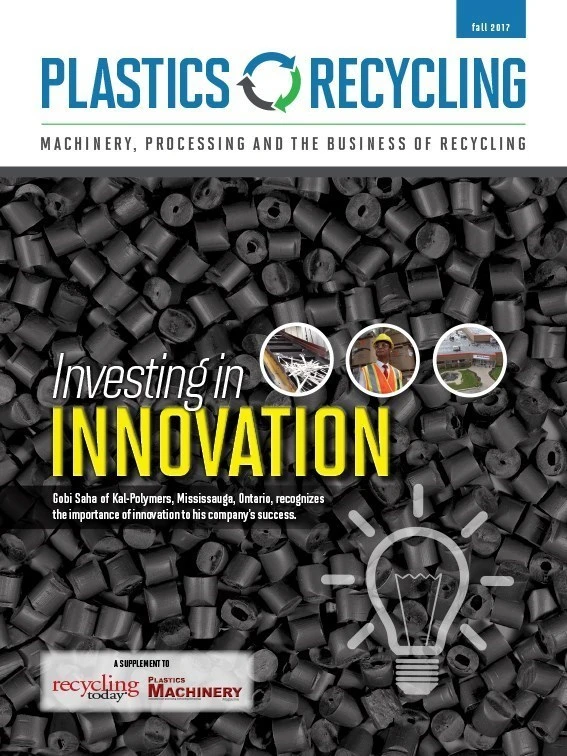
Explore the October 2017 Plastics Recycling Issue
Check out more from this issue and find your next story to read.
Latest from Recycling Today
- AF&PA report shows decrease in packaging paper shipments
- GreenMantra names new CEO
- Agilyx says Styrenyx technology reduces carbon footprint in styrene production
- SABIC’s Trucircle PE used for greenhouse roofing
- Hydro to add wire rod casthouse in Norway
- Hindalco to invest in copper, aluminum business in India
- Recycled steel price crosses $500 per ton threshold
- Smithers report looks at PCR plastic’s near-term prospects