
Recycled plastics don’t always behave as processors desire or expect. Because of physical degradation caused by repeated exposure to heat and pressure, they might fill molds improperly or break easily once transformed into parts. Sometimes their past histories become all too apparent, just with a simple whiff.
But, by using modifiers made by several materials manufacturers, including Polyvel, Struktol, Vertellus and Evonik Industries, recyclers can breathe easy, knowing their products will exhibit the physical properties they want.
A variety of modifiers, including viscosity modifiers, chain extenders, reodorants
Viscosity modifiers
Recyclers commonly use viscosity modifiers, which can improve the melt flow of recycled plastics, says Kevin Cronin, vice president of sustainability and R&D at Ultra-Poly, a Portland, Pennsylvania-based compounder and recycler dealing primarily with polypropylene (PP), polyethylene (PE) and polyvinyl chloride (PVC).
Resins with poor melt-flow characteristics may not adequately fill injection molds, among other problems.
“If we have a fractional melt polypropylene, compounding in precise amounts of active peroxide compound can break that viscosity,” Cronin says. “There is a chain scission within the polymer backbone that can take a fractional melt and bring it into an injection molding grade, for instance. That’s generically known as
Numerous companies offer visbreaking products. Polyvel, Hammonton, New Jersey, and Struktol, Stow, Ohio, are two of the best-known manufacturers of viscosity modifiers, which are primarily used with PP.
“They are chemical visbreaking additives that are designed to take a very low-melt-flow polypropylene and make it a higher melt flow,” says Mike Fulmer, Struktol vice president for plastics and wood-plastic composites. “It allows the compounder control of the viscosity of their final compound. We have several different grades of this product.”
One of the challenges of viscosity modification is dealing with contaminated recycled PP. Many modifiers that reduce the viscosity of PP can increase the viscosity and decrease the melt flow of any PE contaminating the resin. The net result is little change in viscosity and
Struktol’s standard visbreaker is RP 11, which is recommended when a recycler is processing 100 percent PP or when the level of PE contamination is very low, at 5 percent or less. However, when contamination is higher, the company recommends RP 37 or RP 38, both of which are designed to increase the melt flow of PP without increasing the viscosity of PE.
Polyvel markets a range of peroxide masterbatches for use in PP recycling.
“We make a line of peroxide concentrates,” says Polyvel Sales Engineer Dean Dodaro. “It is a pelletized version of peroxide that polypropylene recyclers use to increase melt flow.”
Polyvel manufactures CR5P, CR10P and CR20P masterbatches, which represent 5, 10 and 20 percent peroxide concentrations, respectively. Polyvel can recommend a particular product and dosage based on the amount of melt-flow increase a customer seeks.
“The idea that a little bit goes a long way is why we have different concentrations for peroxide,” Dodaro says.
Chain extenders

Chain extenders are additives that relink molecular chains and increase viscosity and mechanical properties. This allows resins, including many engineering plastics, such as nylon and polyethylene terephthalate (PET), which degrade during processing, to be used in higher-value applications.
Indianapolis-based Vertellus manufactures its ZeMac family of chain extenders, which can be used with virgin and recycled nylons and other polyamides. One of its products, ZeMac Extend M600, also has been used to upgrade recycled PET from postconsumer bottles to produce injection-molded PET products, according to the company. Vertellus also is working to develop other compatibilizers for PET mixed with nylon.
Ashok Adur, commercial development director for plastics at Vertellus, says the company originally used ZeMac as a coupling agent for glass fiber compounded into some
“When I came in, because of my compounding background, we said we should be able to apply that same chemistry to upgrading recycled nylon,” Adur says. “We found we were able to upgrade recycled nylon to pretty close to what prime nylon was.”
However, he says, the company quickly found results could be inconsistent because of variations in recycled nylon quality.
“Unless you have consistency, it is very hard to develop a process where you can utilize this on a regular basis because you cannot keep tweaking how much of our product you use,” Adur says.
The bulk of the nylon recycling stream in the U.S. comes from carpet scrap, and it typically has a variety of other materials mixed in, he says.
As a result, Vertellus now is working with two companies that have access to a consistently high grade of recycled nylon. They can recycle that resin into prime-quality nylon, he says.
With other nylon recyclers, Vertellus took a different approach. It found that ZeMac can work with recycled nylon of inconsistent quality if it is blended with virgin nylon at a ratio of about 20 percent recycled to 80 percent virgin.
However, with relatively low prices for nylon, using additives to create materials has less appeal.
Reodorants /deodorants

Some recycled plastics have residual odors because of how they were originally used. That makes reodorants and deodorants popular modifiers.
“Odors are very often a general problem with recycling from postconsumer applications, like packaging,” says Rudolf Pfaendner, division director for plastics at the Fraunhofer Institute for Structural Durability and System Reliability in
Solutions can be as simple as buying additives that impart a pine smell to mask bad odors.
“It is a smell additive that offers a good impression, or it at least leaves you in a good mood,” Pfaendner says.
“The other story,” he continues, “which, from the chemical point of view, is much more attractive and much more interesting, is that you add an additive that can scavenge odor.”
Odor scavengers react chemically to suppress odors in
“So,
Nevertheless, various products are available on the market that
He cites Tego Sorb PY 88, a zinc ricinoleate that works by eliminating odors rather than by using fragrance to mask them. The product is produced by Evonik Industries AG, Essen, Germany.
Another frequently used product is Struktol’s RP 17.
“It’s primarily an odor-mask technology,” Fulmer says. “It goes in and covers up existing odors.”
The product works with recycled materials ranging from ground tires to PP and PE with a noticeable odor.
“Just a small amount of RP 17 can cover up that odor and make the odor of the compound very neutral and more acceptable to the
Polyvel markets two categories of odor managers: an absorber, which is mineral-based, and a mask/neutralizer, which combines deodorizing with a pleasant fragrance, Dodaro says. Both types of odor managers are sold under the company’s ZO series of modifiers.
Regardless of a compounder’s or a recycler’s goal, an additive likely is available to help achieve it.
For more information: Evonik Industries AG, 49-201-177-01, www.evonik.com; Fraunhofer Institute for Structural Durability and System Reliability LBF, 49-6151-705-0, www.lbf.fraunhofer.de/en.html; Polyvel Inc., 609-567-0080, www.polyvel.com; Struktol Co. of America, 330-928-5188, www.struktol.com; Ultra-Poly Corp., 800-932-0619, www.ultra-poly.com; Vertellus Holdings LLC, 616-748-7802, www.vertellus.com
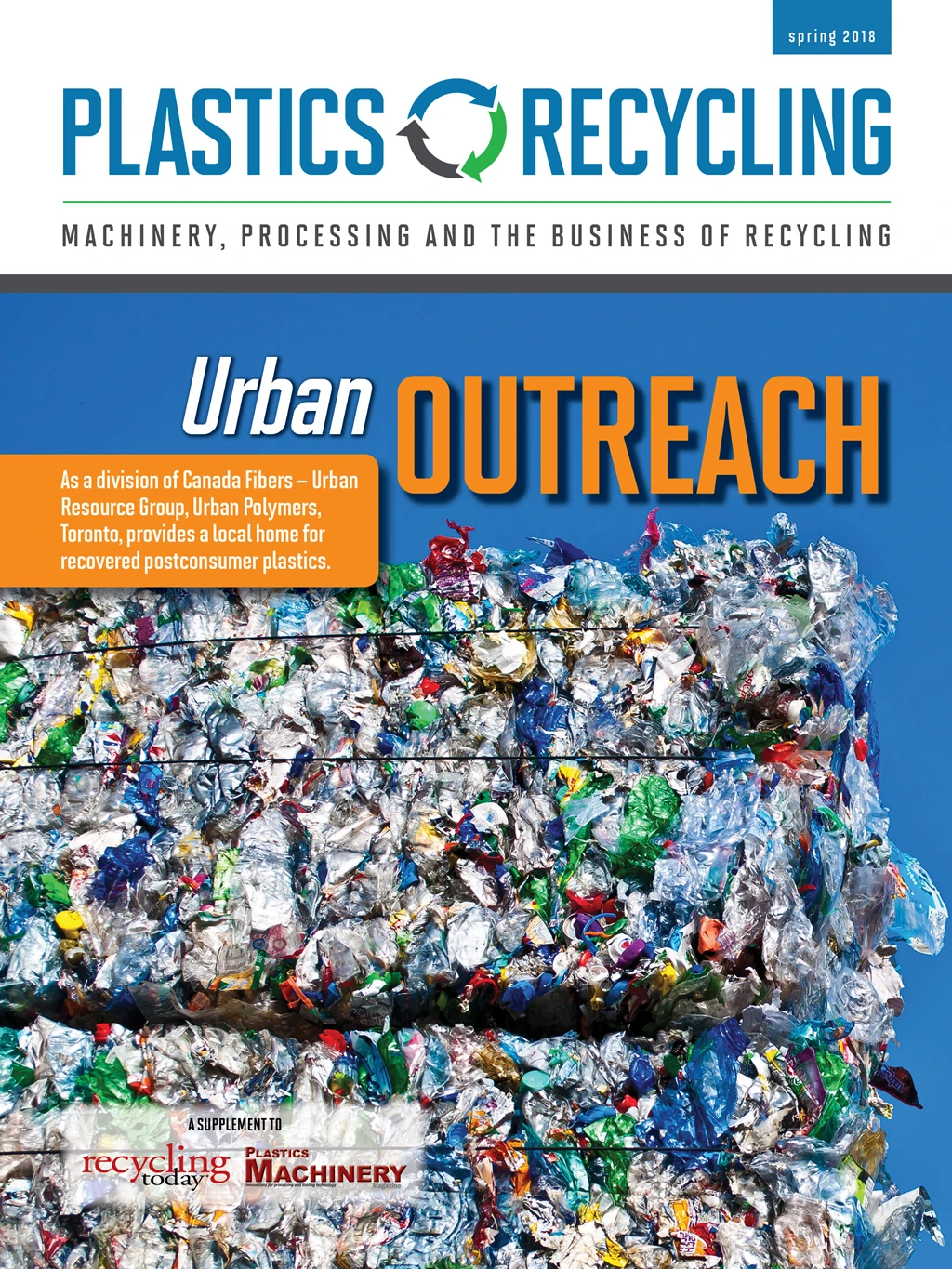
Explore the May 2018 Plastics Recycling Issue
Check out more from this issue and find your next story to read.
Latest from Recycling Today
- Rebar association points to trade turmoil
- LumiCup offers single-use plastic alternative
- European project yields recycled-content ABS
- ICM to host colocated events in Shanghai
- Astera runs into NIMBY concerns in Colorado
- ReMA opposes European efforts seeking export restrictions for recyclables
- Fresh Perspective: Raj Bagaria
- Saica announces plans for second US site