
When Bret Garrison decided to expand his business to include plastic recycling, he decided to further vertically integrate operations to compete against larger companies in the marketplace. Mega Recycling & Compounding Services LLC, Romeoville, Illinois, shares a building with its sister company Mega Polymers Inc. Garrison also is in the process of establishing Mega Compounding Technology LLC and Mega Molding Co. LLC in the same building.
Mega Recycling began operations in 2014 with one grinder from a Chinese manufacturer. Since then, it has grown to include seven grinders.
Garrison, who is president of Mega Recycling, says the recycling operation, which “starts with the grinders,” directly supports Mega Recycling’s sister companies and allows the company to be competitive in the marketplace.
“Think of a company that’s vertically integrated with four different companies under one roof, and it all starts with grinding,” Garrison says. “If we didn’t have the grinders, then the other three companies could not exist competitively in the marketplace.”
Wise investments
Mega Recycling’s operations include a 15-horsepower grinder from Rapid Granulator Inc. of Leetsdale, Pennsylvania, two 60-horsepower grinders from a Chinese manufacturer, two grinders from Zerma Machinery & Recycling Technology of Shanghai (100-horsepower and 25-horsepower machines) and two from Cumberland, New Berlin, Wisconsin (100- and 60-horsepower machines).
“We started, like a lot of people, with very affordable Chinese grinders,” Garrison says. “They paid for themselves quickly, but they don’t last long.”
Garrison recalls the excitement among his team when Mega Recycling began using the first grinder to process a diverse array of recovered plastics. Since purchasing that grinder, Mega Recycling outgrew its original 25,000-square-foot facility. Mega Recycling and its sister companies will operate in a 75,000-square-foot facility, where all the operations will function “harmoniously,” he says.
“It took off in a matter of two years,” Garrison says of the recycling operation. “Once you get over the hump and you know what you’re doing, things escalate quickly. We have truckloads coming in every day.”
He adds, “They were very humble beginnings to say the least. We’ve been in this building two-and-a-half years. We got the Zerma grinders two years ago. We chose the Zerma because their salesman came out and really supported what we’re trying to accomplish.”
Mega Recycling runs the grinders 12 hours per day, five days per week. Polypropylene (PP), high-impact polystyrene (HIPS), polyethylene (PE), polycarbonate and nylon, among other plastics, are sorted and ground before being compounded into resins, which will be molded into plastic parts by Mega Molding.
Mega Recycling processes about 3 million pounds of PP per year. The two Zerma grinders are “dedicated to processing PP,” with the 100-horsepower Zerma being the “star” of the recycling operation, Garrison says.
“It’s brand new,” he says. “It runs very efficiently. It just chews up plastic about as efficiently as you can ask for.”
Keeping clean
Garrison says cleaning the grinders regularly is integral to producing the high-quality value-added “brand name” resins that Mega Polymers prides itself on. The biggest challenge with the grinders, he says, is balancing cleanout times and work schedules to reduce downtime while ensuring the equipment is “properly cleaned out before the next material comes through.”
He continues, “The challenges of grinding, of course, are cleaning out the grinders and making sure your time is used most efficiently.”
An attractive selling point for the Zerma and the Cumberland grinders was that they featured designs to facilitate cleaning, Garrison says.
“Both are designed in such a way that they open up and they clean so much easier than some of their competitors,” Garrison says. “Spending a little more money upfront really saves you in the long run because they designed the equipment to be opened and are much easier to clean.”
He adds that the Zerma grinders don’t need to be cleaned out often because they’re dedicated to processing PP; however, the other grinders must be cleaned once per week to prepare for processing other plastics.
Building the brand
Investing in the grinders not only has allowed Mega Recycling to process a variety of materials, it also puts the company in a strong position to provide a steady stream of high-quality resins to Mega Compounding and Mega Molding as well as to current and potential customers.
“Whatever material comes out of those grinders goes directly to Mega Polymers, Mega Compounding or Mega Molding,” Garrison says. “All three of those other companies potentially are a customer of Mega Recycling, which owns the grinders.”
Inspired by Henry Ford, who in the 1920s began making much of his own steel rather than buying it from suppliers, Garrison adopted the vertical integration model in his businesses.
Today, the process of recycling materials to produce a new product is in “fractions,” Garrison says. The vertical integration model offers a more “positive impression of what the industry is capable of doing if people think out of the box and stop thinking of recycling in the traditional sense,” he says.
Garrison’s four companies will “work harmoniously,” from sorting and grinding material at Mega Recycling to compounding regrind into pellets at Mega Compounding Technology to molding parts at Mega Molding.
“If you’re going to compete against the other giants of the market, there’s a lot of little guys out there like us that are forced to think outside of the box,” Garrison says. “I think [by] starting with the recycling operation, the grinding operation, it allows us to do some other things that put us in a position to compete against anybody and everybody.”
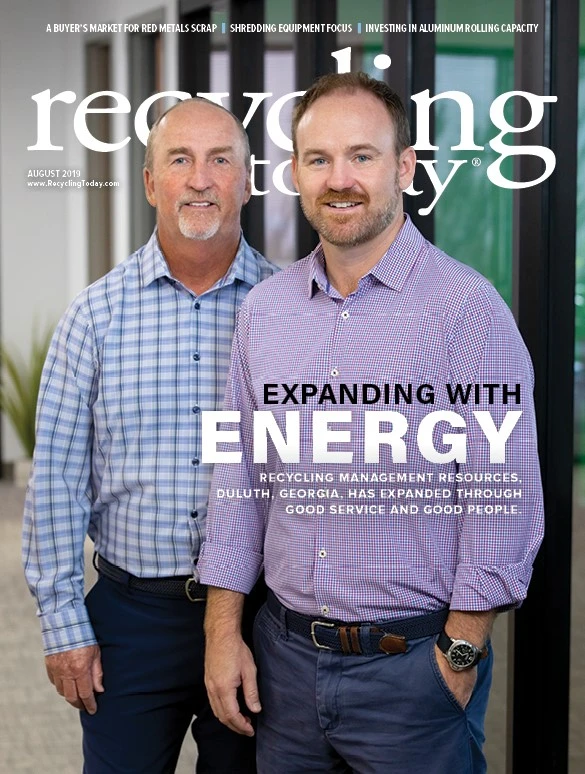
Explore the August 2019 Issue
Check out more from this issue and find your next story to read.
Latest from Recycling Today
- Eagle Dumpster Rental identifies its MRF-unfriendly items
- American Securities acquires Integrated Global Services Inc.
- Fleetio integrates Maintenance Shop Network add-in
- 3rd Eye expands suite of fleet safety solutions
- Newsom orders SB 54 revision
- Biffa sees recycling, composting opportunities at events
- Copper market navigation stress lingers
- IWS ramps up NJ MRF